OGP recommendations to focus on industry well control training
By Linda Hsieh, managing editor
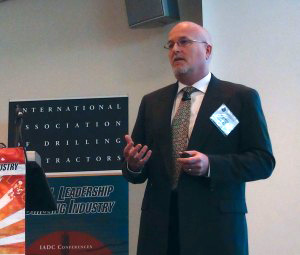
A workgroup under the OGP Wells Expert Committee (WEC) is nearing the launch of a set of recommendations to enhance industry’s well control training, examination and certification that outlines five discrete levels of well control training that are role-dependent. For example, the group would like to re-focus driller training back toward early detection and shut-in rather than supervisory training, Gareth Williams, who chairs the WEC Human Factors, Training & Competency Workgroup, said in a presentation at the 2012 IADC Drilling HSE Europe Conference in Amsterdam on 27 September. “We’re focusing too much on drillers doing the well control calculations. It’s fine for them to do that, as long as they don’t forget their primary purpose of early detection and shut-in,” Mr Williams said.
His workgroup is one of four under the WEC that are collectively working to improve prevention of incidents; the other three are studying BOP reliability, international standards and the creation of an incident database. “Our objective is to have a step-change improvement in the competence and behaviors of operational teams across our whole industry. It’s not just deepwater, high-tech wells. We’re looking at the whole of our industry,” Mr Williams explained.
The Human Factors, Training & Competency Workgroup is specifically pursuing two tracks. “One is by taking the existing vehicle that we’ve got of well control examination and certification and making it better, both in terms of technically what’s taught but also the behavioral piece,” he said. “The second element is to provide tools to assure the competence of our teams.”
Members have divided its work into three phases, the first of which resulted in the well control training recommendations that OGP is expected to launch as OGP Publication No. 476. The document has been reviewed and endorsed by all WEC members and aims to provide clear guidance for industry’s well control training accreditation programs such as IADC WellCAP, Mr Williams said. “There’s a one-year time period that’s expected to develop the training courses, then two years to implement it,” he said.
The recommendations, which apply to all well operations, define specific improvements to the technical content of training syllabi and specify minimum levels of training for a wider range of personnel that may contribute to the avoidance of a well control situation. Further, a more systematic auditing process is adopted to ensure training goals are consistently achieved.
Phase Two of the WEC workgroup’s project will look at developing crew resource management training for operations teams in partnership with a university, and Phase Three will take up competence assessment and assurance, Mr Williams said.
He believes that human factors, not equipment nor procedures, are the key to preventing “similar” well control incidents as those that have occurred in the past. “We change the equipment, we write a new procedure, and we think the problem will go away. Probably the exact same problem will be resolved by that,” Mr Williams said. “If, in addition, we’re brave enough and bold enough to address the human factors, then we will prevent similar incidents from happening, and this is what we now need to do. Stop responding purely with equipment or procedural changes and deal with the human factors as well.”