RFID technology applications help to improve efficiency, economics of completions, stimulation operations
Extended-reach North Sea well demonstrates potential to expedite hydraulic fracturing cycle times as cementing, other applications for RFID are developed
By Euan Murdoch, Crystal Wreden and Alex Goodwin, Weatherford

Many conventional downhole tools, designed for the comparatively shallow and simple wells of past decades, are difficult to actuate from the surface in deep or complex wells. Mechanical or hydraulic actuation in these cases can require operators to make multiple intervention trips downhole, driving up operational expenditure (OPEX) and threatening the economic vitality of the wells. The industry’s search for more efficient and reliable downhole control systems and tools has led to a growing interest in radio frequency identification (RFID) technology.
RFID applications in oil and gas extend beyond inventory and asset tracking. RFID technology can be used to control diverse equipment by pairing small RFID tags with an active antenna in a downhole tool. The tags are coded with a specific signal or command and dropped or pumped downhole. As the tags approach the tool, the active antenna generates an electromagnetic field that energizes each tag to begin the transmission of its unique command data. The commands are processed by the downhole tool, which then opens, closes or takes a reading, as directed.
Weatherford began its development of RFID tools in 2005 and completed the first field trials of a drillstring-deployed downhole valve in 2006. This early work led to the development of the JetStream RFID drilling circulation sub, which enables efficient cuttings transport and hole cleaning, and the RipTide RFID drilling reamer, which enlarges the borehole below casing restrictions. In each application, RFID downhole technology produced benefits, such as increased safety and efficiency in high-cost, high-risk drilling environments.
Benefits of RFID in Completions
Weatherford has applied the same RFID principles to improve the efficiency and economics of completions and stimulation operations. Regardless of their function, all RFID-actuated tools share many operational benefits over tools that are activated by mechanical or hydraulic means.
The primary benefit of RFID completion tools is to remove the need for intervention, which in turn reduces both risk and OPEX. Traditional mechanical completion tools typically require actuation using equipment such as coiled tubing or wireline. The process of mechanical actuation often occupies a good deal of deck space and manpower, both of which are at a premium offshore. Intervention operations consume large amounts of OPEX while increasing operational risk, thereby posing a critical challenge to the economic viability of a project. RFID-equipped downhole tools can be actuated without mechanical manipulation from surface, which all but eliminates these issues.
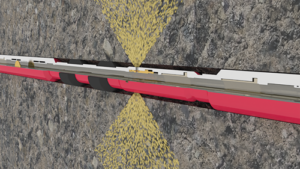
Each RFID tag is pre-programmed on surface with a code that is specific to a given downhole tool. Commands instruct the tool to actuate immediately or after a specific condition has been met, and a series of error-checking variables ensure that accurate data transfer has taken place. Multiple tags with different commands can be dropped to selectively activate or deactivate a tool multiple times, without having to perform interventions. The selective pairing of one tag to one downhole tool allows multiple RFID tools to be installed in the same completion string with no risk of interference.
While RFID is the primary form of actuation for these tools, other forms of remote actuation are also available. In closed systems with no flow path available to the RFID tag, the tools can be controlled using frequency-modulated pressure cycles or programmed to activate at set times or intervals. Combining all three activation modes in the same application gives the user a highly flexible system that can be configured to meet operational needs without adversely impacting economics.
In hydraulic fracturing applications, RFID-enabled isolation devices avoid the need for balls and seats or plug-and-perf operations. As Figure 1 shows, ball-drop systems offer limited options during screenouts and must be milled out after stimulation is complete, adding rig time and cost to the process. The absence of ball seats in RFID tools yields a uniform inside diameter that makes it possible to run any number of tools in sequence. Additionally, the RFID system’s ability to accurately indicate tool function and provide screenout contingences reduces uncertainty, enabling improved financial risk planning in offshore and other high-cost environments. Finally, when the two methods are compared in offshore tight-gas applications – where an aggressive tip-screenout philosophy makes screenouts more likely – the frac cycle time is significantly lower using RFID-enabled tools, which lowers OPEX.
