Petrobras looks to disruptive technologies to ensure all E&P projects have ‘double resilience’
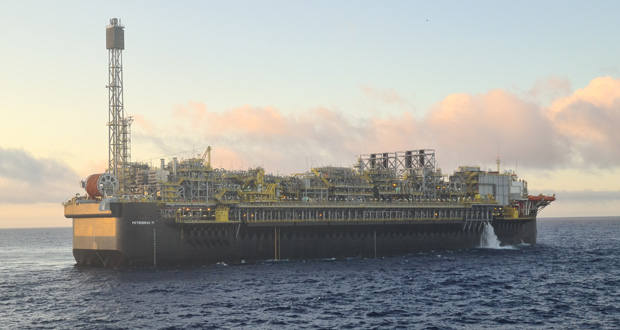
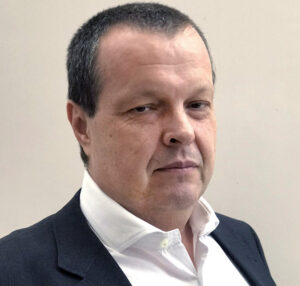
Petrobras’ João Henrique Rittershausen: Innovations like True One Trip, all-electric completions help to support strict goals around cost, emissions
By Linda Hsieh, Editor & Publisher
João Henrique Rittershausen is Chief Production Development Officer at Petrobras.
What do you see as the biggest challenges for the drilling industry right now?
Today, the biggest challenge is to complete our drilling campaigns on schedule and within budget. We have already seen incremental increases in the dayrates for rigs, and we also see problems in the supply chain due to the low level of operations that the industry had seen in the past few years.
While Petrobras has not seen any impacts on the timelines of our projects so far, we do see challenges with the returns of rigs that were in cold stack. Because of the increase in drilling activity, we understand that sometimes the only way to have the rigs we need is to bring them back from cold stack. So, in our planning and our bids, we are allowing more time for the mobilization of those rigs because we understand that the rig contractors and their sub-suppliers are seeing challenges with both people and materials. They need more time to bring those rigs back to normal operation mode in a way that will ensure safety, integrity and reliability.
At the same time, we’re also increasing the duration of the contracts we offer to make it more feasible for the rig contractors to invest in bringing the rigs back to operation.
Overall, the industry has lost a lot of experienced people in the past few years, so this return in the market is not easy.
How are you addressing the challenge with rising costs? Does that mean fewer wells will be drilled?
Not at all. We understand that oil prices will always be volatile, so we have built our projects to be resilient even at a Brent oil price of $35 per barrel.
In our newest 2023-2027 business plan launched in December, we outlined $78 billion in CAPEX, with 83% going to exploration and production. To ensure project sustainability, all of our projects are planned under the concept of Double Resilience, which means they are resilient both economically to $35 and environmentally, with a carbon intensity of only 15 kg of CO2 equivalent per barrel.
What is Petrobras doing to ensure this type of resilience for your projects?
The answer to this is innovation. When it comes to cost reduction, we cannot just keep doing the same things in the same ways. We need new technologies and new equipment so that we can deliver more cost-effective wells. For example, Petrobras has developed our True One Trip concept, which involves drilling the well in just three phases and installing the completion in one run. We’re also using a drill-through wellhead system to reduce drilling time by avoiding the need to trip the BOP.
When you consider the first wells that we drilled in pre-salt years ago, a well would take us more than one year to drill. Today we can drill that well in around 60 days.
What about on the environmental side? What are you doing to support emissions reduction from drilling operations?
That is very important to the resilience of our projects. Even though we know that drilling operations are not the highest emitters in our projects, we need to be very connected to this challenge, and everyone must have plans on reducing emissions.
When we look at emissions reduction, there are three big areas for us: wells, FPSOs and subsea systems.
With wells, the best option to reduce emissions is to reduce the time required for well construction. That’s a win-win because we will reduce both the cost and the emissions. However, we can only do this with cooperation among all the companies involved – Petrobras, drilling companies and service companies, and this means we need to have better equipment reliability. In a field like Búzios, for example, where a single well can produce 60,000 barrels per day, reliability is very important.
