Eni approach to business sustainability relies on improved operational efficiency, safety
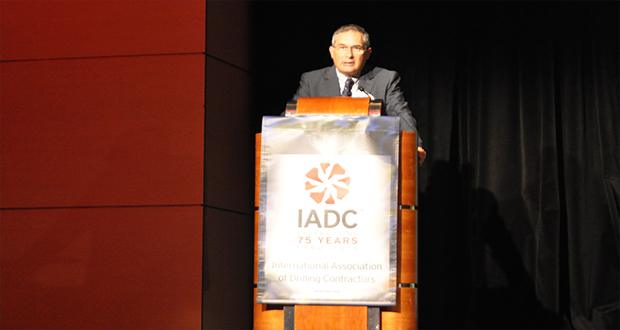
Technology and innovation is Eni’s answer to the current down market, Alessandro Puliti, Eni Senior VP of Drilling and Completions, said in a keynote speech at IADC World Drilling 2015 in Rome on 17 June. Only by improving safety and operational efficiency can the industry achieve a sustainable business model, he emphasized. “At Eni, we firmly believe that safety and operational efficiency represent the pillars for business sustainability in this environment and in the next years,” he said. “A strong R&D, advanced competence, work process, innovation and proprietary technologies are the leverages to effectively improve safety and operational efficiency.”
In Eni’s approach to well operations management, human resources sit at the core and utilize three pillars – competency, process and technologies – to achieve a safe and efficient operation. The competency piece emphasizes training, know-how and a culture of safety, while the process piece looks at factors such as organizational model, best practices and rig inspections.
A critical improvement that Eni has made in the process component is through real-time monitoring of drilling operations, Mr Puliti said. “We have dedicated collaboration rooms assisting in the real-time drilling center and two centers of excellence, which take advantage of the recent progress in digital technologies and real-time data monitoring to create an advanced work environment,” he said. “Experts from various disciplines collaborate on the most important operational aspects with a common aim of optimizing the performance in drilling and productivity worldwide.” Eni’s real-time monitoring capacity has expanded from just 16 wells in 2009 to an expected capacity for 81 wells this year.
The third component in this model is technology, and Mr Puliti noted his pride in the multiple proprietary drilling technologies that Eni has developed and implemented over the past couple of decades. These innovations played an important role in keeping Eni’s global nonproductive time on its operated wells below 10% in 2014, he said.
One of these technologies is the extreme-lean profile technology, introduced in 2000, that is based on a reduced clearance between the casing and open hole. It enables the company to reach the reservoir with a bigger hole diameter or to have an additional casing string to reach deeper targets. This, Mr Puliti said, means it’s now standard for Eni to run casing in a 14 ¾-in. borehole instead of the traditional 17 ½ in. “We have less cuttings, less rock to be drilled, less cement and more casing sizes available to reach the target and to be used as contingency or to drill deeper in difficult drilling areas.”
Five years after this, the company introduced the Eni-circulating device. It allows for continuous mud circulation to maintain constant bottomhole pressure while making up or breaking out pipe. “Drilling without interrupting mass circulation during pipe connections has been a dream of the drilling community since almost a century,” Mr Puliti said. Eni has drilled more than 100 wells using this technology and recorded more than 15,000 trouble-free connections during continuous circulation. The continuous circulation device has also provided increased wellbore stability and control of equivalent circulating density, he said.
Another innovation he cited is the Eni-near balance drilling system, which allows constant bottomhole annular pressure to be maintained at all times while circulating; this helps to manage the annular dynamic hydraulic pressure profile. The system can decrease the likelihood of kicks and stuck pipe incidents, as well as enable drilling through narrow pore and fracture pressure gradients. The technology, Mr Puliti said, has already saved Eni more than $30 million in HPHT and deepwater wells.
Finally, one of the newest additions to Eni’s toolbox is the Eni-deepwater dual casing system. It allows the operator to run and cement the conductor pipe and surface casing in a single run in deepwater wells. “Traditional techniques applied to set conductor pipe and surface casing do not ensure seabed, subsea wellhead stick-up and verticality,” Mr Puliti said. Using Eni’s system, the operator has been able to ensure perfect verticality of the wellhead and an improved cement bond. This has translated into an average reduction of two days from the drilling time for each well, according to Mr Puliti. “In a subsea operation, that’s very important. It amounts to a couple of million dollars saved per day,” he said.