Nabors develops MPD Return Flow Pathways procedure to manage non-well control use of rig chokes
Internal Well Control Committee evaluates BOP stack configurations to prevent deviations from best practices
By Richard Grayson & Adam Keith, Nabors
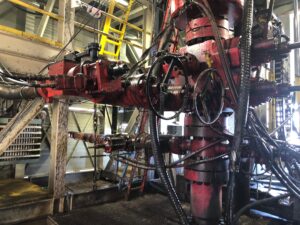
Shale formations are common drilling targets and frequently present many challenges. Examples include swelling, sloughing, general wellbore instability and natural fractures, which can mask over/underpressured formations. These can be common in high-pressure, high-temperature wells in formations such as the Tuscaloosa Marine shale and Haynesville shale.
Further, rotating control devices (RCDs) are becoming more common. They convert an open-loop system into a closed-loop system, providing an additional barrier for safety, as well as environmental benefits like capturing background gas while drilling wells and ensuring it is properly handled or flared. More importantly, however, they also enable managed pressure drilling (MPD).
MPD can serve as a solution to most, if not all, of the complications listed above. It can also assist in overcoming the inevitable cost of dealing with these complications. There is a down side, however, and that involves making compromises that may seem reasonable but ultimately prove to be shortcuts that do not yield the safest or most effective solution possible.
Drawbacks of Technological Advancement
RCDs are used for more than just MPD wells. With other advancing technologies through rig integration, automation and advanced choke actuation techniques, there is an ability for risky – or at least debatable – methods of drilling.
“Poor-boy” MPD is a common term used throughout the industry, with several definitions, but usually it refers to utilizing the rig’s well control chokes to apply pressure while drilling and/or during connections, not well control events. This may not be new to the industry, but that does not negate the fact that primary well control equipment is being utilized for purposes other than well control.
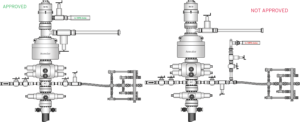
From employing trained and skilled operators to perform this task, modern technology has enabled anyone on location to control backpressure. This could be the operator’s representative or the driller, neither of whom may be adequately trained in the proper practice and technique. This can lead to a loss of well control best practices, such as considering an exceptional amount of gas as “normal” or purposefully being hydrostatically underbalanced while believing the surface backpressure is correctly compensating.
Any type of plugging, erosion, loss of containment, freezing or general loss of function to the well control chokes on a rig can end in disaster, especially if already hydrostatically underbalanced.
“Rule of thumb” MPD in the field or nonsensical plans, like holding the exact same amount of surface backpressure while circulating and during connections, are becoming more common. Drilling engineers who have never used MPD are beginning to employ it on rigs, whether motivated by a mandate from upper management or following a colleague’s lead, but they may be leaving hydraulics design to wellsite supervisors, who in turn may leave it to the mud management company.
Simply simulating equivalent circulating density in a hydraulics simulator does not encompass everything in proper MPD planning. With “on-the-go” MPD that isn’t properly vetted by a drilling engineer with MPD experience, planning and execution often fall short. This domino effect can frequently be traced back to the original motivation of cutting costs with available technology.
Besides the obvious safety concerns for people, improper MPD techniques also risk loss of the operator’s wellbore and the drilling contractor’s rig. These effects can even be seen throughout the industry in the form of market irregularities – essentially, fit-for-purpose systems and personnel are viewed as too expensive because this “cheaper” solution has been used elsewhere.
Proactively Defining MPD Flow Paths
Nabors’ internal Well Control Committee was formed in 2016 to address various issues, including the MPD issues discussed here. Members are drawn from multiple in-house disciplines, such as operations (all geomarkets), engineering, MPD, well control assets, BOP testing, operations excellence, drilling systems, training and QHSE. This group meets monthly, facilitated by Senior QHSE Manager Richard Grayson.
With regard to MPD, one issue brought before the committee was the return flow pathway. The committee became concerned that, in some cases, Nabors was being requested to connect equipment and conduct operations in ways that did not conform to industry best practices or adhere to guidance found in such documents as API 92M, Managed Pressure Drilling Operations with Surface Backpressure. These included requests to utilize the rig choke manifold and rig chokes as the primary pathway for MPD return flow.
The committee discussed and debated this practice, ultimately determining that the potential problem of plugging in the choke manifold due to cuttings could not be ruled out. If this occurs, the primary well control pathway needed for a well kill would not be available. This is not an acceptable result.
Nabors’ position is that the primary well control pathway – BOP wing valves, choke line, choke manifold, chokes – may not be compromised by MPD activities. This pathway must be tested and available for use in a well kill when needed. No exceptions can be made.
