Companies zero in on cementing process to have outsized impact on well construction emissions
Solutions being deployed include well planning and emissions monitoring software, as well as technologies with reduced Portland cement
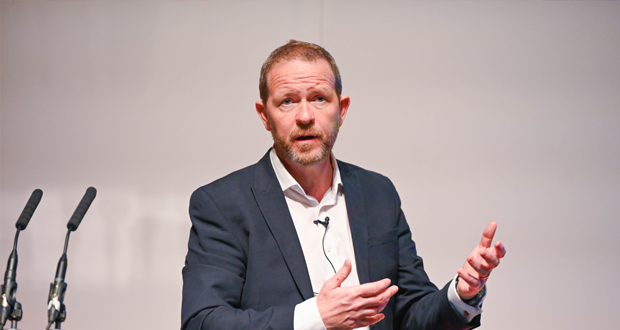
By Stephen Whitfield, Associate Editor
As the world continues to move toward a low-carbon future, the oil and gas industry’s ability, to not only reduce its emissions but also to quantify its emissions reduction performance, has become a priority.
One component of the well construction process with significant potential for emissions efficiency is cementing. Studies have shown the production of cement to be an emissions-intensive process involving heating kilns to very high temperatures, as well as calcination, a chemical reaction that occurs when raw materials like limestone are exposed to those high temperatures. Other steps like quarrying and transport also add to the emissions footprint.
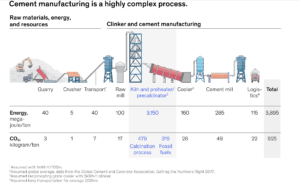
One part of BP’s work in this area is its Well Design Optimizer software program, launched last year. It’s a tool that its engineers can use to estimate greenhouse gas (GHG) emissions as they are planning wells. Cementing is one of four components that the software measures, along with fuel usage, planned testing and planned casing, Mr Therond explained in at the 2023 IADC World Drilling Conference.
The software uses pre-established emissions factors to obtain estimates of CO2 generation from various activities. Emissions factors are representative values that attempt to relate the quantity of a pollutant released into the atmosphere with an activity associated with the release of that pollutant. When multiplied by activity indicators input by the drilling engineer, the software can provide an estimate of the CO2 emissions that the given activity will generate.
Mr Therond noted that the software is not a tool for reporting or calculating emissions; the estimates generated by the software are only shared within BP and with its third-party contractors. The goal, rather, is to help personnel decide if any actions can be taken through better well planning to help reduce emissions.
“This is a tool for estimating emissions so that drilling engineers can understand what options they have to reduce emissions without compromising the well’s construction,” he said. “It might sound very simplistic, but I think this is the first step, so we can start understanding and acting upon these numbers. Right now, we don’t have the tools that allow us to have quality conversations with the drilling engineers.”
One of the first projects where BP deployed the Well Design Optimizer was an offshore well drilled last year in the Mediterranean Sea. The process began by entering data related to:
- rig type (drillship);
- number of days planned to drill the well (183);
- estimated diesel consumption (31 tonnes/day);
- the type of well testing (flaring);
- the specific gravity of the gas flared during testing (0.70);
- duration of testing (1 day);
- the production rate during well testing (50,000 standard cu ft/day); and
- the slurry densities for each hole section in the well.
From these inputs, the software generated an emissions estimate for the well, multiplying select variables by given emissions factors for each variable. It estimated that the well would generate nearly 24,000 tonnes of CO2 over its lifetime, and only 2% of that would come from cement usage. Since that is within the 1-5% average range BP typically sees, it confirmed no action was required to revise the well plan and cement usage. If the estimates had been abnormally high, however, the operator could have taken early steps to alter the design.
Reducing Portland cement in completions
Halliburton is also working to help operators reduce emissions from cementing through its Verified Integrated Design Application (VIDA) and Envana Catalyst emissions monitoring software. VIDA is a design modeling software that identifies the risk mitigation factors within a well’s design; it can also be paired with Envana Catalyst to provide a comprehensive estimate of the amount of CO2 generated by specific pieces of equipment used on a well during the well’s lifecycle.
To get these estimates, the drilling engineer first inputs basic data for the planned well, including the number of days planned to use a given piece of equipment. Those inputs are then automatically transferred to the Envana Catalyst program, which runs them against other inputs and emissions data stored in a historical database from equipment used on similar wells drilled by Halliburton clients.
Using the inputs provided by the drilling engineer, as well as the historical data, the Envana Catalyst program calculates emissions estimates for the rig’s equipment and displays the results within VIDA. Once the well is drilled, the emissions data from the equipment is input into Envana to provide additional data points for future well designs.
“We have the information from years and years of our operations, and thousands of calculations in different geography iterations,” said Patrick Lynch, Regional Business Development Lead – Low Carbon Ventures at Halliburton. “We’ve learned a lot because, if you’re simulating cementing operations around the world, there are a lot of different options you can take with the blend.”
The software systems, when combined, can provide a granular breakdown of which parts of the drilling and completions process are generating the most emissions. At the World Drilling conference, Mr Lynch discussed a pair of cementing operations, one from an offshore well and one from onshore. For the offshore well, users input the expected pumping hours and idle hours for the rig’s cement pumping unit, along with the location of the well, the estimated mileage transporting the cement from the manufacturing site to the rig, the type of cement used (Portland cement), the batch mixer and the liquid additive system.
From those inputs, the Envana system estimated that 98% of the emissions generated from cementing would come from the production of the cement blend, with the remaining 2% split among the batch mixer, cement pumping unit and the liquid additive system.
The onshore well saw similar results: It was estimated that 81% of the cement job’s emissions would come from the cement blend, 14% from the consumption equipment (the cement pump truck, storage bin and the bulk truck), and the remaining 5% from transportation of the cement to the wellsite.
These examples were indicative of a larger trend Halliburton noted in its emissions data, Mr Lynch said – that the production of cement accounted for more than 90% of the total emissions from its oil well cementing operations. This highlighted the importance in reducing the amount of cement used. In 2021, the company launched its NeoCem E+ and EnviraCem systems, which contain a reduced amount of Portland cement mixed with locally sourced byproducts. Compared with the company’s conventional cementing system, the NeoCem E+ system contains 50% less Portland cement while EnviraCem cement contains 70% less.
Using locally sourced byproducts is the key differentiator for these solutions, Mr Lynch said. When companies create cementing solutions with reduced Portland cement, they often sub it out with mined materials that can only be found in limited locations around the world. This leads to additional CO2 emissions from the extraction and the logistics of transporting them to a facility for processing.
Because NeoCem E+ and EnviraCem “are heavily comprised of locally produced products and some minor manufactured components, they can provide reduced CO2 emissions in our cementing operations,” Mr Lynch explained. “The point is, rather than having a single source for the raw materials in our cement and then transporting that around the world, we’re trying to take away the transport-related aspect of the emissions wherever possible.”
In addition to emissions-related benefits, the reduced-Portland cement systems can also better withstand the downhole demands from continual pressure and temperature changes throughout the life of the well compared with conventional cement systems. He credited this to Halliburton’s approach to specifically tailoring its reduced-Portland cement blends to the needs of specific cementing jobs.
“We can leverage our database of lab testing along with our physiochemical understanding of the materials to create tailored engineered systems designed to produce specific properties downhole. Every cement is specifically engineered to do an efficient job, and we’re seeing benefits in properties like thickening, fluid stability and fluid loss control,” he said. DC