2012 IADC/SPE Drilling Conference: Exclusive roundup of abstracts from 18 technical sessions and 13 e-poster sessions
TECHNICAL SESSION I: DRILLING AND BIT TECHNOLOGY
IADC/SPE 151456
PDC Cutter and Bit Development for Challenging Conglomerate Drilling in the Luno Field Offshore Norway, S. Hellvik, E. Hoel, Lundin Norway; R. Nygaard, Missouri University of Science and Technology; M. Andersen, M. Francis, National Oilwell Varco
The Luno discovery in the Southern North Sea has created unique drilling challenges. The reservoir planned with horizontal producers and inclined water injectors consists of both sandstones and conglomerates with varying sizes and distribution of granite clasts.
After the field tests were conducted, it was decided to initiate a polycrystalline diamond compact (PDC) development project to develop a PDC bit with cutters that could withstand the challenging drilling of the conglomerate for the field development phase. From the various cutter performances observed during the field test, further laboratory and field testing was conducted. The cutters showed preliminary performance results of three to four times the initial durability potential.
IADC/SPE 151789
Solving Deep 22-in. Carbonate Drilling Challenges in Northern Kuwait, A. Al Saleh, A. Shehab, M. Al Khaldy, Kuwait Oil; G. Portwood, O. Ghoneim, H. Maliekkal, Schlumberger
The operator must drill a deep, vertical 22-in. hole section in a high-pressure, high-temperature environment to efficiently tap Jurassic reserves in the North Kuwait gas fields. Historically, the section has been drilled with polycrystalline diamond compact and carbide insert (TCI) bits. Neither could consistently complete the hole section in one run. To solve this problem, a forensic investigation of TCI bearing, carbide materials and insert shapes was conducted. The study resulted in new impact-resistant carbide grades and unique insert geometries tailored for Middle East carbonate/sandstone drilling.
IADC/SPE 151569
Innovative PDC Cutter Technology Leads to Step-Out Performance Improvements in Diverse Applications in Shale Plays, D.E. Scott, M.J. Meiners, M.R. Isbell, Baker Hughes
This paper will highlight the latest innovative polycrystalline diamond compact cutters, which have led to improved consistency in diverse US land applications, including shale plays and traditional applications, when combined with the latest in bit design, drilling systems and application techniques. Case studies from multiple fields will be shown with more than 35% increase in rate of penetration, more than 50% improvement in footage, improvements in reliability and a significantly improved dull condition, which gave the operator more confidence in making the target intervals.
IADC/SPE 150030
New HT/HP Technology for Geothermal Application Significantly Increases On-Bottom Drilling Hours, S. Orazzini, ENEL Italy; R.S. Kasirin, G. Ferrari, A. Bertini, I. Bizzocchi, R.J. Ford, Q. Li, J. Zhang, Schlumberger
Standard geothermal roller-cone (RC) bits and components, including grease and elastomer seals, are adequate for temperatures only up to 300°F. At higher temperatures, the bits’ internal components and lubrication system can degrade, leading to bearing failure and limiting on-bottom drilling hours.
To solve the problem, a series of tests were conducted with temperature-resistant elastomers and grease compounds in a controlled laboratory environment. The experiments resulted in a new line of RC bits equipped with an innovative bearing system that includes new composite elastomer seals with Kevlar fabric and a high-temperature (HT) grease formula. The new technology platform has increased seal life, lubricity and load capacity at elevated temperatures in HT and high-pressure applications.
TECHNICAL SESSION 2: DRILLING PROCESS AND TECHNOLOGY
IADC/SPE 150931
Multiple Criteria Casing Seat Selection Method, B.S. Aadnoy, E.Kaarstad, M. Belayneh, University of Stavanger
This paper presents a new integrated method for selection of casing seat locations that includes the fundamental gas filled casing criterion, the kick margin, the riser margin, the minimum mud weight to drill the next section and the assessment of the weak point in the well. The objective is to avoid failures below the wellhead and that the casing shoe represents the weak point in the well.
IADC/SPE 150942
An Early Warning System for Identifying Drilling Problems: An Example from a Problematic Drill-Out Cement Operation in the North Sea, E. Cayeux, B. Daireaux, E.W. Dvergsnes, International Research Institute of Stavanger; G. Saelevik, M. Zidan, Statoil
We describe the validation of a software solution that automatically detects changes in downhole drilling conditions. Based on early warnings provided by the system, drilling teams can take preemptive action when conditions start to deteriorate. The principle of the system is to compare results from calibrated physical models of the well with surface and downhole measurements.
IADC/SPE 151381
Dynamic Modeling of Gas Distribution in the Wellbore During Kick Situations, H.F. Spoerker, OMV Exploration & Production; C. Gruber, W. Brandstaetter, University of Leoben
This paper presents a computational fluid dynamics simulation of the distribution of influx gas in the drilling fluid during kick situations. Focus is put on the bottomhole inlet region of a vertical well with the aim of obtaining a highly resolved phase distribution. An interfacial tracking method is used to simulate the unsteady motion of incompressible drilling fluid and compressible gas, taking into account turbulence, as well as non-Newtonian rheology. This method describes both phases with a single set of equations and solves an equation to calculate the local volume fraction of the phases. Hence, no prior assumptions need to be made regarding flow patterns. The result of these simulations will subsequently be used to model the chemical reaction kinetics of the buffering process between H2S influxes and high pH drilling fluid environments.
IADC/SPE 151389
Drilling Performance is a Function of Power at the Bit and Drilling Efficiency, R.C. Pessier, S. Wallace, H. Oueslati, Baker Hughes
This paper will show how the power at the bit and drilling efficiency vary as a function of drill string and bottomhole assembly configuration, bit selection and drilling parameters. Field examples will illustrate the magnitude of parasitic losses caused by well geometry and the downhole environment. In many cases, it is striking how little power is left for the drill bit, which in the end dictates the potential rate of penetration and thus the cost per foot and economics of the drilling process.
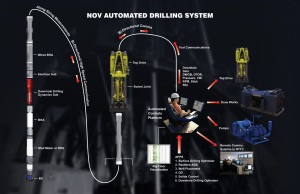
TECHNICAL SESSION 3: RIG AUTOMATION AND TECHNOLOGY
IADC/SPE 151193
Near Field Developments with an Upgraded Brown-Field Platform Rig: Sharing the Learning from a Three-Well Extended-Reach Drilling Program, M. Mota, G.W. King, W.D. O’Donnell, ExxonMobil; K. Hewit, KCA DEUTAG; P.A. Dumont, Shell
The paper will summarize the upgrade concept selection, concept definition and modifications for a two-stage upgrade of a 35-year-old platform rig on a production platform. This individual extended the drilling radius from 15,000 ft to 25,000 ft, increasing the well control system rating from 5,000 to 10,000 psi. This combination enabled the development of new fields that could not support subsea infrastructure.
IADC/SPE 150973
Building an Automated Drilling System Where the Surface Machines are Controlled by Downhole and Surface Data to Optimize the Well Construction Process, T. Pink, A. Bruce, H. Kverneland, B. Applewhite, National Oilwell Varco
After substantial industry research, it was decided that an automated drilling system needed to satisfy several criteria while improving operational safety and drilling a faster, better well: be the same on every rig, have an open architecture downhole and on surface, designed to be economically viable in the unconventional market, designed so the rig can be run with fewer personnel, and be customer-configurable. The significance of the project to build this automated drilling system could be vast.
IADC/SPE 151412
Data Aggregation and Drilling Automation: Connecting the Interoperability Bridge between Acquisition, Monitoring, Evaluation and Control, A.G. Sadlier, M.L. Laing, J.A. Shields, Baker Hughes
In this paper, we review several technologies in use through the drilling industry – WITS, WITSML, OPC and PROFIBUS – and present case studies about the current roles these technologies play and the problems they solve. The authors analyze the limitations between these interoperable systems and associated barriers in achieving the drilling automation vision.
IADC/SPE 151190
Case Study on Bottomhole Assembly Tool, R. Verhoef, National Oilwell Varco
In these days of rig automation and advanced rig mechanization, the industry may wonder why running the bottomhole assembly (BHA) still requires more people on the drill floor and more equipment than when tripping in or out. This paper presents design challenges, prototype testing and field testing leading to the final version of the Bottom Hole Assembly Tool, which provides solutions to the main challenges in handling the BHA.
TECHNICAL SESSION 4: DIRECTIONAL DRILLING AND HOLE PLACEMENT
IADC/SPE 151039
The Design of BHA and the Placement of the Magnetometer Sensors Influence How Magnetic Azimuth is Distorted by the Magnetic Properties of Drilling Fluids, T.I. Waag, Teknova; T. Torkildsen, Wellpos; P.A. Amundsen, University of Stavanger; E. Nyrnes, Statoil; A. Saasen, Det Norske Oljeselskap
This study focuses on how the magnetic distortion caused by the magnetic drilling fluid is influenced by geometric issues. This has been analyzed by finite element studies of several measurement-while-drilling tool geometries and locations of the bottomhole assembly (BHA) in the wellbore. Knowledge about the magnetic properties of the drilling fluid is essential for estimation of wellbore accuracy and multi-station analysis of magnetic survey data. Our results demonstrate the importance of the geometry of the BHA and the directional tool.
