Drilling supply chain pressures mount amid pandemic disruptions
Drilling contractors emphasize risk management and enhanced communications to ensure operational continuity across rig fleets
By Stephen Whitfield, Associate Editor
The global outbreak of COVID-19 has wreaked havoc on the drilling business, with an oil price crash and lower activity levels leaving drillers with a difficult landscape to navigate. However, despite operators’ pullback and limitations placed on people’s movement, many drilling sites remain active around the world. Regardless of the pandemic, those projects still need equipment and personnel to ensure continued safety and performance.
- Risk management has become highy critical as companies assess potential for supply chain disruptions.
- Companies must prioritize shipments and evaluate options for transporting goods to rig sites amid limited flight availability and increased travel restrictions.
- Extra precautions are being taken to ensure adequate stocks of food and cleaning supplies on rigs to protect the crews.
On a surface level, supply chain management has not been significantly affected by the coronavirus outbreak. Representatives from several drilling companies told DC that they have prioritized continuity, but the shift to work-from-home has not impacted their ability to keep in touch with suppliers. The threat of disruption remains, however. In the weeks since many countries began implementing stay-at-home orders, supply chain teams have worked in overdrive to make sure that they understand emerging risks.
“This is above and beyond the typical risk assessment trigger,” said Jeff Thomson, Director of Supply Chain at Vantage Drilling. “This is the ‘what if this happens, and then this happens, and then this happens’ and so on to the Nth degree. This is affecting the world on every level possible. You can’t assess risk against that. The ramifications of these events will forever transform our industry and those who survive it.”
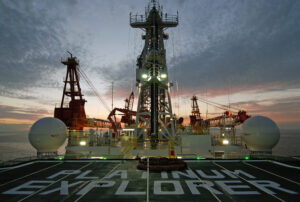
Mr Thomson said there is still a lot that drillers do not know about the virus that could have significant impact on supply chain management, like how long the virus can live on a given surface and how long a human carrier might go without showing symptoms.
That uncertainty has led supply chain teams to consider possibilities that it would not need to consider under normal conditions. Greg McGavin, VP of Global Supply Chain at Seadrill and Chairman of the IADC Supply Chain Committee, said that the biggest risk his team faces is having a critical supplier shut down operations on short notice due to COVID-related issues, either internally or due to outside influence.
“This is a risk that, from the day-to-day perspective, we would generally not have considered pre-COVID because we have strong suppliers on whom we have performed due diligence prior to any orders being committed to them,” Mr McGavin said. “Now that COVID’s kicked in, we’re worried they can suffer the same physical consequences that any of us can. Somebody in a facility could get infected, and that gets the facility shut down, or the facility is shut down due to them being defined as ‘non-critical.’ If that occurs, it could put something onto a critical path that we would never have considered before.”
The threat of disruption means that Seadrill has started to engage with its list of core suppliers on a far more frequent basis – these are the companies that it relies on most often for equipment, inventory and services. Seadrill then assesses the chances of those suppliers potentially being impacted by COVID-related circumstances, such as understanding if a supplier’s warehouse/supply or storage facilities are located in a high-risk country. If those suppliers are defined as being potentially at-risk, Seadrill then examines ways to mitigate the impact of disruption, either by raising inventory levels for critical equipment and materials or by sourcing from other vendors where possible.
“We had to identify the suppliers we absolutely depend on to keep the fleet running,” he said. “The companies we go to all the time, are they at risk? If so, what are we going to do to ensure that, if there is a disruption, we have coverage and access to those items that we’re buying from them?”
Understanding risk
In April, Wood Mackenzie released a report outlining supply chain risk in the wake of COVID-19. The report established two fundamental challenges for suppliers in the upstream sector. First, service providers are in much worse financial shape than during the 2014-2015 oil price downturn. Secondly, COVID-19 has disrupted the supply of manufactured equipment and the ability to transport service personnel across borders.
