SEMS rule marks new beginning in environmental, safety practices
By Joanne Liou, editorial coordinator
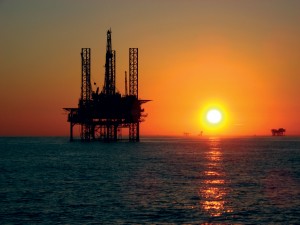
HOUSTON – Facing an impending deadline, companies from all corners of the industry capitalized on an unprecedented opportunity to help themselves reach a shared goal: to facilitate the safest and most environmentally sound workplace while mitigating the potential dangers inherent to drilling operations.
The US Bureau of Ocean Energy Management, Regulation and Enforcement (BOEMRE) – recently replaced by the Bureau of Safety and Environmental Enforcement (BSEE) – announced in October 2010 mandatory practices required to operate on the US Outer Continental Shelf (OCS). The 15 November 2011 deadline gave the industry little more than a year to complete what initially seemed like an insurmountable task: comply with BOEMRE’s call to implement a mandatory safety and environmental management system (SEMS), a program that operators are required to develop and maintain with the cooperation of contractors and other third-party service providers.
Although the use of a safety and environmental management system is not a new idea, the regulatory mandate sent waves through the industry; the considerable task was going to require more than a revision in protocols. “SEMS had its first place in the Gulf of Mexico as API RP 75 (SEMP) in the early ’90s. It was a voluntary program at that time,” Bill Walker, HSSE adviser at Cobalt International Energy, said. “The concept is not radical or new.”
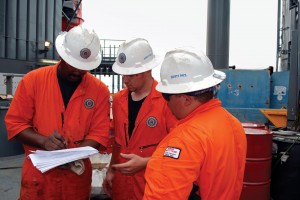
With the support of the Offshore Operators Committee (OOC), the Center for Offshore Safety (COS) and IADC, in conjunction with leaders from oil and gas companies, drilling contractors and other contractor companies, the industry united to create a thoroughly SEMS-compliant environment. A collaborative effort was forged to create a SEMS toolkit to advance E&P activities on the OCS. “With the lessons that we have learned from the offshore disasters, we will continue to make a difference in safety,” Jack Isbell, safety specialist at Rowan Companies, said. He participated in the SEMS Taskforce Competence Subcommittee and in developing the SEMS Compliance Readiness Worksheet. “The SEMS is an effective method for making that difference. It’s a more systematic way to work safely and protect the environment, and when you have a lot of very complex systems working, that systematic method is necessary.”
The implementation process cultivated not only the collaboration of various departments within each company but also among competitors. An expansive task force emerged from a modest meeting of seven people from different companies in February, but without a sponsor. At a second meeting in March, the OOC stepped up to sponsor the group, which then facilitated a number of meetings and the formation of subcommittees addressing different aspects of SEMS implementation. By June, about 150 people from all facets of the industry were participating on the OOC SEMS Taskforce, which went on to create the SEMS Toolkit.
The introduction of SEMS regulations to the US OCS is a process that is still unfolding. Implementation of a SEMS program was just one major variable that operators and contractors had to overcome; moreover, the industry is subject to government interpretation and revisions of the regulation, which could call for further cooperation within a highly competitive industry.
On top of that, the recently proposed SEMS II, which modifies and adds to the current regulation, will create its own challenges. Among other things, the new proposal calls for: mandatory third-party audits, providing all workers with stop work authority, documenting employee participation in SEMS development, formal approval of all job safety analyses, designation of an individual having “ultimate work authority” and guidelines to report of unsafe working conditions. The comment period on the proposed rule closes 14 November, and a final rule isn’t expected until spring 2012 or later.
What is SEMS?
In 1994, the then-Minerals Management Service (MMS) recognized API RP 75 to fulfill the principles of a safety and environmental management program. Oil and gas companies operating on the OCS were encouraged to voluntarily adopt the recommended practice, which was intended to reduce the risk and occurrence of accidents and pollution on offshore oil and gas drilling and production facilities. Regulators identified four elements of the original 12 elements of RP 75 that were necessary in an effective program, based on incident investigations and performance reviews with operators.
