Better reporting systems, clearer communication and additional training can help improve understanding of BOP failures
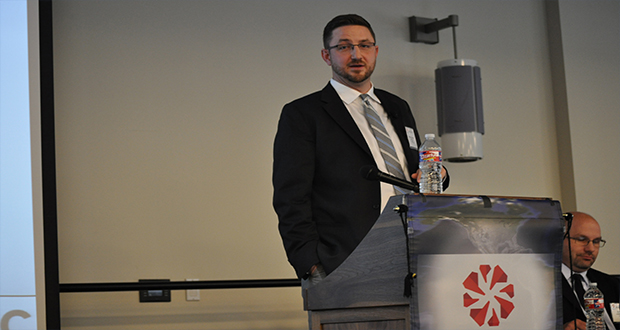
By Kelli Ainsworth, Editorial Coordinator
One of the keys to successfully maintaining BOPs is understanding how and why they fail, said Matthew Nelson, Subsea Well Intervention Engineer at Chevron. Speaking on 16 September at the 2015 IADC Asset Integrity and Reliability Conference in Houston, Mr Nelson explained that root cause analyses (RCA) for BOPs is a major part of the company’s asset management plan. RCAs enable the company to understand how a failure occurred in order to prevent future failures. However, RCAs often face failure themselves, due to an array of physical, human and organizational reasons. “There are a lot of obstacles that can get in the way of getting a good lesson out of a failure,” he said. Chevron has studied these reasons and generated recommendations for overcoming them.
Some of the barriers to a successful RCA are physical. For example, BOPs have to be brought to the surface to be studied for an RCA. When taken out of a subsea environment, some of the symptoms of the system’s failure that could help diagnose the failure’s cause may now be absent. In addition, the rush to get back to work can cause details to be lost. Finally, because BOP systems are so complex, there may be many points at which a failure could have occurred. It can be difficult to determine what actually lead to the failure. “There might be too many potential causes and you can’t narrow it down any further,” Mr Nelson said. “It can be complicated troubleshooting and analyzing these systems.”
Human factors can also be a stumbling block to a successful RCA. Due to personnel turnover, crews coming on or off an offshore rig for weeks at a time, “communication can be lost,” Mr Nelson said. It’s also not always clear to personnel on a rig whom they need to contact to troubleshoot a BOP. In addition, rig personnel may not be properly trained to perform an RCA – they may not know what data to collect, how much detail is needed and when data should be collected.
Organizational factors that can contribute to RCA failure include the need to keep the rig working. “There is a huge focus on turning to the right and continuing operations,” Mr Nelson said. “Those needs for keeping the rig working can easily put RCA efforts on the backburner.” Even when companies are able to focus on performing RCAs, if they lack an adequate failure recording system, RCA data can just get lost. “When you’re trying to collect data and learn about a system over a lifetime, over years, not having systems set up to properly record failure data can really damage you when you’ve got to come back later and you can’t find it,” Mr Nelson said.
After working to understand why RCAs fail, Chevron established recommendations to address these physical, human and organizational obstacles to RCAs. One of the keys to overcoming physical challenges to RCA data collection is utilizing real-time data recording, Mr Nelson said. “By recording real-time data, you get past not being able to replicate subsea data on the surface,” he said.
To address human error in RCA data collection, Chevron recommends creating a clear communication protocol. If it isn’t clear who rig personnel should call to address a failure, then it could involve dozens of emails and phone calls until someone with the expertise to address an issue is found. A clear communication protocol can cut this down dramatically so “you’ve got the right people involved, they’ll troubleshoot, gather the data and get the ball rolling so that we don’t repeat the same mistake,” Mr Nelson said.
Having dedicated personnel on a rig who are familiar with the BOP equipment to work on failure identification while other personnel focus on getting the system working again can speed up and improve RCA efforts. “We have engineers out there who are familiar with the systems who will work on failure identification,” Mr Nelson said, “We find it helpful to capture the right data when these failures happen.” Providing more in-depth RCA training to rig crews can also aid in the efforts to identify failures. Mr Nelson likened this training to learning how to repair a car – when a person has worked on a car in the past, they’re better able to identify the source of problems when they occur, and then fix them. “By troubleshooting and working on a system, you end up learning it more inside and out. That will help our maintenance crews not only understand their systems more but help us start RCA investigations,” Mr Nelson added.
Creating an implementing a failure reporting system can combat organizational factors that can cause RCAs to fail. Such a system can help not only the operator but also contractors and OEMs. Chevron has found that RCA efforts are most successful when the drilling contractor and OEM are brought into discussions. “Everybody’s bringing something to the table, bringing in some detail about the situation and sharing something,” he said. Such discussions can lead the OEM to change the design, testing and manufacturing techniques for equipment. Drilling contractors can benefit from RCA discussions, as well, and may end up refining their maintenance schedule as a result. Operators can apply learnings from RCAs to well control practices and well design. “We stake our reputation on the safety of our ships offshore and our ability to maintain well control,” Mr Nelson said. “If we slip at that, lives and assets are lost.”