Noble developing modular rig package to facilitate safe, long-term drilling of CCS wells
Set for commercial release later this decade, package will address challenges like CO2 ventilation, potential corrosion of BOP materials
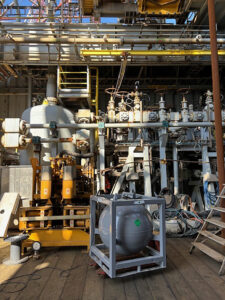
By Stephen Whitfield, Senior Editor
Carbon capture and storage (CCS) figures to be a significant part of the low-carbon future. In the International Energy Agency’s (IEA) Sustainable Development Scenario – under which global CO2 emissions from the energy sector fall to zero on a net basis by 2070 – CCS accounts for nearly 15%, or 10.4 billion tons, of the cumulative reduction in emissions.
Drilling contractors are uniquely positioned to play a major role in the scaling of CCS development. Their rigs can be used to drill the wells needed to inject CO2 into reservoirs. They can also perform interventions on the injection wells and drill relief wells if there’s an uncontrolled release of CO2. However, the properties of CO2 will require drillers to make modifications to existing rig equipment, processes and procedures.
For instance, much of the work around CCS today involves using conventional rigs to drill into depleted reservoirs or saline aquifers. But scaling CCS development will require using equipment suited for repeated exposure to and handling of CO2. There are still numerous technical challenges to doing that. For Noble Corp, finding ways to mitigate these technical challenges will be critical to its near- and long-term plans in the CCS space.
“We understand the problem really well, and we understand some of the solutions that we could do,” said Zach Bruton, Senior Business Developer – CCS at Noble. “We’re now going down a path where we’re getting both operators and our vendors to all be on the same page around who can do what. We need to create the ecosystem, and then we can start laying steel and doing this at scale.”
Mr Bruton outlined several core challenges to drilling wells in CO2-rich environments that have been identified from various CCS research and development projects in which the company is currently involved. These learnings are helping the company as it develops a modular package of equipment, tentatively scheduled for commercial release later this decade, that drillers can use to modify their rigs for drilling repeatedly in pure CO2 environments.
Among other things, Noble is currently involved in a CO2 injection pilot for Project Greensand, a joint industry project between Ineos and Wintershall Dea in the Danish North Sea. Under this project, liquidized CO2 captured and transported from Ineos’ oxide factory in Belgium is injected via a well to the Nini West sandstone reservoir for permanent storage. The partners took FID in 2024 on a second-phase program to store up to 1.5 MMt of CO2 per year in 2025-2026 via the Nini platform and to drill a new well into the sandstone reservoir.
Noble has also been collaborating with DNV and BP on a CCS-enabled rig design for drilling and workover operations in a CO2-rich environment. Further, it conducted testing on the Noble Interceptor jackup last year, along with other theoretical and laboratory studies, looking at the effects of CO2 on materials and its environment.
One challenge Noble identified from this work was the weight of the CO2. As CO2 is 50% denser than methane, circulated CO2 settles downwards instead of rising upwards like natural gas. This makes it impossible to circulate out the CO2 at the topside, as one would do with methane in a conventional hydrocarbon drilling operation. Mr Bruton said this could pose a significant safety risk to rig crews.
“If you tried to circulate out the CO2 topside, it would literally fall back onto your drilling floor, and now you have this incredibly toxic CO2 in the air that has a knack for displacing oxygen. If you see even a slight decrease in oxygen, you will feel that in your tissues. If you get too high a concentration of CO2, people can get dizzy, get headaches, even pass out, and they can eventually die if the CO2 levels stay high enough for long enough.”
To address this concern, Mr Bruton said rigs drilling and working in a pure CO2 environment should not use their legacy ventilation lines for venting CO2.
