D&C Tech Digest
Conductor-casing support system commercialized on Ekofisk
The first commercial application of a new support system for conductor casing operations is under way on ConocoPhillips Norway’s Ekofisk field.
The system, supplied as part of Claxton Engineering Services’ risers, conductors and flowlines business, supports the first well conductor casing string that the rig places in each platform slot. The conductor is initially placed and cemented using the rig. Following this, the split-design support system is moved into position, attached and then elevated to the necessary height. The rig then skids over to the next well while the system supports the conductor until the cement sets, up to eight hrs. This delivers time and cost savings on multi-well programs.
Another key feature is the system can be moved without a crane or forklift.
The initial work scope for the system is six wells; a second phase that may include up to 30 wells is being planned.

Statoil to boost production with seismic cables on seabed, completes first multilateral well offshore Brazil
New seismic tools are expected to bring in 30 million extra barrels of oil from the Snorre and Grane fields when Statoil and its partners start using permanent reservoir monitoring (PRM).
Snorre and Grane are two oil fields in the North Sea with large remaining reserves. Approximately 700 km of seismic cables will be placed in trenches on the seabed to cover an area totaling approximately 240 sq km (190 on Snorre and 50 on Grane). Combined, this will be the world’s largest seismic project of its kind, according to Statoil.
It will provide more frequent and better seismic images of changes in the reservoirs. Installation work starts this year at Snorre and in 2014 at Grane.
Separately, Statoil also recently completed its first multilateral well offshore Brazil as part of the company’s increased oil recovery (IOR) efforts at the Peregrino field. This is the first multilateral well in Brazil with gravel pack in both branches.
The Peregrino field is located 85 km offshore Brazil in the Campos basin in about 100 meters of water in licenses BM-C-7 and BM-C-47.
Statoil has doubled the expected recovery factor from about 10% when Statoil bought into the field to about 20% expected recovery when the field was sanctioned. A high degree of reservoir exposure, the drilling of long horizontal wells with geosteering technology to maximize length and optimize placement, and water injection to improve oil recovery have helped increase recovery at Peregrino.
LNG fuels hydraulic fracturing in Eagle Ford
Ferus has successfully completed one of the first hydraulic fracturing operations utilizing liquefied natural gas (LNG) as engine fuel in North America.
The pilot project involved six dual-fuel 2,250-hp pressure pumper units, powered by LNG, to stimulate well performance in the South Texas Eagle Ford shale.
“LNG offers significant environmental and cost-saving advantages and is quickly becoming the alternative fuel of choice for heavy-duty, high-horsepower, on-road and off-road applications in North America,” said Dick Brown, president and CEO of Ferus. “We intend to be at the forefront of this growing industry as more and more diesel consumers make the switch to North America’s abundant supply of natural gas.”
Ferus managed the supply chain on behalf of its client, including LNG supply, transportation and on-site storage and vaporization using specialized equipment and personnel.
Converted frac units reduce diesel use by 65%
Baker Hughes has converted a fleet of its Rhino hydraulic fracturing units to bifuel pumps to improve operational efficiency, lower costs and reduce health, safety and environmental impacts.
The new pumps use a mixture of natural gas and diesel, reducing diesel use by up to 65% with no loss of hydraulic horsepower. The converted fleet, which meets all US Environmental Protection Agency emissions standards, can also reduce a number of emissions, including nitrogen oxides, carbon dioxide and particulate matter.
Using the converted Rhino Bifuel units, Baker Hughes recently completed a hydraulic fracturing job in the Eagle Ford Shale for Cheyenne Petroleum Co. Baker Hughes was able to pump 35 stages using three of the converted Rhinos during each stage. By substituting natural gas into the converted diesel engine, the bifuel alternative can operate twice as long as engines running solely with the onboard diesel.
300th wireless system shipped to connect rigs
Redline Communications Group has shipped more than 300 of its RAS wireless nomadic systems, providing broadband connectivity to rigs in the US and the Middle East.
