Innovations drive packers to new stages
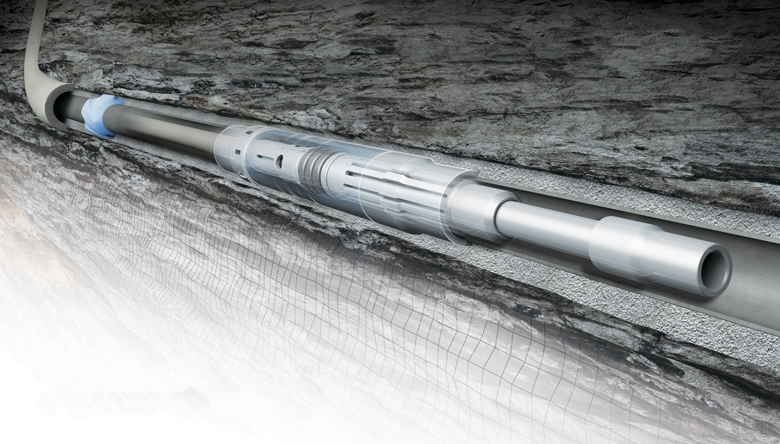
Shift to open-hole completions, rising stage counts push packer strengths, capabilities
By Katie Mazerov, Contributing Editor

How do you push 60 packers into a well? Just a few years ago, that capability was unfathomable. Today, thanks to innovation that is keeping up with the demands of unconventional wells, including tight oil and gas and shales, deepwater and ultra-deepwater developments and increasingly harsh environments, packer technology is evolving with industry trends and expanding the R&D envelope for the challenges that lie ahead.
Deeper wells, longer laterals and rising stage counts in the unconventional sector and the continued push to ensure cement integrity are driving development of packer designs and associated downhole services and products such as valves, ports and sleeves.
“Industry has made great strides in recent years,” said Dan Themig, CEO of Packers Plus Energy Services, an early innovator of open-hole, multistage completion systems, which are increasingly being used in the North American unconventional sector. “There was a time when nobody thought we could push five packers into a well. Today, as rising stage counts have necessitated that more packers be placed in the well, five stages is never enough. Almost all plays are looking at 20-plus stages.”
Packers have played an important role in the oilfield for more than 75 years, starting with mechanical designs that are still used universally to seal the annular space between two strings of casing or between the casing and the wellbore. Along the way, inflatable and swellable packer technologies emerged to address more challenging applications and niche markets, providing quick, customized solutions for a wide variety of downhole applications. With nearly 50 years of experience working with inflatable and swellable packer technology, TAM International has been a leader in advancing packer technology to help operators minimize risks, lower costs and boost production, according to Ray Frisby, VP Technology.
TAM began building inflatable packers in 1968 and continues to advance the capabilities of commonly used inflatable packers, which are increasingly vital to ensuring cement integrity. “Operators continue to drill deeper and in more difficult environments where cementing operations can be very challenging, so we continue to look for technology advances to help ensure long-term well integrity,” Mr Frisby said.

Permanently installed, casing annular packers are run as part of the casing string to isolate formations that may flow or take fluid during the cement job and cause well integrity problems later in the life of the well. Inflated with wellbore fluids, inflatable packers can be set in either cased or open holes to ensure a high-quality cement job. Last year, TAM developed and qualified a 22-in. inflatable casing annulus packer and cementing valve for a major operator to address shallow gas flows in a high-profile deepwater field, Mr Frisby said.
Inflatable packers also are routinely used to perform testing, isolation or remedial operations, he added. For drilling applications, inflatable service packers are often set in open holes to perform a plug-back for sidetracking operations. Similarly, production applications with inflatable packers can prevent water encroachment into the payzone.
“We have developed multiple options for inflating and deploying packers, including the capability to run packers on slickline,” Mr Frisby continued. “While deployment on pipe is most common, we also have designed a reliable method to deploy and set inflatable packers without a work string, coiled tubing (CT) or even electric line.” The system is routinely used with TAM’s line of high-expansion inflatable packers, which can run through production tubing and expand up to three times the original run-in outer diameter of the packer, giving operators an alternative to conventional workover rig operations.”