We are also working to increase the efficiency of diesel consumption through the use of incentives with our contractors, as well as additive technologies.
With FPSOs, we are investing a lot in new designs to reduce emissions – for example, topside electrification, optimization of the seawater cooling system, as well as carbon capture, utilization and storage. In subsea systems, we are looking at various initiatives like the application of diverless solutions.
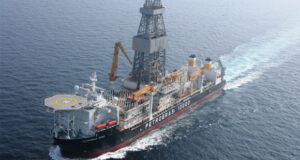
What do you think of when it comes to the future of drilling and wells?
We would like to have autonomous rigs and disruptive drilling technologies. In the long term, we would like both our drilling rigs and our FPSOs to be unmanned – but, of course, this is not going to be easy. When you talk about an unmanned operation and autonomous rig, everything must be redesigned, and we need to have much higher levels of reliability than what we have today. I don’t think we can just take today’s rigs and transform them into an autonomous rig; it will require a completely different approach.
Digitalization will be a key enabler, and we need to automate the processes around well planning, design and operation, as well as have integration with the supply chain. We will need well structure alternatives, high-performance completions, real-time integrity monitoring, rigless maintenance, and wells that can self-stimulate and be self-abandoned.
Of course, this is all a vision for the future. We don’t have a project saying we will have an autonomous rig within a certain time period, but these are things we are always studying and thinking about. Along the way, it can also inspire the development of other new technologies that we can implement today.
In October last year, Petrobras selected seven rigs from a “mega tender,” and all the rigs are required to be ready for operation in 2023. What is Petrobras doing to make sure that it will be ready to start so many drilling rigs and campaigns?
From Day 1 after signing the contract, we are working closely with the rig contractors to review lessons learned with previous rigs that have undergone acceptance tests. We also have careful planning and talk about how we will commission the rig, then look at their people and skills. When we start a new rig, it’s important that we are not just taking experienced people from other rigs that are already in operation.
Also, I would also say it is not unusual for Petrobras to start multiple rigs in a short time period. In addition to the rigs, from 2023 to 2027 we will also be implementing 18 new FPSOs, which will be half of all the FPSOs delivered worldwide in that time period. We will do very detailed planning, and we’ll be successful in starting these operations in the schedule that we need.
Petrobras has invested significantly in the Equatorial Margin. How does that region fit into your plans for the next few years?
Nearly half of Petrobras’ $6 billion of exploration CAPEX from 2023 to 2027 will go to the Equatorial Margin. It is very important to Petrobras to start working in this new frontier region, and we hope to begin drilling the first well there in early 2023.
We believe this frontier has significant potential, and opening this new exploration area will bring a lot of value both for Petrobras and Brazil.
When it comes to innovation for offshore rigs, what upgrades would you like to see?
Today, it is not easy to request big changes in drilling rigs, so we are trying to hire rigs that will require the least amount of changes to operate for Petrobras. However, we still see some advancements that would be good, particularly technologies around diesel consumption reduction and riserless operations. We would also like to see BOPs with a higher shearing capacity, because when you look at a risk matrix for an oil company, a blowout is the highest risk we have. We need to do everything we can to ensure we will not have an uncontrolled well.
We would also like to see more dynamically positioned (DP) rigs that are capable of operating in shallow waters. Today’s environmental restrictions mean that sometimes we cannot use moored rigs to drill and complete shallow-water wells anymore, and we need DP rigs that can allow us to conduct abandonment operations for those types of wells.
And, of course, digitalization is a very important point to us because we see automated drilling as the future. We are discussing new initiatives with rig contractors and service companies to use automation systems so that, no matter who the driller is, we can always have software that is using the best knowledge of the best driller to control the drilling system. We are confident that automation can increase the efficiency and the value creation throughout the drilling process.
If we look at well completions specifically, what do you see as the biggest challenges and technology gaps?
For us, it’s all-electric completions. We want to move from a mix of hydraulic/electric to all-electric completions that can be more reliable and cost effective. We are working with several companies to have all-electric completions qualified.
Within the next couple of years, we expect to install the first electric, open-hole intelligent completion, and we expect this to be a game-changer for us in terms of reliability and capability to manage the reservoir. DC