IADC/SPE 150107
Successful Application of Geomagnetic Referencing for Accurate Wellbore Positioning in Deepwater Project Offshore Brazil, B. Poedjono, D. Montenegro, Schlumberger; P. Clark, S. Okewunmi, Chevron; S. Maus, University of Colorado; X. Li, Fugro Gravity and Magnetic Services
This paper outlines a collaboration among operator, contractors and academic experts and the development of the High Definition Geomagnetic Model by the National Geophysical Data Center, which improves the spatial resolution to 30 km. The large-scale magnetic field study was integrated with the Bacia de Campos aeromagnetic survey to account for the entire spatial spectrum of the geomagnetic field to the km scale. Using ellipsoidal harmonic functions and an equivalent source technique, two 3D geomagnetic references with downward continuous models were produced for comparison purposes, and the results were validated by observations from downhole magnetic tools.
IADC/SPE 151431
High-Angle Gyro-While-Drilling Technology Delivers an Economical Solution to Accurate Wellbore Placement and Collision Avoidance in High-Density Multilateral Pad Drilling in the Canadian Oil Sands, K. Brown, Cenovus Energy; K. Beattie, C. Kohut, Gyrodata
Cenovus Energy initiated an aggressive infill drilling program early in 2011 in its Pelican Lake polymer/water flood project in northeast Alberta. By mid-year, the company had drilled 52 injection and producing wells, and drilling was scheduled to continue at the same pace through year-end. This paper will provide the results of the initial tests and analyze GWD performance during drilling, with statistics compiled from more than 60 wells. The savings from eliminating the backup surveys will be presented along with other benefits and observations.
IADC/SPE 151221
Converting Static Friction to Kinetic Friction to Drill Further and Faster in Directional Holes, L. Skyles, Y. Amiraslani, National Oilwell Varco; J. Wilhoit, Devon Energy
In “sliding” operations during directional drilling, the challenge has always been to overcome static friction between the drill pipe and the hole wall while the pipe is not rotating. This static friction can be overcome and even converted to kinetic friction by using a mud-operated downhole tool that axially agitates the drill string; constantly breaking static friction.
IADC/SPE 151047
Using Deep-Azimuthal Resistivity and 3D Seismic for Optimal Horizontal Well Placement: An Integrated Approach, Nipisi Field, Western Canada, S.J. Omovie, Baker Hughes; W.R. Pearson, Pradera Resources
This paper focuses on the integration of geological/3D seismic mapping and measurement-while-drilling azimuthal resistivity for optimal horizontal well placement in a tight limestone reservoir, as well as the limitations of each technology when used in isolation. It illustrates how utilizing this approach, the operator was able to achieve 100% reservoir exposure.
IADC/SPE 151436
High-Definition Geomagnetic Models: A New Perspective for Improved Wellbore Positioning, S. Maus, M.C. Nair, University of Colorado; B. Poedjono, Schlumberger; S. Okewunmi, Chevron; D. Fairhead, GETECH; U. Barckhausen, German Federal Institute for Geosciences and Natural Resources; P.R. Milligan, Geoscience Australia; J. Matzka, Technical University of Denmark
This paper will illustrate the details of the new high-definition geomagnetic reference; its application in different hemispheres to improve well placement, prevent and mitigate the danger of collision with existing wellbores and enable precise relief well drilling; and its use with magnetic tools in real-time steering to save rig time and reduce drilling costs.
TECHNICAL SESSION 5: DEEPWATER
IADC/SPE 151186
Upgrading the Real-Time Drilling Optimization Culture in Brazil’s Challenging Deepwater Operations: The Utilization of a Remote and Rigsite Multidisciplinary Collaborative Concept, A. Borella, D.S. Gozzi, I. Fujshima, K.L. Vello, Petrobras; S.B. Alves, I.J. Thomson, R.M. Krasuk F. Buzzerio, Baker Hughes
In recent years, deepwater drilling operations have become more challenging and expensive with new exploratory frontiers and the rise of rig rates, demanding the need for first-class drilling optimization technology and services.
This paper will present the fundamentals of this real-time remote and rig site drilling optimization concept, with focus on integration between the operator and the service company, the operational aspects with regards to appropriate communication protocols and decision-making processes, highlighting the performance improvement achieved to date.
IADC/SPE 151198
Establishing an Industry Best Practice on Subsea Wellhead Fatigue Assessment, D. Buchmiller, T. Horte, G. Grytoyr, L. Haug, Det Norske Veritas
Wellhead fatigue has received priority attention within the drilling industry, especially on the Norwegian Continental Shelf. Focus has been on developing a universal wellhead fatigue calculation methodology. Motivation for developing an industry guideline stems from the fact that existing international standards provide limited or no guidance on wellhead fatigue calculation. This is part of an ongoing joint industry project facilitated by Det Norske Veritas with participation from Statoil, BP, BG Group, ExxonMobil, Marathon Oil, Eni, Shell, Total, Talisman, Woodside and Lundin.
IADC/SPE 151350
Newbuild Construction Cycles – An Evolving Paradigm, I. Hope, Seadrill; S. Livingston, J.L. Ogg, National Oilwell Varco
Current trends and lessons learned from the recent newbuild trend will be discussed, focusing on the handover of turnkey rigs to drilling contractors.
The paper will focus on where the new risks can be identified while providing methods for a drilling contractor to apply their valuable knowledge and experience. The objective is to ensure the most efficient way of ensuring that these highly complex rigs meet the needs of both the drilling contractor and the customer.
IADC/SPE 151487
Continuing Efficiency and Assurance Advances for Deepwater BOP Testing, C. Franklin, R. Cully, IPT Global
Recently, a significant advancement to deepwater blowout preventer (BOP) leak detection was introduced through an industry-sponsored software development project.
This paper introduces and discusses these advancements. Rigs will utilize a customized schematic of the BOP and manifold within the application. With this working model, the subsea engineer will have the ability to optimally design each of the required tests by simply clicking to close and open manifold valves, BOP rams, annulars, etc.
IADC/SPE 151182
Blowout Preventer Health Monitoring, J.E. Mckay, BP; C. Simmons, National Oilwell Varco; T. Hogg, Ensco; G. Starling, Rock Oilfield Group; M. Doty, National Oilwell Varco
This paper aims to present the use of a real-time dashboard to determine blowout preventer (BOP) health based on levels of system redundancy, the required coordination between the rig contractor and BOP manufacturer on system development, software and hardware development and installation, “traffic light” logic development, operational considerations for BOP health, any lessons learned from the Ensco DS 4 pilot, and future plans for the technology.
IADC/SPE 151733
Focused Approach to Solving Deepwater Reaming Problems, C.H. Dewey, L. Paez, P.C. Desai, Schlumberger
This paper presents an innovative and focused approach to the deepwater reaming operations where all drilling and operational issues are analyzed and a comprehensive solution is developed that meets the challenges presented by the specific application. The authors will provide an overview of the features and system functionality and each of its critical components.
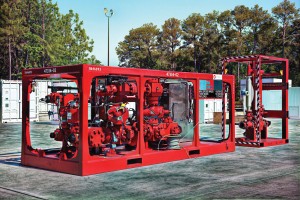
TECHNICAL SESSION 6: MANAGED PRESSURE DRILLING
IADC/SPE 151168
Next-Generation Managed Pressure Drilling System Enables HPHT Horizontal Wells in the Haynesville Shale, J. Montilva, J.F. Mota, Shell; I. Poletzky, M. Sati, R. Lovorn, J. Grable, Halliburton
This paper describes implementation of a fully automated MPD, which incorporates a rig pump diverter (RPD) that allows smooth transition from circulating to non-circulating downhole during connections while maintaining continuous rig pump circulation. The RPD system allows flow to be diverted from the stand pipe to the choke manifold, enabling precise control of bottomhole pressure for controlled transition from drilling mode to connection mode. This paper will further describe the time savings and enhanced drill crew workflow using the RPD system in not having drill crew to shut down or manipulate the rig pumps during connections.
IADC/SPE 151518
Automated Managed Pressure Drilling Allows Identification of New Reserves in an HPHT Exploration Well in Sepat Barat Field, Offshore Malaysia, I. Azian Bt A Aziz, L. Umar, N. Nordin, T. Nesan, Petronas; F. Rojas, F. Zapata, G. Garcia, A. Waquih, B. Subroto, B. Dow, Schlumberger
The Sepat Barat field is located in Block 313 on the west side of the Malay Basin, Malaysia. It is notorious for its steeply rising pressure ramp, narrow drilling operation window and interbedded sand, coal and shale formations.
This paper will describe the design efforts employed while preparing to drill the SBD-2 well. The challenges and lessons learned, particularly managing pore pressure prediction with multiple techniques, will be discussed. Lessons learned and recommended workflows for similar projects will also be outlined.
