Drilling automation: New design tool helps to chart roadmap for the future
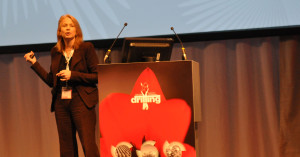
Drilling automation is improving operational safety, efficiency and economics and providing access to fields and reservoirs once thought inaccessible, but having a clear roadmap to track progress and define long-term goals will help to accelerate industry’s journey along that path, a technology application expert said in a presentation at the 2013 SPE/ IADC Drilling Conference & Exhibition in Amsterdam on 6 March. “There are some perceptions that the drilling industry hasn’t moved as quickly as other industries have toward automation,” Ginger Hildebrand, software governance manger for Schlumberger, said in her presentation. “But we operate primarily in a very unstructured environment where we can’t directly observe everything that is important.”
In reality, the drilling industry hasn’t approached automation much differently than other industries, she noted. “We started out with manual processes that over time became industrialized and improved, then moved to the mechanization phase and finally to the automation phase. That is the roadmap we are following.”
Going forward, however, a new way of charting the automation roadmap, using a new design tool, shows how the three main components of drilling automation – rig site manpower, rig equipment automation and remote connectivity —can interact in one system, Ms Hildebrand explained.
The design aid is based on a ternary chart, a two-dimensional diagram that that can be applied to real-world applications. “This design aid charts the traditional human (rig site manpower) and computer (rig equipment automation) contributions to the process but also adds the component of remote control to the overall discussion around the elements of what makes an automation system work,” Ms Hildebrand explained. “The contribution of each component may be different, but they must all add up to 100%. For example, a reduction in human effort will be assumed by increased automation and/or the level of remote-connectivity engagement.”
Charting a path
The design aid can be used to chart hypothetical scenarios showing the current level of automation; the future, or desired, state; and a path connecting the two that can be used to determine the development of automation over a specific time frame. Automation efforts developed by other industries, including aviation, mining and telemedicine, fit the three-component framework, Ms Hildebrand noted.
At a 2012 workshop on well construction management, drilling personnel who were shown a ternary chart model indicated they thought the current level of automation was low but were optimistic about the future; this indicates that future states will show a reduction in rig site manpower requirements, which is consistent with the major goal of automation in general, she said. The group also suggested little movement was needed for land drilling, with a small reduction in personnel balanced by more automation and increased use of remote operations, and viewed current well control practices as primarily manual operations that will become highly automated in the future. Offshore drilling was perceived to be more advanced in automation.
“This was about generating a conversation and having a quantifiable way of saying where we are and where we want to be,” Ms Hildebrand said. “The new design aid has elevated the level of remote connectivity to being a first-class member of the roadmap exercise for drilling automation and suggests some refinements and aids in communication as we map our way to the future.“