By Gary D Humphrey, Ko-min Tjok and Luo Yang, Fugro GeoConsulting; Paul J Fourchy, Murphy Exploration & Production Company
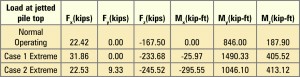
Hundreds of jetted conductors have been installed at offshore locations throughout the world in the past few decades. Traditionally, these jetted conductors are installed for deepwater exploration wells at the onset of drilling, but they have also acted as seabed-support structures, which must sustain loading of various natures.
In recent years, several jetted conductors have been installed and used as foundation piles for subsea structures. In general, wherever appropriate, the installation of jetted piles provides major construction cost and time savings.
The Thunderhawk Field is located in Mississippi Canyon Block 734 in the Gulf of Mexico. The water depth varies from about 1,740 m (5,710 ft) to about 1,894 m (6,215 ft). The subsea system consists of a manifold supported by a 914-mm (36-in.) diameter jetted pipe pile. The manifold will serve four subsea completion wells.
A jetted pile was the preferred option for manifold support because:
• Use of the existing pile/manifold connector design from a previous project could potentially save time and costs.
• The installation of the pile could take place at least 12 months prior to the load application; therefore, the pile continued to gain axial capacity with time.
• The use of a mobile offshore drilling unit (MODU) for installation instead of a dedicated construction vessel provided significant cost and construction savings.
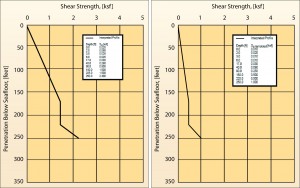
DESIGN CRITERIA, LOADING
The axial capacity of jetted piles is derived in a similar manner as that for driven piles, utilizing empirical procedures in the API (2008) Code or similar methods. Specifically, the skin friction, representing the dominant load-bearing component, is computed using an empirical factor in conjunction with a measurable or quantifiable initial soil parameter.
Table 1 shows the normal operating and two extreme loading conditions on the jetted pile top. The jetted pile is subjected to forces in the axial (Fz) and lateral (Fx and Fy) directions, bending moments (Mx and My) in two directions, and a torsional moment (Mz).
SOIL CONDITIONS
The soil conditions at the manifold location, as revealed by a single borehole, are relatively uniform and dominated by homogeneous, very soft to very stiff, highly plastic clay. The soils exhibited essentially a linear composition, increasing shear strength with depth. The specific soil parameters obtained from the borehole – the designed undisturbed and remolded shear strength profiles, the strain corresponding to 50% of the failure deviator stress (ε50) data and submerged unit weight profile – are used in to evaluate the axial and lateral capacities of the installed manifold pile.
Based on the laboratory strength and index testing results, conservative undisturbed and remolded shear strength profiles for the axial and lateral capacity calculation at the Manifold location were selected (Figures 1 and 2).
JETTED PILE INSTALLATION

Installation of structural casing in deepwater has historically presented problems for operators. Deeper water depths usually precluded the use of pile hammers to install conductors for exploration wells at the onset of drilling. The use of jetting has become the most common method employed to install surface conductors in deepwater.
Jetting is accomplished with a positive displacement motor where operators can simultaneously drill and set conductor pipe or piles from a floating vessel. The drilling assembly is suspended within a pre-assembled conductor pipe or pile. A typical assembly consists of a conventional drill bit, positive displacement motor with slip-on stabilizer, drill collars, running tool, bumper subs and drill pipe. A jetting sub is generally used. The drilling fluid is usually seawater, and returns are carried up through the casing.
The mud motor operates on a reverse application of the progressive cavity pump principle and supplies rotational power directly to the bit without drillstring rotation. Reciprocation (raising and lowering the conductor/pile during jetting) is usually also used to “force” the conductor/pile to a predetermined depth and when encountering more competent materials.
AXIAL PILE CAPACITY

The immediate axial capacity of a jetted pile is equivalent to the load required to penetrate the pile during, or immediately following, installation. The penetration of a jetted pile, and hence its immediate axial capacity, is therefore limited by the maximum available weight on bit (WOB) during installation.
Jetting reduces the soil resistance to penetration by removing the soil beneath the pile tip. As the soil is removed, some of the soil adjacent to the pile is squeezed into the cavity, reducing the lateral soil pressures. Reciprocation of the pile (raising and lowering the pile during jetting) further reduces soil resistance by removing additional soil from the walls of the jetted hole, by remolding and reworking the soil within the vertical travel distance of the pile and by increasing the water content of the soil immediately surrounding the pile.
Prior to reciprocation, the reduction in soil resistance during jetting is a function of the soil shear strength. After the start of reciprocation, the reduction in soil resistance is entirely controlled by the jetting procedure and equipment employed. Pile installation records suggest that after reciprocation, the soil resistance is reduced to that of weak slurry, with a shear strength unrelated to its initial strength and water content.
A number of Gulf of Mexico deepwater jetted pile and conductor installation records were analyzed, and relationships were developed for estimating the immediate axial capacity of jetted piles and conductors in cohesive soils based on the jetting procedure used.
These relationships were calibrated against the installation records for the Thunderhawk prospect (Figure 4) and developed for estimating the immediate axial capacity. The Thunderhawk manifold pile drawing is shown in Figure 3. It can be seen in Figure 4 that the estimated immediate axial capacity matches well with measured weight on bit during installation (i.e., the actual axial capacity during installation).

The immediate axial capacity represents the capacity of a jetted pile during or immediately following installation, and this capacity will increase with time after installation, as the soil squeezes back around the pile and regains strength through consolidation and thixotropy.
Since the lateral soil pressures around a pile are reduced by jetting and the removal of the soil (and are below the natural ambient lateral pressures), a driving mechanism for consolidation similar to that created by pile driving does not exist. Increases in the capacity of jetted piles after installation have been observed over short periods. Load tests have been performed on a 762-mm (30-in.) diameter conductor up to three days after installation.
CONCLUSION
As a construction time and cost-saving solution, the jetted pile foundation has been used to support subsea manifolds in the deepwater Gulf of Mexico. The prediction model was developed to estimate the immediate axial capacity of jetted piles and the capacity gain with time after the installation based on deepwater Gulf of Mexico jetted pile and conductor installation records. The estimated immediate axial capacity showed agreement with the measured WOB during installation. Beam-column analyses were used to evaluate the axial and lateral displacements of jetted pile under the design load and verify the applicability of jetted pile as an alternative foundation type for support of a subsea manifold.
i need information on the casing jettin in deepwater