IADC/SPE 151392
An Improved Dynamic Well Control Response to a Gas Influx in Managed Pressure Drilling Operations, W. Bacon, Blade Energy; A.Y. Tong, University of Texas at Arlington; O.R. Gabaldon, C. Sugden, P.V. Suryanarayana, Blade Energy
MPD offers the capability to control an influx dynamically without conventionally shutting in. One current method employs applied back pressure (ABP) to force flow exiting the annulus to equal flow entering the drill pipe, which is interpreted as influx cessation. However, solely ensuring flow continuity does not imply influx cessation, unless the annular fluids are incompressible. In this work, the impact of compressibility on dynamic well control is investigated.
IADC/SPE 151416
Automated Drilling Systems for MPD – The Reality, S. Saeed, R. Lovorn, K. Knudsen, Halliburton
Though there is a lot of material pertaining to the benefits and functionality of MPD automated drilling systems, there is little technical information on how the systems actually functions. This paper will examine the internals of such a system and detailing how it actually works. The components, technology and architecture used will be presented in detail.
IADC/SPE 151085
Mud Cap Application Solves Chronic Drilling Problem in a Highly Fractured, Low-Pressure Reservoir, J.J. de Guevara, M.A. Lozada, M. Torres, G. Silva, J. Zaldivar, Pemex; R. Gonzalez, J.P. Sizer, Quantum Reservoir Impact
This paper describes the first successful mud cap application in the Cantarell Field in the Bay of Campeche. Mud cap drilling was applied from 2,843 meters to the total depth of 3,360 meters. The 517 meters was drilled with increased penetration rates, from an average of 28 meters/day before starting mud cap to over 100 meters/day after applying this technique. In addition, the consumption of drilling fluids was decreased by 73%.
IADC/SPE 151249
Continuous Circulation Drill String Sub, J. Weir, R.S. Goodwin, R. Macmillan, National Oilwell Varco
This paper describes the current managed pressure drilling (MPD) market and the philosophy adopted for a new side-entry sub. The new sub is focused on safety, reliability and becoming part of drilling process. The design does not place rig personnel near the high-pressure drilling mud. The sealing component between the high-pressure drilling mud and atmosphere is easily removed and inspected between every connection. This ensures reliability of the barrier, regardless of how long the sub has been in operation.
TECHNICAL SESSION 7: DRILLING PERFORMANCE AND OPTIMIZATION
IADC/SPE 151451
Real-time Motor and Turbine Performance Monitoring and Optimization, M. Ringer, A.B. Johnson, M. Barrett, G. Goldsmith, G. Flint, S. Mao, D. Terracina, Schlumberger
We present the results from a field test where both a turbine and a positive displacement motor were instrumented to provide real-time measurement of their shaft speed. This permitted the construction, in real time, of the actual performance characteristics of the motor and immediate feedback as to the driller’s operating point on the motor’s power curve. This information was then used to optimize the drilling parameters used by the driller to maximize instantaneous output power of the motor and the rate of penetration.
IADC/SPE 150959
Successful Optimization Strategies Combine to Deliver Significant Performance Boost at the Edge of the ERD Envelope, Sakhalin Island, Russia, R.W. James, P.E. Pastusek, G.R. Kuhn, A. Andreev, J.R. Bailey, L. Wang, ExxonMobil
Numerous performance enhancement initiatives were used by the operator for the Sakhalin I project in drilling and completing the extended-reach drilling (ERD) program at the Odoptu Field, Sakhalin Island, Russia. As a result of the drilling successes and favorable production performance, the initial seven-well ERD program was expanded to nine wells. The operator’s philosophy of relentless redesign to remove limiters from the drilling process resulted in significant performance improvements in all areas of drilling and completion operations. This paper will provide details and results for many of the key performance initiatives employed.
IADC/SPE 151177
Performance Drilling – Innovative Concepts Improve Benchmarking and Optimization Processes, G. Mensa-Wilmot, P. Yimpoonsap, Chevron
Performance drilling is globally accepted as an enabler to drilling cost reductions. This realization is particularly important considering today’s applications and harsher drilling environments. To improve and make performance drilling more effective, innovative concepts – formation drillability, drilling index and performance drilling evaluation – will be introduced. The paper will show and discuss how the new concepts have been used on different projects globally.
IADC/SPE 151502
Revolutionizing Drilling Performance through Advanced Real-time Advisory System, B. Dow, R.J. Harmer, J. Belaskie, Schlumberger
This paper will discuss the development and field application of a new technology that allows data to be turned into actions at the well site, improving overall well construction performance. The development team applied a rich understanding of existing well-site workflows, technology and workplace ergonomics and key attributes from gaming and telecommunications industries.
TECHNICAL SESSION 8: FLUIDS TECHNOLOGY I
IADC/SPE 151469
A New SBM for Narrow Margin Extended Reach Drilling, J. Lee, D.D. Cullum, J. Friedheim, S. Young, Schlumberger
A new synthetic-based drilling fluid (SBM) with a new emulsifier and rheology modifier package has been designed for narrow extended-reach drilling. This flat rheology SBM utilizes a single emulsifier to simplify fluid formulation, improve emulsion stability, enhance thermal stability and provide surface-wetting and fluid lubricity.
This paper describes the new flat-rheology SBM system with examples showing typical mud formulations, fluid properties, barite sag performance data, field test data and computer hydraulics simulation of equivalent circulating density impacts.
IADC/SPE 151231
Integrated Drilling, Completion and Stimulation Approach Facilitates High-Productivity Horizontal Well with 10,000 ft Pay Interval, J.D. Jorden, A.M. Jackson, M.A. Al Marzouqi, Zakum Development; S.R. Keller, C.E. Shuchart, C. Ivan, M.V. Phi, ExxonMobil
A linear maximum reservoir contact well with a 10,000-ft horizontal completion interval was drilled and completed in a major carbonate oil field offshore Abu Dhabi. This paper will describe the integrated drilling, completion and stimulation approach taken for planning and executing this well.
IADC/SPE 151413
Rheological Properties of Invert Emulsion Drilling Fluid Under Extreme HTHP Conditions, J. Lee, S. Young, Schlumberger; A. Shadravan, Texas A&M University
This article compares the rheological properties of invert emulsion drilling fluid generated from three types of rheometers from low temperature/pressure to extreme high-pressure, high-temperature (HPHT) conditions and analyzes rheological models that can be used to predict the behavior of invert emulsion drilling fluids under extreme HPHT conditions.
The data indicated several factors that can critically affect the rheology measurements, including drilling fluid chemistry, instrument setup and test schedule.
IADC/SPE 151453
Colorado Drill Cuttings Injection Pilot Results, K.R. Kunze, ExxonMobil; E.E. Romero, Imperial Oil Resources; S. Duck, ExxonMobil
From December 2007 through April 2011, the operator conducted a two-phase drill cuttings injection pilot at the Piceance Field in Western Colorado in an effort to reduce the environmental footprint. This was the first subsurface injection of drill cuttings in Colorado and utilized a lost-circulation zone in the Wasatch G formation as the ideal injection interval. The operator proved injection as a technically feasible option for drilling waste disposal during full-field development at Piceance.
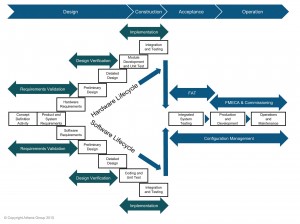
TECHNICAL SESSION 9: IMPROVING BUSINESS MANAGEMENT: CONTRACTS, MANUFACTURING WELLS, ORGANIZATION
IADC/SPE 151394
Contractual Language Needed to Help Reduce Integrated Control Systems Risk on High-Specification Assets, B. O’Grady, Athens Group
This presentation will help drilling contractors, operators and shipyards develop and leverage contractual software standards to create an environment where vendors and stakeholders can work together to improve systems quality onboard high-specification assets and where all parties involved in asset construction and operation are accountable for helping to ensure that software-related issues do not result in nonproductive time or HSE risk.
IADC/SPE 151442
Drilling Contract Historical Development and Future Trends Post-Macondo: Reflections on a 35-Year Industry Career, C.A. Moomjian, CAM OilServ Advisors LLP
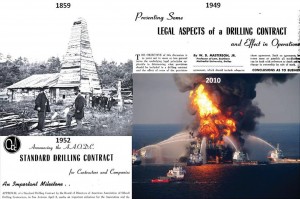
The author reflects upon a 35-year drilling industry career, more than half of which was as general counsel for major drilling companies, to describe the evolution of drilling contracts and discuss future trends.
The paper describes contractual provisions that were implemented to address technical innovations, such as horizontal drilling, extension into deepwater and dual-activity capability, and discusses the impact of the BP Macondo blowout and oil spill on contract terms. The paper also examines the important choice of law and dispute-resolution provisions.
IADC/SPE 151051
Manufacturing Wells: Myth or Magic, J.P. De Wardt, DE WARDT & CO.
This paper will describe the history of lean manufacturing and under what circumstances it can be applied successfully to well construction. It will build on the differences between project type and various ongoing business type of wells. It will describe where the opportunities are and where the barriers lay in the generation of value. It will also describe where manufacturing techniques run into challenges.
