7 ways to set up a successful joint rig auditing task force: lessons learned from OMV case study
By Stefan Wirth, OMV E&P, and Andrew Calderwood, ModuSpec Engineering
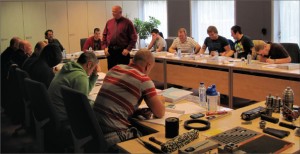
Audits performed on drilling and workover rigs and associated equipment are an important means of ensuring safe and efficient operations of the complete unit. With the need for such audits, the associated workload has increased significantly throughout the E&P industry over the past few years. Due to the increase, operators are struggling to have adequate personnel available in order to conduct such audits.
OMV, as a mid-sized operator, acknowledged that it would not be possible to internally build a team in the near future with an adequate amount of qualified people. The company decided to join with ModuSpec Engineering to provide OMV with the proficient personnel required.
While ModuSpec could assess rigs and equipment based on API and other international standards, OMV’s internal standards and policies had to be included into the scope. Both partners thus decided to form an auditing task force, comprising about a dozen surveyors and a training program to ensure that the surveyors understood OMV’s specific requirements.
At the time of writing, this task force had been up and running for over one and a half years and had resulted in several lessons learned. This article will provide an overview of major lessons learned in the implementation and operation of a rig auditing task force.
1. Operator setup
To establish a suitable rig audit task force, there needs to be an adequate setup within the operator’s organization. Experience has shown that it is most beneficial to have a separate department working closely with the auditing contractor. This department will have to maintain direct contact with the contractor and internally coordinate the individual audits. It is vital that this department maintains constant awareness of all relevant internal standards and procedures.
In OMV’s case, it is also responsible for the development and revision of all drilling- and workover-related standards. In addition, members of this department also needed to have sound knowledge of applicable international standards because they will act as a quality-control institution for the whole audit process.
2. Contractor setup
The contractor has to provide the majority of the manpower required to execute the audits. His personnel must satisfy certain prerequisites, including but not limited to:
• A profound knowledge of drilling and workover equipment;
• In-depth understanding of drilling and workover operations;
• A highly developed personal HSE culture;
• High communication skills;
• Extensive knowledge on applicable international standards;
• Knowledge of applicable local country standards.
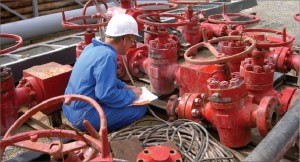
The contractor has to work in close association with the operator when training his personnel in order to meet special requirements. As audit contractors normally employ a significant number of surveyors, it is not possible to train all of them in the particular requirements of an individual client. This is the main reason for forming a rig audit task force.
To arrange for timely audits, it is beneficial that the members of this task force are located, where possible, in close proximity to operator branches.
3. Training
Operators need to train the members of the Task Force on their own standards and procedures, which set the stage for the audits. It is important to understand that classroom training alone will not be sufficient – learning by practice is of great importance. During this initial phase, the operator has to provide additional support and guidance to the surveyors.
The partnership between OMV and ModuSpec showed that certain flexibility in conducting the required training is of essence. It is therefore recommended to make maximum use of modern learning tools (e-learning) that allow such flexibility.
4. Clear interface structure
In the course of the partnership, ModuSpec surveyors expressed its need for having a clear contact point with the operator. This was partially related to the experience of many surveyors where the scope of work might change when dealing with different personnel from within the operator’s organisation. A clear and single point of contact prevents such problems and enables a quick and effective way to incorporate and plan changes due to unexpected occurrences. On the other hand, a clearly defined interface structure is also beneficial for the operator as it creates a sole point within the company to coordinate and control the audits.
5. Independence
The operator will receive only comparable audit reports if he can make sure that the audit scope remains consistent. The surveyors, as service providers, will always have to follow client requirements. It must be made clear to operator subsidiaries that they are not empowered to change the audit scope directly with the surveyors; otherwise, the audit outcome may vary quite significantly.
6. Feedback and continuous learning
Each audit is documented by an audit report, which is a significant decision-making tool for management on how to proceed with the audited unit. However, before the final version of the report is issued, the audit contractor supplies a preliminary report to the operator, providing the opportunity for both operator and contractor to learn from each other’s knowledge and experience by discussing the findings. This leads to an improved final version of the report and to a continuous improvement of overall audit quality.
7. Focus on HSE
Although a rig and equipment audit will always be much more than a pure HSE audit, it cannot be emphasized enough that the focus of the audit needs to be HSE. Therefore, all audits are structured around the identification of deficiencies in regard to equipment, crew competence and management systems that could lead to major accidents, with major accident in this context being defined as any incident that may lead to fire, explosion, injury or death, major spills and/or loss of reputation.
Equipment performance is of secondary concern, with the subsidiary having the option to incorporate performance checks on the equipment in order to have a tool for the comparison of different units. However OMV will only accept units on contract or to continue operation where no critical safety findings have been identified or where previously identified critical deficiencies have been resolved.
CONCLUSION
In light of the Macondo incident in the US Gulf of Mexico, it is anticipated that control of the risks involved in drilling and well intervention operations will receive even more attention by all operators moving forward. Auditing, as the major tool in this risk-control process, will be given a higher profile but should also become accepted as a routine task within the industry.
Many operators might not have the manpower available in-house to handle all required audits on their own. A rig auditing task force as described in this article may bridge the gap between staff restrictions and still having operator-specific quality-control measures in place instead of relying solely on “industry standards” or “best practice.”
This article is based on a presentation at the IADC Drilling HSE Europe Conference & Exhibition, 29-30 September, Amsterdam.