Surveillance system tracks movement of personnel and equipment to reduce risk of injury in rigs’ red-zone areas
In GOM field trial, system helped to identify blind spot around moving tong system
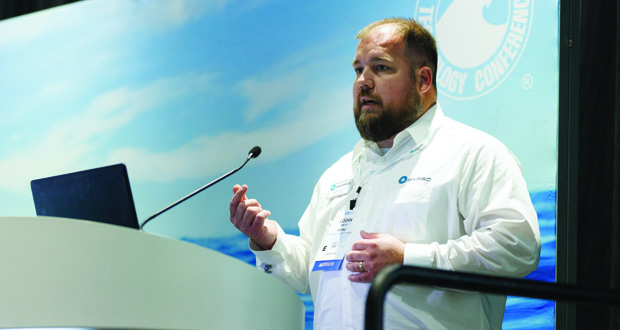
By Jessica Whiteside, Contributor
A hazard monitoring system that uses sensors to track personnel and equipment movements on the rig floor has the potential to improve the safety and efficiency of offshore well construction activities, according to an Expro presentation at this year’s Offshore Technology Conference.
The system digitally tracks equipment and personnel movements on the rig floor in real time. The tracking enables monitoring of personnel entries into the red zone, with the goal of preventing collisions between humans and machines. OSHA statistics indicate that three of every five onsite fatalities in the oil and gas extraction industry are a consequence of struck-by/caught-in/caught-between hazards.
Risks can be particularly high when operations are only partially automated and still have a manual component that requires human intervention. As the deepwater segment moves toward greater use of remotely controlled equipment, there will still be individuals that may need to enter the red zone, such as casing, completions or mud system personnel, said Logan Smith, Product Champion for Expro.
If someone is running a remote-operated machine from a panel, for example, their view may be blocked at some point and they may not notice someone else entering the red zone. Current anti-collision systems on rigs are designed around the equipment state – making sure the top drive won’t collide with the pipe racker, for example – and not the personnel state, Mr Smith said. Anticipating more automation of tubular-running services, Expro developed a central monitoring command and control solution that could increase awareness of personnel proximity to equipment in the red zone and help stop unsafe operations before it’s too late.
System design and requirements
The monitoring system uses ultra-wideband radio frequency technology to provide precision location and movement information within set boundaries established for safe operations. Anchors (wired or battery-powered) are mounted in key locations around the rig floor. These anchors transmit and receive signals from battery-powered sensor tags worn by personnel and mounted to equipment. Mr Smith described the concept as similar to the technology used in some shipping facilities to track the location of forklifts.
When a worker comes to the rig floor, they put on a tag that will enable their position and movements to be monitored in real time. When they leave the rig floor, they return the tag to check out of the system. Each tag is configured with a set of anti-collision rules and is represented in a 3D rendering on the system’s application screen.
The location data – accurate to within 10 cm – is transmitted to a centralized network hub that controls equipment movements and locations. The system is run from a laptop located inside the driller’s cabin, which serves as a human-machine interface and is connected via Ethernet cable to a network electrical box on the rig floor. Control systems for each tool being monitored communicate with this network electrical box, which is equipped with an emergency stop (E-stop) connection.
The system can be configured to halt rig equipment automatically when an unsafe human interaction is detected within the predetermined red zones. E-stops can also be used to manually stop the system. Further, the system can be configured to alert the equipment operator to certain situations and wait for a human decision on the next step, rather than automatically stopping the equipment.
“It’s kind of redetermining how we run these rig floors,” Mr Smith said.
Operational benefits
In addition to identifying unsafe situations where personnel may be too close to moving equipment, the system provides data to help end users make decisions on risk mitigation and operational performance that could lead to cost savings, not least by reducing corrective costs associated with lost-time incidents.
The movement data collected by the system can be displayed via a customizable dashboard to aid analysis of personnel behavior in red-zone areas. For example, the data can be shown as a heat map visualization that displays the locations of personnel and equipment tags, capturing the path of movements and identifying areas of movement concentration. Red-zone entries can also be presented in graphical form.
This kind of information can provide insight into where a procedure should be improved in the future, Mr Smith said. He added that the system can be helpful in seeing where variances in behavior may arise between different crews, particularly from short-service supports, and providing opportunities to increase their situational awareness.
“You see a short-service employee moving around the rig floor at various points where they shouldn’t be, then we’re able to step in at that point in time and say, ‘During this operation, here are your safe points … You shouldn’t be wandering from this place to this place.”
The system can be applied easily to third-party equipment and personnel on the rig, even with multiple third parties sharing the rig floor. If a third party is bringing in a piece of equipment during a casing operation, for example, “we want to be able to slap the system on there and say we know where that piece of equipment is during this movement so we can figure out how to make those operations even better,” Mr Smith said.
Field test successes
The first field trial for the surveillance technology was held on an offshore rig in the Asia Pacific region and focused on a tong system and rotary hand slips. The goal was to observe trends in personnel behavior around entering the red zone during operations such as tubular connection and makeup. The system tracked personnel movements over an 18-hour period, recording more than 275,000 data points. The team was able to feed that data back to the customer to support analysis of rig safety and process improvement opportunities.
A second field deployment, held on a bigger deepwater ship in the Gulf of Mexico, tied the system into multiple pieces of rig equipment involving activities like pipe rack-back and running operations. During this trial, the team allowed the system to complete a shutdown operation if personnel entered the red zone during an operation. The system worked as expected, halting the moving tong when someone got too close. At first, the personnel overseeing the operation couldn’t figure out why the system had stopped the maneuver – until they saw a person walking out from behind the tong. The individual had previously been out of their line of sight. Such awareness could then be used to adjust the procedure to remove the blind spot identified by the system.
“It highlighted the fact that complacency is there,” Mr Smith said. “People entered the rig floor that weren’t initially part of the operation.” DC