IADC/SPE 151338
Is There a Place for the High Reliability Organization in Drilling? J.L. Thorogood, Drilling Global Consultant
This paper will consider how apparently successful organizations can drift into failure as a result of the consequences of organizational complexity. These ideas will underpin a review of high-reliability organization theory and suggest ways that the principles might be applied to the management of drilling operations in the future.
TECHNICAL SESSION 10: STEERABLE AND DOWNHOLE TOOLS
IADC/SPE 149696
Rotary Steerable Tool Damage Prevention by Utilization of an Asymmetric Vibration Damping Tool, T.G. Burnett, B. Feauto, I Forster, A. Kabbara, National Oilwell Varco
This paper will provide an overview of the extensive research and testing of the tool, plus successful field performance. It will also focus on dual placement of the tool in horizontal applications. A number of added benefits were discovered during this run, including improved directional control, smoother trajectory and improved bit life. The vibration-damping tool resulted in extensive cost savings to the directional company and operator.
IADC/SPE 151322
Qualification of a 4.75-in. Rotary Steerable System for Complex 3D and High Build-Up Rate Applications in Through-Tubing Drilling Operations, M. Eidem, S.K. Andersen, K.M. Winterst, Statoil; S. Schwartze, C.C. Clemmensen, Halliburton; A.K. Nesheim, Baker Hughes
In collaboration with Baker Hughes, a modified 4.75-in. AutoTrak X-treme system successfully demonstrated maximum build-up and dogleg of 15°/30 meters in wells with 5.75-in. pass-through, verified capability of performing coiled-tubing drilling with regards to high dogleg capability with low weight on bit, demonstrated drilling capabilities with motor and with low RPM, demonstrated capability of holding tangent and verified high life time.
IADC/SPE 151603
Roller Reamer Fulcrum in Point-the-Bit Rotary Steerable System Reduces Stick-Slip and Backward Whirl, D.R. Stroud, N. Bird, P. Norton, Weatherford; M. Kennedy, M. Greener, X Driling Tools
An increasing proportion of wells are drilled using RSS, whose bottomhole assembly (BHA) dynamic behavior is very different to that of steerable mud motors. This return to rotary drilling has renewed industry interest in detrimental dynamic phenomena such as backward whirl. Preventing these undesirable dynamics is crucial to drilling efficiency, and it is widely recognized that the nature of BHA/borehole contact points plays a key role in preventing backward whirl.
This investigation focuses on how roller reamer technology can be adapted for use as a key component in rotary steering assembly to prevent borehole traction without causing side cutting and hole enlargement and without adversely affecting system steerability.
IADC/SPE 151096
Axial Excitation and Drill String Resonance as a Means of Aiding Tubular Retrieval: Small-scale Rig Testing and Full-scale Field Testing, I. Forster, R. Grant, National Oilwell Varco
This paper describes the work carried out at National Oilwell Varco on an in-house designed and built, small-scale vibration test rig, which was developed with the purpose of studying the effect of axial excitation on tubular retrieval.
With reference to offset data, the paper presents actual field data that demonstrates significant reductions in time spent during tubular retrievals and the corresponding cost savings.
IADC/SPE 151337
Development of a New Advanced Multiple Activation System for Concentric Underreamers, B. Torvestad, T. Ray, J. Hu, O. Gjertsen, Schlumberger; M. Muir, Maersk Oil and Gas
A new system has been developed that makes it possible to perform multiple activation/deactivation of the underreamer. The most obvious advantages are infinite open/close cycles for selective underreaming and the more flexible placement opportunities within the bottomhole assembly due to the activation method. Other advantages are time savings through the elimination of several runs, shorter activation time and higher flow-rate capabilities.
The authors will discuss the application challenges, benefits and engineering efforts, including field testing, that led to a commercial ream-on-demand system.
IADC/SPE 151500
Hammer Motor Smashes Its Way to Speedy Success in Brazil, R. Gee, T. Ramirez, S. Barton, D. Valmorbida, National Oilwell Varco; J. de Souza, C. da Fonseca, Petrobras; B. Cote, BBJ Tools
This paper discusses a case study from Brazil where the operator has been using turbine motors to drill vertical wells through hard rock formations. The hammer motor displayed significantly higher rate of penetration than the turbine motors without reliability constraints while also reducing bit costs and tool technician costs. These improvements in drilling performance have improved the economics of drilling these formations and are expected to be applicable to other drilling applications.
TECHNICAL SESSION 11: COMPLETIONS, ZONAL ISOLATION AND CEMENTING
IADC/SPE 151470
Special Considerations in the Design Optimization of High-Rate, Multistage Fractured Shale Wells, C. Sugden, G. Ring, P.V. Suryanarayana, Blade Energy; J.A. Johnson, M.R. Chambers, EXCO Resources
In this work, the major factors influencing normal and special loads on production casing in shale wells are discussed. A method for optimization of shale well production casing design is then introduced, followed by the constraints on the applicability of different design options.
IADC/SPE 151241
Interventionless Surveillance in a Multilateral Horizontal Well, C.A. Andresen, B. Williams, ResMan; M. Morgan, T. Williams, T.W. Crumrine, A.J. Bond, J. Franks, Pioneer Natural Resources
This paper reviews a case study from the Oooguruk field in Alaska, where a new style of chemical tracers embedded into the completion equipment were used to derive a quantitative estimate of the inflow distribution in a dual horizontal, multilateral well. This insight into the reservoir performance was obtained with no intervention into the well and only minor modifications to the completion design.
IADC/SPE 151147
Improvements in Production Liner Cementing for Coiled Tubing Drilling (CTD), M.O. Johnson, BP; J. Milne, Baker Hughes; C. Diller, Northern Solutions
This paper will begin with an update on the status of CTD on the North Slope and discuss how many of the challenges with drilling through/below the production tubing have been dealt with. The cost for a CTD sidetrack with an equivalent amount of reservoir exposure and zonal isolation is about half that of a rotary sidetrack. This is due to efficiencies in leaving the production tubing in place, efficiency of operations and less consumables.
IADC/SPE 151134
Innovative Well Completions Meet the Challenges of Producing High Wax Crude in a Giant Onshore Field in India, V. Kumar, T. McKenzie, R. Singh, A. Wenk, S. Chandra, Cairn India
Specialized rig setup and wellhead systems were designed to allow simultaneous deployment of production tubing, heater string, chemical and instrument lines, and electric submersible pump cables. The wellhead design ensures that barrier policies are maintained through well construction. Simultaneous running of all completion components warranted a specially designed tubing-running system and coiled-tubing deployment system built into the completion rig. Jet pump power fluid exposes the completion to high loads, which also made the completion design challenging. This paper describes the successful design and deployment of these innovative completions and wellhead systems.
IADC/SPE 151405
Slotted Liner for Continuously Acid Jetting Stimulation, S.S. Kofoed, F. Marketz, Maersk Oil; J. Krabbenhoeft, Krabbenhoeft Aps
In the appraisal well HDA 09 in the Danish part of the North Sea, it was determined that in order to make this well economically attractive, a negative skin of around 2 was required. Simulations showed that a skin of 2 can only be obtained if wormholes are made throughout the reservoir. This is possible by pin-pointed acid stimulation in open hole but, with stability issues while stimulating, this was not an option. A liner resembling open hole while stimulating had to be designed.
This paper will show the details of the study, including finite element analysis of the slotted liner design in regards to width and length of the slots, plus recommendation for manufacturing.
IADC/SPE 151171
True Zonal Isolation in Open-Hole Alternate Path Gravel Pack Completions, M.D. Barry, M.T. Hecker, C.S. Yeh, T. Moffe151403tt, ExxonMobil
New open-hole technology enables more extensive drilling to capture additional pay, selective completions to isolate undesired zones and production flow control inside the screen base pipe, similar to cased-hole conditions. True zonal isolation in open-hole gravel pack completions facilitates more flexible well planning and operational execution while maintaining reliable sand control. This paper will explore the range of application opportunities that this new technology presents.
TECHNICAL SESSION 12: DRILLING SYSTEMS AUTOMATION
IADC/SPE 151474
Drilling Automation: Potential for Human Error, F.P. Iversen, L.J. Gressgaard, International Research Institute of Stavanger; J.L. Thorogood, Drilling Global Consultant; M.K Balov, V. Hepsoe, Statoil
The authors analyze how use of a drilling support system in different modes and levels of automation may influence the system operator’s performance and risk of human error. Development of a systematic method for detecting mode confusion problems by model checking is central in this respect. The test cases have been simulated in a synthetic test environment created at the International Research Institute of Stavanger.
IADC/SPE 151736
Automated Closed-Loop Drilling with ROP Optimization Algorithm Significantly Reduces Drilling Time and Improves Downhole Tool Reliability, C.D. Chapman, J.S. Flores, W.M. Faisal, H. Yu, Schlumberger
This paper describes the optimization algorithm and focuses on the system architecture used to integrate the algorithm with the rig control system. The deployed architecture enables the algorithm to receive real-time data from the rig control system and drilling acquisition system to provide a complete data set to the rate-of-penetration optimization algorithm.
