New West Africa contract for VALARIS DS-15 drillship
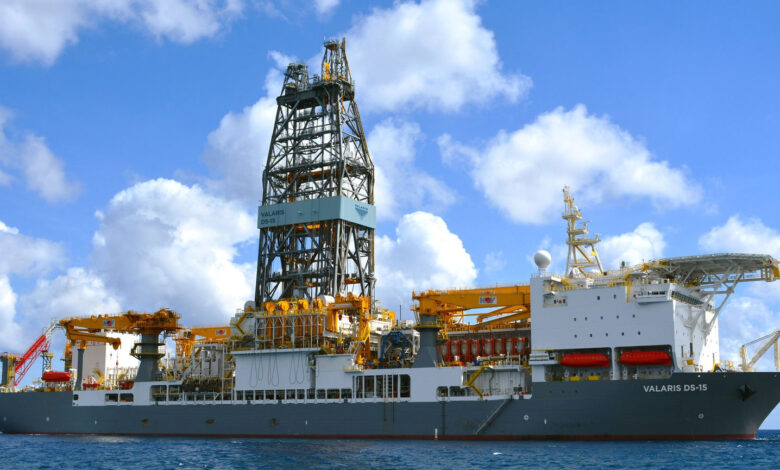
Valaris was awarded a five-well contract offshore West Africa for the VALARIS DS-15 drillship. The contract is expected to commence in Q3 2026. The total contract value, based on an estimated duration of 250 days, is approximately $135 million and includes priced options for up to five wells with an estimated total duration of 80 to 100 days.
As part of the contract, the rig will be upgraded with an enhanced managed pressure drilling system.