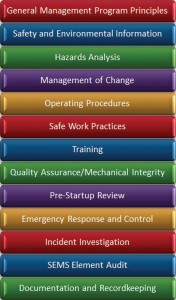
In 2009, the then-MMS proposed a rule to mandate that leaseholder/operator management systems include those four elements: hazard analysis, management of change, operating procedures and mechanical integrity. “Prior to 2010, BOEMRE looked at regulating four of the now-13 requirements,” said IADC industry compliance specialist Julia Swindle, who has been participating in the development of the SEMS Toolkit under the OOC SEMS Taskforce. “Then Macondo happened, and now they’re including all 13,” she said. An additional section was added to the original 12 elements to address the responsibilities of companies’ general management.
The October 2010 SEMS final rule, which includes API RP 75’s 12 sections, applies to current and future OCS operations and facilities under BSEE’s jurisdiction, including drilling, production, construction, well workover, well completion and well servicing. BSEE and the Bureau of Ocean Energy Management (BOEM) replaced BOEMRE on 1 October.
Operators are responsible for having a SEMS in place, and contractors need to be prepared to respond. “Although contractors are not required to have a SEMS for their own operations, their cooperation is necessary for operators to be in compliance; therefore, it is in contractors’ best interest to anticipate operators’ needs and proactively cooperate with operators,” Dr Brenda Kelly, IADC senior director of accreditation and certification, explained. Dr Kelly leads the SEMS Competence Subcommittee under the OOC SEMS Taskforce. Under the final rule, each operator needs a written agreement with each contractor they are working with to document safety and environmental policies and practices.
“Part of the challenge is that although operators must comply with the BSEE regulations, they can interpret how to satisfy them. A contractor must be prepared to follow the operator’s SEMS program,” Dr Kelly said. One benefit of SEMS is that all companies will be held to the same minimum standard, Ms Swindle added. “It is a system that will hold all lessee/operators and, by default, contractors on the OCS to the same requirements and level the playing field,” Ms Swindle said.
IADC HSE Case Guidelines
Recognizing that many members had based their SEMS on the management system guidance provided in the IADC HSE Case Guidelines for MODUs, IADC performed a gap analysis of the guidelines against API RP 75 and the BOEMRE Final Rule.
The results of the gap analysis were made available to members in early 2011, according to Alan Spackman, IADC vice president – offshore technical and regulatory affairs. “The analysis found only minor gaps,” Mr Spackman said, “and these were formally closed with the adoption of amendments to the HSE Case Guidelines for MODUs in October 2011.
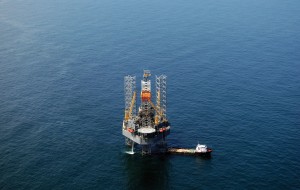
Implementation
Some contractors initially reacted to BOEMRE’s announcement in October 2010 with a wait-and-see approach. However, some also found that their existing safety and environmental management programs paralleled the new regulations. “Having had a SEMS for a number of years and, at the time, being in the process of revising it to meet stricter safety standards, I felt that we were in a good place,” Mr Isbell said.
Jennifer May, director corporate HSE and management system for Hercules Offshore, expressed a similar sentiment and noted that Hercules has had a safety and environmental management system in place since 2007. “We did a gap analysis, and we were very fortunate to find we didn’t have very many gaps,” Ms May, who is a member of the SEMS Taskforce Contractor Guidance Subcommittee, said. “What it has brought to the surface is the execution piece. On paper, people have great systems, great policies, but it’s getting those policies into the hands of the rig crews and getting them to embrace it and use it. That’s the struggle.”
Translating a policy into everyday practice entailed significant time and resources over the past year. “Our engineering department has had a team working on SEMS. Our operations department has a compliance team working on SEMS. HR, training, all the departments that make this company operate have had dedicated personnel on the SEMS implementation,” Ms May said. While the interpretation of the regulation began to take shape through discussions and drafted policies, contractors and operators continued the implementation process through practice and execution in the form of training sessions. “We’ve spent a lot of face time with the rig crews,” she added.