IADC/SPE 151257
Automation in Drilling: Future Evolution and Lessons from Aviation, J.L. Thorogood, Drilling Global Consultant
The paper will review developments of automation in aviation and describe problems that have arisen. It will then describe the analogous efforts in drilling and identify lessons that could be learned. The paper will present a rationale on which further automation initiatives might be based and the related changes that might be necessary as a result.
IADC/SPE 150941
Advanced Drilling Simulation Environment for Testing New Drilling Automation Techniques, E. Cayeux, B. Daireaux, E.W. Dvergsnes, A. Leulseged, International Research Institute of Stavanger; B.T. Bruun, Statoil; M.C. Herbert, ConocoPhillips
Newly developed drilling automation systems locate a computer interface between commands issued by the driller and instructions transmitted to the drilling machinery. Such functions are capable of faster and more precise control than that achieved by an unaided operator and thus can help drilling with narrow margins. To ensure that these systems work properly in all circumstances, an advanced drilling simulator has been developed to enable testing under a range of simulated conditions. The environment described in this paper uses hardware-in-the-loop simulation to verify that the automation techniques being tested respond correctly in real time.
IADC/SPE 151459
Real-Time Drilling Fluid Monitoring and Analysis – Adding to Integrated Drilling Operations, E. Ronaes, T. Stock, Schlumberger
Several attempts have been made to develop automated monitoring equipment for the most typical drilling fluid parameters. Due to the lack of sufficient data-transfer capability, those attempts had only limited success. Improved data flow between drilling rigs and operator and service provider’s land-based support organizations has created a renewed interest for remote real-time monitoring of drilling parameters. Development of data transmission systems like InterACT and data formats like WITSML have initiated the search for and development of new sensors, which can be used for automated real-time monitoring of important drilling fluid parameters.
IADC/SPE 151028
Applying Theoretical Control Strategies for ROP Optimization and Offshore Well Costs Mitigation, M. Folsta, A.L. Martins, Petrobras
The purpose of this article is to show a comprehensive analysis of the adequacy of different process control strategies to support the automation of the drilling process, with special focus on cost reduction. Different case studies are presented showing the potential of drilling automation strategies to reduce operational costs and risks.
TECHNICAL SESSION 13: DRILLING CASE STUDIES
IADC/SPE 151959
Deep Ultra-Slim Hole Drilling in Germany: Operational Experience, Current Developments, Way Forward, M. Elnozahy, M. Schmidt, D. Durkee, ExxonMobil
This paper reviews the operational experience made so far with ultra-slim hole drilling in Germany. This review includes the technical and geological challenges encountered and the different learnings made. Current developments to address the issues and their effectiveness are also discussed. The paper concludes with further areas of improvement for the future, focusing mainly on drilling systems.
IADC/SPE 151181
Use of Liner Drilling Technology as a Mitigation to Loss Intervals and Hole Instability: A Case Study in Mississippi Canyon, S.M. Rosenberg, D.M. Gala, Weatherford
This paper will demonstrate the benefit of using a liner drilling technology to ream, drill and cement a 7 5/8-in. drilling liner and 5-in. production liner in place. Liner drilling technology provided an effective solution to hole instability issues seen while drilling with conventional methods through a narrow mud weight/pore pressure/fracture gradient window laden with depleted intervals and virgin-pressured shales in the Mississippi Canyon block of the Gulf of Mexico.
IADC/SPE 151202
Regeneration of First-Generation Subsea Fields: The Challenges of New Wells in Old Infrastructure, S.R. Stright, V. Srivastava, G.W. King, D. Smith, N.C. Tears, ExxonMobil
The paper will describe how the unique challenges of re-drilling three subsea wells were overcome in old and declining fields where the original wells were designed and drilled with little consideration for redevelopment of the fields through reuse of existing wells.
There has been limited industry experience to date of subsea production well re-drills, and this paper will share the significant lessons learned, which will be of wider application as the number of subsea wells increase along with the requirement to maximize recovery and extend field life.
IADC/SPE 150664
Improving Drilling Performance in the Upper Cretaceous: A Case Study From Santos Basin, Brazil, S. Flores, L. Fagundes, Y. Irokawa, S. Flores, L. Fagundes, Y. Irokawa, OGX; A. Schmidt, H.J. Quinones, G. Landinez, P. De Oliveira, A. Ramos, Y. Medina Marquez, Schlumberger
During a recent exploratory campaign in the Santos Basin, severe levels of shocks and vibrations were encountered while drilling this large and intercalated hole section, resulting in low rate of penetration, premature bit wear, damaged tools, unplanned trips and drill string failures. Three to four bit runs were required to reach section TD. Post job information and drilling data were reviewed by an integrated operator/contractor team. A detailed engineering analysis of bit, BHA design and drilling mechanics was conducted to address the challenges of this section and propose a new approach to the drilling process.
TECHNICAL SESSION 14: FLUIDS TECHNOLOGY II
IADC/SPE 151473
Innovative Fiber Solution for Wellbore Strengthening, J.E. Friedheim, M.W. Sanders, J. Prada, R. Shursen, Schlumberger
We describe the path to designing and testing a new high-fluid loss, high-strength lost-circulation solution. The new pill system has been proven to work for a wide range of loss rates and provides a more effective and permanent seal than traditional treatments. An evaluation of the effectiveness of commercially available high fluid loss pill treatments will be presented, as will the methodology used to meet a set of ideal criteria for its use in the field.
IADC/SPE 151227
Size Degradation of Granular Lost-Circulation Materials, P.D. Scott, D.H. Beardmore, Z. Wade, ConocoPhillips; E. Evans, K. Franks, Chevron
Lost circulation is a major cause of drilling nonproductive time with significant cost implications. Laboratory and field data is presented to demonstrate the relative size degradation rates for several common lost-circulation materials. This data on the relative degradation in the particle size distribution of granular lost-circulation materials will provide improved understanding of their performance for more efficient application of the materials and will lead to improved wellbore strengthening and lost-circulation recycling applications.
IADC/SPE 151334
Integrated Pressure Management Processes for Reducing the Risk Associated with Well Instability Issues: Implications for HPHT Wells, J. Figenschou, A.K. Thorsen, Baker Hughes; B. Thistle, U. Williams, Suncor Energy
Optimizing well control processes are critical in high temperature/high pressure drilling operations so they do not encounter high cost overruns and compromise safety. The key to success is recognizing and mitigating challenges and associated risks early to adequately optimize drilling operations. This leads to a more effective drilling operation with reduced risk, increased safety margins and increased probability of successfully achieving the well’s objectives.
This case describes an integrated work process that has been implemented and incorporates both pre-drill and real-time pore pressure prediction with proactive ECD management during well planning and drilling operations.
IADC/SPE 151404
Improved Stability of Invert Emulsion Fluids, R. Van Zanten, J.J. Miller, C. Baker, Halliburton
This paper details an extensive investigation into the effects that emulsifier concentration, the addition of colloidal fines and shear, have on the stability of laboratory, mixing plant, and field-tested invert emulsion drilling fluids. Fluid stability is intricately linked to emulsion stability, which is directly related to the shear history of the whole fluid, the viscosity of the external phase, the emulsifier type and colloidal solids loading. Optimizing these properties can lead to more stable fluids that exhibit stronger gels and lower sag tendencies.
TECHNICAL SESSION 15: EXTENDED-REACH DRILLING, THE NEXT BIG STEPS
IADC/SPE 149778
Nikaitchuq ERD: Designing for Success on the North Slope of Alaska, M.M. Abahusayn, B. Foster, K&M Technology; J. Brink, M.D. Kuck, J. Longo, Eni
A 52-well heavy-oil field development targeting shallow sands on the north slope of Alaska was kicked off in 2010. Horizontal wells were drilled early in the program that served as data-gathering and technology-proving opportunities.
This paper will discuss the technical challenges, well design solutions and operational practices that were trialed and implemented to enable ER wells to be successfully drilled on the edge of the industry experience envelope, with all wells meeting targeted objectives.
IADC/SPE 151046
Pushing the Extended-Reach Envelope at Sakhalin: An Operator’s Experience Drilling a Record Reach Well, M.W. Walker, ExxonMobil
This paper will describe the evolution of well design changes at Odoptu, as well as the challenges successfully overcome, including remote logistics, wellbore instability, shocks and vibrations, and high torque. Significant achievements include the successful placement of completion equipment at world record depth and the drilling of each hole section with a single BHA.
IADC/SPE 151248
Directional Drilling Tests in Concrete Blocks Yield Precise Measurements of Borehole Position and Quality, E.J. Stockhausen, Chevron R. Lowdon, W.G. Lesso, Schlumberger
This paper discusses the TVD accuracy of the well as a function of different survey spacing and its impact on horizontal well placement. Changes in touch points of the BHA within the varying hole diameter of the slide/rotate sections are also discussed. Metrics are proposed for managing wellbore quality in terms of tortuosity and rugosity, along with their impact to the wider drilling community.
