Physics-based approach improves drilling of FORGE geothermal well by identifying, mitigating limiters
Workflow emphasized continual monitoring of EDR data and constant changes in well design, drilling practices
By Stephen Whitfield, Associate Editor
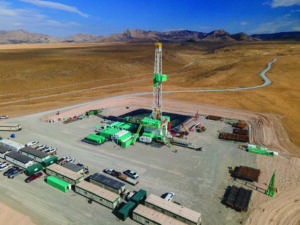
Geothermal drilling is a potentially valuable source of green energy, but scaling it globally will require developers to overcome a number of hurdles. For example, geothermal wells often require drilling through extraordinarily hard rock that can damage expensive equipment. It can also lead to low rates of penetration (ROP) and poor overall drilling performance that can lower a project’s economic value.
While new technologies are often seen as the solution to poor geothermal drilling performance, the application of physics-based drilling practices and workflows is another approach that can help drillers realize significant performance gains, according to Sam Noynaert, Associate Professor of Engineering Practice, Petroleum Engineering at Texas A&M University. This approach doesn’t require developing new tools or advanced technology, he added.
However, in order to deploy physics-based drilling, “we have to continually work with the rig teams and create new workflows that are going to change the way that geothermal drilling organizations really work, just as we’ve done in oil and gas,” Dr Noynaert said during a presentation at the IADC Drilling Engineers Committee’s Q2 Technology Forum on 30 June. “It requires changes to the way you drill your wells.”
Last October, Dr Noynaert and fellow A&M professor Fred Dupriest began working with the drilling team at the Frontier Observatory for Research in Geothermal Energy (FORGE). Located in Milford, Utah, FORGE is a US Department of Energy-funded site for the study and development of geothermal resources. The A&M team aimed to bring their knowledge of physics-based practices and workflows to help refine drilling methods for geothermal projects. Primarily, the team aimed to teach the FORGE crew how to use the physics-based approach to identify and eliminate performance limiters in geothermal drilling.
The work began with FORGE 16A(78)-32, the first deviated well to be drilled at the FORGE site. Drilling operations ran from late 2020 to early 2021.
What is physics-based drilling?
Physics-based drilling focuses on identifying the limiter that prevents drillers from increasing weight on bit at any given time, such as bit balling, stick-slip or an issue with the bottomhole assembly. It requires understanding the physics behind that limiter and then mitigating the limiter in real time by redesigning the well or changing drilling practices.
Based on this concept, Dr Noynaert and Mr Dupriest instructed FORGE crew and management on the physical processes involved in drilling, including drill bit specifics, optimal drilling speeds and the best way to identify limiters.
A workflow was developed that emphasized continual monitoring of data coming from the electronic drilling recorder (EDR). This included the A&M team providing annotated screenshots from the EDR run with their analysis of various trends and other findings involving WOB. For instance, a screenshot could show evidence of an event at a specific depth that could initiate a wear trend on the bit.
In the post-run analysis, the Texas A&M and FORGE teams, along with other vendors like NOV, Schlumberger and Ulterra, would analyze the findings and consider possible engineering redesigns.
Dr Noynaert emphasized that the workflow necessitated much more than the “hit and run” approach. “We’re on call 24/7,” he said. “You can’t just train and walk away. You can’t just put an extra page in a drilling program and walk away. If you want to take this approach into geothermal, you have to understand that you have to remain involved for the entire well.”
Drilling of FORGE 16A(78)-32 was finished 60 days ahead of schedule, something that Dr Noynaert attributed directly to the new workflows. “This approach was not a new technology. It was not lasers or crazy NASA space-age stuff. It was an overall workflow and process, and the key to success here was the involvement of the team.”
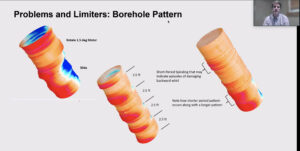
Well testing and limiters
While most geothermal wells are vertical, this well was deviated at a 65° angle from vertical after reaching a depth of 6,000 ft. That angle was then maintained for the remainder of the well’s trajectory before reaching a total measured depth of 10,987 ft. The final 6,000 ft of the well was drilled through high compressive strength granite. The rig used was Frontier Drilling’s Rig 16, a 1,500-hp land unit with a 7,500-psi fluid system.
Because the well was part of a scientific project, not a commercial operation, drilling was intentionally halted more frequently during each run in order to collect data. These pre-planned trips provided bit forensic data that proved particularly useful in identifying limiters, as bits were often pulled in the early stages of damage.
One of the limiters identified was the presence of high-frequency borehole patterns throughout the well. 3D models of caliper measurement data revealed short-period spiraling.
This may indicate episodes of damaging backward whirl, a severe form of vibration that creates high-frequency, large-magnitude bends that result in high rates of component and connection failure.
There was also a more than 80% reduction in ROP as drilling progressed, yet mechanical specific energy measurements indicated that the bits did not suffer noticeable damage despite drilling through the tough granite. This was a unique phenomenon with no clear explanation, Dr Noynaert said. Data showed the presence of high-frequency torsional oscillation, and the Texas A&M team is reviewing its potential impact on ROP. The presence of low-gravity solids in the drilling fluid is also being analyzed.
The team also noted small wear flats whenever it pulled the bit for a core point or a logging run.
“It’s one of several theories we’re considering, where you’re getting a very small wear flat developed due to heat. It’s starting at the chamfer, and then you degrade and it would reach an equilibrium. Then you could drill ahead at a lower ROP until another dysfunction, such as whirl, actually generated run-ending damage if you pull the bit. There are some holes in that theory, but it’s thought to be a thermal-related damage,” Dr Noynaert said. DC
Click here to watch a video about lessons learned transitioning from oil & gas to geothermal drilling.