Rowan hosted two SEMS-specific training sessions at Houston’s Hotel Derek in October, specifically for rig supervisors, offshore installation managers, engineers and HSE technicians. “The management system can be that transfer of experience and understanding that can be done off-site. Are we going to be able to slip and cut drill line at a hotel? Not quite, but we can ensure that they understand how the new rule and its intent will make their rig a safer place,” Mr Isbell said. “They will be able to take the information and apply that logic and understanding to the individual jobs and to the task of slip and cut drill lines.”
Rowan also conducted on-site training on rigs, and training courses for new-hires are being revised to take SEMS into account.
Mr Isbell pointed to the necessity of supervisors’ leadership in building support for and compliance with SEMS. “As great as a training or class may be, the key to the proper use of the management system will be in our supervisors and their continued support of the SEMS,” he said.
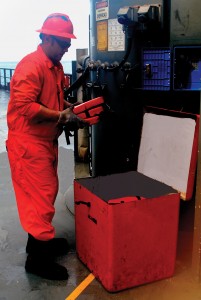
Operators’ involvement
While contractors have a sense of the general requirements that are necessary for compliance, operators’ requirements can vary. Fortunately, Rowan has encountered some common ground among its customers. “(Operators) have been fairly uniform with the requirements and expectations. I think that we have the work of the API, the OOC and IADC to thank for making sure that, of 10 different operators, there are not 10 different sets of expectations,” Mr Isbell said.
Communication also has been a constant key to success in SEMS implementation. “The relationship between the operator, the service contractor and the drilling contractor requires a lot of communication, and SEMS just underscores that and brought it to the surface in the form of a regulation,” Mr Walker noted.
Although the SEMS Taskforce initiative began with operators, they realized that compliance would require cooperation from their contractors. “When the group got together, it was a group of operators,” Ms Swindle said, “but they realized that this was a bigger challenge that would require the cooperation of the contract companies that they work with and that, they being responsible (to meet the requirements), needed to help provide guidance for the drilling contractors.”
The SEMS Taskforce brought together leaders from supermajors and other independent operators: Anadarko Petroleum, BHP Billiton, Chevron, Cobalt and ExxonMobil, as well as from the contractor community, such as Ensco, Hercules, Noble Corp, Rowan and Transocean. Baker Hughes also contributed to the toolkit.
Mr Walker, who chaired the Documents and Data Subcommittee, noted the benefit of the joint effort. “The more conformity we can bring to the process, the less work and expenses will be associated with the contractor providing information,” he said. “We worked on safety questionnaires, letters of agreement, and we’re working on other areas where we can make this a more efficient transfer of information or communication between the operator and drilling contractor.”
Most of the toolkit is geared to aid drilling contractors. “The SEMS toolkit was developed as a cooperative effort with over 50 different companies from all different sectors of the oil and gas industry,” Ms Swindle, who helped compose the compliance readiness worksheet, said. “A lot of really smart people contributed to that effort.”
Subcommittees within the taskforce created worksheets, templates and guides ranging from SEMS audit protocol and training matrices to documentation worksheets and agreement letter templates. The extensive toolkit, which also includes PowerPoint presentations and a list of definitions with examples, is available for free on IADC’s website at www.iadc.org.
The operators’ involvement in the taskforce has created cohesiveness in the industrywide effort and sets a foundation for continual improvement. “It is a continual implementation and audit process that they’re engaged in,” Mr Isbell said. “They are being very cooperative in saying ‘let’s make sure we have all the requirements met, and how can we go above and beyond the minimal requirements and exceed expectations?’ “
In conjunction with drilling contractors’ SEMS training, Cobalt is also implementing a program for anyone – employees, contractors or visitors – to complete a SEMS orientation conducted by Cobalt rig personnel and HSE advisers. The goal is to make everyone “aware of how SEMS is impacting our day-to-day activities on the rig,” Mr Walker said.
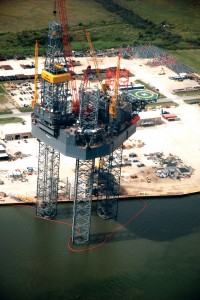
Effects/outlook of SEMS
Embarking on a SEMS-compliant industry, the path remains bumpy for all parties involved. Although many contractors and operators began compliance efforts more than a year ago, “nobody can guarantee they will be in compliance” until BSEE performs an audit, Ms Swindle stated. “BOEMRE made it clear that they want to use auditors that do not have any conflicts of interest, but it seems the only way to do that may be to go outside of the industry. It’s going to be a huge learning curve for everybody.”