IADC/SPE 151386
From Field Test to Successful Integration of Broadband Drill String System for Offshore Extended-Reach Wells, D.M. Veeningen, J. Palmer, G. Steinicke, J. Saenz, T. Hansen, National Oilwell Varco
This paper describes the successful implementation of high-definition downhole operations through project management, collaboration with third-party tool partners and resourceful scalable solutions to solve operational and logistical challenges. Lessons learned include the implementation on two rigs, data swivel installations, the commissioning of a shore base and the pioneering of local repair and maintenance for specialized networked drilling tools, all leading to the complete integration into the customer’s workflow and process.
TECHNICAL SESSION 16: TUBULARS
IADC/SPE 150613
Buckling of Tubing Inside Casing, R.F. Mitchell, Halliburton
This paper presents various ways two concentric pipes can interact when one or both pipes are in compression, leading to a tendency to buckle. The contact forces between the pipes and with the external wellbore are explicitly calculated, and contact or non-contact conditions are determined. All results are analytic so that they can be easily used in spreadsheets or hand calculations.
IADC/SPE 151253
Comprehensive Review of Damages and Repairs on Drill Pipe Connections, T.M. Redlinger, P.S. Griggs, A. Odell, Weatherford; S. Bergo, Eurolncon
This paper will review inspection databases containing several years of drill pipe inspection records, in excess of 100,000 inspection records. The databases contain inspection records for several premium connections and API connections.
The paper will discuss how different inspection standards, premium connections, etc, can affect the damage at the end of the drilling program. The objective is to provide planning factors to the drilling community and to highlight the impact of connection selection and inspection standards on repairs.
IADC/SPE 151140
Innovative Tubular, Hoisting and Deepwater Rig Designs Extend Hook Load Envelope to 2,000,000 Pounds, J.N. Brock, B. Chandler, National Oilwell Varco; C. Selen, Maersk; J. Dugas, W. White, Quail Tools; M. Vasquez, A. Jonnalagadda, Statoil
This case study details the casing-landing operation on Statoil’s Tucker well in the Gulf of Mexico Ridge Block 543, where a string of 13 5/8-in. casing was landed with a total hookload of over 1.96 million lbs. The casing string was set to 24,893-ft MD (24,490-ft TVD) in 6,700 ft of water. This paper will discuss the planning, preparation and load path verificatio, as well as the design, development, manufacture and deployment of the 2 million-lb slip-based landing string that was required for this operation.
IADC/SPE 151810
Burst and Collapse Responses of Production Casing in Thermal Applications, D. Dall’Acqua, T.M. Kaiser, Noetic Engineering; M. Hodder, Shell
This paper describes numerical analyses for combined post yield loading conditions and is intended as a starting point for burst and collapse design for thermal casing.
In contrast to active axial load conditions, burst analysis of axially constrained casing indicates that an initial thermally induced axial strain exceeding yield does not substantially reduce the burst pressure. Sensitivity studies demonstrate the strong influence of pipe D/t and pressure ratios and pipe material mechanical properties on ovalization response.
IADC/SPE 150047
Successful Qualification and Deployment of a High-Pressure Drill Pipe Riser in West Africa, M. Camus, P. Auclair, Total; B. Horsburgh, Cameron; Y. Gallois, C. Rohart, H. Williams, Y. Mfoulou, VAM Drilling
This paper presents a high-performance drill pipe riser product for intervention systems designed and qualified for the USAN Project in Nigeria. The solution was manufactured in 2009, extensively tested and qualified prior to delivery the same year. The qualification performed included the ISO standard requirements and additional testing as requested by the Cameron/TOTAL USAN project team. This string has been successfully deployed since July 2010 offshore Nigeria by TOTAL.
IADC/SPE 151403
Hydrodynamic Loads, Soil and Structure Interactions in Conductor Design for Offshore Platforms and Jackup Rigs, N. Pilisi, D.B. Lewis, Blade Energy
This paper discusses the complete structural design of conductors used in offshore wells drilled from jackups and platforms in open water, by deriving equations and providing the essential steps that need to be followed to ensure the structural integrity of the conductor casing from the Texas deck to the setting depth of a few hundred feet below the mudline. To illustrate the methodology, a parametric study using data from different offshore locations with various water depths, external and internal loads, soil properties and metocean criteria has been carried out for both the drilling and production phases.
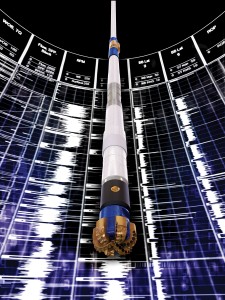
TECHNICAL SESSION 17: DRILLING DYNAMICS – A DEEPER UNDERSTANDING
IADC/SPE 151494
Vibration Failure Analysis in Riserless Conditions, R. Samuel, Halliburton
This paper presents and validates a modified model to predict severe damaging vibrations, analysis techniques and guidelines to avoid the vibration damage to BHAs and their associated downhole tools in the riserless highly deviated wells. The dynamic analysis model is based on forced frequency response to solve for resonant frequencies.
IADC/SPE 151477
Distributed Dynamics Feasibility Study, P. D’Ambrosio, R. Bouska, A.J. Clarke, J. Laird, National Oilwell Varco; J. McKay, S.T. Edwards, BP
To investigate the potential use of distributed dynamics for real-time decision, a test project was run to acquire vibration data along the drill string on a horizontal well in Oklahoma’s Woodford Shale. Four BHAs that included up to five independent Downhole Dynamic Data Recorders were run. The sensors were located a different positions along the drillstring.
This paper focuses on the analysis of the measurements gathered and will provide detail description of the results. Several concepts, as well as common known misconceptions related to drilling dynamics, will be discussed.
IADC/SPE 151395
Efficient and Reliable Vertical Drilling of Top Holes with RSS in Deepwater Gulf of Mexico, E.H. Chamat, R.R. Israel, Schlumberger
Rotary steerable systems (RSS) have become the tool of choice in large-hole sections through unconsolidated sediments. However, challenges in the drilling environment led to less-than-perfect performance in a number of wells in the Gulf of Mexico (GOM); in particular, it is not possible to keep the wells exactly vertical at times, impacting further hole sections drilling. To eliminate the issue, 55 bit runs with 26-in. RSS, performed from 2004 to 2010 in deepwater GOM, were studied using advanced drilling software to solve the cause of inclination build-up.
Analysis of statistics and of the models helped to conclude that, from 2004 to 2009, 84% of the runs were successful, 100% of the runs in 2010 and 2011 successfully helped keep absolute verticality. Recommendations to effectively kick off in the 26-in. section and build up to 20° inclination are given.
IADC/SPE 151133
Eliminating Stick-Slip by Managing Bit Depth of Cut and Minimizing Variable Torque in the Drill String, J. Davis, G.F. Smyth, N. Bolivar, Hibernia; P. Pastusek, ExxonMobil
This paper presents the results of applying depth-of-cut control and drill string design to eliminate stick-slip while drilling. Mechanical specific energy, vibration and penetration rate data will be presented over the course of five wells. Results indicate the managed depth of cut and increased torsional stiffness provided significant reductions in vibrations, leading to multiple field record rates of penetration, improved downhole tool life and reduced bit damage.
IADC/SPE 151556
Drill String Dynamics Simulation Optimizes Multilateral Casing Exit Windows, C.W. Guidry, R. Thomas, Baker Hughes
This paper describes an innovative casing exit milling bottomhole assembly (BHA) and the method by which its design and predicted performance were optimized using in-house drill string dynamics finite element analysis software. This analytical tool helped in designing the milling BHA so that its operational bending stresses were reduced and its fatigue life was increased. Purposefully designed shapes and placements of the BHA’s bladed cutting sections provided a favorable distribution of restraining forces, thus enabling an optimal length casing exit window.
IADC/SPE 151356
Understanding How the Placement of an Asymmetric Vibration Damping Tool within Drilling while Underreaming Assemblies can Influence Performance and Reliability, A.A. Kabbara, J.P. McCarthy, T. Burnett, I. Forster, National Oilwell Varco
This paper describes the work, on test rigs and full-scale rigs, carried out with respect to placement of an asymmetric vibration damping tool (AVDT) within drilling while underreaming operations.
To minimize eccentric wear and maximize drilling performance, the placement of the AVDT within the bottomhole assembly is critical. This paper describes how the placement of intermediate stabilizers between the AVDT and the underreamer can minimize eccentric wear to the underreamer and the adjacent drill string because of forward synchronous whirl induced by the AVDT.
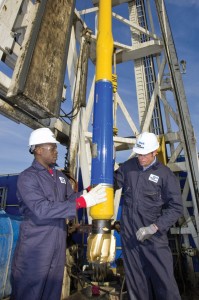
TECHNICAL SESSION 18: SHALE DRILLING METHODOLOGIES
IADC/SPE 151491
Potassium Silicate Treated Water-Based Fluid: An Effective Barrier to Instability in the Fayetteville Shale, B. Fritz, M. Jarrett, Halliburton
Both oil- and water-based fluids have been used to drill in the Fayetteville shale play with mixed results. Oil-based muds provide reliable inhibition and drilling performance, but environmental and economic concerns have generated interest in water-based alternatives.
This paper describes the technical process used to design, formulate and apply the customized potassium silicate treated water-based muds for use in the stressed Fayetteville shale play. Mineralogical analysis, microscopy studies and continuous improvement based on field observations are discussed.