RAS’s high-speed, long-range connection capability allows rigs to become part of a larger networked system, connecting them to corporate systems and the Internet, effectively turning them into ruggedized connected offices.
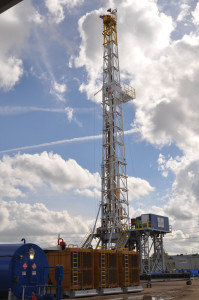
Dual-fuel rig with integrated walking system moves up to 60 ft/hr
By Katherine Scott, associate editor
Independence Contract Drilling recently introduced its newest-design 1,500-hp ShaleDriller Rig 201. The rig, contracted to Newfield Exploration, has been built with an integrated walking system that allows the unit to move at up to 60 ft/hr, as well as a full dual-fuel setup that allows the rig to run on both diesel and natural gas.
“The operator’s main goal is to spend their money and their time in a year drilling instead of moving rigs,” Chris Menefee, vice president and general manager of Independence, said. “If they can put eight wells on a pad and walk a rig back and forth, they’ve got something that’s more hi-tech that’s capable of doing what they want to do better than the conventional method.”
The integrated walking system features uniquely designed hydraulic shoes driven by AC power that are built directly into the substructure and therefore are part of the rig, Mr Menefee said. “Other walking systems are ‘add on’ systems retrofitted on conventional drilling equipment leading to more lines, wires, hoses and manifolds,” he explained.
Further, when the walking shoes are not utilized, they are designed to support the substructure and can be used to level the rig during drilling operations. “Also, our system has an umbilical wire tray designed for multiwell pad drilling,” Mr Menefee continued. “The 200 Series ShaleDriller was engineered to walk with drill pipe in the mast and move from pad to pad without the use of a crane, which results in cost savings for the operator.”
Rig 201, which will drill a seven-well project for Newfield at 30 days each, is the fourth new rig to be built in Independence’s fleet, but the first with a new substructure put together from one piece consisting of a bottom substructure and rig floor. Hydraulic cylinders are attached to the unit to set it in place before other pieces, such as stairs, are added.
Watch an exclusive video and photo gallery of the Independence rig.

Natural gas engines installed to power 1st LNG-fueled drilling rigs in Marcellus
To reduce environmental impact and improve the economic performance of US unconventional gas production activities, Seneca Resources Corp and Ensign Drilling have installed two GE gas engines to power the first liquefied natural gas (LNG)-fueled drilling rigs in the Marcellus Shale.
Seneca converted the power plants of two existing diesel-powered rigs to use LNG in GE’s 1-megawatt Jenbacher J320 turbocharged natural gas engines. The Jenbacher units were combined with Ensign-designed rig packages to provide the electricity needed by each rig. The J320 represents GE’s first US Environmental Protection Agency-certified technology for mobile and stationary drilling applications.
In October, Seneca Resources and Ensign Drilling converted their first rig, which is operating in Lycoming County, Pa. The second rig was converted to LNG in November and was assigned to Seneca’s Marcellus Shale gas leases in Forest, Elk, Jefferson and McKean counties.
Ensign Drilling operates 15 drilling rigs exclusively on natural gas in the US, with 11 of them using GE’s Jenbacher engines. Powering a rig with natural gas instead of diesel can result in up to 60% lower fuel costs, GE believes.
New coring system deployed on ultra-deepwater operations
Corpro is now deploying its Thin Sleeve System (TSS) Core Barrel technology in the Gulf of Mexico (GOM) and has completed three ultra-deepwater operations there. Nearly half of all core-cutting activities within the energy industry are carried out under Corpro.
The company’s TSS Core Barrel significantly improves the quality of coring samples and provides a platform to enhance wellsite processes and core analysis. The barrel is a 20-ft ultra-stable system.
The system creates better core samples because of the presence of two independent inner tubes that protect the core during the cutting process and allows the recovery to take place without transmitting any stress to the core. The TSS inner barrel is made of steel with aluminum liners for a stronger coring system.
TSS is the platform used for Half-Moon On-Ice liners. Geologists in the GOM are able to lift the top half of the aluminum and describe the core at the wellsite.