Case study: Chevron deploys below-tension-ring MPD to drill highly depleted reservoir in GOM
Strategy helped to reduce risk for fluid loss and decreased mud weight requirements
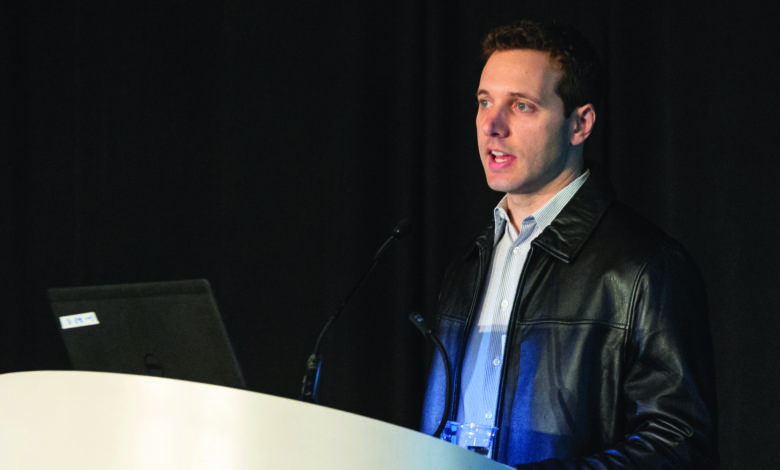
By Jessica Whiteside, Contributor
Complex deepwater drilling environments can become even more challenging as reservoirs mature. Pressure concerns tied to high levels of depletion increase the potential for fractures, downhole fluid loss and well control hazards. To reduce these risks and associated remediation costs, Chevron has found success deploying drillships outfitted with customized surface-backpressure managed pressure drilling (MPD) systems in mature reservoirs in the deepwater Gulf of Mexico.
At the 2022 IADC/SPE International Drilling Conference in Galveston, Texas, on 9 March, Ken Vaczi, Deepwater Drilling Engineer for Chevron, described the company’s experience with its first two deepwater BTR MPD systems in the Gulf of Mexico during a four-well campaign. The company has since expanded its use of the technology to other operations in the region.
BTR (below tension ring) refers to a surface-backpressure MPD system in which the rotating control device (RCD), used to control pressure during drilling, is placed near the surface in the riser but below the telescopic joint.
By maintaining near-constant bottomhole (or other target location) pressure, this MPD approach helps the operator to navigate narrow drilling margins. Other potential benefits include quicker leak-off detection and reaction to losses, safer determination of drilling parameter and mud weight adjustments, greater control of pressure to prevent borehole instability, and more efficient cementing of production liner.
Choosing the right equipment
Chevron decided to apply BTR MPD to the four-well campaign after experiencing major downhole fluid losses during an earlier conventional drilling operation in highly depleted Gulf of Mexico reservoirs. Modeling predicted that the new campaign could face similar conditions, which could trigger downhole losses and make it difficult to reach planned total depth and achieve other well objectives.
Through MPD, the team hoped to mitigate the potential for thermally induced fractures and differential depletion, with some sands in virgin condition and others with high depletion levels up to 8,000 psi – the highest level of depletion that Chevron has drilled in the Gulf of Mexico to date, Mr Vaczi said.
Smaller flow meters tend to be standard on MPD packages, which concerned the project team in light of the erosional velocity of the mud expected to flow through the meter, especially in combination with some of the lost-circulation material they anticipated using for the project.
“To fix the problem, we elected to do a two-size implementation,” Mr Vaczi said. “The larger flow meter could be used for the larger hole sections and the smaller flow meter could be used in the smaller hole sections where the flow rates were less.”
They also included a dual junk catcher to prevent large debris from plugging the automatic chokes and disrupting the ability of the MPD system to automatically manage surface backpressure. When one catcher was plugged, they could switch to the redundant catcher on the fly with minimal impact to operations.
While Chevron had used other forms of surface-backpressure MPD around the world, the four-well campaign marked its first use of the BTR MPD variant on deepwater floating rigs in the Gulf of Mexico. The company worked with MPD equipment providers and two drilling contractors to place permanent BTR MPD systems on two drillships.
Using BTR MPD in the Gulf of Mexico required the submission of a new technology plan to the US Bureau of Safety and Environmental Enforcement. Adding MPD equipment to the rigs fundamentally changed the way some operations, such as tripping, were performed. This necessitated the creation of more than 40 new mandatory rig-specific procedures for each of the rigs and the development of classroom, simulator and onsite refresher training.
Before putting a single piece of MPD equipment on the rigs, the team conducted a five-step review that included a hydraulics check, onshore flow test, RCD durability test, HAZID/HAZOP workshop, and a complete logic system review of the MPD control system.
Achieving objectives
Their careful planning paid off. Mr Vaczi called the application of deepwater MPD highly successful, with all wells drilled to total depth with no losses through the high depletion intervals or the tight margins of the intermediate section.
“We had no major safety incidents throughout the implementation and execution of MPD, and all systems performed as intended.”
Compared with offset wells drilled conventionally, MPD successfully reduced equivalent circulating density (ECD) by 0.5 ppg. Dynamic pore pressure tests performed on all wells enabled the team to further reduce mud weight while remaining within the safe parameters identified by borehole stability studies conducted prior to the startup of operations.
They also successfully ran and cemented all production liners in the campaign using MPD and reduced cementing ECDs by almost 1 ppg compared with conventional operations.
“This is critical to the success of the cementing job in achieving zonal isolation in these intervals,” Mr Vaczi said. DC
For more information, please see IADC/SPE 208771, “Implementation of MPD Systems in the Deepwater Gulf of Mexico to Drill Highly Depleted Reservoir Sections.”