Making the right HSE decisions at right time
Tailored training, qualifications, industry knowledge fast-track individual competence in HSE risk management
By Gareth Book and Steve Lewis, Risktec Solutions
In an ideal world, drilling contractors and operating companies would have access to competent and sensible advice from internal and external professional health, safety and environment (HSE) advisers so that risks associated with their operations are properly managed and unproductive measures and paperwork are not pursued.
In practice, the reality is sometimes that an organization’s HSE advisers may be drowning in a sea of procedures and changing legislative demands, overloaded by responsibilities to provide HSE training and monitor HSE in the workplace, or overwhelmed by technical calculations and large, formal and impenetrable reports delivered by experts.
By providing a fully resourced and competent HSE risk management work force, the drilling industry can hopefully avoid this. If individuals are confident of their judgment, they are in a position to apply their knowledge and skills effectively. Good decisions will be made, and the organization will benefit from improved HSE performance, increased efficiency and enhanced confidence of all stakeholders.

The competence gap
A fully competent individual has gained knowledge and skills through a combination of training, qualification and experience. In the field of HSE risk management, the knowledge and skills of an individual need to cover the drilling industry, as well as the theory and application of technical risk management techniques (Figure 1).
An HSE risk management professional may be proficient at applying risk management tools but, through a lack of training or experience, may not have a good understanding of the drilling industry.
Alternatively, an individual may have many years of experience in the drilling industry but, through a lack of training, may not fully understand a particular risk management concept.
In both of these cases, the competence gap arises when there is a mismatch between an individual’s knowledge and skills and the judgments they must make as part of their role.
Judgments to be made
A competent HSE risk management professional is expected to:
• Confidently provide advice to help the organization make the right risk-based decisions at the right time;
• Keep an open mind and see beyond preconceptions;
• Apply appropriate risk management techniques and accurately interpret results; and
• Draw on their own judgment and apply common sense.
Risk management professionals can be called upon to make an enormous variety of judgments. HSE risk management roles span a broad spectrum, from overseeing HSE management at the rig site and controlling the exposure of individual workers, to building HSE risk management into the design of a new drilling rig or piece of equipment, to making informed, risk-based decisions about company strategy and management of multimillion dollar projects with the potential for far-reaching impacts and societal effects.

Increasing competency demands
The nature of the drilling industry is leading to increasing pressure being placed on individuals to make the right decision at the right time. Legal requirements are becoming increasingly complex as a consequence of catastrophic accidents, especially blowouts. Combined with frequent “raising of the bar” in company standards and operating in progressively harsher and more hazardous environments means that demands on HSE risk management practitioners have never been so high (Figure 2).
Ensuring compliance with prescriptive HSE legislation is generally accepted as the minimum standard to achieve. Indeed, many regulators worldwide have moved beyond this to a “goal-setting” regime rather than a prescriptive “tick the box” regime, and require duty-holders to formally demonstrate control of all hazards via effective management systems and documented formal assessments.
Further, in countries without a well-developed regulatory regime, multinational oil companies set their own high standards, which drilling contractors and well services providers must meet wherever they operate around the world. Meeting these standards is far from easy – it needs to take into account the views and concerns of those stakeholders affected and tends to require the documented consideration of improvement options, both implemented and discarded.
Demographics also are not helping, considering the generational gap that resulted from a low influx of new personnel into the drilling industry in the late 1980s and early ’90s. The work force is aging, with typically more than 50% ages 45 or older.
Bridging the gap with training
There is a wealth of industry-specific HSE risk management training available to fill the gaps in an individual’s knowledge.
Technical training
Off-the-shelf training may not fit the reality in the field. For example, a provider may be brought in by the head office to deliver exactly the same training in a given technique across all drilling rigs of an international drilling contractor, irrespective of the differences among the drilling rigs, operator expectations and any location-specific issues.
In other cases, training may be delivered but not followed through with assessment and checking of learning, so the trainees may go on to misapply the technique as a result of misunderstanding or a lack of complete knowledge of the subtleties and potential pitfalls. This is particularly likely where training is provided as a “one-off hit.”
Competent individuals need to be able to understand and apply risk management techniques but also need to be able to accurately and confidently interpret the results.
Spoon-feeding of information during a short training course, trying to cram in as much as possible without the requirement to critically analyze and research information, is an inefficient use of the training budget because it may not deliver competent personnel.
Academic study
There are broader educational courses covering entire HSE risk management concepts and detailed theory. These courses are generally long-term, spanning months or even years, and usually involve a formal postgraduate qualification such as a diploma or master’s degree.
While such study can deliver a solid grounding in the underlying theories and concepts, they have a tendency to focus on abstract or theoretical examples. They may be far removed from the drilling-specific day-to-day practical realities of the individual’s job, which can be anywhere on a broad spectrum of risk management activities. There may also be an understandable tendency for academic institutions to focus on new and emerging research rather than current good practice in industry.
