Innovations allow rotary steerable technologies to push new boundaries
Automated well trajectory control, component simplification and knowing when to ease up on ROP are all helping to prolong bit runs
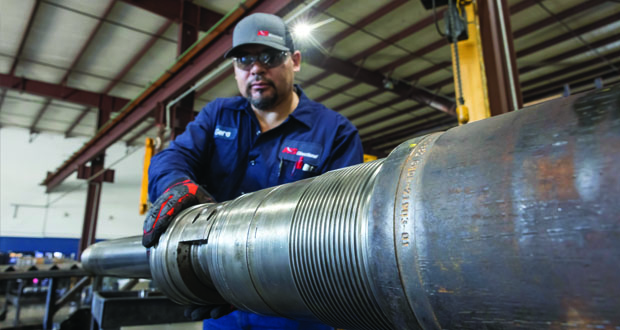
By Stephen Whitfield, Senior Editor
Over the years, rotary steerable systems (RSS) have advanced and evolved into a valuable tool for maintaining high hole quality and fast ROP while drilling through curves and lateral sections. This has been important especially as operators continue to push the lengths of lateral sections in their drilling programs. For service providers and directional drillers, this means that advancing the capability and reliability of their RSS tools in order to meet operator demand is paramount. Providing downhole electronic components that can better withstand high-pressure, high-temperature environments is one such priority.
“In the end, it’s all about ensuring better drilling performance, superior wellbore quality and the best well placement,” said Lei Fang, Global Product Line Director – Drilling Services at Baker Hughes. “Those have always been very important to RSS providers. If you look at the market today compared to five to 10 years ago, there’s been a tremendous amount of change. Drillers want to drill faster, the laterals have become much longer, and more and more BHAs are motorized. In response, you have to ruggedize the design of the BHA to handle the loads needed to drill at these speeds and distances.”
Another focus area for improvement is ensuring RSS tools can stay even longer in hole. By using new techniques to push the bit downhole and removing traditional mechanical components that can become potential points of failure, a more simplified system can be achieved. Simplification can also act as a means to mitigate the potential wear and tear of drilling at longer distances, as well as remove the components that could add to the cost of utilizing RSS.
“There is a potential to expand the market even further, and that’s what I’m really excited about,” said Andrew Law, CEO of Enteq. “Everyone gets excited by the technical wins that RSS enables – the big one-run laterals, the lengthy extended laterals. But the commercial wins – making these tools available to companies that could achieve a benefit using rotary steerable where they wouldn’t normally – that’s what gets me excited.”
Finding the right tools
From a directional driller’s perspective, RSS tool selection is critical for helping customers reach their targets. And figuring out the best ways to utilize those tools is key to drilling longer laterals while minimizing the number of trips needed, or even eliminating trips altogether in a given section, according to MS Directional, a subsidiary of Patterson-UTI. MS Directional has strategically partnered with third-party manufacturers on its RSS tools, and the company utilizes its own communications system, Mercury RT, to connect the RSS to the surface control systems that drillers use to steer the tool.
The company now runs RSS on “just about every job,” said Cody Permenter, Directional Coordinator. “We’re seeing longer lateral lengths and more difficult targets, and that’s driving up demand. As long as you don’t drill at too high of an ROP, you can drill for long lateral distances without wearing out the tools and having to trip again. That’s a big advantage.”
Mr Permenter also pointed out the importance of prioritizing bit placement and steering over pursuing faster ROPs in helping to achieve longer one-bit lateral runs. “Overall, average ROP is still going to be better if you’re drilling more conservatively than if you’re not. If you’re setting a record pace for drilled feet per hour one day but then you have to trip again because you’ve worn out your tools, how effective are you really drilling? If you can be more aggressive, then be more aggressive, but if you see shock and vibration, and the hole is telling you that you need to slow down, backing off and getting decent ROP is preferable. If you’re off bottom, you not making any ROP at all.”
MS Directional is also constantly in talks with its vendors, relaying concerns from the field and looking for tools that can help mitigate those concerns. For example, a common concern is how to drill curves consistently. Operators are looking to reach targets that require more high-severity doglegs, and the current tool offerings have not enabled them to steer the RSS through those doglegs consistently enough.