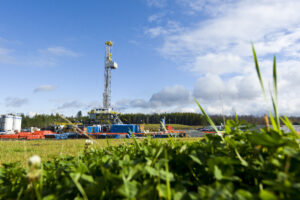
“It should come as no surprise that the biggest challenge in the wake of this outbreak is logistical,” said Joel Shibley, Global Supply Chain Manager at Helmerich & Payne (H&P). “The equipment and services required by our operations are not in short supply, but the ability to get them to the wellsite can be impacted. This is especially true for our international operations.”
In its report, Wood Mackenzie advised the industry to take a “structured and thorough” approach to building resilient supply chains. To that end, a resilient supply chain must be supported by clearly defined governance structures and processes, as well as operated and managed by appropriately trained and capable human resources utilizing technologies that enable those strategies, the report stated.
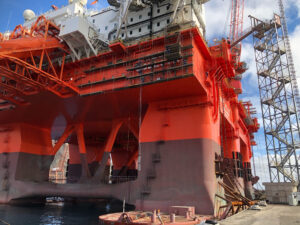
While Wood Mackenzie’s report was aimed at operators, strong management systems and operational discipline are also at the heart of drilling contractors’ responses to supply chain risk.
Bryan Collins, President of Drilling Operations at Parker Drilling, said the company’s IADC-audited competency program was critical in helping Parker to establish a baseline in training personnel on risk management.
We are an operational execution company,” Mr Collins said. “It’s how we do things. Procedural discipline and competency are two very large components of that execution, so this is right up our alley. We look at something like this no differently than we would an emergency response plan.”
Wood Mackenzie said the forecasting of supply chain risk in the case of a severe event, such as the COVID-19 pandemic, requires specialized capabilities.
When it comes to a global supply chain, risk models encompass things like the exposure footprints of suppliers, hazard event histories, probabilities and business interruption data. By identifying these risks, it is easier to address vulnerabilities by building supply chains that can quickly adjust and recover from disruption.
Mr Shibley noted that H&P’s automated inventory management systems have enabled responsiveness in this area. “Our automated systems allow us to efficiently redistribute inventory to areas with the highest demand,” he said. “This has enabled a greater ability to mitigate the risks associated with this outbreak and continue managing a very fluid situation.”
Early response
Mr Thomson at Vantage said he first became aware of the seriousness and how quickly things could change due to the outbreak while traveling through the Far East in early February. As early as 10 February, the Singapore government was starting to check people’s temperatures before they could enter office buildings, and workers had to confirm with the government that they had not traveled to mainland China in the previous 14 days.
Keeping up with the rapid changes that various countries were making regarding closures and safeguards was a significant challenge for Vantage’s supply chain team initially, Mr Thomson added.
“In a very short period of time, more and more countries were limiting or restricting not only passengers but also cargo. You had to really anticipate which country, what service or access could be shutting down next and try and move those respective shipments soonest… This has obviously created a huge challenge in the movement of critical supplies and personnel.”
At Seadrill, Mr McGavin said his team’s primary objective of ensuring the rigs did not see any downtime due to supply chain interruptions did not change, but the pandemic did bring about a “shift in intensity.” Moreover, the focus of keeping a rig operational has shifted. On top of their normal supply chain deliverables, the global supply chain team had to make sure the rig crews had more than enough equipment, materials and supplies to keep themselves safe. The company is also raising the intensity associated with cleaning its rigs. Very early on, he said, the company went from a minimum 14-day stocking level to a 30-day stocking level for food and cleaning supplies.
“My team went from supporting the rig, buying materials, buying equipment and logistically moving the items, to suddenly being focused on sourcing additional medical PPE and cleaning products,” Mr McGavin noted. “They’re looking at whether our rigs have the right amount of cleaning materials, the right amount of food and catering supplies, and other materials on the rig to keep the guys going. The focus now is figuring out how to ensure that we won’t have a supply chain disruption that could impact rig operations.”