IADC/SPE 151466
Using Advanced Drilling Technology to Enable Factory Drilling Concept in the Marcellus Shale, O. Hummes, P.R. Bond, A. Jones, W. Symons, M.K. Bishop, A.M. Serdy, S. Pokrovsky, Baker Hughes; N.A. Polito, Pennsylvania General Energy
In the Marcellus Shale in the northeastern US, operators are moving from a phase of exploration and appraisal of gas wells to the development phase using factory drilling techniques, which are reducing cost per well, increasing the number of wells that can be drilled and maximizing the production from the wells that are brought online. This paper describes how one operator teamed up with a service provider to adopt new technology that led to a drastic reduction in the operational time required to drill a complex 3D profile Marcellus-area well.
IADC/SPE 151752
Understanding Shale Heterogeneity: Key to Minimizing Drilling Problems in Horn River Basin (HRB), S. Khan, S.A. Ansari, H. Han, N. Khosravi, Schlumberger
In this paper, drilling problems experienced in 15 wells in two different areas of the HRB were examined. Some of these wells had severe wellbore instabilities due to high pore pressure, mud losses or lost circulation, tight hole/stuck pipe/pack off, or a combination of these events. Three bottomhole assemblies were lost in these wells, which required sidetracking. Most of these problems were experienced in Fort Simpson and upper Muskwa formations. An in-depth analysis of these wells indicated that shale heterogeneity was not properly characterized and anisotropic horizontal stresses were not considered in the pre-spud analysis, which resulted in incorrect mud weight predictions and trajectory calculations.
IADC/SPE 151175
A Systematic Approach to Improving Directional Drilling Tool Reliability in HPHT Horizontals in the Haynesville Shale, E.G. Pinto, J.F. Mota, Shell; J.L. Grable, D. Ward, Halliburton
This paper examines a systematic approach between a vendor and an operator to drive performance improvement while drilling the lower Haynesville production interval in northern Louisiana. The approach explores how root cause failure nalysis, new condition-based maintenance systems and novel field operations processes were utilized to push measurement while drilling, mud motor and logging-while-drilling performance in this hostile environment.
IADC/SPE 151131
Optimized Steerable Motor Design Overcomes Drilling Challenges in Marcellus Shale Unconventional Plays, A. Jones, A.A. Azizov, S.S. Janwadkar, W. Davila, J.A. Fabian, Baker Hughes; M.T. Nguyen, Range Resources
Although drilling horizontal wells in US land unconventional shale plays has increased exponentially in the last few years, maximizing well productivity and improving drilling efficiency remains a major challenge. This paper will discuss the design, modeling and results of horizontal type wells drilled using the short bit-to-bend steerable motor design in unconventional shale.
IADC/SPE 150971
Results of 25 January 2011 Shale Drilling Technology and Challenges Workshop, D.R. Torkay, Archer; J. Brakel, H. VanMarel, Shell; T. Geehan, Schlumberger; A.D. Shelton, D. Reid, National Oilwell Varco; M. Killalea, International Association of Drilling Contractors; K.A. Womer, KW Technology Services
This paper presents the results from a workshop on shale drilling technologies and challenges in Houston on 25 January 2011. The workshop, sponsored by the IADC Advanced Rig Technology Committee’s Future Technology Subcommittee, brought technology leaders and engineers together to discuss issues related to North American shale drilling. Led by specialists with operating, contracting and technology companies, the workshop goal was to educate the industry regarding existing technologies and challenges.
SESSION 1 E-POSTER:
IADC/SPE 151406
The Effects of Back Rake and Side Rake Angles on Mechanical Specific Energy of Single PDC Cutters with Selected Rocks at Varying Depth of Cuts and Confining Pressures, V. Rajabov, S.Z. Miska, M. Yu, E. Ozbayoglu, University of Tulsa; L. Mortimer, National Oilwell Varco
Polycrystalline diamond compact (PDC) bit design parameters, such as cutter back rake and side rake angles, are among major contributors to drilling efficiency, rate of penetration and durability of cutters. Experiments were carried out at in a single-cutter high-pressure testing facility at Tulsa University Drilling Research Projects. The results with more than 80 high-precision tests show that back rake and side rake angles have substantial effects on rock cutting efficiency and aggressiveness of PDC cutters. Low back rake angle produces higher cutting efficiency and requires the least amount of cutting force and torque in order to cut the same volume of rock. The results provide useful insights into the physics of cutter rock interaction and are valuable to PDC bit design to enhance rate of penetration and drilling efficiency.
SESSION 2 E-POSTERS:
IADC/SPE 151448
Improving Casing Wear Prediction and Mitigation Using a Statistically Based Model, S.B. Mitchell, WWT International; Y.L. Xiang, Pegasus Vertex
Casing wear models use the number of drill string revolutions and contact force between the drill pipe and casing to calculate wear. To improve the accuracy of casing wear models, an extensive database was created from a wide variety of wells with measured depths greater than 13,000 ft. The database results in a statistically based model for determining dogleg severity within vertical, build and tangent sections, as well as total drill string revolutions at various levels of confidence to bound average and maximum expected contact force and casing wear.
IADC/SPE 151212
Optimized Wellbore Design and Drilling Program Due to Advancement in Directional Drilling Technology, S. Pokrovsky, C.G. Small, M.E. Anderson, R. Flores, Baker Hughes; B.C. Knopp, Anadarko
The Eagle Ford Shale is currently the fastest-growing, most diverse unconventional shale play in the United States. It includes areas rich in oil, gas and gas condensate and has large variations in temperature, depth of producible zones, dips and fracturing. The authors will discuss the evolution of drilling operations in the Maverick Basin, located on the western side of the Eagle Ford.
SESSION 3 E-POSTERS:
IADC/SPE 151441
High-Confidence Vertical Positioning for Extended-Reach Wells, N.C. Mohammed, M.E. Terpening, Schlumberger
There is significant potential to improve extended-reach project risk profiles for asset management teams. We outline a methodology that leverages the capabilities of an advanced MWD/RSS system in combination with a dynamically updated SAG (systematic inclination misalignment) model. Results were corroborated initially with independent third-party surveys and later with a high-quality formation pressure while drilling data set from several wells drilled in a hydraulically continuous reservoir prior to production. The techniques described are a primary element of the thin reservoir targeting strategy for future development drilling in Sakhalin.
IADC/SPE 151274
Scaled Tortuosity Index: Quantification of Borehole Undulations in Terms of Hole Curvature, Clearance and Pipe Stiffness, S. Brands, R. Lowdon, Schlumberger
A Scaled Tortuosity Index is proposed that describes the total amount of required elastic energy to bend all the components in the string in all the required configurations to move it to TD. The index is linked to the nominal hole and casing size. This is a different concept from the existing Energy Index; it takes into account that actual hole curvature is not the curvature of the pipe in the hole (governed by stiffness and clearance). Putting tortuosity in the context of stiffness and clearance allows us to evaluate and compare boreholes with high and low frequency/amplitude borehole undulations in a meaningful way.
IADC/SPE 151283
PDC Bit Steerability Modeling and Testing for Push-the-Bit and Point-the-Bit RSS, S. Menand, C. Simon, J. Gaombalet, L. Macresy, DrillScan; L. Gerbaud, M. Ben Hamida, Paris Tech; Y. Amghar, Total; H.J. Denoix, Schlumberger; B. Cuillier, H. Sinardet, Varel
In both point-the-bit and push-the-bit rotary steerable systems, both tilt and side force are applied on the bit. There have been many discussion regarding the deviation mechanisms involved in these two systems. In response, a full-scale drilling bench was developed to test drill bits in push-the-bit, point-the-bit or hybrid push/point mode. This facility enables any coupled tilt side force on the bit to reproduce the RSS mechanisms. This paper is intended to show results of this experimental campaign.
SESSION 4 E-POSTERS:
IADC/SPE 150461
Modeling for MPD Operations with Experimental Validation, I.S. Landet, H. Mahdianfar, O.M. Aamo, Norwegian University of Science and Technology; A. Pavlov, Statoil
Heave motion of floating rigs complicates the control of pressure in managed pressure drilling (MPD). During connections, the drill string is detached from the drawworks and moves with the heaving rig, causing downhole pressure fluctuations. As a step toward designing control schemes to actively attenuate the fluctuations, a fit-for-purpose mathematical model of well hydraulics is derived based on a finite volumes discretization. The contributions of this paper enable development of control systems for automated MPD operations from floaters.
IADC/SPE 151130
Uncertainty Quantification of Real-Time Pore Pressure Models Caused by Normal Compaction Trend Line Setting, A. Bartetzko, S. Wessling, P. Tesch, U. Lautenschlueger, L.J. Andonof, D. Broadhead, Baker Hughes
This paper highlights uncertainty sources associated with the basic stages in pore pressure modeling. Furthermore, filtering of the data prior to trend-line definition may add uncertainty. The uncertainty in pore pressure introduced by the modeling stages is demonstrated on an example data set from an offshore well.