“That’s really the only thing that’s lacking from what the operators want,” Mr Permenter said. “There are some tools out there that the companies say can do it, but we don’t know what the success rates are. When we’re talking to a client, they’re going to ask us, for instance, if we can drill certain severity of doglegs. Yeah, on paper we can, but they want to see the tools and the data. Have you seen success? What worked? What didn’t work?”
Automating trajectory control
Baker Hughes first started developing RSS tools in the late 1990s, and the latest addition to its portfolio, the Lucida RSS service, has been available commercially since 2020. It includes an integrated BHA with both a customized bit and a proprietary interface between bit and drilling BHA, designed to maximize ROP and reduce wellbore tortuosity. The BHA also features near-bit, 16-sector gamma ray sensors that help gather real-time downhole data for geosteering, as well as multi-chip module electronics that are designed to withstand temperature up to 175°C.
“There’s a higher temperature element that’s coming with some of the wells we see now,” Mr Fang said. “If you look at a place like Saudi Arabia, for instance, the gas wells there need equipment that’s going to withstand higher temperatures. So, having electronics that can do that is huge for ensuring the reliability of the system.”
Lucida’s automated well trajectory control system integrates azimuthal and inclination hold modes with continuous proportional steering to automatically correct wellbore trajectory for formation trends. The service also includes near-bit sensors that measure downhole weight-on-bit, torque, bending moment and direction. Accelerometers measure axial and lateral vibration, as well as high-frequency torsional oscillations. The real-time bending moment and direction measurement capabilities can enhance directional control, Mr Fang said, and can help with stringer detection.
In 2022, the Lucida service enabled an unnamed operator to set a single-run record in the Permian Basin, drilling more than three miles in three days.
Baker Hughes was tasked with helping the operator drill a curve and a long lateral in one run, as the driller wanted to avoid the downtime and costs of swapping out drilling tools to finish the curve. For the run, Baker Hughes used a BHA comprised of the Lucida service, its DuraMax motor, the Dynamus extended-life drill bit and a high-frequency torsional oscillation dampener to minimize BHA tool failures.
Using that BHA, 16,666 ft were drilled over the course of three days – 5,078 ft on Day 1, 6,091 ft on Day 2 and 5,497 ft on Day 3 – saving more than a day in planned drilling time while delivering a high-quality wellbore.
“When you’re talking about drilling a three-mile lateral in less than three days while achieving a the dogleg severity of less than half a degree per 100 feet, that means you’ve shown a fantastic combination,” Mr Fang said. “You’re showing the reliability of drilling a long lateral with a high ROP without going off target, and you’re showing the accuracy of your system in consistently calculating where it needs to steer. When you achieve all of that, you’re getting a quality wellbore.”
The Lucida system has also helped to drill long laterals in single runs offshore. For a well offshore Norway in 2022, Baker Hughes was brought on to assist with the drilling of a long
8 ½-in. lateral section with a 270° turn from a whipstock exit in a single run. Other goals included eliminating anticipated whirl in long tangent sections, identifying calcite stringers and adjusting operational parameters to improve ROP.
Baker Hughes deployed a remote operations service for the well. The BHA included the Lucida service, with automated well path trajectory control and continuous proportional steering. It also used a five-blade Dynamus extended-life drill bit, which is designed to optimize ROP in long laterals containing stringers while reducing trips and BHA vibrations. The i-Trak automated stringer detection and mitigation service, which quickly adjusts drilling parameters to improve drilling efficiency through stringers, was also used. With that assembly, a 21,732-ft bit run in the lateral section was achieved, which was the longest to that date.
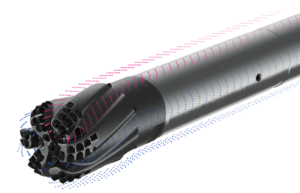
Alternative to conventional RSS
Enteq is offering a newer entry to the RSS market. Over the past five years, the company has been developing its SABER (Steering At-Bit Enteq RSS) tool, which uses an internally directed pressure differential system to steer from the drill bit face.
