Conventional drilling optimization knowledge tapped to help NASA access water on the Moon
By Stephen Whitfield, Associate Editor
For years, scientists have known that water exists on the Moon, likely in the form of ice in deep craters at the Moon’s poles. As these craters are among the coldest places in the solar system, reaching temperatures as low as -233°C, the prospect of exploring for these resources has always appeared unfeasible.
But that previously impossible task may soon be made possible by leveraging the knowledge gained from conventional oil and gas drilling on Earth.
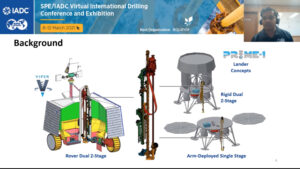
While the differences in environment are significant, the expertise of drilling engineers in designing and executing wells in extreme conditions on Earth is being tapped to help NASA drill on the Moon. Researchers at the Colorado School of Mines believe the reliability of lunar exploration missions can be improved with comprehensive, real-time drilling optimization algorithms. Similar to what are used in the oil and gas drilling industry, these algorithms rely on real-time drilling response mechanisms to adjust various control parameters, ensuring closed-loop automated drilling from the lunar surfaces.
A project funded by an Early Stage Innovations Grant from NASA’s Space Technology Research Program is working to develop these algorithms, according to a presentation at the 2021 SPE/IADC International Drilling Conference on 12 March. The intent is assist NASA with future lunar missions.
If these missions prove the existence of water and ice on the Moon, it could represent a revolutionary shift in space exploration, said Deep Joshi, Senior Drilling Engineer at DrillDocs, a developer of wellbore cleanness and stability software. He’s also a Research Associate at the Colorado School of Mines.
“This water could play a vital role in establishing sustainable human colonies on the Moon,” Mr Joshi said. “It can be used for everything, ranging from human consumption to infrastructure development to fuel consumption.”
Drilling for water and ice on the Moon comes with some different potential hazards than drilling on Earth. Adverse conditions on the lunar surface include radiation, meteoroid strikes and the uncertainty that comes with operating in a vacuum, like the atmosphere of the Moon.
In addition, the lunar surface has a considerably different composition than the rock that a driller would typically encounter on Earth. The lunar surface is covered by a thin layer of fragmental and unconsolidated rock material known as regolith. Underneath that layer is lunar soil, which bears little in common with terrestrial soils since it contains no organic matter and is not formed through biologic or chemical means. As lunar soil is not exposed to the wind and water that shapes the earth, it tends to be sharper than terrestrial soil, with fresh fractured surfaces.
All of these differences mean that optimization objectives are different in a lunar drilling operation compared with terrestrial drilling. On Earth, drilling optimization objectives typically include maximizing ROP and minimizing tortuosity and vibration. On the Moon, however, Mr Joshi said power consumption and the reliability of the operation are much more important considerations. Instead of finding an optimal ROP to minimize tortuosity and vibration, the goal is to create algorithms that could determine the best ROP and RPM to minimize power consumption, drilling time and choking of the auger used for moving cuttings out of the borehole.
For the study, researchers took conventional oil and gas drilling optimization algorithms and adapted them for the differing objectives of lunar drilling. They then conducted drilling tests on a drilling unit similar to TRIDENT, a rotary percussive drill and deployment system designed to be deployed from a roving platform. It is scheduled to be used on NASA’s PRIME-1 lunar mission in 2022 and its VIPER lunar rover in 2023.
The test drilling unit at the Colorado School of Mines utilized a three-phase AC motor controlled through a variable frequency drive to provide rotary actuation, as well as a precision ball screw controlled with a stepper motor that allowed for close control of vertical motion and ROP. A high-frequency data acquisition system installed on the rig measured the drilling force, the height of the drilling head, and RPM.
The tests used lunar soil representative samples and atmosphere and cryogenic (less than -150°C) conditions. After each test, researchers processed data through a filtering algorithm, and that processed data was used to train a regression algorithm to calculate torque and a classification algorithm to predict auger choking.
The regression and classification algorithms were then put through an optimization module and tested on drilling data for two digital twin boreholes drilled in a 3D lunar subsurface sample. Researchers chose an initial ROP and RPM for the drilling unit. Then, after every 10 seconds of drilling, processed data was transmitted to the optimization module. An iterative process identified an optimal ROP and RPM, which were then sent to the drilling unit’s control system, which updated the operating parameters on the unit.
For each borehole, the algorithms calculated an optimal ROP that was significantly higher than the test ROP and an optimal RPM that was significantly lower than the test RPM, Mr Joshi said.
After the operating parameters were adjusted, the drilling unit saw a 40% reduction in power consumption and a 75% reduction in drilling time for the first borehole, while auger choking was eliminated. For the second borehole, power consumption went down by more than 35%, drilling time was reduced by 50%, and auger choking was reduced by 90%.
An automated drilling control system is currently being implemented at the Colorado School of Mines with the optimization algorithms. Mr Joshi said the control system will be fine-tuned using drilling data from various of analog and cryogenic samples with different forms of water ice. Researchers will also test the effect of different PDC bits on the algorithms. While the drilling unit used in the test was similar to the TRIDENT drill that will be used on the VIPER lunar rover, Mr Joshi said the algorithms will have to be retested using data from NASA and updated specifically for the drilling systems that will be used during lunar missions.
“We will have to include the drilling data from those redone tests into the algorithms and retrain them on that data. After that, the algorithms will be much more efficient in working with the drilling system that NASA has,” he said.