Mr Walker agreed that challenges might surface from BSEE’s interpretation of the SEMS language. “Our approach is to do our due diligence to implement, to the best of our abilities, all of SEMS, and then as we receive guidance, we will make accommodations for any changes that may be needed,” he said.
Some contractors remain optimistic in overcoming obstacles and in maintaining a joint effort with operators. “We will take any cases, where shortcomings have been identified, as opportunities to grow, revise, implement and evaluate changes to improve our management system,” Mr Isbell said. “There are going to be some growing pains.”
Because many contractors and operators who operate on the OCS also operate in other drilling markets, the lessons learned from mandatory SEMS implementation in the US are making their way around the world. “Our management system that’s compliant to SEMS is already corporation-wide,” Ms May said, putting SEMS into play onshore the US and on Hercules’ rigs in the Middle East, Africa and Southeast Asia. “For consistency sake, it’s better to have one management system that meets industry best practice.” Rowan also uses SEMS through all operations, including on rigs in the Middle East, Southeast Asia and the North Sea.
Cobalt’s SEMS-compliant HSE management system is also global. “The only caveat is if we are working in a part of the world where, for whatever reasons, regulatory or logistically, there’s some part of our HSE management system that cannot be directly applied,” Mr Walker said. “We might have to make some adjustments to it, but we will not in any case work in a downgraded situation.”
For companies based outside the US or not operating on the US OCS, some industry leaders foresee SEMS or similar programs becoming a reality for them as well. “I am fairly confident that the companies that operate in those regions will have adopted either the requirements that you see here in the Gulf of Mexico or some very similar,” Mr Isbell said. “It’s been said that ‘as goes the Gulf of Mexico, so goes the rest of the industry.’ A lot of that is because the Gulf of Mexico is an excellent training ground and excellent place for development of leadership.”
Future construction of rigs might also take into consideration the SEMS-compliant environments in which they will enter. Rowan’s construction of the Joe Douglas jackup was under way as the company was in the process of implementing SEMS. Given the company’s initial system that was largely already compliant with SEMS, the jackup did not face additional hurdles, but the contractor did move up some parts of the SEMS process.
“We needed to request certain inspections or certifications sooner, whereas we might have been able to have waited until ‘X’ number of months before the rig went to work to request a certain inspection or certification,” Mr Isbell said. “It helped us to be more prepared, and be more prepared earlier.”
The driving forces behind SEMS implementation can be traced back to the priorities of the program: human life and the environment. While it is not possible to quantify the value of the program, SEMS is intended to promote a high-quality workplace to avoid accidents that could result in injuries to personnel and environmental consequences. “If (SEMS) is utilized, it can’t help but have a positive difference on the rig, and you will see it. It’s a trickle-down effect,” Ms May said. “You’ll see efficiencies such as higher productivity, less downtime, overall quality, less property damage and fewer incidents because people are using it.”
Conclusion
An event of alarming magnitude might instigate the establishment of preventive measures, but the utilization of those practices is just as important. “The most significant regulatory change in our industry has been from Piper Alpha and now Macondo,” Ms May said. “However, legislation in and of itself is not the complete answer. We must consistently and persistently do the things that we say we are going to do as provided in a management system to ensure incident-free operations.”
Legislation and, more importantly, the industry’s united front are transforming the drilling environment into a safer one. “I think the participation that we had (in the SEMS Taskforce) was excellent and really precedent-setting for this industry. This is a very competitive industry, and a lot of companies are careful to maintain what they consider to be their competitive edge,” Ms Swindle said.
The deadline to implement SEMS might come and go without much fanfare, but the date marks the beginning of a new era for the industry. “15 November will be the first day of a new era in safety and environmental management in the Gulf of Mexico and other places under BOEM jurisdiction,” Mr Isbell said. “It’s a new era in safety and protection of the environment.”
Rowan Companies’ Jack Isbell and IADC’s Brenda Kelly and Julia Swindle address industry challenges and initiatives related to the SEMS regulations in exclusive video interviews with DC.