Three simple steps to bridging the gap
There are three simple steps to bridging the competence gap:
Step 1: Tailor the training (one-size does not fit all)
Effective training must address real risks that are relevant to the organization and the individual, rather than focusing on trivial or irrelevant theoretical examples, and should make use, wherever possible, of actual company procedures and standards.
The balance between lecturing and practical exercises is also important. To adequately bridge the competence gap, training must provide sufficient practical, hands-on experience of HSE risk management techniques. The exercises should be based on real-life drilling case studies.
Step 2: Obtain qualification (it can prove important)
If training is teamed with assessment of performance and gaining a qualification, employers are assured that their staff will actively participate in the training course and gain measurable skills from attending the training. Individuals receive a recognized qualification, which demonstrates investment in employees and contributes toward professional development.
Traditionally, many HSE risk management professionals have developed their skills through experience and on-the-job practice. Qualification can test understanding and learning.
It is important that the qualification demonstrates real competence in practice and is not just a measure of how well the individual was able to recall the information delivered to him or her during the training course.
Step 3: Understand drilling-specific issues
A thorough understanding of concepts and techniques stands the HSE risk management professional in good stead, but it must be complemented by at least a working knowledge of the technical issues facing the drilling industry. Without this knowledge, hazards may be overlooked, preventive and mitigatory measures may be missed or defeated, and risks may not be controlled.
HSE risk management professionals also require a thorough understanding of the current and proposed regulatory requirements across the industry.
Ideally, the HSE risk management professional should also have at least an awareness of best practices in other major hazard industries, such as offshore production or the nuclear sector.
Case study
How can the positive aspects of training, qualification and understanding of drilling-specific technical issues be integrated into a structured training program that meets an organization’s business needs?
The external training market is very fragmented, with many providers of public courses. Most drilling organizations also have in-house courses, which range from excellent tried-and-tested courses to legacy courses that have not kept up to date. In terms of higher-level qualifications, very few institutions offer first degrees in HSE risk management (e.g., BSc, BEng), although there are a few more offering postgraduate qualifications to master’s level, either by residence or distance learning.
As an example of how the gap in training and education was filled in another major hazard industry, Risktec was approached by a government regulator for nuclear power site licensing to develop a bespoke training program for national recruits who were not sufficiently skilled in nuclear safety and regulation.
A feasibility study explored the options available for building the customized training program. A pilot program successfully delivered the training to the first tranche of students, and the program continues to evolve for each year’s new set of recruits.
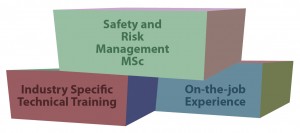
The bespoke training program consists of three components (Figure 3):
• A modular training program providing a solid grounding in HSE risk management principles and techniques, with a good mix of lectures and practical hands-on exercises using real-world case studies relevant to the nuclear regulatory role, combined with a formal assessment of competence and a master’s level qualification;
• Training courses to provide a foundation in the principles, technical issues, legal requirements and regulatory aspects of the nuclear industry; and
• Work experience at nuclear power sites to provide an opportunity to put the training into practice, shadow experienced professionals in similar roles and interact with a range of industry personnel.
The students gain a formal, recognized HSE risk management qualification, relevant knowledge of nuclear technology and regulatory topics, contact with industry practitioners and site experience.
Key benefits
Key benefits to the student include:
• Receipt of a formal qualification from a recognized institution;
• Demonstration of learning rather than just attendance at training;
• Specific learning, where case studies are directly related to the place of work; and
• Pathways through programs are tailored to individual needs.
Key benefits for the company include:
• More skilled resources with formal qualification and greater staff retention;
• Relevant learning, by tailoring case studies and methods;
• Up-to-date learning delivered by approved risk practitioners; and
• Flexible, modular approach allows integration with company existing training and development programs.
Conclusions
HSE risk management is relatively new compared with other professions. The role of competent HSE risk management individuals is to confidently provide advice to help the drilling organization make the right decisions at the right time, and, above all, draw on their own judgment and apply common sense.
An appropriate approach to training is likely to contain:
• Practical hands-on experience of risk management techniques;
• Case studies that are relevant to the individual and based in the real world;
• Assessment of learning and not just testing of information recall; and
• Understanding of drilling industry and technology-specific issues.
Such an approach can fast-track the process of delivering competent risk management individuals to the drilling industry and thereby help to meet the skills shortage and the increasing demands it faces.
This article is based on a presentation at the 2011 IADC Critical Issues Asia Pacific Conference & Exhibition, 23-24 November, Kuala Lumpur, Malaysia.