Advancing advocacy necessitates a more nuanced energy dialogue
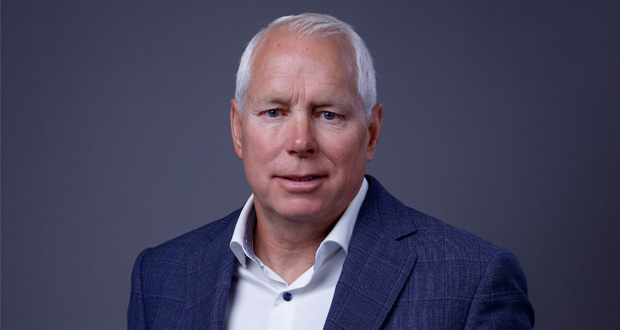
From the Chairman
It’s an honor to serve a second term as IADC Chairman, especially during this monumental year celebrating IADC’s 85th anniversary. Both the energy and cultural landscapes have transformed significantly since I last served in this role in 2019, making IADC’s work more crucial than ever.
As Chairman, one of the main areas in which I’d like to see increased focus this year is advocacy. While we’ve made progress in communicating our industry’s value, the journey ahead remains crucial. We must continue developing more sophisticated ways to engage with stakeholders, policymakers and the public. Advocating for hydrocarbon energy and the role of drilling is going to be an ongoing requirement of our industry for the foreseeable future.
As members of IADC, we all understand that secure and abundant energy makes people’s lives better. Our civilization runs on energy, and it is fundamental to virtually every facet of our lives. While we understand that society needs a comprehensive mix of energy supply systems, it’s disappointing that the current popular dialogue often falls into oversimplified narratives. Hydrocarbons and CO2 have been labeled “bad,” and renewable energy is branded as “good.” This black-and-white, either-or approach ignores the complexity of highly engineered energy infrastructure and the intricate relationship between different energy sources in powering our world. Even more troubling is that it undermines our ability to address real challenges.
It’s our industry’s responsibility to play a more active role in conversations about energy in order to elevate the entire narrative. We need to champion a more comprehensive understanding of energy systems that acknowledges energy security, economics and long-term sustainability goals. By challenging critical thinking with this complexity, we can approach energy challenges with the sophistication and nuance they demand.
Despite the obstacles this industry faces, I’m genuinely excited about what lies ahead. I’ve met many bright and eager students from IADC Student Chapters at IADC conferences and other industry events. Their enthusiasm for innovation and problem-solving gives me tremendous confidence in our industry’s future.
These students want to be part of the solution. At IADC, we can play a vital role in showcasing our industry as the constructive and technologically advanced field it truly is. Through this effort, we can build trust and confidence among the next generation of industry leaders, ensuring a sustainable pipeline of innovation for the future.
The growth in IADC’s Student Chapter program tells a compelling story. Since the beginning of my first term at IADC in 2019, we have gone from three to 21 Student Chapters, with 12 inside the US and nine outside the US. The new IADC scholarship program introduced last fall serves to further encourage and support this industry’s future leaders.
Our industry stands at the intersection of tradition and innovation. As we celebrate IADC’s 85th anniversary, we’re not just looking back at our achievements — we’re actively shaping the future of energy through industrywide collaboration on technology, safety and advocacy. Our association is doing tremendous work to continue advancing our industry, and there are countless ways to get involved. Some examples include joining a committee, attending or presenting at a conference, providing opportunities and mentorship for Student Chapter members and young professionals, or adding your voice to the conversation when IADC visits with legislators.
The path forward is clear: While we won’t change the world’s conversations about energy overnight, we must maintain our momentum and purpose. Our goal is to advance this vital dialogue step by step, shifting the narrative through meaningful engagement at every level. By building a foundation for more nuanced energy discussions today, we’re paving the way for collaborative solutions that will serve our industry — and the world — for decades to come. DC