OMV Petrom and ROMGAZ spud first well of Neptun Deep project
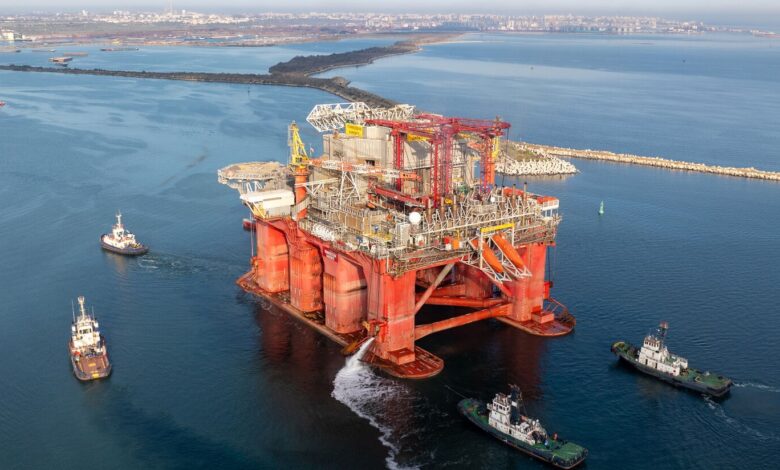
OMV Petrom and ROMGAZ announced the spud of the first well for development and production of the Pelican South and Domino natural gas fields in the Neptun Deep block, located 160 km offshore in the Black Sea. First gas is estimated for 2027.
“We are excited to move to the next stage of the Neptun Deep project, namely the drilling of the ten wells that will ensure natural gas production, out of which four will be in the Pelican South field and six in the Domino field. The first well will be drilled in the Pelican South field, located in waters approximately 120 m deep, with the gas reservoir situated about 2,000 m below the seabed. We estimate that the drilling operations for the ten wells will take us into Q4 2026,” says Cristian Hubati, member of the OMV Petrom Executive Board, responsible for Exploration and Production.
The well foundations for Pelican were installed using the CAN-ductor from Neodrill, which minimizes the overall environmental footprint of the drilling process. The drilling of the first well is estimated to take two to three months.
The drilling will be carried out using the Transocean Barents mobile drilling unit, which has been contracted especially for the project. Halliburton Energy Services Romania and Newpark Drilling Fluids Eastern Europe will provide the integrated drilling services. Halliburton’s international and local experience in Romania will be deployed on a wide range of services such as cementing, directional drilling and well completions.