Simulation verification plays key role in success of Aasta Hansteen dual barge floatover operation
Unique turnbuckles, communications protocol had to be developed for installation of 24,300-ton topside onto spar hull
By Karen Boman, Associate Editor
Maritime service firm Boskalis set a company record last year with the transport of the cylindrical spar hull for the production platform on Equinor’s Aasta Hansteen field development project in Norway. The two-month journey started in April 2017 at the Hyundai Heavy Industries shipyard in Ulsan, South Korea, and ended in June at an inshore discharge location near Hoylandsbygd, covering 14,500 nautical miles. Weighing 46,000 tons and standing 200 m high and 50 m wide, the spar hull towers well above the Leaning Tower of Pisa and the Statue of Liberty and is nearly as tall as the Eiffel Tower in Paris.
Later that same year, Boskalis set another company record in this project by conducting the company’s largest-ever dual barge floatover to install the production platform’s 24,300-ton topside onto the spar hull.
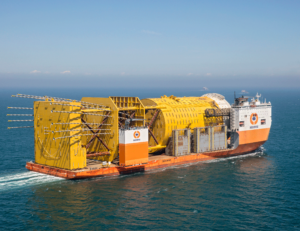
The company had transported the spar hull horizontally on the Dockwise Vanguard vessel, then moved the Aasta Hansteen topside from Hyundai’s yard to Norway onboard the Dockwise White Marlin vessel. Once the White Marlin arrived in Norway on 30 November 2017, the topside was transferred to two S-class vessels by positioning the vessels on either side of the White Marlin. The two S-class vessels started un-ballasting while the White Marlin ballasted down and maneuvered out from underneath, creating a catamaran structure with the topside linking the two hulls. The catamaran structure was then towed out to the vertical spar hull, where the mating was completed early on the morning of 11 December.
Boskalis also broke new ground with Aasta Hansteen, the deepest oil and gas development to date on the Norwegian Continental Shelf, by verifying the dual floatover engineering plan entirely through operation simulation, said Bas Polkamp, Project Director for Aasta Hansteen. The company typically uses third parties or internal “cold eye reviews” to verify parts of engineering. However, for this project, the company conducted a simulation of the exercise with the project engineering and operations teams. For the simulation, multiple five-day sessions were undertaken at Maritime Research Institute Netherlands (MARIN) in a two-year time frame.
Engineers and operations groups had typically worked separately on such engineering projects. “Engineers are still doing a lot of work in the office, and they normally just hand everything over to operations,” Mr Polkamp said. But what may work on paper may not actually work in real life. Working together at MARIN allowed the company to bridge the gap between two separate worlds, enabling more effective verification of the design.
The extent of the simulation scope used for this project was a first for the company and for industry, according to Mr Polkamp, who noted that the simulation exercises also helped to optimize team-building.
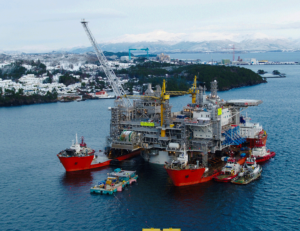
Initially, the plan for the floatover was to use mating-mooring wires between the submerged substructure and dual barge plus topside, to mate the topside with the substructure in a controlled manner. “During several simulation runs, it became clear we were not able to stabilize the substructure and dual barge this way, so we had to leave our base case and engineer out the connecting wires. Ultimately, after a set of risk sessions, we decided to deploy tugs only to maneuver the dual barge with topside over the substructure. By having the tugs rigidly connected to the dual barge, it appeared in the simulation that we had good control of the marine spread.”
The company had to engineer and fabricate 16 turnbuckles – each weighing more than 3 metric tons and measuring nearly 8 m in length, and with a working load limit of 603 metric tons – to establish an adjustable connection between the dual barge and the topside. Turnbuckles, which are tubes that can be adjusted in length, are not typical equipment used for sea-fastening topsides to a dual barge. Boskalis had to create this solution from scratch, Mr Polkamp explained.
Because dual barge floatover projects don’t take place frequently, the company had to create these buckles without clear and specific classification rules on how to support and sea-fasten huge cargoes on a dual barge. The turnbuckle fabricator, Netherlands-based Ropeblock, also had never manufactured a turnbuckle of this size before.
To account for the size of Aasta Hansteen, the company had to reconfigure the design of the shock-absorbing units it had used for the 2005 Corocoro dual barge floatover project, in which the company installed a 3,500-metric ton topside offshore Venezuela.
Due to the large number of parties involved in the project – operations managers, tow masters, superintendents, winch operators, local pilots, barge captains, tug captains, ballast engineers – Boskalis had to establish a unique communication protocol for the different operational steps, particularly during simultaneous operations, such as ballasting three vessels at the same time during topside transfer from the transport vessel to dual barge, or instructing five tugs during the mating operations, Mr Polkamp said.
Despite all the challenges, Boskalis recorded no lost-time incidents for the more than 100,000 manhours spent on the project, from Boskalis’ initial participation on the front-end engineering process in mid-2012 to completion of the floatover in December 2017.
Named for Aasta Hansteen, a pioneer of the 19th-century women’s right movement in Norway, the Aasta Hansteen field will be home to Norway’s first production spar, which will produce gas via subsea templates. The spar platform arrived at the Aasta Hansteen field in the Norwegian Sea on 23 April after a 12-day, 500-nautical mile tow-out from Stord, Norway. Production is expected to come on stream later this year. DC
Click here to watch a video of the Aasta Hansteen dual barge floatover project