IADC/SPE 151034
Performance Evaluation of a New Transient Two-Phase Flow Model, J. Li, M.A. Teixeira, P. Salim, Baker Hughes; Y. Fan, ConocoPhillips
In this paper, a new simplified transient two-phase flow model has been developed. In each time step, the two-phase flow regime, liquid holdup and pressure gradient are estimated with the empirical correlations, which are well developed for the steady state flow. A drift flux equation was also introduced to close the system. The model and algorithm were validated against data collected from the public literature, field operations and other transient software. The benefits of using the transient simulation for the operational design, training and job execution will be discussed.
SESSION 5 E-POSTER:
IADC/SPE 151798
Properties of Filter Cake of Water-Based Drilling Fluid Under Dynamic Conditions Using Computer Tomography, S. Elkatatny, H.A. Nasr-El-Din, Texas A&M University
Heterogeneity of the filter cake plays a key role in the design of chemical treatments needed to remove the filter cake. Extensive lab studies were conducted to measure the filter cake thickness and porosity of 69 pcf water-based drilling fluid using computed tomography (CT) scanner and develop a relationship between the porosity and the permeability of the filter cake.
Using CT for the first time allowed us to evaluate existing models to predict porosity permeability relationships of the filter cake.
SESSION 6 E-POSTERS:
IADC/SPE 150232
Exploration to Production in Two Years: A Contracting Strategy Case Study, V. Passos, OGX; G. McCallum, S. Dubey, G. Lindsay, Schlumberger
An independent Brazilian oil and gas company acquired 21 exploration blocks in November 2007 and increased its portfolio to 29 blocks by March 2009. The challenge of exploiting the blocks was achieved by setting ambitious, time-bound exploration and production goals. The company chose an outsourcing strategy pillared on project management and worked wherever appropriate to minimize the number of contractors.
This paper looks at how this strategy allowed the company to achieve its goals.
IADC/SPE 149906
Advanced Pre-drill Simulations for Safer and More Cost-effective Drilling, D. Sui, T. Gulsrud, E. Kristoffersen, SINTEF Petroleum Research
We have developed an advanced technical method for the evaluation of planned drilling operations with respect to equivalent circulation density, temperature, pore pressure, well stability and torque and drag. The methodology provides an extensive analysis and recommendations based on simulation results. This will contribute to increased safety, reduced risk and reduced costs. The performance of the methodology is demonstrated using data from a North Sea well.
SESSION 7 E-POSTERS:
IADC/SPE 150347
Milling Low-Side Casing Exit Windows in Horizontal Wells: A Case Study, C. Hogg, R. Barker, J.C. Valverde Penangos, R. Caceres Leon, Weatherford; C.A. Gandara, E. Ortiz Prada, P.A. Gil Chipatecua, H. Rueda, Hocol
This paper details a successful re-entry sidetracking and drilling operation in Colombia’s Puerto Gaitan area. To economically reach this new reservoir zone, the casing exit was constructed on the low side of the existing wellbore’s horizontal casing section. Such low side exits are rare due to concerns about interference between the whipstock and drilling assemblies. Additionally, the desire to drill with a rotary steerable system made it imperative that a casing exit be created, which minimized bending stresses on the drill string through the window, therefore increasing drill string longevity.
IADC/SPE 150027
New Tools and Procedures Increase Reliability of Open-Hole Sidetrack Operations, C.H. Dewey, S.N. Swadi, J. Campbell, P. Desai, Schlumberger
A recent research and development effort has identified a new method and associated tools that can be effectively utilized to increase operational reliability in open-hole sidetracking and to save costs in terms of time and materials. The paper outlines mechanical and operational features of various systems along with their respective field performances. The authors will describe field run challenges, how those were overcome, the lesson learned and potential system modifications.
IADC/SPE 149755
Can You Protect Your Motor without Sacrificing Performance? B. Guidroz, S. Barton, National Oilwell Varco
Balancing the performance and longevity of drilling motors is a constant struggle. Operating above recommended parameters delivers higher rates of penetration but can be too aggressive, causing accelerated component wear and premature failure. Conservative operation decreases the component wear but can be detrimental to drilling performance. A novel approach to controlling motor performance allows operators to operate at specified limits while preventing spikes that damage motors. Field testing of the device has resulted in a significant reduction in motor component damage.
SESSION 8 E-POSTERS:
IADC/SPE 151378
Multilateral History – Deepest Level 4 Cemented Junction Installation, A.W. Hua, T.X. Qing, Y.X. Tong, B.D. Xiang, Tarim Oilfield; C.B. Ponton, J.M. Roberts, D.G. Durst, Halliburton
An operator was challenged with increasing production efficiencies from new single wellbores in the deep Tarim Basin reservoirs of China. To optimize production, multilateral drilling and completion technology were implemented on a pilot well.
This project is the first multilateral installation for this client; it was the first cemented Level 4 multilateral in China and is the deepest Level 4 multilateral installed worldwide. This paper describes the objectives, challenges, best practices, contingencies, logistical issues, results and lessons learned from the implementation of this deep set multilateral technology.
IADC/SPE 151023
Optimized Pumping Design Brings Expressive Cost Reduction for Offshore Open-Hole Gravel Pack Operations, J.V. Magalhaes, R.A. Leal, M.V. Ferreira, A.L. Martins, R.P. Santos, A. Calderon, D.N. e Silva, Petrobras; B. Simoes, D. Miranda, D.P. Barbosa, M.J. Hunes, Halliburton
Sand control is a major issue for offshore unconsolidated sandstone reservoirs, where any workover or production interruption is associated with high costs. Horizontal well open-hole gravel packs proved to be a reliable strategy to prevent sand production in the prolific offshore Brazil fields. More than 250 operations were performed in different critical scenarios, such as ultra-deepwater wells, long horizontals and in the presence of shale interlayers.
Pushed by fluctuations in oil production revenues and aware of the expressive costs related to gravel pumping operations, Petrobras started a broad research and field test strategy to reduce operational times and costs. This article details both aspects of the development.
SESSION 9 E-POSTERS:
IADC/SPE 151180
Automation Improves Shaker Performance, K. El Dhorry, B. Dufilho, National Oilwell Varco
One limitation of current shale shakers is their performance can be negatively impacted by changes in feed rate. Standard shakers operate with vibratory motors running at a constant speed, yielding a constant output force. This results in a shaker having its peak g force during non-loaded conditions. As soon as drilling fluid is added to the system, the acceleration decreases and so does the shaker performance.
Results, observations and testing methods from more than two years of testing and operations will be presented.
IADC/SPE 151204
Collaborating on Real-Time Geomechanics Across Organizational Boundaries, L. Magini, F. Zausa, Eni; D. Molteni, N. Fardin, W.A. Pausin, Schlumberger
This paper describes the application of real-time geomechanics to a remote exploration project in a challenging field and how operations benefited from this technique. The stakeholders were based in four locations: rig site, operator’s office, operator’s real-time center and service company’s real-time center. Interaction among stakeholders was coordinated via the operator and service company real-time centers; the use of available infrastructure and remote collaboration software created a collaborative environment.
SESSION 10 E-POSTER:
IADC/SPE 151331
A New, Alternative Weight Material for Drilling Fluids, M. Al-bagoury, C.D. Steele, Elkem Materials
This paper describes a micronized weighting agent suitable for use in drilling, completion and cementing fluids that offers advantages in the control of equivalent circulating density, sag and formation damage.
SESSION 11 E-POSTER:
IADC/SPE 151254
Analytical Model to Predict the Effect of Pipe Friction on Downhole Temperatures for Extended Reach Drilling, A. Kumar, A. Singh, University of Houston; R. Samuel, Halliburton
This paper will present the derivations of the generalized heat transfer model and the application of the model in a field case. The temperatures of the drill string and drilling fluid were calculated at various depths for the considered well profile.
SESSION 12 E-POSTERS:
IADC/SPE 151407
Effective Force and True Force: What are They? R. Samuel, Halliburton; A. Kumar, University of Houston
This paper provides the mathematical treatise and discusses the theoretical basis of effective force and true force and how they are used in torque, drag, buckling, stress and limit calculations. This paper describes the details, apparent definition, pitfalls and context that these forces can be used.
IADC/SPE 149898
Sophisticated Software Analysis System and Use of Torque/Drag Modeling for Complex Well Operations Increases Operational Efficiency, L. Xie, D.P. Moran, L. Yan, J. Mercado, Schlumberger
The authors will discuss new modeling software capable of analyzing complex well operations, including liner hanger and jarring operations in detail.
SESSION 13 E-POSTER:
IADC/SPE 151482
The Best Driller in the Gulf of Mexico, R. Griffon, J.P. Gauthier, Schlumberger
An analysis of more than 100 Gulf of Mexico deepwater wells reveals that one operator is experiencing more drilling success than its peers in terms of consistent and repeatable top-quartile drilling performance. These results are driven by a commitment to the operator’s drilling philosophy, a strong partnership with key service contractors, and a core drilling team of experienced and technically sound professionals.
Editor’s note: The abstracts have been edited for space. The list of papers is current as of 31 December 2011. Paper additions or withdrawls after this date may not be reflected.