The modular drilling package that is under development will feature a second ventilation line that ejects CO2 downwards into the ocean. “Ideally, we don’t want CO2 ever going above your personnel, so you’re never at risk. You want to process the kick below your well control equipment and eject it off to the side and down. When it goes down, it meets the ocean. From what we’ve seen in our studies, it will dissipate into the water within minutes.”
However, even with a second ventilation line, drillers should still build additional contingency plans in case CO2 manages to leak onto the drill floor. Noble is also adding a sensor package that will detect if CO2 concentration reaches above a certain point. These sensors will be placed on the lowest levels of the rig where people typically operate – around the drill floor, around the BOP, the cantilever and the accommodation systems.
The drilling package will also include individual breathing apparatuses for personnel in the instance of increased CO2 exposure on the rig.
“The idea is that the people will put on the breathing apparatuses and wear them until the HSE guy gives the thumbs up that the CO2 levels are fine,” Mr Bruton said. “Really, the risk of CO2 exposure is more for the personnel than the equipment. It’s not like H2S where it’s going to eat through everything right away. We’ll make sure everyone has a breathing mask, we’ll have our sensors, and everybody’s going to be trained accordingly on where to go.”
Corrosion is another issue Noble identified. CO2 and its compounds are corrosive, damaging steel, plastic and elastomers when in contact for extended periods of time. Further, its solubility in oil brings the risk of a blowout. This is not necessarily an issue for a rig drilling a single CCS well on occasion, but for repeated drilling in CO2-rich environments, this corrosive property can be a problem for the BOP, which is typically not made of CO2-grade metal.
Noble’s drilling package will likely include a bypass system made with Inconel, a nickel- and chromium-based superalloy known for high strength and corrosion resistance, that will process kicks before they reach the BOP.
“BOPs are giant pieces of equipment that cost tens of millions of dollars,” Mr Bruton said. “Upgrades would be expensive and time consuming. Here, you plug in the new system below your BOP, and then you have a CO2-grade kick-processing station where all of that metal is going to be upgraded. You can process the CO2 kick and eject it without getting your legacy systems involved.”
One other issue with CO2 wells that is still being addressed by the drilling package revolves around temperature. When CO2 is forced through a valve, such as in the choke line, it can expand rapidly. This causes the temperature of the CO2 to drop, which could potentially damage piping and lead to the formation of hydrates in the choke. Without any mitigation measures, the choke is likely to fail.
Noble identified this temperature issue primarily through metals and elastomers testing in the laboratory, as well as through studies of hypothetical cases based on planned CCS operations; it has not been observed in a test well yet. Mr Bruton said Noble aims to get “a hard value” for the temperatures it expects to see at the choke, as that value will help determine the best technologies to mitigate the temperature drop. Laboratory testing has shown potential temperatures ranging from -40°F to -72°F, well below the ratings for the materials used for the choke.
This year, Noble will participate in the drilling of a research well at the Petroleum Engineering Research, Training and Testing Lab at Louisiana State University (LSU). The testing will include the injection of CO2 in a test well, during which researchers will monitor when the CO2 itself changes phases, and what the temperature profile looks like as it changes phases from supercritical to gas.
While no date has been set for drilling the CO2 well at LSU, as various approvals and rig availability are still pending, Mr Bruton said the project should last through much of 2025. Noble will also continue its work with Project Greensand – the JIP partners plan to demonstrate one or two injection wells between 2025 and 2027, with an additional eight wells planned for 2027-2030 – and it will have discussions with operators and vendors on additional changes to the drilling package.
“Different operators have different concepts, and they’re at different parts of this journey when it comes to the equipment,” Mr Bruton said. “They’re trying to figure out their own risks – like, do they think it’s necessary to do an upgrade with the BOP or not? That’s part of the conversations that we’re having right now. Let’s see if we can all be on the same page with this. At the end of the day, we’ll work with customers in any way they deem fit.”
Mr Bruton said he expects to begin large prototype testing on the drilling package in 2026. Units are anticipated to be ready for commercial use by 2027 or 2028. DC