Drilling & Completion Tech Digest
Ulterra bit sets curve record for Haynesville rig
Ulterra’s 6.75-in. UD511 bit set a same-rig record for drilling a curve section in its first run in the Haynesville shale. The bit drilled the curve in 35 hours at 23.4 ft/hr.
The five-bladed bit with 11-mm cutters departs from the typical drilling program in which seven-bladed, 11-cutter bits and 2°-plus bend motors have been used to ensure steerability while achieving the build rates necessary to hit the target. Average penetration rates for the seven-bladed bits have been 12 ft/hr to 15 ft/hr, although an Ulterra UD711 bit achieved a penetration rate of 20 ft/hr.
Chris Hearn, application engineer for Ulterra, said the steel-body design and short-gauge configuration of the UD511 bit contributed to its performance. “This bit was designed specifically for Haynesville curve and build sections,” he said. The 4.38-in. makeup length provides the shortest bit and the shortest bit-to-bend length currently available for Haynesville slim-hole drilling, according to the company.
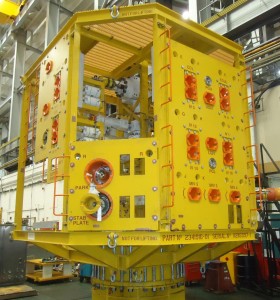
Capping device ready for UKCS subsea wells
A well capping device constructed as a result of recommendations made by Oil & Gas UK’s Oil Spill Prevention and Response Advisory Group (OSPRAG) was introduced to the industry in September.
The device, constructed specifically for subsea wells on the UK Continental Shelf (UKCS), features a modular design so it can be attached to various points of subsea equipment. The cap is rated for deployment in water depths up to 10,000 ft on wells flowing up to 75,000 bbl/day at 15,000 psi. The cap’s portable size and weight makes it relatively easy to deploy from a wide range of vessels.
The capping device was designed and manufactured over a period of seven months, made possible through access to pre-existing equipment and collaboration with the industry’s global supply chain. The device has completed factory acceptance and system integration testing and will be handed over to Oil Spill Response, which will store it in readiness at an operational base in the northeast of Scotland.
Collaborative team to test methane gas in Alaska
The US Department of Energy, the Japan Oil, Gas and Metals National Corp, and ConocoPhillips will work together to test innovative technologies to produce methane gas from hydrate deposits on the Alaska North Slope. The tests will use the “Ignik Sikumi” gas hydrate field trial well, a fully instrumented borehole that was installed in the Prudhoe Bay region by ConocoPhillips and the US Office of Fossil Energy’s National Energy Technology Laboratory earlier this year. Current test plans call for about 100 days of continuous operations from January 2012 to March 2012.
Methane hydrate consists of molecules of natural gas trapped in an open rigid framework of water molecules. Many experts believe it represents a potentially vast source of global energy; the DOE has been studying it for decades.
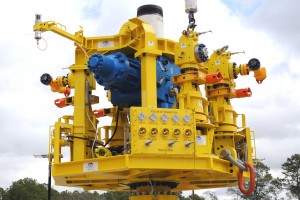
New well containment system for Gulf of Mexico incorporates acoustic monitoring technology
Helix Well Containment Group (HWCG) is using Sonardyne’s wideband acoustic monitoring technology in a new emergency well containment system built by Trendsetter Engineering.
The emergency well response system comprises an intervention capping stack that would be placed over a damaged well to stop its flow. Its design makes it capable of capturing and processing up to 55,000 bbl/day of oil and 95 million cu ft/day of natural gas at surface pressures of up to 10,000 psig.
In an emergency, the supplied Sonardyne data acquisition system would be used to remotely monitor pressure and temperature sensors fitted to the capping stack. The system consists of a surface command unit, intelligent deep acoustic remote transducers and a subsea electronics module that is capable of transmitting data to the surface for immediate analysis.