An inflatable dual-packer straddle system isolates intervals in the wellbore for acid treatments, testing, fracturing, re-establishing connectivity in existing frac stages and analyzing the economics of re-fracturing wells in both open- and cased-hole environments. “We routinely set our inflatable straddle system dozens of times and have set it more than 100 times in a single trip,” Mr Frisby noted. “This multi-set functionality allows operators to treat small intervals to improve well performance or identify candidate wells for recompletion or re-fracturing.”
A Permanent Solution
In 2005, TAM was among the first to introduce swellable packers, commonly used for unconventional, multistage hydraulic fracturing. Swellable packers provide a low-cost solution for ensuring long-term cement integrity to mitigate potential contamination of aquifers, which typically results from well construction problems, not hydraulic fracturing operations, he explained. The packers provide secondary prevention by reacting to migrating well fluids later in the life of the well if problems occur with the primary cement in the wellbore.

Typically deployed on the casing string, swellable packers expand over a period of days, as specially engineered elastomer compounds absorb the fluid in the wellbore. “Swellable packers are highly sensitive to the well environment, and extensive testing is required to accurately predict the packer’s performance in a given wellbore environment and well geometry,” Mr Frisby said. “Our water-swell and oil-swell elastomers are designed to handle everything from challenging low-temperature, high-salinity environments to extreme geothermal applications.”
TAM’s nine compounds for extreme conditions, both hot and cold, include a compound rated up to 575°F and the FastSwell elastomer, suited for low-temperature environments prone to slow swell times. These include Russia, West Texas and deepwater environments near the mud line. “If we know the well conditions, we can provide very accurate predictions of how a swellable packer will perform in that specific environment,” Mr Frisby added. “Many applications are standard, but when we need accurate prediction in an uncertain environment, the vast amount of testing we have performed on our elastomers enables us to provide the right packer for the application.”

