KCA DEUTAG to deploy highly automated T-700 for NAM in Holland
By Katie Mazerov, contributing editor
KCA DEUTAG recently commissioned its new highly automated, small-footprint T-700 Heavy Land Rig (HLR), scheduled to begin work in The Netherlands in February. The rig was unveiled in early December at the company’s manufacturing facility in Bad Bentheim, Germany.
The rig is under a two-year fixed contract, with options, to Nederlandse Aardolie Maatschappij (NAM) and will be initially deployed for NAM’s drilling campaign in the north of Holland. KCA DEUTAG designed and engineered the rig together with subsidiary BENTEC, with input from NAM. “The long-term relationship between our companies allowed a truly collaborative effort during the design and construction phase of this rig,” said Joep Beijer, senior vice president for KCA DEUTAG.
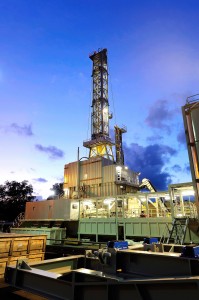
“The key design feature is the highly automated, integrated pipe-handling system that was designed to advance the hands-off philosophy, whereby the pipes are picked up from ground level and transported to well center by automatic sequence,” he explained. “The system increases operational efficiency while decreasing the human interaction on the rig floor, thus enhancing our ability to provide safe, effective and trouble-free operations.” Pipe-handling and racking can handle 2 7/8-in. to 5 ½-in. (single & double) tubulars and up to 20-in. casing without a tool change.
The rig, which has a 480-metric-ton hookload capacity, will kick off operations drilling several deviated wells that will average 5,000 meters deep. The rig can drill up to 7,400 meters, however, and has full extended-reach capacity if that needed.
Meeting high standards
The collaborative design effort also resulted in several features that meet high environmental standards. “It is extremely difficult in The Netherlands to receive approval for drilling locations, so the rig needed to have a small footprint,” Mr Beijer said. “It meets both low-visibility and low noise-emission standards, which are very important in densely populated Holland.” The rig has an overall height of 151 ft, relatively low of typical rigs of that size, and a mast height of 113 ft. “The higher the rig, the higher the top drive, which generates most noise emissions,” he added. The rig also can be operated from the public power grid, which further reduces noise emissions.
The rig includes skidding capacity for drilling on cluster locations. It is designed for tripping speeds of 600 meters/hr and “unlimited” setback capacity. “A conventional rig is limited by the mast setback capacity,” Mr Beijer said. “With this design, we are laying down tubulars at ground level, so the setback capacity is limited by the location size.”
The top drive from BENTEC has a hoisting capacity of 1.1 million lbs and offers a continuous torque of up to 63,000 Nm (approximately 46,400 ft-lbs), a rotating speed of 230 RPM and working pressures up to 7,500 psi. The drawworks, also manufactured by BENTEC, was designed with an open front to eliminate noise resonance and reduce noise due to redundant container ventilation. A remote station on the drawworks facilitates safe slip and cut operations.
The overhead crane was designed to be a “one hand” operation for handling bottomhole assemblies, cross-over, stabilizer and special tools.
The T-700 is a further development of the EuroRig, which was designed with a small footprint and low environmental impact requirements and carries full European certification. Mr Beijer said the EuroRig has been well-received, with three units currently involved in shale gas projects in Poland. The company is also building Cluster Slider rigs, which can skid easily from one well to another, for the Russian market. Technical know-how obtained during these operations can be easily incorporated in next design of the EuroRig to make the unit fit for production drilling, he added.
EuroRig and Cluster Slider are trademarked terms of BENTEC.