Digitizing logistics process improves offshore rig communications, reduces errors
Side benefit of streamlining the tally workflow was the potential for reducing personnel on board
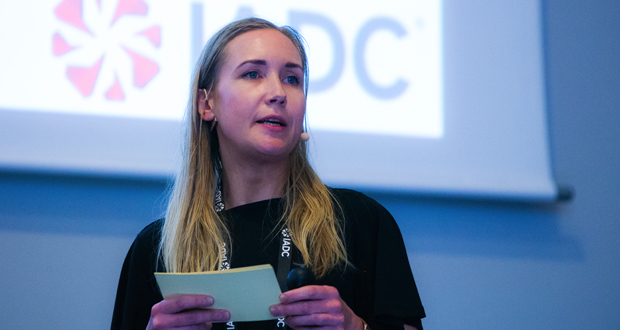
By Jessica Whiteside, Contributor
The tally is a key logistics tool on an offshore rig used daily to track and manage the inventory of pipes, casing and other downhole components. Traditionally, the tally is compiled manually, but a pilot project offshore Norway proved the process could be digitized. Rig efficiency and communications were improved, and the tally led to a reduction in workload for roles on the drill floor and pipe deck.
The pilot received support from the Research Council of Norway and involved the collaboration of Equinor, Transocean and HMH. Representatives of the HMH project team shared their experience and discussed the benefits of the digital tally approach at the 2022 IADC World Drilling Conference in Paris on 21 June.
“The goal for us is to create solutions and products that are relevant, that are user friendly and that provide enhanced situational awareness at all levels of the operation,” said Ann Jorid Haugland, HMH Head of Automation & Digitalization.
User involvement was a hallmark of the pilot initiative. The system designers headed out to the rig to hold workshops with onsite crews and operational experts to identify areas for improvement in the existing tally system and associated work processes and to gain insight into how information was communicated between offshore and onshore personnel.
Ms Haugland described the rig’s original tally process as “extremely manual.” A lot of the data was recorded with pen and paper, and there was spotty sharing of information between roles with different responsibilities and between systems owned by different actors. This created the potential for human error and expensive downtime. In some cases, an operation would be postponed while people double-checked the manual tally.
Susanne Håland, Lead Functional Architect for HMH, said the rig crews took ownership of the digitalization effort and there was little resistance to change. In fact, she said, “many loved it and were eager to learn about the end product.”
Implementing a digital solution
The digital tally workflow starts onshore when the items are ordered and enter the system. It continues onboard the rig when the items arrive and are identified. The digital system tracks each item and enables the tally to be easily shared with all locations so there is common knowledge about where each component is at any point in time, along with information on its history, condition, measurements and other characteristics.
Drillers can use this data to develop a digital running tally to aid in the planning and execution of the next drill string. Users view the digital tally on a series of interactive dashboards that enable information to be analyzed and communicated more quickly and easily. The dashboard can even alert users if the wrong item is being added to the drill string.
This enhanced data sharing has enabled greater functionality and more efficient ways of working, Ms Haugland said. She noted that run planning that used to take an assistant driller two or three hours with the manual tally now takes 30 minutes. Personnel also made fewer mistakes after the launch of the digital system and spent less time looking for items.
“This is all about taking control of the information and sharing it both with our systems and other systems to provide smoother and more efficient operations,” Ms Haugland said.
While reducing personnel onboard was not a primary objective of the pilot, the ability of the digital system to alleviate workloads and facilitate communications between personnel in different locations created what Ms Håland called an “information foundation” that allowed some tasks to be moved off the rig and done onshore, while others could be performed with reduced staff.