Maersk looks beyond traditional rig downtime scope, adopts data-based approach to reduce operator NPT
Initiatives launched in 2018 under a new user-centric approach focus on improving data collection, identifying patterns and increasing knowledge sharing
By Peter Emil Sorensen, Peter E.J. Andresen and Jacob Fog Odgaard, Maersk Drilling
Maersk Drilling’s ambition is to deliver operational excellence while pairing innovative technologies with new business models. The company calls this Smarter Drilling for Better Value.
Because the rig is the central hub for all activities delivered in a drilling campaign, there is real potential to improve efficiency and effectiveness for oil and gas companies.
A tangible example of Smarter Drilling for Better Value is to actively take part in removing waste from the well construction process.
The main direct sources of waste in the process are nonproductive time (NPT) and invisible lost time (ILT). Although Maersk Drilling has substantial activities targeting both sources, this article mainly addresses NPT.
The portion of time lost to NPT is approximately 20% of total time spent on constructing the well. Drilling contractors have historically focused on the portion directly attributed to rig downtime, which has been reduced to 2% to 3% over the past few years. The standard dayrate contracting model has not incentivized the drilling contractor to focus on anything else.
A Q4 2017 snapshot of rig downtime vs total NPT for Maersk’s jackups substantiates the issue:
Total rig downtime: 3%
Total NPT: 22%
The latest downturn has taught the industry that consistently losing 20% of the value in well construction due to NPT is not sustainable, and all stakeholders must contribute to reducing this waste.
To reduce or remove the remaining – and much larger – amount of waste, Maersk Drilling has engaged in several activities to understand and address the sources of NPT that exist across the well construction process. These activities are split in two, where the first helps to identify where to focus the efforts of the second:
1. Identification of specific sources of NPT through improved reporting, data collection and analysis;
2. Reduction of NPT through sharing of best practices; data-based well monitoring and advisory tools; and close cooperation with other stakeholders onboard the rig.
Although there are good examples of well operations where both of these activities have been in focus, these have been discrete efforts and not institutionalized. As a result, they have not provided the opportunity to leverage the knowledge gained on a larger scale.
In this article, Maersk Drilling offers its perspectives on how NPT can be identified and removed in a much more effective way.
2018 initiatives
Several initiatives have been introduced in 2018 to reduce customer NPT, and Maersk’s approach is outlined in Figure 1 (below). It illustrates what have been the traditional focus areas of a rig contractor and, more importantly, the areas that are being studied more extensively.

Maersk Drilling’s ambition is to enhance its position as a key partner and differentiate itself in the market by being structured and proactive, as well as actively showing that it cares about what has typically resided outside the drilling contractor scope
There is not one single solution to the challenge of reducing customer NPT. Attacking it from different angles by either collecting or building incremental data and increasing knowledge has been chosen as the best possible approach.
The Maersk Drilling “customer NPT reduction roadmap” consists of a list of future initiatives. Three of those initiatives that were started in 2018 are described here.
Improve data granularity and look for patterns
Like any other drilling contractor, Maersk Drilling records NPT in its daily operations report (DOR). However, to reduce customer NPT, it is instrumental to start collecting more details about the “events” that arise, such as who the service providers are and what the root cause(s) were that resulted in customer NPT. Collecting more data is expected to provide insights that ultimately will help to bring down NPT. As a first step, by the end of the first half of 2018, Maersk Drilling will make it mandatory to include underlying causes every time customer NPT is recorded in the DOR.
Further, the company will be looking at data that it already has to gain insights about the amount and share of customer NPT. It is expected that patterns will be identified, leading to insights and triggering questions that would need to be investigated further. Using statistical models is another way to enable discoveries that have not been identified previously. All of these efforts can potentially increase value for all parties involved in drilling operations.
Increase knowledge sharing on reducing customer NPT
As part of the performance management framework, it was decided that customer NPT would be anchored as a specific KPI on which to measure the operational teams. It has been learned from previous years that if performance measures are established to drive behaviors and/or drive strategical initiatives, then a well-defined measure will strengthen the focus.
In the past couple of years, further emphasis has been placed on behaviors and how performance contracts with rig teams can drive even stronger safety performance, operational performance and customer satisfaction.
