Drilling & Completion Tech Digest
Rice University’s next-gen microchip plots cracks, pores through frac fluids
Rice University’s Integrated Systems and Circuits (RISC) laboratory has developed a new generation of microchips, approximately the size of a grain of sand, that travels downhole through fracturing fluids to plot the cracks and pores through which oil and gas move to the surface. Activated by electromagnetic signals sent from an aboveground transceiver, the microchips return real-time data to create high-resolution maps of reservoirs and formations formed by hydraulic fracturing.
The ongoing miniaturization of microchips, combined with their declining design costs and improved performance, aim to make an impact on the oil and gas industry. Data obtained from the chips can be used to decrease oil extraction costs in an era where low oil prices demand greater technology efficiency and innovation.
For example, the RISC laboratory developed a prototype spectrometer – a device used to analyze chemicals – that for the first time uses microchips to locate and measure asphaltenes, deposits that clog production pipe.
The lab greatly reduced costs from a $500,000 cabinet-sized machine traditionally used for the process to a $100 microchip that can be sent downhole to do the same.
RISC’s microchip research is being funded through sponsored research grants, most recently a $1.9 million award to the laboratory by a major oil producer.
“What this technology now allows producers to do is create intelligent oil and gas fields without a large capital expenditure, which is crucial when oil prices are hovering at $30 a barrel,” explained Aydin Babakhani, Assistant Professor of Electrical and Computer Engineering and leader of the RISC laboratory.
Curve bit run sets records in Laramie County, Wyoming
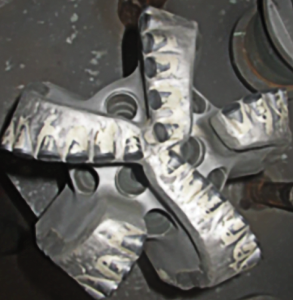
A recent Varel curve bit run in Laramie County, Wyo., set records for fastest curve in the field, fastest curve for the contractor and fastest curve for the operator, according to Varel.
The 8 ¾-in. VS513HG was run in the hole at 8,064 ft in the vertical section to complete the vertical section to TD before reaching the kickoff point for the curve.
The curve was drilled and landed in the horizontal section in only 2.7 hr. The directional driller said the bit toolface control allowed them to rotate through most of the curve.
The entire section, including the vertical interval, was 596 ft with an on-bottom time of 3.3 hr.
Average ROP for the section was 181 ft/hr, and the bit was dull graded: 0-0-NO-A-X-IN-NO-BHA for another run.
ExxonMobil, Hunting to develop autonomous tools for well construction
ExxonMobil Upstream Research has signed a joint development agreement with Hunting Energy Service’s Titan Division to develop new autonomous tools technology focused on creating a step-change in well construction and intervention efficiency. The companies said they expect to produce the first commercial autonomous tools in a few years, with initial tools focused on perforating and pipe-cutting devices.
The agreement brings together the Titan Division’s equipment manufacturing capabilities and expertise in tool development, energetics and safety systems and ExxonMobil’s autonomous tools technology and expertise in an onboard navigation system. Autonomous tools eliminate the need for communication or physical connection of tools back to the surface using a proprietary onboard navigation system. Once the devices reach the target depth, the tools then perform designated actions. The unique design dramatically reduces the time required to perform multiple operations during drilling, completion, workover and abandonment activities.
CONSOL deploys ceramic proppant in Utica gas well
CARBO Ceramics has announced the successful use of an ultra-conductive, low-density ceramic proppant technology in the Utica for CONSOL Energy. This was the first well to utilize the KRYPTOSPHERE LD proppant. It was deployed at a depth of approximately 13,500 ft. The proppant eliminated the need for gel and crosslinked fluids, leading to a reduction in overall completion costs. Initial production from the first well flowed more than 61.9 million cu ft/day of natural gas in a 24-hr period, making it one of the highest producing wells in the Utica to date.
Program to clean produced water starts in Middle East
Sorbwater Technology, a Norway-based company that has developed a patented technology capable of cleaning oil and other substances from water, recently announced that it has completed its first deliveries and is now engaged in a pilot project in the Middle East to clean produced water without any discharge and recover fresh water for reuse.