The intervention capping stack will be continuously maintained by Trendsetter at its facilities in Houston, where it will remain on-call for immediate deployment as needed.
A total of 24 operators in the Gulf of Mexico are participating in the HWCG.
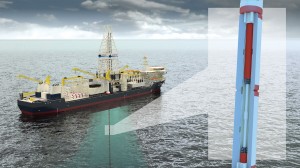
Buoyancy module on landing string to expand floating rigs’ deepwater operating range
Landing Strings Solutions and Trelleborg Offshore have developed and manufactured the world’s first buoyancy module system deployed on a drill pipe landing string. The system aims to enable safer and more cost-effective deepwater operations.
The patented system comprises buoyancy modules placed around the landing string pipe body and secured between two fully composite conical stop collars. Each module is made up of two halves approximately 2 ft in length, with the total quantity required dependent on the range of landing string drill pipe used.
The system is designed to offset the landing string weight by up to 80%. This reduction in weight makes it safer for heavy casing strings to be used from deepwater floating rigs.
The system also reduces the overall hookload, thereby lessening the mechanical stresses shared by the rig’s hoisting system, increasing the rig’s load-landing capabilities and improving the environmental operating range. It could expand the operating range of third-, fourth- and fifth-generation rigs to step out into deeper drilling depths.
The modules incorporate a polyurethane coating to protect the syntactic material, developed and tested by Trelleborg, from the degrading effects of typical synthetic-based mud, while providing abrasion resistance. The system is designed to cope with the harsh conditions encountered inside the marine drilling riser. The solution boasts a high-temperature resistance and can operate in pressures up to 6,000 psi.
To eliminate unnecessary additional rig time, the modules are assembled onshore and secured in enclosed bolsters, which are then delivered offshore. Post-job cleaning, disassembly and inspection are conducted at Landing Strings Solutions’ Port Fourchon facility in the Gulf of Mexico.
New subsea tree systems to help Centrica develop marginal North Sea fields
GE Oil & Gas’ SVXT shallow-water vertical tree subsea systems are headed for fields in the UK Southern North Sea gas basin and the East Irish Sea, under contracts with Centrica Energy Upstream of Aberdeen. The SVXT subsea system merges horizontal and vertical tree technologies, reducing weight by 20% and decreasing height in a pre-configured modular style. The design enables low-cost installation using standard jackups.
“The SVXT systems incorporate GE’s latest design for shallow-water applications and offer new, innovative features to meet Centrica Energy’s specific requirements,” said Matt Corbin, GE Oil & Gas regional leader – UK and continental Europe. “The SVXT tree system is smaller and lighter than any traditional shallow-water systems on the market and also offers the lowest installed cost.”
Centrica also will deploy one MVXT system, a standard structured M-Series vertical subsea tree, in the UK Central North Sea. Greg McKenna, commercial director for Centrica, said GE’s new subsea tree technology will help the operator to develop marginal fields by ensuring economic viability.
TOTAL extends application of riserless mud recovery
TOTAL, an early adopter of AGR’s riserless mud recovery (RMR) system, has extended its contract for the technology by four years. RMR enables engineered mud to be used in the top-hole section of a well, with all mud and cuttings returned to the rig.
TOTAL first signed up to use the system in 2006.
The contract also includes use of AGR’s cutting transportation system (CTS), which enables operators to take cuttings, cement, mud and other deposits away from the well, keeping templates debris-free.
AGR will soon pass the 500-well mark for deployment of the RMR and CTS systems.
Subsea trees to be installed using heave-compensated system
Delmar Systems will install five subsea trees using the Heave Compensated Landing System in the Tamar gas field offshore Israel in the Mediterranean Sea for Noble Energy. The subsea trees will be installed in the Matan block in a water depth of approximately 5,500 ft.
Delmar will work with Transocean’s Sedco Express semisubmersible for tree installation operations on Tamar, one of the Mediterranean’s largest finds. Project commissioning is expected in late 2012.