Case study: Laser measurements, machine learning boost motor performance in the Permian
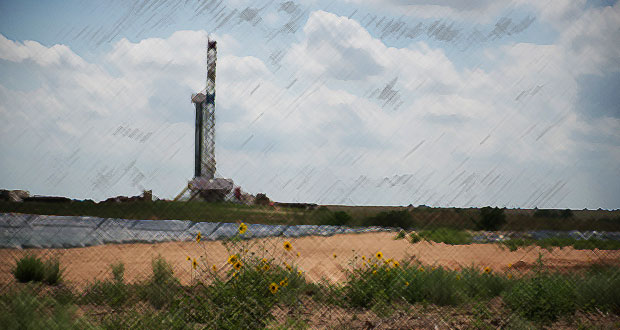
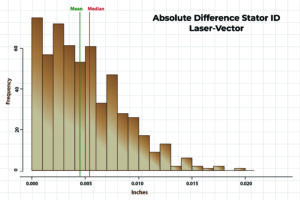
By Lonnie Smith, Turnco
An operator in the Permian Basin was having inconsistent runs caused by motors that were either not producing the horsepower expected or were failing prematurely for power section chunking. In both scenarios, the motors exhibited the same power section fit and were run in similar drilling circumstances, yet did not perform with the same consistency. To reduce nonproductive time (NPT), the operator sought to accurately measure and test its motors prior to installation.
The power section of positive displacement motors consists of an internal (rotor) and external (stator) component. When paired, they create a “fit” and maintain a critical seal at the bottom of the well. The rubber lining within the stator can swell or shrink when exposed to heat and drilling fluids. If the stator cannot handle these conditions, it will disable the power section’s ability to uphold the fit required to maintain a seal. This failure can cause the rubber lining to chunk or stall, resulting in motor failure or weakness.
Traditionally, the power section fit of a motor is determined by a vector gauge. Because so many manual measurements are required with this method, miscalculations can occur frequently. To resolve performance inconsistencies, the operator instituted dyno-testing on all motors before deployment. The additional testing proved useful, and motor run reliability improved. However, the additional testing was costly and time intensive. It also put additional strain on vendors’ supply chains as each motor had to be sent for testing prior to installation.
According to results provided by a leading dyno-testing provider in North America approximately 6% of approximately 14,400 motors failed between 2018 and 2021. A large group of manufacturers of power sections and motors were represented in this data set.
More cost-effective solution
As an alternative to the dyno-tests, the operator sought out Turnco’s Laser-AI. In November 2021, Turnco began taking measurements of stators with an inspection system laser device. Each measurement took up to 3,600 laser measurements and produced a 360° profile of the stator. These images were then stitched together into one electronic file. The 360° profile measurement gave the operator a digital log and comprehensive view of the stator, not just the ID minor (a limitation of the vector technology). After being measured, the stators were assembled onto a motor and shipped to dyno-testing.
Part of Turnco’s initial efforts included testing its data set against the dyno-test, ensuring the accuracy of its algorithm. Ultimately, Laser-AI combined each motor’s data set with supervised machine learning techniques and was able to predict stator performance on the dyno-test with greater than 95% accuracy.
As the Laser-AI algorithm evolved, it allowed the stator to be rejected with the same criteria as a dyno-test, but results were realized before the motor was built, rather than after it was assembled and shipped to a dyno-testing facility.
Results
The operator was able to modify its quality program to only dyno-test a sample of the motors, rather than every single one, reducing spend on dyno-testing by 80%. Additionally, the operator shortened its supply chain, enabling motors to go directly to the rig, saving two days of mobilization and transportation efforts. Most importantly, vector measurements were taken for each stator and compared with measurements the laser produced. It was discovered that, on average, the stator measurements were more accurate by 0.004 in. when utilizing Turnco’s method, resulting in more consistent motor performance outcomes. In 11% of instances, stators were more then 0.011 in. off or were completely out of tolerance.
Turnco’s methodology enabled the operator’s motor vendor to perform the laser measurements internally and upload files into the Laser-AI software.
Ultimately, the technology eliminated the inconsistencies in stator performance and improved NPT by rejecting motors prior to use. DC