Perspectives: Dan Mueller, ConocoPhillips
Well cementing: a small player with big impact
By Linda Hsieh, assistant managing editor
Cementing may be a small portion of the overall well construction cost, but its impact on the success or failure of a well is anything but, said Dan Mueller, cementing specialist for ConocoPhillips.
Especially in deepwater, where time equals big money, having to perform a squeeze operation to repair a poor cement job can easily push a project into serious and costly trouble. “You hear these numbers thrown around and they almost seem unreal, but if you don’t get a competent cement sheath around the shoe of a surface casing in deepwater, it will cost at least $1 million,” he said, “and that’s a conservative number.”
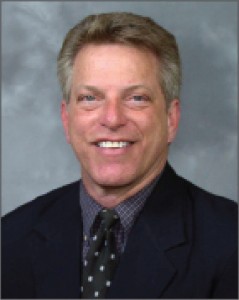
The high stakes at play – plus the increasingly hostile conditions under which wells are drilled today – means that preplanning on a well-by-well basis is crucial. Thermal modeling, wellbore stress modeling, hydraulics modeling, computational dynamics modeling – everything that can be done has to be done to make sure nothing gets overlooked. In today’s complex wells, Mr Mueller explained, anything that’s an “unknown” has the potential to damage the cement’s effectiveness.
All of which means that cementers have their work cut out for them. In fact, Mr Mueller likens the role of cementers in well construction to that of cornerbacks in football: “When we fall down and someone passes for a touchdown, everyone sees it. … When there’s a failure (in cementing), it’s typically quite noticeable and costly, even catastrophic. … You have to always ask yourself, ‘What haven’t I thought about? What can go wrong? If it does go wrong, how can we fix it?’ ”
STARTING FROM BOTTOM
Graduating from the University of Oklahoma in 1979 with a degree in geology, Mr Mueller started his career in Houma, La., with The Western Company of North America, which provided services such as cementing and fracturing. It was a base-level, physically demanding job that, as tough as it was, gave trainees valuable field experience with cementing equipment and allowed them to gain familiarity with the overall cementing process, he recalled. By 1989, Mr Mueller had worked his way up to a research associate in the company’s R&D facility just outside of Houston.
In 1991, he joined BJ Services as a senior research engineer working on cement research and development. It was during his 17-year tenure with BJ that his focus landed on designing deepwater cements – dealing with higher numbers of casing strings, lower ECD tolerances, temperature differences between cold seawater and hot producing wells, etc. He also looked hard at mechanical integrity, a significant concern in a deepwater well.
In 2008, Mr Mueller joined ConocoPhillips as a cementing specialist, where he now provides well cementing support for the company’s global drilling projects. His day-to-day responsibilities have not changed significantly from his position at BJ, he noted, yet, working from an operator’s perspective does have its advantages. “We get to see early on the well plans – what they’re intending to do, trying to achieve, how the well will be drilled. … It gives you the opportunity early in the process to offer input and suggestions.”
SOME THINGS CHANGE, SOME DON’T
Looking at the technological evolution of cementing since he entered the industry 31 years ago, Mr Mueller noted that there have definitely been major improvements in automated mixing systems and in the cements themselves. Operators now have a wide variety of cements available to them – resilient cements, self-healing cements, high-performance lightweight cements, foam cements, CO2-resistant cements – something for every application, it seems.
Yet, the basic overall process of cementing has not changed. It’s still mixing and proportioning cement and water at surface, then placing it into the wellbore with a triplex pump and displacing it to its proper point, he said.
Moreover, the overall objectives of cementing have not changed. “It’s the goal of any cementing operation to establish and maintain zonal isolation for the life of the well … we always have to keep that in mind,” Mr Mueller said. “We basically have one opportunity to cement the well properly, and we have to do all that we can to ensure the cement is properly placed and intervals being cased off are properly isolated. That’s as true as it was 50 years ago.”
Fortunately, some things do change with time – like mind sets about safety. Mr Mueller emphasized that he has witnessed major and welcome improvements on this front. “Every morning meeting I sit in, irrespective of where I am globally, always starts with HSE… I can look at a piece of equipment and compare it very closely to what it was in 1979, but the safety culture has changed profoundly. I can’t wait to see what happens 20 years from now when it’s been a part of that psyche for a generation of oilfield workers.”