The Quarterly Customer Satisfaction survey is already strongly embedded in the performance matrix, and the addition of the “customer NPT” KPI gives even more weight to customer-related performance.
The approach in 2018 has been to get the most learnings out of both NPT events that were prevented and NPT events that occurred. Since 1 January, rig teams have been requested to share “one pagers” to document established ways to prevent NPT, as well as to capture and share within the organization how more can be learned from the NPT events that are faced.
The expectation is that customer NPT can be reduced if more data is collected and by spending more time on studying the data. In addition, everyone in the organization must learn from each other. Sharing best practices, which is part of the Plan-Do-Study-Act approach, has proven to be a successful way of learning from processes and improving performance.
Reducing downhole NPT: A practical example

A large portion of NPT is attributable to downhole problems. Used correctly, some of the thousands of data points produced every second can provide greater insight into the behavior of the well through better visualization and by applying advanced analytics.
Objective
The driller has a key role to play in reducing the oil company’s losses from downhole NPT. Therefore, the focus has been to optimize the flow of information to that role. The objective is for driller to be able to identify downhole problems as early as possible and intervene before the problems escalate.
Ground rules
Two important ground rules have been applied throughout the project:
1) The system has to be autonomous and require no input from the driller. This means that the system will recognize the current operation and show only the information relevant to that operation.
2) The system must be based on what information can be gathered from the rig’s own sensor data, thus avoiding reliance on input from third parties. Certain applications, such as hookload development, can be augmented by adding torque and drag modeling data.
Better visualization
When irrelevant information is removed from the driller’s view, the important information becomes more visible. The automatic rule-based segregation of data enables the system to show only relevant data to the driller.
Dynamic alarm bands are applied to the data, reducing false alarms and supporting the identification of anomalies.
Advanced analytics
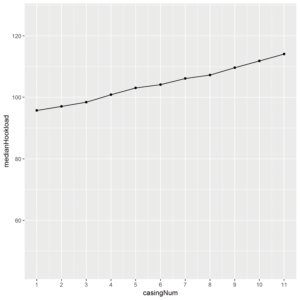
By using advanced analytics, including artificial intelligence, tools have been provided to the driller to show what “good” looks like and provide context to the presented data. Artificial intelligence is used to predict the near future, based on learning from history. Examples are:
• Flowback on connections – The driller will know what the flowback curve should look like when they turn off the pumps.
• Return flow vs pump rate – The driller will know how the return flow should behave when changing pump rate.
• Hookload development – The driller will know how the hookload should behave while tripping in or running casing. Because data is available from when the drill string was at TD, it enables a prediction of how the hookload should develop when running casing, by correlating the hookload developments. This is done purely based on collected data and without applying a physical model.
Challenges
Similar tools are already provided by third parties. While fairly advanced, these tools are often different from contract to contract and from rig to rig, and the interface is rarely designed with the driller in mind. As a result, it was decided that the tools would be designed in-house in order to enable a consistent roll-out across the fleet.
The project met several challenges, largely related to data access and handling. Most of the sensor data was not originally designed to leave the proprietary systems, so even mapping has been a huge task.
Once data is extracted from the system, it has to be stored where it can be accessed for analysis. With Maersk Drilling’s rigs producing approximately 20 trillion data points per year, a cloud-based solution was necessary. Surprisingly, building the artificial intelligence engine was not amongst the biggest challenges.
The largest challenges were:
• Data collection from proprietary systems;
• Access to data through third-party firewalls;
• Storage of data offshore;
• Transmission data from offshore through firewalls;
• Storage of data onshore;
• Translating a large amount of historical data into understandable data for machine learning purposes; and
• Mapping and sorting of data.
Next steps
The database with detailed NPT information is already increasing in size, enabling a stronger focus on NPT pain points and close cooperation with oil companies on the reduction of those pain points.
The focus will, therefore, be on maximizing the value of the gathered reporting data and either implementing advanced analytics-based tools or cooperating closely with other stakeholders onboard the rig, targeting the largest NPT pain points. DC
This article is based on a presentation at IADC World Drilling 2018, 19-20 June in Copenhagen, Denmark.