Lifting guide: Hoist safety tips every rigger, operator should know
Pre-operational checks, attention to lifting capacity, proper rigging all help to reduce incidents
By Peter Cooke, Columbus McKinnon
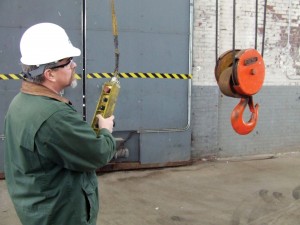
All too often, hoisting-related accidents in North America could have been prevented simply by properly training operators on the operation, safe rigging, inspection and maintenance procedures of the hoist. Training of equipment operators isn’t just the smart thing to do; it’s a requirement. Training should not be looked upon as an additional cost but as a means to reduce overall costs by reducing the number of injuries and product malfunctions, as well as increasing productivity. Whenever there’s a lifting task, the job should be done right, from the initial inspection to the end of the lifting operation.
PPE Requirements
Before starting a lift, all PPE normally required for a work area should be used, including eye, hand and/or hearing protection. In addition, any time a load is lifted higher than 5 ft, there is a greater risk of a head injury. This can be minimized by wearing a hard hat. Others involved in the lifting operation, such as riggers and spotters, should also wear head protection if the load is to be lifted 5 ft or higher.
Pre-Operational Checks
Operators should perform a pre-operation inspection and preparation procedures to identify potential problems, prevent accidents and enhance the safety of the work environment. For hand hoist and lever tools, consult ASME B30.16 (underhung hoist) and ASME B30.21 (lever tools). Make sure the hoist is not tagged with an out-of-order sign.
Next, a visual inspection of the hooks, chain, wire rope or synthetic straps should be performed. Check for broken wires, damage to chain such as cracks, nicks, gouges, wear and stretch, kinks, twists and latches on hooks for proper function. Per ASME B30.16, all hoists must be equipped with a safety latch that is working properly unless the application makes the use of a latch impractical as determined by a qualified person.
It should also be checked if the hoist is properly reeved. All warning and safety labels must be present and legible. Make sure there are no signs of oil leakage on the hoist and on the floor beneath the hoist. The work area should also be clear of any accumulation of materials to prevent tripping or slipping. Additionally, check for poor lighting.
After a visual inspection, test-run the hoist with no load. Run the hoist all the way up and all the way down. If any unusual sounds can be heard coming from the hoist, report it immediately and tag the hoist out of service.
Be sure that the hoist stopping distance is normal and there is not excessive drift. This can be accomplished by lifting a light load, use 50 lbs/load bearing parts of chain (reeving) for hand hoists and 100 lbs/load bearing parts of chain for lever tools. This will ensure the brake is operating properly.
Safe Operations
Two prime causes of accidents are overloading and poor rigging, so attention should always be paid to the hoist’s lifting capacity. Under no circumstance can the total weight to be lifted exceed the hoist’s capacity. Further, never lift a load where the weight is uncertain. Load weights can be found in manufacturers’ catalogs, drawings, bills of lading, steel manuals or labeled on the load itself. Weight can also be obtained using a dynamometer, crane scale or weight scales.
If there is no other means to determine the weight, it can be calculated. Consult a rigging handbook or engineer to help determine and calculate the weight of an object.
The hoist’s constraints should also be well understood. Pay attention to the pull to lift full-load values. Each hoist is designed to lift under the power of one person. It should not take two people to pull on a hand chain or lever arm, nor to put an extender on a lever tool (cheater bar). This is a sure sign the hoist is overloaded.
If it takes 58 lbs of pull force to raise 1 ton, any pull force over this value will overload the hoist. Consult the manufacturer’s specifications and train the equipment operators on what each pull force should be. Many US hoist manufacturers (and some manufacturers outside the US) offer overload protection devices for hand-powered hoists, either as standard equipment or as an added-cost option. This device protects the user, the overhead structure and the hoist from an excessive overload condition.
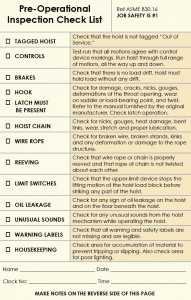
Several hoist manufactures use a friction-type, clutched hub as a part of the hoist’s chain wheel or lever arm. When the pull on the lever or hand chain is great enough to slip the clutch and prevent the load from being lifted, the operator becomes aware that the hoist is overloaded.
Rigging Safety
Use proper rigging techniques when lifting loads. Rigging training for the operator is important. Rigging handbooks and proper equipment should be readily available to ensure a safe lift. If there is any doubt about the safety of the equipment or lift, stop the hoist, lower the load and report the condition to the supervisor.
Conduct all lifting operations so that no one will be injured if there is an equipment failure. Use proper hand signals and communication with all workers involved with the lift. Pre-planning a lift with everyone involved will ensure proper equipment and personnel are in place.
Safe Rigging Practices
The following is a review of very basic safe rigging practices:
- When rigging, make sure the load hook and the upper suspension form a straight line.
- The chain or body of the hoist should never come in contact with the load.
- Never tip load hooks.
- Always use a sling or lifting device to rig around loads, and use engineered lift points for attachment.
- Never work under suspended loads or lift loads over people.
- Never lift people with a hoist.
- When leaving the hoist unattended, land any attached loads.
- When the job is complete, place hoist or hook location in a place that will not interfere with the movement of people or materials.
When you’re at the controls of a hoist, you’ve got a lot of responsibility in your hands. Your co-workers are counting on you to use skill, good judgment and common sense.
This article is based on a presentation at the 2012 IADC Lifting & Mechanical Handling Conference & Exhibition, 18-19 July, Lafayette, La.
Great read, thanks for sharing. I agree with you, it’s very important to check all the machines before starting them. So many accidents can be prevented if you ensure that everything works properly in the first place. I am going to share this with my nephew; he’s in the construction industry!
I thought it was interesting reading, “Training of equipment operators isn’t just the smart thing to do; it’s a requirement.” I’m glad to hear it’s mandatory, those machines can do a lot. I’ve always thought it would be cool to learn how to operate a crane. Is there a lot of training that goes into it? Thanks for sharing!
I’m a little surprised that most accidents when lifting loads are caused by lifting loads that are too large. It should be painfully obvious to any operator that it is a bad idea to lift a too heavy load. The only solution to this problem that I can think of is to make sure operators are continuously trained on safety practices.