Drilling optimization culture built on real-time data, communication
Cycle of continuous feedback, improvement drives strategy for better performance in Brazil’s Santos Basin
By Augusto Borella Hougaz, Danilo S. Gozzi, Isao Fujishima, Klaus L. Vello, Petrobras; Sandro Alves, Ian Thomson, Raul Krasuk, Frank Buzzerio, Baker Hughes
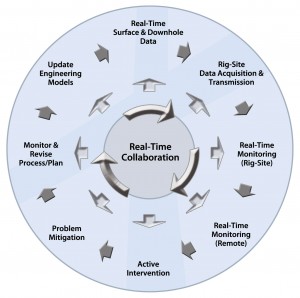
In recent years, deepwater drilling operations have become more challenging, with new exploratory frontiers and the rise of rig rates demanding first-class drilling optimization technology and services. In Brazil, deepwater well construction activities have increased significantly since the first major pre-salt discovery in the Santos Basin in 2006.
In this highly demanding and challenging drilling scenario, building a drilling optimization culture based on the synergy and integration between a major deepwater operator and a leading service company has proven to be fundamental for achieving better drilling results and superior performance.
The creation of a multidisciplinary drilling optimization group, integrated with the operator’s drilling team in 2008, and the introduction of a highly specialized downhole drilling dynamics measurement-while-drilling (MWD) tool changed the drilling optimization concept in Brazil. This concept pioneered the remote (off-the-rig) downhole drilling parameters surveillance in deepwater operations.
This article presents the fundamentals of this real-time remote and rig-site drilling optimization concept, with focus on the integration between the operator and the service company; the operational aspects with regards to appropriate communication protocols; and decision-making processes, highlighting the performance improvement achieved.
Background
Demand for first-class drilling optimization technology and services is growing fast. In Brazil, a novel real-time optimization drilling service was implemented in 2008 in the Santos Basin. Through its implementation and execution, it became clear the importance of knowing not only where (wellbore placement) and what (formation evaluation) you are drilling but also how you are drilling, which is mainly driven by the integration between operator and service company.
After three years, it was clearly observed that the higher the integration between service company and operator in a proactive and collaborative environment, the higher the drilling performance. Today in the deepwater Santos Basin pre-salt environment, the real-time optimization drilling service is part of the drilling program in almost every well, from the top-hole section (typically 26-in. hole) to the reservoir section.
The ability to gather and interpret reliable downhole MWD data in exploration or new development wells is crucial to help with the early detection and identification of unexpected drilling behavior, allowing better judgment of actions to be taken because it switches from perception- and experience-based decisions to ones supported by real-time data. This can save rig time and mitigate catastrophic failures.
Real-Time Drilling Optimization Team
In 2008, a culture of real-time optimization was started in Brazil’s Santos Basin with a multidisciplinary optimization team. The service companies’ real-time drilling optimization team was formed to provide quality real-time drilling services and support the operator’s decision-making process.
To accomplish this objective, the team was conceptually designed to incorporate members with diverse backgrounds, such as directional drilling, MWD engineers, mud logging, geosciences, geology, bit runners, etc.
The contact during service optimization and real-time monitoring is accomplished daily and directly between the teams, both in the office and on the rig site. This constant interaction between responsible personnel, including the manager of the well, design engineers and geologists (office and crew operator), coupled with the rig team, makes all difference in the outcome of the operation. The project is always aiming to continuously improve performance while monitoring and adjusting drilling parameters in real time when necessary. It also operates with the objective to capture lessons learned to feed future projects.
To accomplish effective remote and rig-site real-time drilling optimization, the use of a highly specialized downhole drilling dynamics MWD tool is key as it records and transmits dynamics real-time data (stick slip, whirl, etc) and downhole drilling parameters (WOB, torque, etc), which allow a better judgment of the downhole conditions while drilling. This in turn allows better support for adjusting and changing the surface drilling parameters to optimize operations in a continuous feedback cycle (Figure 1).