The committee spent 14 months researching, fact finding, discussing, creating, reviewing and approving an MPD Return Flow Pathways procedure document for inclusion into the Nabors Well Control Management Manual. From first discussion in December 2017, the final document was released to the organization in January 2019.
Other conclusions are that the RCD is not considered well control equipment. That is, during a well control event, the well is not considered secured underneath the RCD alone; it must be protected with the use of a BOP securing device.
MPD providers must provide their own surface backpressure sensors, instead of opening the rig’s HCR and relying on its casing pressure sensor, and they must share their information with the drilling crew in order to make informed decisions about the state of the well and operations.
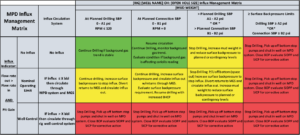
For MPD operations where MPD operators and equipment are present at the drilling site, an Influx Management Matrix is to be created and agreed upon by operator and contractor.
For third-party MPD operations where no MPD operators are present at the drilling site such that Nabors employees are at least partially responsible to operate the third-party MPD equipment, no Influx Management Matrix will be permitted such that any influx will be considered a kick and the rig BOP will be closed to secure the well.
These are not blanketed generalizations. The Nabors Well Control Committee surveyed its entire fleet of rigs, reviewed results of in-house well control equipment readiness inspections, and even had third-party companies audit certain operations. The issues were debated for months, and the resulting document was approved by top management. Nabors believes that these are reasonably prudent measures that do not significantly hinder the ability to drill and complete a wellbore using MPD techniques.
The information should not be taken out of context either. Criteria about the Influx Management Matrix does not mean gas cannot be circulated through an MPD manifold. Rather, the kick tolerance of the section and proper operating limits, whether downhole or surface limited, must be ascertained and defended prior to beginning operations. The goal is not to hinder operations but to reduce risk by engineering it out of the equation.
Figure 1 shows one of the earliest considerations of the committee. This involved a customer request to connect the MPD return flow pathway to the side outlet of a ram. This ram just happened to be the bottom ram of a class 3 BOP stack.
We note that bringing the MPD return flow pathway down from its traditional place above the annular preventer has advantages. First, many rigs have limited space under the rig floor. Connecting the MPD return flow pathway to the RCD, bell nipple below the RCD, or teeing off from the flow line can involve very tight spaces, creating a difficult work environment. Second, work above the annular probably involves use of man lifts or elevated walkways. Rigging up the equipment below the annular possibly permits conducting the work from ground level. In almost all cases, this makes for more space and a safer operation.
However, returning to the above example, the Nabors Well Control Committee saw issues with the requested configuration. Attaching the MPD return flow line to the side outlet of rams forces all the cuttings from the wellbore to turn at the ram cavity. Few statistics exist to quantify the effect this has on the ability of the ram to seal the wellbore when needed, but the committee was unanimous in believing it has a negative effect. That is, turning the flow at this location is abrasive to the metal and risks a build-up of cuttings that could inhibit the functions of the preventer. After much debate, the committee determined this arrangement is not best practice and not approved for MPD operations on Nabors rigs.
Considering Figure 1 again and noting that side outlets of rams are below the ram’s blocks when closed, we see that the MPD return flow pathway is also below the bottom rams. Best practice dictates to never conduct drilling operations below the bottom rams of the BOP stack. Once again, this was designated by the committee as not approved for MPD operations on Nabors rigs.
The Nabors MPD Return Flow Pathways procedure contains 12 scenarios. Each is applied to both class 3 and class 4 BOP stack configurations. The results are displayed graphically at the end of the document along with “Approved” or “Not Approved” designations. Figures 2 and 3 are examples of these graphical representations.
Influx Management Matrix
An example of an Influx Management Matrix can be seen in Figure 4. It defines the process boundaries that dictate when MPD operations should be handed off to the conventional well control system and procedures. There are circulating and static pressure limits along the top and influx volume limits on the left. These limits are calculated based on the kick tolerance of each section and agreed upon beforehand between the drilling contractor and operator. Then, field personnel are trained on its use.
The intent is not only to improve response time for reacting to influxes by defining what actions to take with exactly what operating circumstances, but it is also designed to reduce the frequency of improper operations where well control should be resorted to sooner rather than later.
Nabors believes that MPD is a valuable tool that can be leveraged to great advantage when drilling a wide variety of wells. However, Nabors also believes that there is no reason to deviate from sound, proven best practices. Other drilling contractors, as well as operators, are encouraged to adopt a similar stance. DC