Most commercial RSS are either “point-the-bit” systems, which means that they change direction by bending the main shaft running through the bit, or “push-the-bit,” meaning that they use pads on the outside of the tool to press into the wellbore and change direction. The SABER tool does neither. Instead, it creates and controls a system of high-velocity and low-velocity fluid flow at the base of the bit, which creates high-pressure and low-pressure zones. These fluid forces can then change the direction of the bit.
The tool is based on a fluid dynamics concept published by mathematician and physicist Daniel Bernoulli in the 1700s, which states that pressure in a fluid decreases as its velocity increases. It’s the same principle that explains how an airplane can stay in the air.
“When you compare this to other RSS tools, we’re not using any mechanical means to push the bit,” Mr Law said. “We’re just controlling the flow, but by doing that you can generate the same forces as you get with a conventional RSS. Just as you can use pressure differentials with airflow to generate lift on the wing of an airplane, we can use pressure differentials with fluid flow to generate movement with the bit.”
Enteq is marketing the SABER tool as an alternative to conventional RSS, as the pads and pistons external to the collar of a typical “push-the-bit” system have been removed. These pads and pistons are typically subject to extreme wear and tear in a traditional RSS offering, Mr Law said.
“The main thing with SABER is that we don’t have all of the mechanical pieces you see in an RSS. If you look at any RSS tool, you typically have brackets pushing out against the formation. There’s a generator providing power, then you have a control system, then you have the brackets pushing against the formation. Now, all you have is an internal valve inside that bit. There are zero external moving parts, which means it’s a simple system with fewer points for failure,” he said.
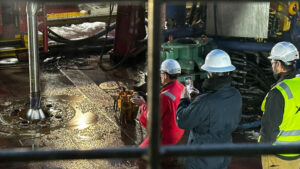
SABER originated from an unrelated Shell research and development project in which the operator discovered that a plugged nozzle in a drill bit created differential pressure that could lift a block of rock. Following an investigation of the anomaly, Shell carried out a proof of concept on the possibility of using imbalances in pressure as a means of steering the drill bit. That led to the development of a rough prototype.
Enteq acquired the IP for the prototype in late 2019, then spent the next four years revalidating theoretical modeling and historic test results, as well as redesigning the prototype into a commercial system.
The removal of the pads and pistons was already part of Shell’s original design. Among the main changes Enteq made to the design was the optimization of the central bearing hanger, which includes an impeller to help minimize the amount of fluid needed to push the bit. It also incorporated an electrical generator, a CPU navigation unit, a drive force to provide rotational force and a bit valve cartridge to direct the fluid flow that steers the bit.
The tool’s design is modular, and because it has fewer moving parts than conventional RSS, it can be sold at a lower price point, making it a more cost-effective option, Mr Law said. “It’s a simple system, and it’s designed to be a versatile system. We don’t have all the complicated assemblies and mechanical bits that you see in an RSS. It’s really a few parts.”
Enteq conducted two tests to validate the SABER tool in 2023. The first test took place in March in Norway. In that trial, the tool drilled through 100 m of granite as something of a stress test – granite is a much harder rock than what is typically found in onshore oil and gas drilling. In that test, the gearbox, motor assembly and pressure compensation mechanisms all performed as intended, and Enteq was able to generate sufficient power to control the valve and steer the bit.
The second test took place in August at Oklahoma’s Catoosa Drilling Test Facility. The testing revolved around two goals: confirming the effectiveness of the steering concept and identifying operational limits.
Testing proved the tool’s ability to induce significant dogleg severity in typical downhole conditions and navigate diverse formations, mirroring a real-world commercial environment. Enteq was able to generate a build-and-drop, hold-and-change azimuth when needed to, and turn. The testing validated the tool’s suitability for the company’s target commercial applications in horizontal wells.
The tool is expected to become commercially available this year, and Enteq said it is in talks with non-major operators to bring the tool to market.
“We’re close to this tool being used commercially in the field,” Mr Law said. “You need to have a customer that appreciates this tool as an end-stage product and not just something fresh out of the box. It will definitely work, and we want companies who want to work with us. Really, we’re selecting our customers as much as they’re selecting us.” DC