In general terms, the main objectives for the drilling optimization service are:
• Drill safe and fast;
• Twenty-four hour real-time monitoring service;
• Technically support operator decision-making process;
• Visualize downhole data in real time;
• Optimize overall performance while drilling;
• Minimize and control the vibration levels;
• Monitor the wellbore quality;
• Improve and accelerate learning curve; and
• Document best practices and achievements.
The service has to allow decision-making process improvements in two directions:
• Make decisions based on measurable facts and critically analyzed data instead of perception or experience, which is not always comparable; and
• Make decisions in the real-time, 24/7 drilling optimization service for an extended period allows the building of a local database of local best practices and operator/service company common understanding.
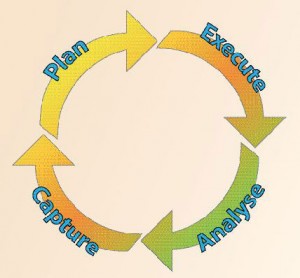
Improve/Accelerate Lessons Learned Process
Improving and accelerating the lessons learned process is always required, but it becomes mandatory when the activity level multiplies the rig count by an order of magnitude and operating costs are rising significantly. Capturing documented lessons learned and disseminating knowledge are critical components in this working environment.
Drilling process improvements include many different actions; some are related to new methods, technologies, drilling practices and new concepts. Performing something new or innovative presents challenges and risks, which need to be properly addressed by providing accurate downhole data in real time that allow appropriate risk evaluation and mitigation actions.
Engineered Optimization Process With Continuous Improvement Cycle
The engineered optimization process has been used for decades in various applications and is based on the continuous improvement cycle (Figure 2). In this application, the process involved teamwork and close cooperation between the operator and the drilling service companies. The key components are:
1. Plan – Establish objectives for the well, reasons for optimization and pre-well planning.
2. Execute the drilling phase by implementing the optimization plan.
3. Analyze post-well analysis, reviewing the actual performance.
4. Capture lessons learned.
Each step is broken down into subcomponents, building on one another to develop a thorough understanding of the application and drilling environment while ensuring nothing is overlooked (Figure 3). The emphasis of this cooperative program is on detailed engineering of every step, using the process to work smarter and more efficiently. The engineered optimization process relies heavily on knowledge management and on the application of drilling best practices and procedures, which require highly competent application engineering. The “capture” requirement of the “continuous improvement cycle” was used by the service company to ensure that past mistakes were avoided and good past performance was repeated.
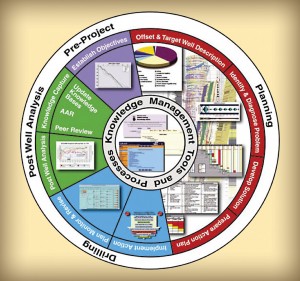
Case Study 1
Starting Remote Optimization Concept in Deepwater Operations
The first step was to analyze and understand the previous scenario, including drilling operations problems and challenges, as well as the technology and drilling parameters used, drilling practices and the interaction between all those factors. The most appropriate technology and drilling practices were then presented and discussed.
The drilling of development wells in the Santos Basin had opportunities for optimization and recurring problems that could be solved and/or minimized with changes in the bottomhole assembly (BHA) configuration, and especially with the control and management of downhole data. The real-time drilling optimization service was implemented in a development horizontal well in the Santos Basin in late 2008. At that time, the interaction was among the well manager, the drilling optimization engineer and the rig team.
After the excellent results of the first well, a sequence of development wells in different Santos Basin fields were drilled using the same service concept. For each new well drilled, the results showed improvements, not only in cost reduction but in communication between the teams.
Development Wells
Previous Scenario
Before the implementation of the optimization service, the main problems and observations reported were:
8 ½-in. section – Two trajectories (one directional and one horizontal), medium interbedded formation:
• Low penetration rate;
• High temperature (approximately 195ºC);
• Presence of risk to stick by differential pressure;
• Sticking events related to mechanical issues;
o Backreaming to minimize stuck events risk.
