Role-specific well control training requires new thinking under IADC WellSharp
By Linda Hsieh, Managing Editor
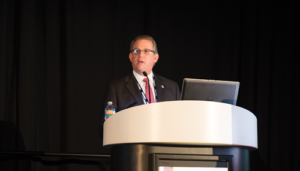
Among the most critical enhancements that were made as part of IADC’s new WellSharp well control training and assessment program is that training is now role specific. No longer is everybody lumped into just two or three different courses. The training curriculum is now tailored to the skills and responsibilities for each position on the rig – a total of 78 positions have been identified so far. Yet, in the year since WellSharp has been officially launched, the vast majority of people taking a WellSharp course has continued to attend supervisor-level training, Mark Denkowski, IADC Executive VP of Operational Integrity, said. “We are talking vigorously to operators and contractors to get them to adopt the mentality of role-specific training,” he said in a presentation at the 2016 IADC/SPE Drilling Conference on 2 March in Fort Worth, Texas.
Compared with the three levels of training offered under IADC’s legacy WellCAP program, WellSharp has five levels of training – awareness, introductory, driller, supervisor and engineer. “We moved from a situation where we trained everybody somewhat generically to a very role-specific training design,” Mr Denkowski said. “We looked at each position on a rig and analyzed his role with respect to well control. Then, we wrote the curriculum to that specification.” For a driller, for example, well control is about kick detection and shut-in. “They have a lot of other roles, but if they get that one thing right, we mitigate the hazard and the risk is reduced. If they get it wrong, we may have major events.”
However, although WellSharp provides well control training that has been tailored to the driller’s position, only 12% of drillers who have been through WellSharp training so far have actually taken the driller-level course. Instead, they appear to be taking supervisor-level training, according to IADC statistics. The association found that 72.6% of all trainees have taken supervisor-level training, even though only 43% of them needed such training.
This type of mismatch between job position and the level of training received is beneficial to neither the trainees nor their companies, Mr Denkowski said. “For example, you have a derrickhand who goes to the supervisor-level training because his company says that’s the best level. But he’s really just dragging the class down. The instructor finds that he’s teaching this derrickhand basic math. It dilutes the experience of the people who actually need to be in that class,” he said.
Supervisor-level training was designed for toolpushers and others who will remediate or kill the well, if required. The driller-level training, on the other hand, focuses on barriers and barrier management, situational awareness and kick detection and shut-in. It does not burden the driller with the concerns of killing a well. “Drillers will assist in the killing of the well, but that’s not their primary role. That’s why it’s not part of the course,” Mr Denkowski explained.
Looking forward, he urged companies in the drilling industry to go beyond the type of traditional thinking where all rig crews must take supervisor-level training in order to demonstrate competency. “That’s not good for the system, and it doesn’t work,” he said. “Let’s make sure that people’s positions and training are aligned properly, and the right information is applied at the right time.”
For more information on WellSharp, click here. For more details about Mr Denkowski’s presentation, please see IADC/SPE 178889, “A Paradigm Shift in Well Control Training and Assessment.”