UK CMA clears Shelf Drilling’s acquisition of five jackups from Noble Corp
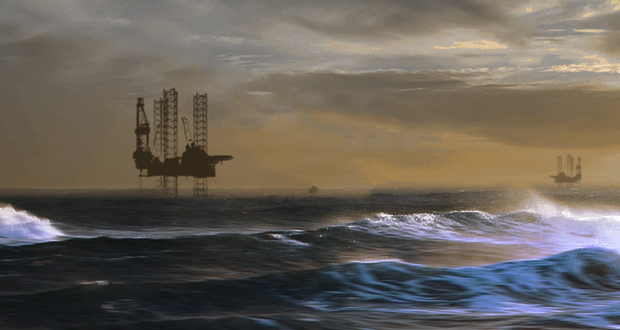
The UK Competition and Markets Authority (CMA) has cleared Shelf Drilling’s asset purchase agreement for five jackups from various subsidiaries of Noble Corp for $375 million. The CMA’s decision came as part of its acceptance of legally binding undertaking from Noble and Maersk Drilling in relation to the merger between the two companies announced in November 2021. As part fo that deal, Noble was required to divest five jackups – the Noble Hans Deul, Noble Sam Hartley, Noble Sam Turner, Noble Houston Colbert and Noble Lloyd Noble and released offshore and onshore personnel.
Completion of the rig purchase agreement remains subject to certain conditions, including the. completion of the merger and certain other customary conditions. Closing of the acquisition is expected to take place in October 2022.