• Drilling parameters not optimized (approximately 100 rpm / 10-30 Klbf), using surface data;
• Recurrent directional and MWD or logging while drilling tool failures;
o Insufficient dogleg severity; and
o Reported high vibration levels and high temperatures as causes.
• Additional runs leading to greater drilling time and higher costs;
• Changes in the parameters, with significant focus on attempts to reduce vibration levels;
• Shock sub placement;
• Unsuccessful attempts to sidetrack the well with rotary steerable systems (RSS);
• Exceeded buckling load while drilling in slide mode with motor;
• Low drill bit depth-of-cut control (DOC) and toolface control problems;
• Use of motor with adjustable kick-off sub (AKO) without directional needs, compromising the borehole quality; and
• Bits used were heavy for the specific formation drilled.
Optimization Proposals
After thorough analyses, including peer reviews with the operator, a plan of action with appropriate proposals was elaborated. Covering new technologies and real-time drilling optimization service previously established, discussed between the operator and service company, the initial goal was focused on solving or minimizing recurring problems but always striving for continuous improvement by working directly with the well manager.
The main points of the proposals were:
• Optimize BHA design and configuration to drill the section in a single run;
• PDC bit designed for the application;
o Diamond volume management;
o Appropriate cutter selection to address formation abrasiveness;
o DOC for improved toolface control;
o Lateral movement mitigator to minimize vibration levels and lateral impacts; and
o Secondary stability features.
• Equivalent circulating density (ECD) and borehole cleaning real-time monitoring;
• Early detection of stuck-pipe tendency;
• Perform the sidetrack with drilling BHA, reducing a trip to do it;
• High-temperature procedures implementation to minimize the potential for BHA electronics components failure; and
• Use of highly specialized downhole drilling mechanics and dynamics diagnostics MWD tool with 24-hr real-time monitoring service to provide support for all drilling operations with fast response to take action.
Results
During the first drilling optimization service performed in the Santos Basin, it was observed that drilling performance improved whenever the integration between operator and service company worked. Results obtained at the end of the study were highly positive, going beyond the expected and planned project, being repeated in the following development wells. Relevant points of this achievement are:
• Drilling performance more than doubled with adjusted downhole drilling parameters in real time;
• Operation time and costs significantly reduced;
• Minimized vibrations levels (observed only low to moderate);
• Minimized sticking events, identifying nonproductive time and taking action with fast response;
• No failures caused for vibration or high temperature; and
• Teamwork guaranteed by integration between well manager, geologist, drilling optimization engineer and rig team.
Reservoir Data Acquisition
To expand the success achieved in the development wells, the real-time drilling optimization service was implemented in highly demanding reservoir data acquisition (RDA) and development deepwater wells in the Santos Basin.
In a new pre-salt scenario in carbonate reservoirs in the Santos Basin, an opportunity for improvement was observed on the new drilling optimization culture based on the synergy and integration between the operator and service company. The key to success was the direct integration between the operator’s design engineer team, which is responsible for RDA/development well projects, and the service company’s support teams.
A direct communication channel between design and drilling optimization engineers – which was already established in the first pre-salt well drilled with this concept – enabled the constant feed and support for the project execution. The result was a significant improvement for each drilled well, supported by an accelerated lessons learned process, updating procedures, and reducing time, risks and operations costs.
The following examples are divided by drilling sections – 26 in., 14 ¾ in. and 8 ½ in., not by chronological improvements.
Previous Scenario
Before implementation of the integrated real-time drilling optimization service, the main reported problems and/or observations for RDA/development wells were:
26-in. Section
Issues in the post-salt section were:
• Relatively low penetration rate;
• Drilling parameters that were not optimized;
• Lack of remote access to drilling surface data (flow rate, torque, rpm);
• No downhole drilling data/measurements;
• High tricone bit revolutions due to high motor and surface RPM;
• Reduced bit life – trip for bit hours/revolutions;
• Lack of smooth and steady WOB; and
• Formation-induced deviation tendency.
