Efficient management system the foundation of strong HSE culture
Changes under way in Romanian oil, gas industry to improve communications, change attitudes toward safety
By Marian Cirnat, Grup Servicii Petroliere
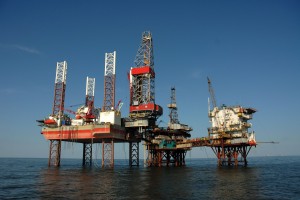
had gone more than 1.8 million manhours without an LTI.
There is a lot of discussion these days about HSE culture, but what does HSE culture really mean? Informally, it can be described as “the way we do business around here,” and a mature and efficient HSE culture means that we are doing business this way not because we are required to but because we strongly believe in what we are doing. However, is that always the case?
Romania-based Grup Servicii Petroliere (GSP) has been working since its establishment in 2004 to develop a sound HSE culture. This involved looking to IADC as a fundamental knowledge reference source. The oil and gas industry has had significant learnings over the years, contributing greatly to the development of HSE culture. International associations, including IADC, and national and international regulatory bodies also have played roles in creating a framework that empowers companies to develop their own HSE culture.
The industry has reached high levels of positive results in meeting established HSE standards, wherever drilling contractors and other oil and gas specialists carry out their activities. This objective is reached through a rationalized and fully assumed HSE culture that results in positive attitudinal and behavioral changes.
Companies say they are HSE-responsible in all activities, but how is their responsibility reflected? In applying the same set of standards; in the harmonization of incompatibilities between the company’s HSE management system requirements and local regulations; in the increased efficiency of the management systems; in the determination to apply rules and best practices even when they are not mandatory in a particular geographical area; in hiring local personnel and providing them with proper training; and in purchasing top-quality equipment/materials and constantly having the highest regards to long-term costs and benefits.
Being fully responsible means that all of these aspects are part of everyone’s responsibility toward personnel safety, and they are dealt with through a flexible and efficient management system.
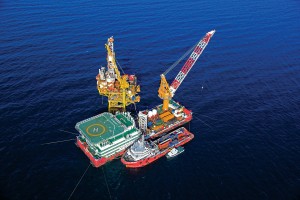
In Romania, a country with more than 150 years of history in oil and gas E&P, production was the primary focus until 1989. This led to setbacks in the HSE culture, with many people working in the Romanian oil and gas industry not having solid HSE knowledge. Further, communication and training inconsistencies resulted in cracks in a sound HSE culture.
Soon after Communism fell, access to international standards and best practices opened, including those related to HSE. This led to the development of proper HSE management systems that were capable of changing people’s attitude toward safety. Further, when Romania joined the European Union in 2007, all European directives and regulations were adopted, leading to further increases in the local HSE awareness level.
Romania has implemented efficient HSE management systems at a national level and is starting to register fundamental changes in people’s mentality and attitudes. Our HSE culture improves by the day.
There are six main components, described below, in the development of our HSE culture, and all are essential to achieving a mature and sound HSE culture as they are interconnected.
The foundation
The foundation is represented by a well-structured and efficient management system where individual and group responsibilities are clearly displayed and where communication and the relationship between various positions and organizational structures are clearly defined.
Management involvement
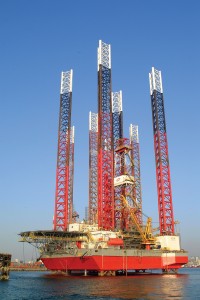
Management’s commitment and style are significant factors in the well being of an HSE management system. Without management commitment, there’s no foundation for an efficient management system (i.e., a natural, unconscious bias for production over safety, the tendency to focus on the short term and being reactive rather than proactive).
Leading by personal example
How many people have noticed a top manager or client representative being the first to cut safety short? We can’t expect employees to adhere to safety rules when management is the first to override them. Managers and supervisors have to be an example for all employees in order to strengthen the HSE management system implementation process.
Employee involvement
Employees should believe in what they are doing, rather than doing something only because they have to or because they want to please their supervisors. The best approach is to openly discuss HSE with them and get them actively involved by asking for their opinions about safety. They need to be encouraged to step forward and ask questions or come up with suggestions. Show them you care.
Asking them to do something only because it is company policy will not lead to positive results. The moment they are given the opportunity, they will revert to the same unsafe behavior they’re used to. People must understand that the HSE management system, along with all procedures and manuals, is the tool the company has provided them to have a safe working environment. It is not the company’s management system but the employees’ management system, as they are the ones using it; they are the ones who can provide precious feedback about the way the management system is working.
Without employee involvement, the management system will never be tailored to their needs. All employees have to take part in the development of the HSE management system and need to have clear HSE responsibilities.
Training, competence
Having the right people in the right place is essential in conducting safe and efficient activities. The process of choosing the right people starts from the pre-employment and employment phases. Impressive CVs mean nothing without a real screening process. A robust and continuous training program pays the effort.
Communication

Communication at all levels represents the foundation for good safety practices. Means for ensuring proper communication must be easily available. One example is the communication needed to deal with various emergency situations; this means of communications must work flawlessly and be periodically assessed.
GSP Programs
As a Romanian company, GSP has challenged its personnel’s mentality and attitude toward safety and addressed all of the factors discussed above by implementing programs and practices:
• Regular visits by managers to all work places to observe how personnel work and discuss safety matters;
• Continuous search for investment in new and safer equipment and systems;
• Leading by personal example is a concept demonstrated by every manager and supervisor;
• Creating the proper tools and environment for improving personnel’s involvement in safety: HSE observation cards, internal HSE inspections where the entire work force is involved, the “HSE Team of the Day” and “The Best HSE Observation Card of the Month,” on-site HAZID training and reward programs;
• Developing and demonstrating the “no blame policy” on a day-to-day basis;
• Continuous assessment of associated risks and corrective/preventive actions follow-up;
• Investigation of all accidents/incidents and communication of safety alerts and lessons learned to all personnel; and
• A proper screening of all new employees and their periodical training, both professional and HSE.
After more than four years since GSP implemented the change process of the existing HSE culture, the results are now visible:
• People are reporting any unsafe or positive act and/or situation they notice and taking immediate corrective action(s) where required to prevent any undesirable events from occurring;
• People are coming to management with suggestions for improving the level of safety at their work places;
• People are proactive rather than reactive;
• Personnel are performing the inspections they are responsible for and taking immediate corrective action(s) when needed;
• People are actively participating in periodic safety meetings and safety campaigns;
• People are actively participating in task risk assessments during dedicated toolbox talk meetings;
• Front-line supervisors are starting to understand their leadership responsibilities in terms of safety and acting accordingly;
• Letters of satisfaction have been received from clients with good scoring for the company’s HSE achievement; and
• Excellent accident-free records.
This article is based on a presentation at the IADC Critical Issues Continental Europe 2012 Conference & Exhibition, 23-24 May, Bucharest, Romania.