Selective standardization approach could help industry sidestep market barriers, achieve full automation
Competition, supply chain complexity make it difficult to collaborate on automation, but selective standardization provides advantages to all players
By Ekaterina Minyaeva, OTM Consulting
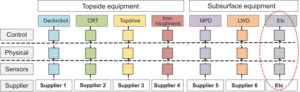
Drilling standardization, collaboration and automation have become major buzzwords in the industry in recent years, promising higher reliability, improved safety, increased efficiency and decreased costs. Due to the complexity associated with the automation of rig floor equipment, however, full automation of processes and equipment will not be possible until there is a higher level of collaboration and standardization.
Despite the vast majority of industry representatives actively supporting and promoting the notion of collaboration and standardization, including standardization of rig floor layout and equipment, the practicalities make it challenging to achieve. The drilling industry is highly competitive and has a very complex supply chain. Although there is a clear “need” and “want” for collaboration, to date it has been largely elusive.
But is drilling automation really critical or is the industry automating just for the sake of it? Drilling automation is primarily driven by three critical industry challenges: efficiency, cost reduction and reliability. It also addresses operational aspects, such as:
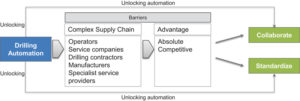
• Health and safety (HSE) – automation, including semi-automation, can address HSE initiatives by removing personnel from the drill center;
• A reducing pool of expert resource – the industry is losing a high number of experts in drilling, both due to staff cuts and retirements. However, it still needs and will continue to need expert service. Automation can address this through machine learning and the ability of machines to perform complex tasks when human skills might be lacking;
• Well design – the drilling of complex wells without requiring human resource and the drilling of a large number of simpler wells. Again, automation can assist;
• Data overload – humans can ignore or overlook sensor readings. Humans also tend to struggle to read and process the massive volumes of data that are being generated in real time and at high speeds. Machines, on the other hand, can handle the amount of real-time data and make decisions based on historical trends and can react faster and more accurately, thereby, reducing errors.

Despite all the benefits outlined above, the automation of a single piece of machinery on the drill floor will not provide all the anticipated benefits. The full process needs to be automated before a step-change improvement will be seen. To automate the full process, the drilling industry needs to collaborate to ensure that equipment on the drill floor “talks the same language” and can utilize plug and play functionality. At the moment, this is not the case, as each vendor is focused on developing its own autonomous/semi-autonomous technologies (Figure 1). With vendors effectively locking down their proprietary hardware and software (i.e., control, physical, sensors), the rig systems are not interoperable. Plug and play becomes impossible.

The main drivers forcing vendors’ behavior is that the drilling industry has a very complex supply chain with a large number of players and significant competitive and absolute advantage associated with drilling automation. This results in the industry’s reluctance to collaborate as major players already have a well-established market position while smaller players might be running the risk of becoming redundant or being absorbed by larger companies due to their potential impact on the supply chain. The obstacles to genuine collaboration have a major impact on the ability of the industry to achieve full drilling process automation and create a range of challenges for operators and drilling contractors (Figure 2).
Competitive advantage is mainly associated with service providers and vendors, i.e., companies that compete in order to influence the market share of their competitors. Absolute advantage is mainly associated with operators, where companies also compete but do not strive to influence the market share of other players. Additionally, each of the supply chain members has its own strategy that determines the type of products being developed, its position in the market and, more importantly, its competitiveness and the type of competition it is addressing.

As seen in Figure 3, “shapers” typically dictate the needs for the future and develop technologies that set the vision for the future. Visionaries react to shapers. However, they are also very proactive and look not only at enhancing current services and developing solutions for the future but also at creating new business models and environments. Adapters are focused on quickly adapting and continuously adjusting their services to address immediate market needs. The actions of visionaries often have significant consequences for both shapers and adapters as they typically impact market and business models and provide a unique technology offering not available from other market players.
Given their market-leading position, it is arguable how beneficial it is for visionaries to collaborate with other players who want to expand into the drilling automation segment. We can see already that there are market solutions providing unique technological solutions not available from other suppliers, which are starting to disrupt the existing shape of the market. These solutions are planting the roots of a “one-stop shop” approach. This approach would mean that operators would not need to shop around for multiple suppliers; everything would be provided by a single company. The down side of this is that the operator – and drilling contractor – gets locked into an arrangement with a single company. The potential implications of the one-stop shop are major market changes, with market consolidation and a reduction in the number of vendors.
Given the perceived competitive advantage and complex supply chain issues described earlier, collaboration will be difficult to achieve unless there are benefits for all participants. One way forward is to consider the selective standardization of critical components/systems so that drilling automation processes can progress whilst maintaining competition and supporting the existing market positions.
Selective standardization through industry collaboration has benefits for companies with any of the described strategies (Figure 3):
• Visionaries – sustaining current market position whilst ensuring it won’t change in the future due to service users not seeing value in higher-priced silo’ed solutions and other companies starting to offer competitive solutions but on the open-platform basis;
• Shaper – de-monopolization of the market and supporting market competitiveness: ability to pick and choose any vendor and be able to plug in its systems; and
• Adapters – ability to expand presence on the drilling automation market and increase competitive advantage.
But the key benefit of selective standardization through collaboration for all market players is essentially unlocking the true value of drilling automation. Selective standardization needs to first and foremost address equipment components that are both high cost and have a high impact on the ability to automate. Following that logic, an open-platform master control system with the ability to facilitate plug and play across equipment from different vendors and, therefore, control all rig operations is the single most significant enabler of drilling automation (Figure 4).
In addition to control systems, the selective standardization of common elements for topside drilling equipment at the component level is another area where drilling and drilling automation can capitalize. This approach will drive modularity and standardization of equipment components, therefore promoting cost reduction and overcoming interoperability challenges, both control and physical.
In conclusion, while it is clear that despite progress in drilling automation, achieving full drilling process automation and, therefore, extracting maximum value remains the major challenge. The key obstacles to unlocking the value are the complex nature of the market and the competition in the segment, which drives deficiencies and has a negative impact on the overall market. Collaboration through the selective standardization of control systems and equipment components is the key enabler for extracting value from drilling automation whilst ensuring participating market players benefit from collaboration. DC
Click here to watch a video interview with Ekaterina Minyaeva.