Liability, cybersecurity and cost among barriers to achieving interoperable rig systems
D-WIS interface offers a standardized concept, but more collaboration is needed for industry to truly move beyond proprietary protocols
By Stephen Whitfield, Senior Editor
Click here to watch a recording of the virtual panel discussion, originally aired on 13 February.
The premise of interoperable rig-based systems holds appeal for many wellsite stakeholders for different reasons, but building a truly interoperable infrastructure is no easy feat in the drilling world. While industry efforts to enable open and interoperable communication among key components and systems used in drilling have seen notable progress in recent years, there are still some pain points that must be overcome in order to make widespread interoperability a reality.
A virtual panel discussion (“Breaking Barriers: Drilling Contractors Engage on Interoperability”), hosted by DC and live-streamed from IADC’s Houston office on 13 February, saw representatives from five major drilling contractors – H&P, Nabors, Noble, Patterson-UTI and Transocean – discuss those pain points and the different digital tools they’re developing to work within an interoperable framework.
The discussion also included a look at D-WIS (Drilling and Wells Interoperability Standards), an industry initiative to create standards and recommended practices (RPs) allowing stakeholders to connect devices, sensors and telemetry systems. These standards and RPs would also cover the sharing of this data, as well as apps on new and existing rig control systems covering automation and related applications.
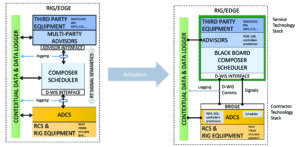
John Macpherson, Associate Fellow – Drilling Service at Baker Hughes and a D-WIS technical subject matter expert (SME), outlined one of the latest developments from the initiative, a conceptual architecture covering interoperability for drilling process automation.
The architecture consists of a drilling rig with an automated drilling control system (ADCS), which interfaces with an advisory stack of applications covering various functions and third-party equipment like MWD/LWD, rotary steerable systems, MPD systems and so forth. Any transaction between the control system and the apps, along with the contextual data behind those interactions, are logged within a data logger.
Within this architecture, the D-WIS interface would serve as an equalizer among different proprietary control systems and applications. The D-WIS interface is standardized, meaning that, regardless of how the data logging is structured, or how data is formatted, within a third-party system, the ADCS will be able to read the data coming from that third-party system, and vice versa, without issue.
“The D-WIS interface is the really important piece here. It has to be standardized among all ADCSs, so that the advisory stack can come on board and just plug and play with the system,” Mr Macpherson said. “With the ADCS, they can appreciate exactly what’s being attached to it. On the other side, the language of the interface attached to the ADCS is also known.”
Collaboration through initiatives like D-WIS are important to addressing the challenges present in developing an ecosystem of interoperable systems, said Anil Godumagadda, VP – Digital Solutions at Patterson-UTI and a member of the D-WIS Advisory Committee. Leveraging a unified framework, such as the D-WIS framework, will enhance interoperability by enabling the industry to move beyond proprietary protocols used by different service providers and rig types. However, Mr Godumagadda said there are still practical issues to making that framework a reality.
For one, he pointed out the need for protocols and application programming interfaces (APIs) that can actually interface with various rig control systems. These protocols and APIs must be able to function without affecting rig control systems and operations.
He also pointed out the need for data mapping – meaning, the need to develop standards for naming various data tags within the D-WIS interface.
Further, Mr Godumagadda pointed to the need to address liability concerns with the data. Namely, this means clarifying ownership – who is responsible for the data once it runs through the interface.
“Liability is a big component,” he said. “When we go into this, obviously the drilling contractor is going to be the face of the job, but if there are operational challenges with the data, how are you going to handle it? Who’s going to take ownership of those issues? It cannot always be the drilling contractor, which we have seen in the past.”
Mr Godumagadda also stressed the challenge of allocating the resources necessary to support and sustain a robust interoperable system: “There are going to be costs involved in adopting any new framework, any new implementation. How are we going to pay for it? We have to be mindful of these things.”
