Automated directional drilling gaining trust among industry users
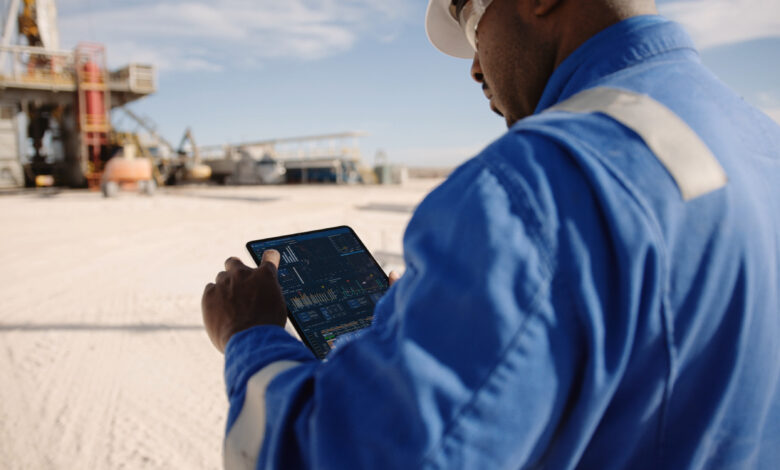
Innovations in software continue to enable better predictive capabilities, helping operators achieve repeatability and consistency in their wellbores
By Stephen Whitfield, Associate Editor
Unpredictable directional drilling performance can have a significant detriment on a drilling operation, leading to higher costs and potentially missed production. While many directional drillers perform at a high level, the practice of accurately predicting drill bit positioning and trajectory is difficult to master, and the human element means that failure is always a possibility.
To address these issues, the industry has increasingly looked to automation of directional drilling. Repeatability and consistency are recognized as the bedrock of the value around these automated systems.
“Drilling a record one day and then falling behind your expected days on well the next day is not acceptable in today’s environment,” said Marcus Howell, Director of Automation Technology at Patterson-UTI.

The next step beyond that, once predictability is achieved, is ensuring the quality of the wellbore drilled and accurate placement. “An automated directional drilling system that’s not incorporating the latest survey data analytics and accuracy and insight really decreases the probability for efficiency and optimizing reservoir recovery. Things like that matter for operators,” Mr Howell continued.
Patterson-UTI uses Cortex, a proprietary operating system commercialized in 2020, on its APEX rigs to host various automation applications, including those from third parties.
For example, the Automated Directional Drilling Control app utilizes a cloud-based FDIR (fault detection, isolation and recovery) system, developed by Superior QC, to provide real-time corrections and more accurate well placement. This reduces tortuosity and maximizes exposure to targeted production zones.
By deploying edge computing through the Cortex system, Patterson-UTI can now use advanced algorithms to stream large sets of downhole data and deploy fleetwide updates in a short period of time. The system has multiple communication adapters with read-write capability for EDR data, data from the control system and from third-party equipment.
Sorting out high-quality data with minimal latency is a must for any effective automated directional drilling system, Mr Howell said. “We collect copious amounts of data from our systems, but we have to deliver that insight in a useful manner. With Cortex, we can process valuable drilling data that generally gets overlooked from a wellbore perspective. It’s basically combining this data in a new manner, calculating a more accurate wellbore shaping trajectory at 15-ft increments. That allows our operator clients to make a lot more informed business decisions.”
Data management
Data management is indeed a key area where automated systems can make a difference, said Todd Benson, Chief Innovation Officer at Helmerich & Payne (H&P). Most variance in directional drilling is a result of differences in knowledge or experience between individual directional drillers. By having centralized data systems – which can connect with other systems across a customer’s fleet – the amount of knowledge that any single decision-maker has of a given drilling environment can be amplified significantly. This eliminates variance and ensures all drillers operate at the same optimal level.
“With downhole sensors, we’re still dealing with speeds that are relatively like smoke signals, and we’re dealing with lag times and distances that are quite cumbersome,” Mr Benson said. “But the algorithms in an automated system can essentially predict, recognize and expect things to happen before they’re actually confirmed by the sensors. That’s really the big advantage of an automated system, both as an aggregation of larger datasets and as something that can mine all those datasets.”