14 ¾-in. Section
Issues in the evaporitic section were:
• Bit changes/more runs;
• Salt formation mobility problems and doubts;
• Low penetration rate;
• WOB control instability;
• Doubts about salt drilling response for directional issues;
• Drilling parameters not accurately optimized;
• Lack of downhole drilling data/measurements;
• Common sense between drilling dynamics changes and undefined salt interfaces variations;
• Excessive time spent on connection operations;
• Stop criteria undefined (total section depth); and
• Identified optimization opportunities to reduce time and costs.
8 ½-in. Section
Issues in the pre-salt section were:
• Low penetration rates;
• Rock mechanic characteristics variations;
• Use of the same drilling system (impregnated bit and turbine); no different system used for comparison;
• Common sense between drilling dynamics changes and undefined pre-salt lithology variations;
• More runs to change the bit based on extremely low penetration rates;
• WOB control instability;
• Lack of accurately optimized drilling parameters; and
• Identified optimization opportunities to reduce time and costs.
Optimization Proposals
26-in. Section
• Use of motor low speed (LS) to minimize bit revolutions and optimize the tricone bit life and run;
• Use of automated motor-assisted vertical system for drilling in vertical mode and minimize any inclination increment tendencies;
• Use of highly specialized downhole drilling mechanics and dynamics diagnostics MWD tool with 24-hr real-time monitoring service to provide support for all drilling operation; and
• Direct communication channel between design engineers, well manager, geologist and drilling optimization engineers.
14 ¾-in. Section
• Use of RSS and PDC bit;
• DOC control to guarantee better dynamics conditions and drilling optimization possibilities;
• Better borehole quality;
• Drilling dynamics stability minimizing vibration effects;
• Use of highly specialized downhole drilling mechanics and dynamics diagnostics MWD tool with 24-hr real-time monitoring service to provide support for all drilling operations; and
• Direct communication channel between design engineers, well manager, geologist and drilling optimization engineers.
8 ½-in. Section
• Use of motor LS automated drilling system to minimize vibration levels and prioritize high WOB application;
• Use of PDC bit with motor, seeking better performance and data to improve PDC bit design for this new scenario;
• DOC control to guarantee better dynamics conditions and drilling optimization possibilities;
o Better borehole quality; and
o Drilling dynamics stability minimizing vibration effects.
• Use of modular stabilizers to improve BHA configuration;
• Prioritize high WOB and low drill string rotation;
• Use of highly specialized downhole drilling mechanics and dynamics diagnostics MWD tool with 24-hr real-time monitoring service to provide support for all drilling operations; and
• Direct communication channel between design engineers, well manager, geologist and drilling optimization engineers.
Results
26-in. Section
The last real-time drilling optimization service implemented in the Santos Basin was for this section, changing paradigms on drilling parameters and dynamics response. The significant results of the integrated real-time drilling optimization service on post-salt formation were:
• Reduced operation time and costs, minimizing risks by 24/7 monitoring service;
• Optimized drilling parameters;
• Paradigm changes, ROP improved by an average of 100% to 200%;
• Monitored drilling dynamics, gathering knowledge about post-salt lithology variations;
• Understanding of “how we are drilling” with downhole data, improving the lessons learned cycle related to procedures and projects;
• Downhole WOB always applied near to bit, specified limit to optimize ROP;
• Improve WOB application control with downhole WOB real-time data, optimizing ROP, reducing vibration levels and minimizing bit structure damage risks;
• Torque response monitored by downhole data, supporting any decision based on bit structure indications;
• Improve bit life with total rpm to TD reduction;
• Downhole data supporting the lithology change identifications, helping to identify the evaporitic section; and
• Use of motor LS with the steerable function (could be the better option to ensure vertical drilling as planned).
