By learning to better leverage the power of data, industry can turn drilling from art into science
Standards for rig control interfaces will be required, and likely driven by operators, for industry to fully exploit potential of software, analytics, automation
By Linda Hsieh, Managing Editor
Randy Mutch is VP of Wellsite Technology for Ensign Energy Services.
What are the major challenges facing our industry today?

Often we hear about the “great” crew change. This describes a shift from an older generation of drillers, more used to mechanical rigs and drilling through experience and intuition, to a younger generation of both drilling engineers and rig hands who are far more comfortable with technology and data, and who understand and are looking for more automation. A critical challenge will be how our industry manages this handover without losing a lot of the older generation’s tacit knowledge.
Another major challenge is continually improving performance and safety, which isn’t new. Today, however, we’re looking at making some fairly dramatic shifts in the drilling industry by leveraging technologies that have been developed in other industries.
Drilling is a complex business, and it doesn’t yield easily to analysis. There are a host of challenges you don’t see at a chemical or automobile manufacturing plant: It’s happening a long ways away, the instrumentation is unreliable, and the conditions are poor. With drilling, there are a lot of built-in challenges in terms of even understanding our operations, particularly when the data is anecdotal.
Is automation a part of the solution?
Without a doubt. With automation, we won’t have to rely so much on the knowledge that is in the driller’s brain. Instead, we can use both information technology and automation to augment the driller’s capabilities to create a safer, more consistent and more efficient workplace. For example, a driller making up a joint of pipe may be exceeding or falling below the recommended torque; his ability to manually hit a precise makeup torque is not perfect. We get far more accuracy using sensors and instrumentation, where all the driller has to do is push a button. You also reduce the potential damage to pipe threads and, ultimately, to drill pipe failure.
Another example is hoisting the pin out of a tool joint when the driller is making a connection. The driller is trying to compensate for the changing height as he’s pulling out of the box, but if he uses a little too much strain, he’ll put 20,000 or 30,000 lb of tension into the connection. When it pops out, thread damage can potentially occur. If you’ve automated the connection using accurate information about position and load sensitivity, then you can hoist out or stab in more precisely and smoothly and with a lot less potential damage to the threads.
So, automation is not just about improving safety and performance but also about preventing equipment damage and failure.
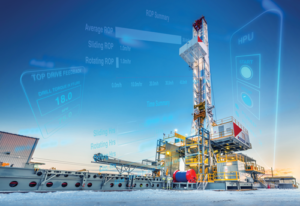
It sounds like you’re saying we shouldn’t rely so much on the driller’s experience. But one of the first things I heard when I joined this industry was that drilling is an art, not a science. Do you think that perception is changing? Is the industry now taking a more scientific approach to drilling?
I think that perception is changing quite rapidly. Early in my career I spent a lot of time in the field, on the brake handle as a driller and later as a wellsite foreman. For the past 20 years I’ve been in computer technology. People like to believe that what they know is special and can’t be reproduced, but I can tell you that a lot of what drillers think is intuition can be measured, predicted and controlled through technology. We will solve the easy problems first through application of technology and increasingly bootstrap our way up to more challenging and complex problems. I do not underestimate the capability of technology to do a better job of managing the drilling process.
As an example, consider drilling fluid. A good driller can look at or smell drilling fluid and get a sense of its health. You can get a feel for viscosity by the way it slips through your fingers. Good drillers attend to the drilling fluid. They visit the shale shaker and look at the cuttings. They look at how their pipe is moving when they make connections, how much friction there is, how much difficulty there is to break circulation. The driller’s brain is taking in a lot of information, so I understand the argument that it’s an art.
But it doesn’t necessarily have to be. If you can detect this information at a sufficient level of detail and accuracy, you can identify potential hydraulic- or fluid-related problems as they develop to make the right recommendation to avoid lost circulation or a kick. I believe that much of this can become a science.
Do you think the industry is accepting the power of data and how it can improve drilling?
I think that acceptance happens quickly if you have a compelling case to prove that you’re saving real dollars. Look at how bit technology has evolved. We’re drilling three or four times faster using bits that were developed with the use of very sophisticated data analysis.
In some cases, the challenge is the lack of reliable data to demonstrate the impact of the technology that’s being developed.

Is it hard to find the right data to capture?
It varies. For pipe handling, it’s not hard. Right now we’re capturing great data when we’re rotating and hosting pipe, and we’re very closely measuring tripping and connections to understand the process. Other areas don’t yield so easily to analysis, like moving a rig, nippling up BOPs or pressure testing, because there just isn’t a lot of good data. You almost have to put video cameras out there to monitor those complex operations because there are hundreds of variables involved.
How do you see the drilling rig itself evolving over the coming years?
A drilling rig is a costly, almost custom, machine with a long life span. Not many get built every year, so evolution in the construction cycle is slow compared with other industries. I don’t think you’ll see a revolutionary new rig take over the market in the next five years.
For me, the real potential for change is around software, data and data analysis. I firmly believe that we can take our existing rig fleet and improve its performance without having to spend millions of dollars replacing equipment. If we can appropriately instrument the rig, measure and control it, we can get a lot more productivity.
You spoke last September at the IADC Advanced Rig Technology Conference about the need for more standards. Is it your belief that standards will help to accelerate technology adoption in our industry?