H&P made a significant stride in the automated space with its acquisition of Motive Drilling Technologies in 2017. Its bit guidance system, Mr Benson said, is the industry’s first use of cognitive computing to guide the directional drilling process.
The system runs on a Class 1-Div 2 industrial computer deployed on the rig, receiving real-time drilling and trajectory data using a standard WITS0 protocol. Self-learning algorithms create and analyze millions of potential steering options from sensor data gathered at directional survey stations, or reference points that correspond to a measured depth along the well path.
The system evaluates each path based on drilling time, tortuosity risk and future production potential. It then presents these evaluations to the driller, who can follow optimized turn-by-turn instructions it receives from any connected device.
The Motive system is used as part of H&P’s AutoSlide, a suite of drilling services that automates the control of surface equipment and steerable mud motors to optimize sliding in deviated and horizontal well drilling.
The company is also leveraging advanced physics models with DrillScan, a 2019 acquisition, to provide a better understanding of drill string mechanics and well integrity.
Eventually, these models are expected to form the foundation of H&P’s comprehensive system that incorporates automated directional drilling apps and automated geosteering apps.
Remote centers
Data visualization and analysis are at the heart of Patterson-UTI’s PTEN+ Performance Center in Houston, a central command unit dedicated to rig monitoring and analytics. Launched in 2018, the center is scaled for use on all of Patterson’s rigs. It is staffed by drilling optimization engineers, pressure-pumping analysts and directional drilling specialists who remotely monitor jobs to provide support for tool setup, troubleshooting and service consistency.

Mr Howell described the center both as a controlled environment designed to push internal performance and as a place that integrates the strengths of the automated system with the strengths of the people in the field. The company’s performance optimization team uses the analyses conducted by engineers at the performance center with its customers both in the office and the field, sharing lessons learned across multiple rigs.
“Data is at the heart of our center,” Mr Howell said, noting that operator customers have access to Patterson-UTI’s data dashboard and visualizations. “We have a big advantage in our ability to display control systems data, and that’s something that a lot of operators want to get into now. They want to know what parameters we’re running in any given section. They want more transparency, and we want to give that to them. They can see exactly what the drillers are seeing.”
Last year, Patterson-UTI also commercialized its cloud-based HiFi Nav wellbore placement service, which automates data transfer from the well site to the performance center. It utilizes algorithms to improve knowledge of the wellbore position during horizontal and vertical drilling and to reduce geological uncertainty in real time.
This year, the company is field-testing its cloud-based HiFi guidance, which takes the output generated by the HiFi Nav wellbore placement service and geosteering target changes to calculate steering decisions. The result will be to ensure the wellbore stays within the producing zone and optimal ROP range.
Performance centers are not a novel concept in the industry. Hess opened its real-time operations center in Houston in 2015, implementing an automated directional software guidance system to help improve motor slide drilling.

The center took oversight of the bulk of its Bakken drilling, supporting up to six rigs as part of the overall fleet. Due to the downturn and changes in the Bakken rig count, the real-time center has scaled with the activity level and currently supports two rigs there.
Hess now keeps two directional drillers in that center, and drillers at the rig have taken over all directional drilling activities at the wellsite.
Matt Isbell, Senior Drilling Advisor at Hess, said utilizing automation tools through the center has had a notable impact on the company’s efficiency in the Bakken. Since 2015, Hess’ well cycle time has improved by 37%, and its drilling and completion costs have dropped by approximately 20% since 2018. While the automated guidance software was not the sole reason for these gains, Mr Isbell said there’s no doubt it played an integral part.
“Our focus is really around reducing operational variations, and automated directional drilling has had a huge impact on that,” Mr Isbell said. “By putting all of our automation tools into one piece of configurable software, we’ve been able to consolidate the body of knowledge generated by an automated system and consistently make similar decisions across our operations. With this guidance system, we can reduce how much time we spend adjusting the trajectory of the well. Reducing that variation over time is what will drive the operational improvement.”
Cloud systems
Nabors primarily utilizes two technology platforms to enable automated directional drilling for its operator customers: SmartSLIDE, a directional steering control system that automates slide drilling, and SmartNAV, a collaborative directional guidance system. The two apps go hand in hand, each performing a different function of the directional driller – execution of the slide for the former, and automated directional decision making for the latter.