The pilot commenced in January 2016. If successful, the Sorbwater system will be deployed in several plants, with each installation treating between 200,000- 300,000 bbl/day of produced water, thus saving valuable groundwater resources and reducing costs of disposal of wastewater. The trial is in the range of 400 bbl/day.
Acoustic telemetry network acts independently of formation, fluid, flow
By Kelli Ainsworth, Editorial Coordinator
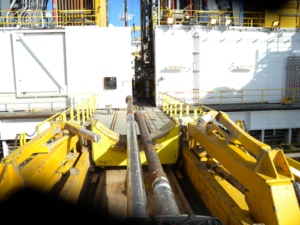
Obtaining any downhole data, in real time and particularly during completion installation operations, can be a challenge for deepwater operators using conventional methods such as mud pulse telemetry. XACT Downhole Telemetry has developed an acoustic telemetry network that can be incorporated into standard drill strings to provide real-time telemetry and distributed measurements along the length of the wellbore any time the drill pipe is downhole.
“Being able to send acoustic signals through drill pipe, which is in the hole for almost 90% of all operations, means that you now have the potential to access data 90% of the time,” said Andy Hawthorn, Director of Applications at XACT.
The system consists of nodes that resemble drill collars and pick up and handle like drill pipe. They are incorporated into the drill string every 4,000 to 5,000 ft. These nodes act as repeaters for the acoustic telemetry but also individually measure internal and external temperature and pressure, weight, torque and bending moment. A high-voltage charge is sent across a piezoelectric stack, which generates an acoustic signal that is carried up the drill string to the surface.
Once the signal reaches the surface, it is captured by the XACT Electronic Acoustic Receiver, which is attached to the top drive or frac head. The receiver then wirelessly sends the data to an onsite computer, from which the data is integrated with other surface data and shared with real-time operations centers or other offices.
Because the acoustic signal travels up the wall of the drill pipe, the network is independent of formation, fluid and flow. While electromagnetic telemetry systems can experience transmission problems in some formations, the XACT network has been designed to transmit effectively in all formation types, according to the company.
Measurement systems that are dependent on fluid flow to gather or transmit data cannot provide data when tripping or when the pumps are off. Mr Hawthorn said industry data indicates that 75% of kicks occur off bottom or while tripping. The XACT telemetry network’s ability to work in low- or no-flow situations also means it is effective in managed pressure, underbalanced and total loss situations.
Because each node takes separate measurements in addition to boosting the signal, the network provides distributed measurements that allow the users to observe what is happening downhole through every section of the well, rather than relying on only bottomhole and surface measurements, or analyzing data after the fact.
“Our system is about providing more intelligence about downhole conditions in real time than exists today,” said Jason Roe, XACT President and CEO. “It enables decisions that operators don’t currently have the ability to make in real time. Right now, it’s just analyzed after the fact and applied to the next well. This system allows you to analyze downhole conditions and apply solutions immediately to efficiently and reliably drill and complete your well in a cost-effective manner.”
The network is also fully through-bore so operators can cement, frac, drop balls and pass wiper darts with the system in the wellbore.
BP and Shell sponsored the development of the acoustic telemetry network. Working closely with these major operators not only allowed XACT access to multiple wells for testing and proving the system, but it also helped the company know exactly what problems operators are facing and to develop a solution that addresses those problems. “The last thing you want to be is a solution looking for a problem, and as well complexity continues to increase, so does the need for better understanding of downhole conditions in real time,” Mr Roe said.
XACT’s acoustic telemetry network has been used in multiple deepwater wells for real-time applications, including cementing, liner running and during a frac pack installation, in the deepwater Gulf of Mexico. These applications have largely targeted areas where downhole data was previously not available in real time.
Looking to the near-term future, the company is working to make the network fully bidirectional by building on the current network capabilities.
“The beauty of this telemetry system is that when you induce signals in the pipe, they naturally travel both directions,” Mr Hawthorn said. “What we’re working on as a part of the network evolution is bi-directionality so we can talk down to tools, as well as receive data.” This would allow operators to send signals through the telemetry network to change the settings or configurations of tools or other mechanical devices when needed.