Yes, I believe that. There is already work going on in both IADC and SPE around the controls interface on a drilling rig. The industry needs the ability to take third-party packages – drilling optimization, for example – and safely and cost-efficiently integrate them with rigs controls. We have had experiences where our customers wanted to put innovative technology on a rig, but the project was defeated simply on the expense of custom integration. Having a standardized interface is really important.
Are you saying that drilling control systems shouldn’t be proprietary technology?
They will be proprietary because that’s always going to be a form of competitive advantage. I’m saying they need to be able to talk to and play well with each other. Think of printers and how you used to have to install a specific driver to set up the printer. Now they have universal drivers, which takes away a lot of the setup and complexity for the user. That’s where we need to get to with the drilling rig, where different components and different software packages interface relatively easily with rig controls.
Do you see that happening with some of the software and systems being developed now?
I think there’s agreement that it should happen, but there are also competitive pressures pushing in the other direction.
I believe that control interface standards must be driven by operators because they’re the ultimate beneficiary. It might not be a traditional role that you see filled at an energy company. They have operations people, drilling engineers and geologists, but not necessarily people who specialize in data definitions and interface standards. That’s starting to evolve, however, and we’re seeing more engagement from operators around the need for open standards.
Do you see more recruitment of employees with the types of skills that you referenced, perhaps software or data engineers?
It’s a tough sell, particularly on the contractor’s side because traditionally we hire hands-on guys or mechanical engineers. But I will say that the new generation of workers coming in already has a very different approach to data management and analytics. They’re aggressive.
With all the work that contractors are doing to improve efficiency, do you think their business model should shift toward a more performance-based model?
I absolutely do, and practically speaking it’s already happening, for several reasons. The first reason is personnel. Operators had hired a lot of smart, young engineers when times were good, and they wanted to retain those engineers through the downturn. Rather than letting the best and brightest go, they put them in the field as drilling optimization engineers, monitoring drilling performance.
The second reason is that people are really looking at data now. The tools for processing data have improved exponentially. Even on a standard desktop computer you can now run fairly sophisticated statistical analyses on large data sets. You get results quickly, and you can visualize them. It’s really exciting because it allows us to see patterns we couldn’t easily see before.
In terms of how performance-based contracts work, how can they become sustainable if the performance target is always moving?
It’s tricky, and it will vary by customer. In one instance we have a customer who works with us to set the targets. They involve the rig manager and even the drillers to review our best well and our average, then ask us what we believe we can achieve on a specific operation. This gives us skin in the game because we weren’t simply given a target; we had a real role in the process.
I believe that’s a successful way to approach performance-based compensation. You start by measuring your performance, and then expose those measurements to the people that actually impact performance. It’s critically important to keep communication going with the rig hands.
Ensign started the Edge Analytics project in 2015. Can you talk about the benefits that you’re seeing?
The Edge Analytics package is helping us in many different ways because it can inform all aspects of the drilling process. It helps us improve on-bottom drilling by looking at ways to optimize rate of penetration by making adjustments to RPM and weight on bit. It also helps with flat time reduction by helping us to understand and measure those non-drilling processes more precisely.
Then, we can use this knowledge to reduce nonproductive time, which encompasses well problems like lost circulation or stuck pipe. These problems often account for 5% to 10% of a well, and I think they can be better managed or even avoided with the use of good data. Equipment failures also lead to nonproductive time. Especially with top drives and drawworks, probably the two most critical pieces of equipment, we want to ensure that we don’t have unplanned failures.
How are you using data to predict failures?
You look at sensor information from the equipment. With bearings, for instance, you can measure changes in vibration. You can also look at heat signatures or at the power that a piece of equipment draws. Many of these sensors are built into the gear, so if the data is used properly, you can predict an upcoming failure with some confidence.
There’s also work being done in areas like sonic signatures. Old-school drillers would hold a screwdriver or wrench up to their ear and set it against the pump to listen to the “guts” of the pump. A good rig hand can actually hear and detect a liner or piston beginning to wash.
Now consider using a microphone or audio sensor feeding high-frequency data into a system that can absorb and analyze it. The system is doing the same thing that the driller did but with more precision, accuracy and frequency. We’re just scratching the surface in this area.
Can you give me an example of how Edge Analytics has been used to improve equipment management at Ensign?
We experienced brake failures on a certain class of drawworks more frequently than predicted by the manufacturer. We used our analytics to discover the problem. It turned out that the way the systems had been programmed, the brakes automatically set more frequently than expected. In other words, the brakes were cycling more often than predicted, which meant they weren’t failing prematurely at all. They were just doing the work in 12 or 16 months that we thought would take 24 months.
The analytics allowed us to understand our choices. We could do maintenance on those particular components more frequently, or we could change the programming. Once you have the data, you can start to make better decisions.
Does all the data that’s collected go to a central repository or is it analyzed on each rig?
We stream all the data to a central database in real time. We’ve also set up systems that store data locally on the rig so it can be reviewed independently by the rig manager, or a mechanic or electrician traveling to the rig. We’re not currently making minute-to-minute decisions remotely; the actual data analytics and reporting is done periodically offsite. Over time we’ll be looking at ways to move some of the analytics to the wellsite and to do it in real time.
Are your customers asking for access to this data, and how are you addressing such requests?
They are, but we’re proceeding cautiously. We certainly want to work with our customers and share the benefits and value, but we also must understand the implications and risks of data sharing. As the amount of data available increases and the possibilities multiply, our industry needs to look beyond the traditional contract for language that will protect both the operator and contractor. Data sharing is not straightforward, and the contractual relationship between operator and contractor must be redefined before data can truly be shared. DC