2-in-1 bit: Dual cutting structure boosts ROP
Combination of TCI and steel tooth improves performance in abrasive sands in Pinedale tight gas
By Keith Smelker, Shell; Connie Burch, Mark Freeman and Floyd Felderhoff, Baker Hughes

Drilling at a high penetration rate while maintaining durability to complete abrasive sand sections in the Riverside field of Pinedale, Wyo., has been a challenge. The introduction of a new line of drill bits into the Pinedale area using a combination of tungsten carbide inserts (TCI) and a steel tooth cutting structure has led to increased performance, reduced risk and cost savings for the operator.
By combining the two cutting structure types, the drill bit was able to attack the formation more efficiently while resisting abrasive wear in key areas to drill longer-footage intervals. Improving the durability of the drill bit also helped to reduce the risk of losing cones, decreasing nonproductive time lost to fishing.
A typical well is drilled with an S-curve profile to gain displacement from the multiwell pad. The 8 ½-in. roller cone bits are normally used to drill the directional part of the hole using directionally steerable downhole motor assemblies. Once the well has returned to vertical or reaches casing point, the bits are pulled.
Using the service company’s design application review team process, the team of engineers and field support personnel from the operator and service company was able to identify the key limiting issues and make recommendations for the design of two different drill bits. These limiting issues were related to erosion and coring of the center of the drill bit.
The drill bit designs used both traditional and nontraditional cutting structure features, along with improved drill bit hardfacing materials.
Based on field observations and results, this article describes the initial benchmarking and field analysis, along with recommendation for design improvements. The results will be shown by comparing current field results with previous benchmarks. These improvements resulted in a 52% rate-of-penetration (ROP) increase in the first TCI run of the interval and a 59% increase in the second run. This improvement delivered a 20-hr decrease in drilling time over the entire 8 ½-in. section, significantly reducing the cost to drill that interval.
Vanguard application
The Pinedale Anticline is in the Greater Green River Basin, south of the city of Pinedale, Wyo., and north of the Jonah Field in Sublette County. Production in this field predominantly comes from the Lance and Mesaverde formations. The wells are constructed with 9 5/8-in. casing set in 12 ¼-in. surface hole at 2,500 ft true vertical depth (TVD).
The 7-in. intermediate casing is set in 8 ½-in. hole between 7,500 ft and 10,000 ft TVD. The 4 ½-in. production casing is set in a 6-in. hole between 13,000 ft and 14,000 ft TVD.

Multiple S-shaped wells are drilled from a single pad, with the tangent section generally drilled at less than 30° from vertical. The kickoff point varies, with the build usually completed in the surface hole and the remainder of tangent and drop to vertical completed in the intermediate hole. The production hole is drilled vertically to total depth.
Two 8 ½-in. Vanguard TCI drill bits are generally used to drill through the intermediate section of the Fort Union formation to the top of the Lance formation. The Fort Union formation in this area is sorted sandstone interbedded with siltstone and stringers of extremely abrasive sandstones.
The mud system is inhibited clear water, with viscous sweeps made at every stand. The bottomhole assembly is a conventional, directional assembly using a bent housing motor with stabilization at 30 ft and 60 ft. The first TCI bit drills from surface casing at about 2,600 ft to 6,000 ft, and the second continues to drill to about 8,000 ft.
If intermediate casing is not set, the mud system is displaced to oil-based mud and the section is finished with an 8 ½-in. polycrystalline diamond compact (PDC) drill bit. The drilling parameters for this section are:
• 35,000 lbs weight on bit;
• 45-55 surface RPM;
• 155-185 total RPM;
• 500-525 gal/min flow rate.
Historically, this is a challenging section to drill due to the abrasive stringers. There have been multiple instances where the cones of the roller cone bit were lost and fishing operations were required.
Typically, the bit runs are limited to 35 hrs, if not pulled earlier for a torque spike, which is an indication that the drill bit has a mechanical issue. Trials to replace the two TCIs with one PDC of equal or higher gross ROP have been unsuccessful, with dulls often damaged beyond repair.
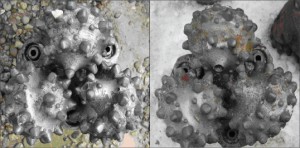
Design Application Review Team (DART)
A cross-functional team made up of participants from the service company’s applications engineering, research, product development, design engineering and operations groups was assembled. The design application review team’s focus was to address unique drilling problems and achieve customer objectives with an optimized drill bit solution. The team worked to identify the drilling problems and limitations posed by the application, then applied appropriate technologies
to eliminate these issues. Initial steps were to review the application and current use of the drill bits. These included 8 ½-in. MXL-S11G TCI drill bits, which were being used in the directional portion of the wells to cut through the abrasive sands sections. The review included observations of the used drill bits, discussion with the end user or customer and the actual performance of the bits.
During this review, it was determined that the drill bits were performing well with respect to penetration rates and distance drilled.
The issue with the bits was seen in the final dull condition as the cone steel was eroded while drilling through the abrasive sands. This in turn would lead to potential coring and loss of cutting structure if the runs continued long enough in the sands. The largest risk of this condition was the loss of cones as the center compacts lost their grip and fell out.
Once the problems were defined, the team outlined potential solutions and an action plan, which included combining the traditional TCI cutting structure and a steel tooth spearpoint in the cone with improved erosion resistance from new hardfacing materials available in the drill bit industry.
By combining the best of the two cutting structure types, TCI and steel tooth, the bit could capitalize on the best features of each. The outer TCI part was designed to address the fast drilling action needed to maintain the required penetration rate. The steel tooth part was designed with industry-leading hardfacing material on the inner part of the drill bit to mitigate the erosion and loss of cutting structure. The hardfacing material increases the resistance compared with the steel by a factor of up to 10, which allows the bit to be run longer with lower risk of failure.

Conclusion
The combined use of the TCI and hardfaced steel tooth cutting structures has shown that the proper combination of these technologies will improve performance in certain types of applications. This application of advanced materials that have been developed in recent years resulted in better performance than possible with the continued use of traditional design concepts.
This combination improved the project’s drilling performance by 54% while reducing the risk of seal failures and losing cones.
Reference: Les Devine, Burlington Resources Algeria; Martin Ellins, Alasdair Scotchman, Norman May, Baker Hughes OASIS; Sean Connell, Hughes Christensen/Baker Hughes, “Systematic Team Approach to Drilling Optimization Reduces Well Construction Time by 15%, Ghadames Basin, Algeria,” IADC/SPE 74522, 2002 IADC/SPE Drilling Conference, Dallas, Texas, 26-28 February 2002, Dallas, Texas.
Vanguard is a Baker Hughes’ Hughes Christensen trademark.