Standardization of reliability processes benefits decision support for subsea technology
ISO, API standards help to guide reliability management for subsea all-electric Christmas tree technology qualification
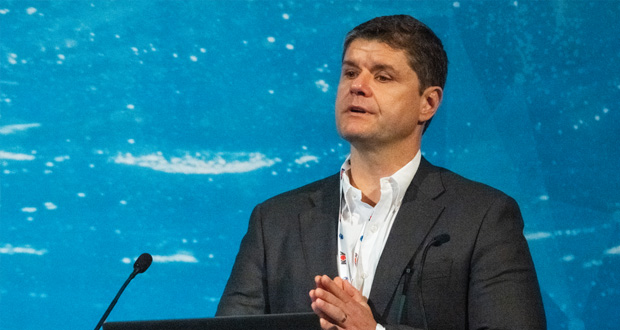
By Jessica Whiteside, Contributor
Qualification of new technologies in oil and gas can take years — no surprise in a sector where equipment failure can have costly and catastrophic consequences. Crafting a robust reliability management program aligned with international standards has been an essential part of the technology qualification process for joint industry projects (JIPs) to develop a standardized subsea all-electric Christmas tree (eXT) and associated components.
Technology evolution
The industry has been pursuing commercialization of the subsea eXT concept as a more sustainable alternative to traditional electro-hydraulic trees for well over a decade. TotalEnergies introduced the first subsea eXT in 2008 at its K5F development in the North Sea. That model, while successful operationally, did not prove to be cost competitive. Subsequently, TotalEnergies and several other major operators and subsea production system suppliers launched multiple JIPs to work together to establish a more streamlined and cost-effective eXT.
The JIP approach has led to a high level of standardization in both specifications and the qualification process, with some eXT technology reaching technology readiness level (TRL) 5 on the API scale.
The industry is interested: The Underwater Technology Conference honored the eXT last year with its UTC Award for contributions to underwater technology. As Brazil pursues electrification to decarbonize its oil and gas sector, companies like TotalEnergies, Equinor, Chevron and OneSubsea are partnering with the country’s National Agency of Petroleum, Natural Gas and Biofuels to develop an eXT model for Brazil’s ultra-deepwater pre-salt reservoirs. And future eXT deployment could extend beyond oil and gas. While the Northern Lights carbon storage project will use traditional subsea trees when it debuts on the Norwegian Continental Shelf this year, all-electric trees could be part of a future expansion.
The new eXT technology is designed to simplify the subsea architecture by reducing the need for hydraulic infrastructure, including the umbilical and related topside equipment, which creates the potential for longer step-outs.
The eXT relies on battery-based rather than spring-based actuators, reducing the risk of mechanical breakdown. Electrification occurs via a subsea cable that includes fiber-optic lines for communication and enables enhanced status monitoring and valve control for emergency shutdown and other functions. The critical nature of the equipment, as well as its relationship to efforts to electrify other elements of the subsea field, has led the JIP partners to integrate reliability management methods and technology qualification processes.
“Any alterations to the design need to at least maintain or, preferably, improve the reliability to ensure safety,” said Alexandre Braga Lacerda, Technology Manager with OneSubsea, who spoke about reliability and quality management for eXT technology qualification at this year’s Offshore Technology Conference. He and co-speaker Runar Østebø, Advisor Subsea Technology and Operations for Equinor, shared insights from their companies’ JIP collaboration and discussed the value that industry collaboration and attention to international reliability standards can bring to the development of novel subsea technologies.
International standards
In addition to functional safety, quality management and subsea technical standards, the eXT technology qualification process has been guided by reliability management practices prescribed by international standards for assessing technical risk, particularly those from the International Organization for Standardization (ISO).
These include the ISO 20815:2018 standard on production assurance and reliability management and the ISO 14224:2016 standard on collection and exchange of reliability and maintenance data for equipment. Such international standards, which often inform national regulations, reduce the need for companies to develop bespoke requirements and specifications. However, companies involved in technology qualification should assess whether their existing governance needs updating to accommodate new features of the novel technology.
“The application of international standards was very important for us as it governs decisions on both sides, not only on suppliers but on the operators, as well,” Mr Braga Lacerda said, calling these standards “fundamental” to the achievement of a reliable and robust system.
Reliability management program
Development of the eXT reliability management program was a joint supplier-operator effort that followed project risk categorizations in ISO 20815:2018 and technology qualification methodology in API RP 17Q:2018 and DNV-RP-A203:2019.
The reliability process began with the creation of an operator-defined reliability business case that charted performance objectives and related requirements. It identified the main reliability target as technical availability – the percentage of time available for operation of the equipment when only corrective maintenance is included in the downtime. A secondary target was operational availability, which includes both corrective and preventive maintenance in the downtime. The goal for both these objectives was to achieve better performance than traditional electro-hydraulic controls systems.
A multidisciplinary team was tasked with steering the reliability management program. They assessed and verified the technology’s ability to meet the operator-defined objectives at the component and product levels. This included putting the concept, component and design through multiple rounds of failure modes, effects and criticality analysis (FEMCA) and other risk assessment and qualification testing, before moving on to final system-level assessments.
This comprehensive evaluation can be time-consuming as the various analyses can identify risks that need to be addressed or opportunities for improvement that need further investigation, but “it’s important to reiterate this process as many times as needed,” Mr Braga Lacerda said. “Do not focus on reliability only as an end result or outcome. Incorporate considerations for reliability along the way, from concept to close-out of the project.”
Data reliability
An important element of technology qualification is getting the right data to support realistic reliability predictions, and the reliability data qualification process outlined in ISO 20815:2018 is a good place to start. However, finding applicable data can be challenging for a novel technology as industry event databases derived from ISO 14224:2016 may not always provide sufficient depth of detail on similar technologies to enable accurate comparison; if there is uncertainty, you may need to consult alternative data sources.
For instance, with electronic components, Mr Braga Lacerda said, the technology changes so rapidly you will need to seek a state-of-the-art source to ensure the data and methodology are up to date. Ideally, the latter will incorporate failure rate prediction models that take environmental factors and life-cycle considerations into account. Reliability data screening for the all-electric project drew from sources such as the exida Component Reliability Database Handbook Set and the Nonelectronic Parts Reliability Data, among others, and was supplemented with theoretical justification and expert judgement where needed.
Historical data from an operator or supplier’s experiences with similar equipment can become an input into the estimation process, Mr Østebø said. While history is not necessarily a forecast for the future, it creates an important framework for realistic predictions.
“When it comes to new technology and then using the historical data, sometimes people say, ‘Well, you cannot use the historical data,’ but that’s not completely true because by what we call the reliability data qualification process, we assess the validity and the relativeness of the historical data,” he said.
The ability for suppliers to work closely with JIP operator partners who will be the future end users of the system has helped to expedite reliability management decisions and put everyone on the same page, Mr Braga Lacerda said.
“We have gone through a lot together. Having the inputs from the operational philosophy makes a difference.” DC