Both apps are integrated with RigCLOUD, a data visualization software that allows Nabors to process KPIs in real time and collect information on how the SmartSLIDE system is performing, which will then allow personnel to modify how the system is tuned to a particular area.

“It’s like driving an autonomous vehicle,” Austin Groover, Senior Operations Manager at Nabors, said in describing how the two apps work together. “You need the GPS system to tell you when to turn, when to get off the highway and how to avoid the traffic that’s coming up, but you also need something that actually navigates the vehicle. You need the system that accelerates, decelerates, turns the wheel and compensates for snow on the road.”
As of Q4 2020, the two apps have been used to drill more than 655 wells across seven basins.
In 2020, Nabors deployed SmartNAV and SmartSLIDE for an operator in the Delaware Basin. The challenge was to improve drilling performance while maintaining wellbore quality, as well as to provide a proof of concept for automated directional drilling across the operator’s rig fleet. Deployment of these automated solutions increased toolface control during curves by 35%, reduced time associated with drilling the lateral by 14% and was 61% faster than their fastest offset curve.
These performance improvements enabled well delivery 2.84 days ahead of the operator’s target offset. Because of the success of this deployment, the SmartNAV and SmartSLIDE systems are now utilized on 100% of this operator’s rig fleet.
For drilling contractors, automated directional drilling technologies will only become more important going forward, as it’s a key enabler for maximizing the footage delivered for an operator per day. “From our perspective, now that you’re using an automated system, you can trust that the decisions being made are the optimal decisions and that they take in mind the important metrics the operator has laid out,” Mr Groover said.
People in an automated system
Besides consistency and repeatability, one of the other key advantages to automated directional drilling is a reduced need for people at the wellsite. For instance, Hess now only uses one directional driller for every six wells in its Bakken operations, compared with 12 directional drillers per six wells five years ago. Mr Isbell noted the significant positive safety impact of moving these personnel out of the field, not only because of reduced exposure but also because having less variation in drilling processes and standardizing the work leads to enhanced safety, quality and delivery performance.
However, real-time centers and other automation efforts shouldn’t be viewed as a means to get people off the well site, he added. Rather, they’re should be viewed as ways to get new tools to people so they can run a rig more efficiently and safely. “The way we’ve kept our workers involved is by giving them responsibility for these systems and showing how they can continuously improve those systems,” Mr Isbell said. “That’s giving them additional skills as they master the software and the digital processes. The real-time center plays a critical role in this, whether it’s enhancing the software and the algorithms that we use to deliver the work or coming up with requirements for a new solution.”
Trey Adams, Vice President of Digital Operations, Sales and Marketing at H&P, agreed that humans will continue to play an important role, even in an automated directional drilling system. However, the advancement of these systems over time will lead to a redefinition of roles, with the directional driller becoming less of a technician dealing with physical, moving devices and more of a digital worker. What won’t change is the importance of still having that knowledge of the physical rig and the well. Even as the industry incorporates higher levels of automation into directional drilling, there will always be the need for a human driller on the rig to make judgment calls when necessary.
“Some elements of drilling are very difficult to digitize, and it will be very difficult for the directional driller to let go of that control,” he said. “The rigs are always going to need people in a practical sense because the nature of the rock we’re drilling is not homogenous. Automated systems and algorithms can – and will – do really great things, but you need people to oversee and make some of the final decisions.”
Mr Howell acknowledged organizational buy-in as a challenge for the industry in implementing automated systems. With Patterson-UTI, he stressed the importance of “delivering a message” that the directional driller is still an important piece of their organization. He noted that owning its own directional drilling company – MS Directional, acquired in 2017 – has allowed for automated systems to be built in-house, with collaboration across disciplines. That flexibility has made it easier for the company to generate buy-in.
“We try to make sure that our guys know there’s a place for them, even if not on location,” Mr Howell said. “We bring our people in when we’re working with our applications and we ask their opinion. At the end of the day, they are the people using the system day in and day out. The directional driller needs to fully understand how the systems work. We can’t take the human aspect fully out of directional drilling today, but we can scale people’s abilities and better utilize their skillsets in more crucial aspects of our operations.” DC