14 ¾-in. Section
The real-time drilling optimization service was implemented for the evaporitic section, mainly looking for optimization, fixing directional monitoring issues and providing support for stuck events related to salt mobility.
The significant results of the integrated real-time drilling optimization service on the evaporitic section were:
• Reduced operation time and costs, minimizing risks by 24/7 monitoring service;
• Drilling parameters optimized;
• ROP improved an average of 75% to 125%;
• Drilling dynamics monitored, gathering knowledge about the evaporitic section (lithology variations);
• Understanding of “how we are drilling” with downhole data, improving the lessons learned cycle related to procedures and projects;
• Downhole WOB always applied near to bit, specified limit to optimize ROP;
• Started the use of auto-drill technology to optimize downhole WOB application;
• Optimization of auto-drill application, minimizing damping effect and improving WOB control;
• Auto-drill applications were optimized, resulting in ROP improvement, vibration reduction and minimizing of bit structure damage risks;
• Lithology changes were monitored by downhole drilling parameters, as torque responses, helping to identify evaporitic section variations;
• Stuck events minimized by applying backreaming procedures and mud weight control improvements;
• Directional drilling performed with success, supported by directional monitoring service; and
• Clear criteria for section’s end was established based on downhole drilling parameters.
8 ½-in. Section
• ROP improved using impregnated bit;
• PDC bit runs supported improvements for bit design;
• Impregnated bit runs showed better results than PDC runs in the initial tests;
• Downhole data supported future plans and decisions seeking performance improvement;
• Drilling dynamics were monitored, knowledge was gathered about the pre-salt formation (lithology variations);
• Auto-drill application was optimized, resulting in ROP improvement, reduction in vibration levels and minimizing of bit structure damage risks; and
• Need for more improvements with high technology to get significant results.
Conclusions
The partnership established between operator and service company in the wells drilled in the Santos Basin became a strategy to improve and contribute to the successful results obtained in drilling operations since 2008. All decisions were made jointly. This created a specific communications pattern, and the mutual confidence grew with each new work accomplished. After the first service, a culture of continuous learning was started, allowing continuous improvement for future projects.
Since 2008, more than 200 hours of real-time drilling optimization operations have been conducted in Brazil, with more than 183,000 meters drilled in deepwater wells, mostly in the Santos Basin and in exploratory wells.
The keys for this success are:
• Create a strong teamwork culture between the operator and the service company to achieve an “integrated real-time drilling optimization service”;
• Keeping an open mind to new ideas, and discussions and always looking for a holistic view;
• Working closely with all personnel/areas involved on the operation to ensure continuous global performance improvement; and
• Use of a highly specialized downhole drilling dynamics MWD tool/drilling optimization service to ensure:
o Better drilling dynamics control;
o Real-time downhole parameters change responses, helping to guide actions both for drilling and geologist teams (drilling dynamics issues);
o Better borehole quality and conditions control (ECD, pressure);
o Better directional trajectory control and identification of any abnormal events using bending moment and bending toolface data (local high DLS, spiraling tendencies). This mainly supported the directional drillers on the rig site;
o WOB transfer and cutting bit structure monitoring;
o Vibration downhole diagnostics (near the bit) ensured more precision for downhole parameter adjustments to minimize vibration levels;
o Drilling horizontally as smoothly and efficiently as you would vertically; and
o Creating the longest wells economically and efficiently, knowing exactly where and how you are drilling.
This article is based on IADC/SPE 151186, “Upgrading the Real-Time Drilling Optimization Culture in Brazil’s Challenging Deepwater Operations: The Utilization of a Remote and Rigsite Multidisciplinary Collaborative Concept,” presented at the 2012 IADC/SPE Drilling Conference and Exhibition, San Diego, Calif., 6–8 March 2012.