3 classes for PDC bits of the future: fit for purpose, special application, part of automated drilling system
History indicates industry is likely to exit current market downturn with significant innovations to PDC cutters, bit technology
By Dan Scott, Baker Hughes
Editor’s Note: This article is the second in a two-part series on PDC technology. The first part, published in the July/August 2015 edition of DC, summarized where we have been and how we got here in PDC cutters and bits.
Historically, periods of significant downturn and economic strain on the industry have yielded innovative improvements in polycrystalline diamond compact (PDC) cutter or bit technology. These events and the resulting technological developments were reported in the July/August 2015 issue of Drilling Contractor and in an IADC eBook.
This year finds the industry in another major down cycle and disruption to the industry for drilling contractors, service companies and operators, with resulting impact on the PDC cutter and bit manufacturers. Predicting the future is just second guessing, but having been asked to build upon the prior article from last year, we have stepped back, searched the intellectual property and publications in the industry, and looked at what the future may hold for bit and PDC technology.
The hybrid bit, which combines rolling cones with the PDC bit, has demonstrated steady and significant growth since being introduced. It will continue to be improved upon and will grow in importance, replacing both traditional roller cone bits and PDC bits in many applications. The launch of a steerable version has opened another avenue to extend the range of suitable applications. The bit’s smooth and stable behavior improves reliability of downhole electronics.
Special-application bits
Based on industry literature and patent activity within the cutter and bit companies, I estimate that there will be three basic classes of PDC bits in the coming years. The first will be a robust, stable and steerable bit with the latest high-performance PDC cutters that will typically complete the shoe-to-shoe interval in its targeted applications. The cutters will be thermally stable and more resistant to impact behavior and damage.
They may be designed with abrasion-resistant diamond mixes for the most abrasive applications. They may contain special features for chip management, such as a polish or a contoured face, and/or non-planar shapes.
Industry literature points to continued development of non-traditional-looking cutters in the future. The latest improvements in the diamond synthesis technology of higher pressures and higher diamond densities will be a common factor in cutters from any of the major PDC cutter companies. Most of the bit designs will have some proprietary version of depth of cut control to help in secondary stability, and many are designed for specific applications and/or customers. The bit manufacturers offer various types of technical support to the contractors and operators for the selection and operating parameters and follow-up performance analysis.
Price-sensitive markets
A second class of PDC bits taking on its own persona is the more generic, less demanding applications that are extremely price sensitive. For these, existing technology is adequate to meet the operator’s basic needs. This area is generally known as “fit-for-purpose” in our industry.
In these applications, PDC cutters may come from any number of sources. These could be either major suppliers or one of the rapidly developing new suppliers. These cutters will generally have some level of thermal stability and are targeted to be general-purpose cutters, with a balance of wear resistance and durability. Cost will be a significant factor once a minimum threshold of performance is exceeded.
It is most likely that these cutters will outwardly look like traditional PDC cutters. The bit designs generally will not be custom-built for a specific application and will have limited special features to help minimize the cost of the product. These will often be solicited through the tender market on bids and by nature will come with minimal technical support. Both of the above future bit families – those for high-performance special applications and generic types for price-sensitive markets – are building from the technology in place today and are extensions of existing products or philosophies that will mature.
Automated drilling systems
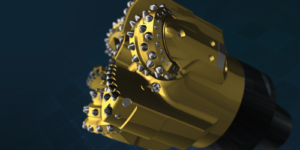
The third class of bit market segmentation expected to develop into a significant factor in terms of value, if not units, is an instrumented, high-technology bit that is an integral part of an automated drilling system. At least two service companies currently offer bits that are instrumented or contain devices to measure and monitor parameters at or near the bit. It is not unrealistic to make the leap from recording parameters and conditions to feeding them in real time to other downhole systems or to the rig floor/remote control center for processing.
The IADC Advanced Rig Technology Committee and the SPE Drilling Systems Automation Technical Section Committee are both growing in size, indicating a mounting interest and, as a result, growing patents around the bit as an integral part of the system.
From the literature review, it appears that several operators, service companies and cutter suppliers are staking out a position in patents. The literature suggests that bit conditions, such as load on a cutter, temperature of a cutter, dynamic instability, actual rate of penetration, rate per minute and weight on bit, are among those that may be measured and acted upon.

Obtaining formation evaluation data at the bit from gamma, resistivity, pore pressure, sonic and other parameters would prove very valuable to an automated steerable system, and, as such, are another area of speculation and patent activity. From the amount of activity in the patent arena, we believe that an instrumented bit is in the future and over time will be an integral part of the automated drilling system.
Another component of a high-end bit is the ability to adapt to the environment. Bits with self-adjustable depth-of-cut features have been reported in industry literature, with substantial laboratory testing to refine this feature and initial field testing reported. The patent art has many examples of a bit with adaptive control features. We can envision a bit in the future with sensors and the ability to adapt to the conditions being sensed.
As an example, at Baker Hughes we are close to launching a self-adjusting drill bit that offers an automatic pressure-related response to changing conditions experienced in real time downhole. The combination of integrated self-adjusting depth-of-cut control elements with the latest synthetic diamond cutter technologies allows the bit to adapt to changes in the formation without any interaction from the surface. It will help to smooth out the drilling process and reduce harmful vibrations that could damage the bottom hole assembly.
New, automated techniques for choosing the best features to optimize bit performance and eliminate the trial-and-error design process of the past have been introduced. Software has been developed, built upon the collective experience of numerous experts and thousands of laboratory and field tests. Preliminary software testing and field trials have shown it to be very effective at identifying features, which, when packaged appropriately, perform better than in the prior offsets.
With more exposure and successful outcomes, it is expected that this type of automated process will play a significant role in future bit designs. Along with selecting the hardware in bits, automation can be instrumental in choosing the right class of bit for particular applications and the best features for maximizing the performance of the bit and reducing the cost of drilling.
Depending on the application requirement, the bit of the future will be a fit-for-purpose economical product, a special application bit with features chosen to maximize the performance in an application, or a high-tech, instrumented bit that is an integral part of an automated drilling system. Many of the features for the high-tech instrumented bit can be adapted to the hybrid, furthering its application growth and performance gap over other bit types.
Based on past history, the industry will come out of this downturn with an improved PDC product and other drilling technologies that will increase future well efficiency and productivity. DC
Click here to read Part 1 of this 2-part series.
Click here to purchase the Drilling Contractor Drill Bits eBook.