Wirelines
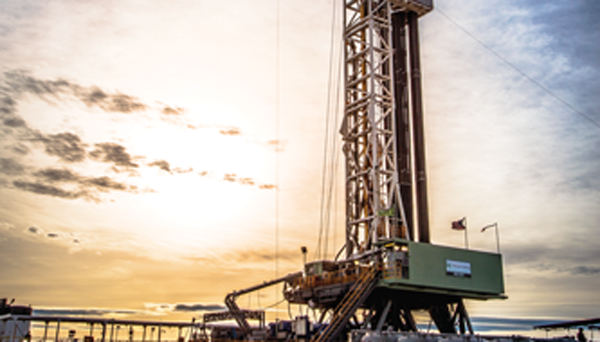
BSEE proposes revised well control rule
On 11 May, the US Bureau of Safety and Environmental Enforcement (BSEE) published its proposed rule, Oil and Gas and Sulfur Operations in the Outer Continental Shelf – Blowout Preventer Systems and Well Control Revisions. This most recent version addresses concerns raised by stakeholders after the rule was initially introduced on 28 July 2016.
Most notably, this proposal intends to:
• Revise certain submittal requirements;
• Clarify drilling margin requirements;
• Remove references to lifeboats;
• Remove certain prescriptive requirements for real-time monitoring;
• Replace the BAVO requirement with use of third party;
• Revise accumulator system requirements; and
• Revise control station and pod testing schedules.
In response to the proposed rule revisions, IADC President Jason McFarland said, “Since the rule was first issued, IADC and its members have strongly asserted the need to reconsider certain provisions that we believe are overly prescriptive, do not enhance safety of operations and in some cases increase, rather than decrease, risk. We are optimistic that BSEE has listened to input from all stakeholders and incorporated that feedback into the revised proposed rule.”
Click here to access BSEE’s latest well control rule.
SafeOCS releases 2017 annual report
SafeOCS recently issued its 2017 Annual Report on Oil and Gas Production Safety System Events. The SafeOCS program is a resource for industry members to share key observations and lessons from equipment- and safety-related events and is administered by the US Bureau of Transportation Statistics (BTS). Its objective is to identify potential high-consequence risks from aggregated, industrywide data and share findings to mitigate risks. BTS began collecting data on equipment component failures in December 2016.
In 2017, the first full year of mandated Safety & Pollution Prevention Equipment (SPPE) incident reporting, nine of 59 production operators in the Gulf of Mexico reported 112 failures. The remaining 50 operators did not report any failures.
Click here to access the new SafeOCS report.
IADC meets with USCG, NIST and US Senate to discuss cybersecurity challenges
On 4 April, representatives of the IADC Cybersecurity Committee met with the US Coast Guard (USCG) and the National Institute of Standards and Technology (NIST) in Washington, DC. Committee Chairwoman Siv Hilde Houmb with Secure-NOK; Melissa Mejias, IADC Legislative Analyst; and Sean Plankey with BP met with the groups to discuss the IADC Guidelines for Baseline Cybersecurity for Drilling Assets.
While in Washington, DC, the group also met with the Senate Commerce, Science and Transportation Committee to discuss S.2083: Strengthening Cybersecurity Information Sharing and Coordination in our Ports Act of 2017.
APPEA publishes 2018 edition of key statistics
The Australian Petroleum Production and Exploration Association (APPEA) recently released its 2018 edition of Key Statistics. Information provided in the report includes a consideration of supply and demand, economic contributions of industry, capital investment facts and safety performance statistics.
Click here to access the APPEA report.
US Interior: No lower offshore royalty rates
In April, US Secretary of the Interior Ryan Zinke announced that his department will not lower royalty rates for future offshore oil and gas lease sales. On 28 February, the Royalty Policy Committee had made its initial recommendations, including one to set a royalty rate of 12.5% on all Outer Continental Shelf lease sales at all water depths through 2024. However, an improving economy, federal tax reforms and higher energy prices, along with greater regulatory certainty, have led to positive market conditions, all of which influences the decision to keep the royalty rate in 200 m of water and deeper at the current 18.75%.
Brazil’s ANP approves revised local content rules
Brazil’s National Agency of Petroleum, Natural Gas and Biofuels (ANP) recently approved lower requirements for the use of locally produced goods and services in oil field development. While onshore oil and gas projects require 50% “local content” goods and services, offshore activities and equipment will require 18% for exploration; 25% for well construction and 40% for subsea systems and 40% local content for stationary production units.
Operators have expressed a preference for this revised, more certain scheme. As such, operators will be allowed to transition from concession contracts to the new scheme.
OPITO reports on future of UK oil and gas workforce
OPITO, in partnership with Robert Gordon University’s Oil and Gas Institute, recently released the UKCS Workforce Dynamics Review. The review assesses the changing skills requirements for the industry over the next 20 years.
The research indicates that more than 40,000 new workers will need to be recruited over the next 20 years, which would include 10,000 positions not yet currently in existence. Other findings in the report project that 80,000 workers will likely retire or leave the industry by 2035.