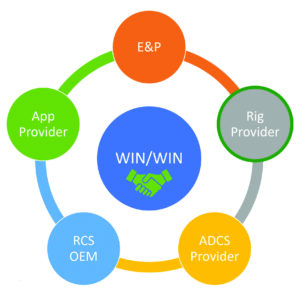
Cybersecurity compliance will be needed to protect systems and data running through the D-WIS interface. Network segregation will be critical to mitigating any risks that might come with data migrating in an interoperable ecosystem, said Rafael Guedes, Product Director at Nabors. If a breach or a cyberattack were to occur on one dataset, segregation would prevent that attack from spreading to other datasets.
“Separating the operational technology, or OT, the machines that control the rig, from the external world, putting the networks through a firewall and trying to keep that firewall as updated as possible are all ways we can leverage the technology we have,” Mr Guedes said.
However, too much segregation can also be detrimental. He noted that an interoperable ecosystem relies on the interconnectivity of systems by nature, as it involves standard interfaces to connect systems from multiple parties.
To that end, the end user in an interoperable system must accept some level of cyber risk and prepare themselves accordingly.
“Just like we do well control drills at Nabors, we do cybersecurity drills, as well. Basically, we simulate an attack and look at what we would do. That generates a lot of discussions and action items. How do we make sure that we have the right information at hand? If you lose connection on a rig today, can you still operate it?”
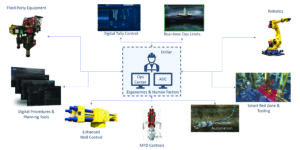
Getting buy-in from the industry is another challenge the panelists emphasized. And it’s not so much a challenge of enthusiasm, but more so a challenge with capital costs. That spend cannot be one-sided, the panelists agreed.
“When you’re looking at solutions out there, we have to find ways to lower that barrier to entry,” said Travis McGuire, Operations Performance Manager at Transocean. “There are some that may be economical, but they take a ton of rig time to implement. You may need to spend 30, 45 or even 90 days just integrating the system. You need some sort of ability to bring that service time down, at least for us in offshore. It is really one of the major hurdles out there.”
Robert van Kuilenburg, Offshore Performance Improvement Manager at Noble, said “there certainly needs to be some kind of sharing of the wins” when it comes to the adoption of new technologies on rigs. Third parties like drilling contractors have not seen financial rewards for many of the automated systems that have become prevalent on today’s rigs.
“A lot of this adoption has been pushed on all the drilling contractors on basically our dime,” he said. “At the end of the day, our clients are reaping most of the benefits. There certainly needs to be a discussion. We’re rolling out the whole infrastructure on our side. Let’s talk about, how can we make sure that the wins are actually wins for everybody?”
But even though the question of cost is still out there, the panelists agreed on the overall willingness of the industry to push towards greater interoperability.
Andy McMillan, Senior Project Manager at H&P, pointed out how far the industry has come in adopting digital systems over the past few years and the impact those advances have had on efficiency. He expressed optimism that the industry will continue to push even further in advancing toward an interoperable ecosystem.
“The fact that we’re talking about data interpretability, instead of just asking how we are going to get people to actually run this stuff, is something. If you go back 10 years, I think our biggest concern was getting that adoption from the field. Now that’s shifted a lot more,” he said.
Mr McMillan also noted the value interoperability can have in helping drillers take advantage of the significant amount of data coming from the rigsite. However, he warned against the possibility of interoperable systems placing an additional strain on the driller – essentially giving them an additional interface to analyze data. As interoperable systems become more commonplace within the industry, it will be important for their developers to keep in mind the needs of the people in the field.
“We don’t want to have a system where we can get to a certain place and then the driller has to configure things, and we have all these options for configurability. That’s just adding more set points for the driller to think about. We want to have a model that takes a lot of work off of the driller,” he said. DC