Managing travel and cargo
Not surprisingly, the COVID-19 outbreak has spawned a massive disruption in air travel. According to the online air traffic monitor Flightradar24, global air traffic was down by 41% in March 2020 compared with the same month in 2019, and the International Air Transport Association (IATA) said approximately 8,500 passenger aircraft – around a third of the world’s commercial passenger fleet – have been grounded as countries implemented travel restrictions.
Air travel is an important element of supply chain management, with the IATA estimating that approximately 45-50% of air cargo travels in the belly hold of passenger aircraft.
These restrictions have forced drillers to prioritize. Mr Collins said they have had to utilize cargo ships for less urgent deliveries, primarily for work that, due to the virus, has been delayed but not canceled. He said this shift has the added benefit of keeping costs down, as rates for cargo ships are often cheaper than air.
“Because some of our work in the future has been pushed out, we don’t need to fly all of our shipments all the time,” Mr Collins said. “If a client has shut down for two months because of COVID-19, we don’t need to fly equipment out to that client immediately. We can put it on a boat and reduce the cost. Those are the things we’re managing right now. Our supply chain people are talking to the vendors about whether or not flights are still needed, or if it’s best for us to hold an order.”
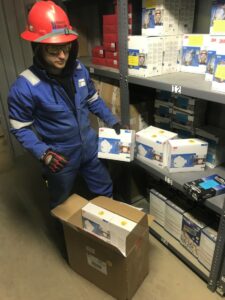
Mr Collins said Parker’s prior experiences dealing with challenges in Russia and other countries have made the company better equipped to find solutions during the current situation. For example, the company already had protocol in place to better manage sourcing options in its Arctic operations. It had also built a strong network of suppliers to mitigate potential disruptions caused by shipping restrictions. In the current environment, Mr Collins said, that flexibility is vital.
“When you’re an international company and you have the US issuing sanctions on Russia, you have to deal with a lot of contingencies in terms of getting things through,” he noted. “Managing that earlier, I think, helped us. If you have sanctions, the US and EU are shut down, so we already saw folks increase inventory levels in anticipation of dealing with those challenges, whether it’s getting stuff from a certain country or from a certain supplier.”
Communication focus
With so much uncertainty surrounding COVID-19, supply chain teams have placed a premium on communication, meeting more frequently with each other and with other teams to gather as much information as possible about potential impacts within their companies.
Mr Thomson said communication with Vantage’s suppliers and freight forwarders has increased since the initial outbreak, and his team receives status reports on every critical shipment on a daily basis, if not more frequently.
“The companies we go to all the time, are they at risk? If so, what are we going to do to ensure that, if there is a disruption, we have coverage and access to those items that we’re buying from them?”
– Greg McGavin, Seadrill
Mr Collins said Parker’s internal leadership group has also been meeting on a regular basis to discuss supply chain. “We’re meeting three times a week to discuss this,” he said. “We had not done that before. This has impacted so many groups on so many levels. I think the frequency of the meetings and the number of people involved is much higher than with previous emergencies.”
Mr McGavin said he has more than 10 additional scheduled meetings per week related to various elements of Seadrill’s management plan, resulting from COVID-19’s potential impact. The company instituted what he called “weekly touch points” with core suppliers and OEMs, and it meets daily with critical suppliers. The company also meets at least three times weekly with third-party suppliers who are important to day-to-day operations on the rigs, such as catering and travel for personnel. “We’re in a situation where everything has to be coordinated and scheduled, and you need to have phone calls and meetings to deal with things that you normally would have done in a 10-minute conversation,” he said.
Communication with the rigs is also paramount during this time. Mr McGavin said his hemisphere and corporate teams need to be “super responsive” to any concerns raised by rig crews, continually updating them with as much information as possible.
“The crews have been working on these rigs for extended periods,” he said. “We’re practicing this level of social distancing, but the guys on the rig face more challenges. The moment anything bubbles up with a rig crew, we address it immediately and provide the information to waylay any concerns they might have.” DC