As the industry moves into more open-hole style well development, especially in the offshore sector where sand control is a frequent issue, packers that can provide zonal compartmentalization with reliable sealing have become essential in reducing cost and improving reliability. “A conventional packer that works fine in a cased hole that is round and even won’t work well in an open hole that is rough, uneven and over-gauged,” explained Randy Simonds, Director of Sand Control for Weatherford. “Swell packers were designed to address that limitation, but they take several days to swell. In today’s cost-conscious environment, operators want an immediate answer to their zonal isolation problems.”
Weatherford has developed a mechanical packer that is designed with a self-energizing cup-seal isolation technology to provide a strong seal that effectively molds immediately to the changing and irregular geometry of the horizontal, open-hole wellbore where shales and other problem zones need to be isolated. The cup can expand at different diameters and provides a fixed and limited amount of force into the formation so as not to put too much pressure on the rock and damage the borehole.
Open-Hole Isolation
Designed with independent setting mechanisms around the circumference of the elastomer seal, the packer features a wide range of expansion capabilities in boreholes with large internal diameters up to 9 ¼ in. The packer can be set without intervention using radio frequency identification devices pumped downhole, pressure pulses or a timer, or set hydraulically in a variety of environments, achieving up to 1.2 ovality. In addition to zonal isolation, the system includes a packer design that enables deployment of multizone gravel packs and frac packs in a single run.
Two outward-facing cup-seal assemblies provide bi-directional pressure. A rock anchor, or slip, may be deployed between the cup-seal units to hold the packer in place by anchoring into the rock. Underneath the cup, a series of independent supports are activated by a mechanical lock. The levers expand and create the seal at different diameters in the irregular open hole. When the cup comes in contact with the wellbore, a clutch mechanism slips to hold the cup in place while limiting the stress placed on the formation.
Once the levers have fully deployed, the packer is uniformly set across the circumference of the wellbore. The cup seals are tension-set, allowing them to maintain form as the steel components expand or contract due to thermal fluctuations. The rock anchor absorbs the load so the packer does not move, which ensures the rubber is not destroyed by scraping back and forth on the rock. The cup-seal isolation packer has been run in more than 50 wells globally, including offshore West Africa and Asia Pacific, deepwater Gulf of Mexico and in open-hole land wells in the Middle East.
With the challenge today of drilling deeper and longer wells in the unconventional sector, and the shift in some plays from cemented plug-and-perf completions to open-hole completions, reliability in packer technology is paramount, Mr Themig of Packers Plus maintains. “A few years ago, frac stages were typically 150 to 300 ft apart. Today, the spacing between frac stages may go as low as 65 ft. As we go to these higher stage counts with more tools, including packers, being run in deeper plays, reliability is a huge issue. It must be 100%. In the Bakken, Niobrara, Permian Basin and the deep Duvernay play in Canada, 40 to 60 stages in a well is common and rising. The push now is for technology to move the industry to 60- to 100-stage jobs to adequately drain the reserves and complete the work in a few days.”
Tighter stage intervals and increasingly higher fracturing pressures needed for rock that is more difficult to break are driving an uptick in the company’s 15,000 psi-rated Titanium XV series dual-element mechanical packers used primarily in open-hole wells. “These packers are being used successfully in the Duvernay, which, with more recoverable oil than the Eagle Ford, is requiring at least 60 stages,” Mr Themig said. The short length of the dual 5-ft length packers with two short sections of rubber element provides reduced torque-and-drag during installation. An enhanced, hydraulic ball-activated flow port, run between the packers, can deliver 60 to 100 stages and allows specific zones of the wellbore to be fractured selectively.
Recently, the company launched a field trial for Quadrant, a system that uses a shifting tool run on CT, rather than balls, to open individual or multiple ports between packers and pump an unlimited number of frac stages at low or high pump rates. “The system enables us to pump a 60-stage well one stage at a time, or three simultaneously,” he explained.
Liner Hanger Packers
Packers Plus is also introducing a new liner hanger packer for the compression forces required in horizontal wells where equipment needs to be pushed into the well. Configured with an anti-preset mechanism, the new design will ensure the completion system is fully installed and provide the high-pressure sealing capability of a production packer, Mr Themig noted.
Liner hanger packers, installed permanently in the well as part of the liner hanger assembly commonly used in cased holes, are increasingly being used to achieve greater well integrity and for cost efficiency, according to Terry Howard, Director of Technical Support and Training for TIW, a provider of custom-engineered drilling and completions equipment for the oil and gas industry. “Back in the 1980s, liner-top packers were run on about 20% of liners installed in wells,” he said. “Today, they are used 80% to 90% of the time.”
In many cases, operators are running the packer as standard equipment with the liner to avoid having to install one later in case of a poor cement job. “In the past, operators chose not to run the packer with the liner. However, if the top of the liner did not test well after the cement was pumped, they had to suspend operations and go back in with the packer, which involves extra days and rig time and more trips in and out of the hole,” Mr Howard said. “It comes down to overall cost, and being preemptive saves money in the long run.”
Deeper wells and higher pressures and temperatures have been drivers for improving the strength and capabilities of liner hanger packers. “Thirty years ago, a liner-top packer that would hold 5,000 differential strength was considered top of the line,” he noted. “Today, we’re at 10,000 psi and looking to go to 15,000 psi.”
TIW’s liner hanger packers are used globally, but deepwater is a key market as customers see the importance of having the additional seal, he continued. “Customers also want liner-top packers to be more robust in terms of how much pressure they will hold at increasingly higher temperatures,” Mr Howard said. “The temperature ceiling is typically around 400°F, but we have seen environments as high as 450°F, and some operators are predicting 500°F.”
To overcome the limitations of elastomers in high temperatures, TIW has developed an expandable liner hanger packer, the XPak, which creates a metal-to-metal seal between the liner hanger and the casing where the packer is being set. Expansion is provided with a hydraulic tool that exerts a tremendous amount of force and stretches the steel tube until it contacts the outer casing. “The packer is similar to solid expandable technology in the setting method, but it provides a much more reliable seal, holds higher pressures and can operate in higher temperatures than conventional rubber compression-set packers,” he explained. “It is ideal for extreme environments.” An elastomer installed in the packer serves a secondary seal.
FastSwell is a trademarked term of TAM International. Titanium XV is a registered term and Quadrant is a trademarked term of Packers Plus.