Interventionless Stimulations

Operators in high-cost offshore environments have long sought an enabling technology to expedite hydraulic fracturing cycle times. In June 2015, Weatherford deployed its AutoFrac lower-completion system into an extended-reach North Sea well with a 6-in. open hole and a bottomhole static temperature of 80°C (176°F). The operator needed to reduce the time and risk associated with multizone stimulation in this well. Conventional techniques, such as plug and perf, ball-drop sliding sleeve and coiled tubing-based fracturing, were time-consuming and lacked contingency options in the event of a premature screenout.
The lower completion system incorporated seven RFID-controlled stimulation sleeves and seven RFID flapper valves. These tools enabled remote isolation and access to the reservoir by applying alternating frequency-modulated pressure pulses that opened one sleeve at a time for selective fracturing of each stage. Post-stimulation, RFID tags could be circulated to close the flapper valve prior to moving to the next stage.
Following the installation of the system at a measured depth of 6,300 to 6,400 m (20,600 to 21,000 ft), an RFID-actuated flapper valve was closed to isolate the toe, the hanger was set, and the liner was successfully integrity tested. When the operator was ready to begin stimulation operations, they used pressure pulses sent from the platform remotely to open the first sleeve and simultaneously activate the tools in the first section. Once access to the reservoir was confirmed via a pressure drop, the stimulation vessel began the treatment.
RFID tags pumped at the 3-ppg proppant stage commanded the next flapper valve to close after a predetermined delay. This enabled completion of the first treatment and shut-in analysis prior to isolating the zone. An early screenout occurred during the flush stage, leaving proppant-laden fluid in the wellbore. The flapper valve successfully closed despite the screenout, allowing for a closed cleanout to be performed. If a ball-drop completion system had been used, the operator would have needed to mill out the ball seats at this juncture and proceed with a plug-and-perf operation, resulting in a significant increase in OPEX.
After the cleanout was complete, another set of pressure pulses opened the second sleeve to provide access to the zone, and fracturing operations commenced. Once formation breakdown was achieved in this zone, another frequency-modulated pressure pulse was applied against the open formation, which triggered the flapper valve to open after a preset delay.
This same sequence was repeated for subsequent zones moving up the well, enabling stimulation treatments to be completed within approximately 12 hours per stage. After the final treatment, cleanout occurred without any milling or shifting operations. The client saved time in both primary and contingency operations during the multizone stimulation, as the RFID technology reduced the number of coiled-tubing runs and enabled efficient recovery from screenouts while retaining full functionality.
Completions Applications Continue
Weatherford is actively advancing RFID technology for applications beyond stimulation jobs. The RFID-operated OptiBarrier is a multi-cycle barrier ball valve that serves several purposes. The valve is rated to ISO28781 V1 with a zero gas-leak rate. It can be run as part of the lower completion and closed using an RFID tag to prevent fluid loss following gravel-pack applications or while running the upper completion. The valve can then be re-opened remotely at a later date.
The valve can also be deployed as a suspension valve to isolate the wellbore while installing a subsea tree: After remotely closing the valve using RFID tags, the subsea blowout preventer is removed and replaced with a tree. The suspension valve can also be reopened at a later date using a pressure cycle. Using a ball valve with these capabilities avoids the need to have a vessel present to set a plug via coiled tubing or slickline, which saves money and reduces the risk of damaging downhole equipment or having to perform a fishing operation to retrieve tools.
The RFID-enabled CrossStream reverse-cementing system improves cementing operations in weak and depleted formations where fluid losses are a concern. RFID tags enable the system’s three tools – a circulation tool, fall-through flapper and crossover tool – to function multiple times, directing the cement’s flow path down the annulus by gravity assistance. This results in lower bottomhole equivalent circulating densities, which reduces the risk of fluid losses, inadequate cement coverage and costly remediation in weak or depleted zones. Initial onshore field trials have proven the potential of this system, and it is now ready for offshore field trials.
Another advanced cementing technology is the RFID port collar. An interventionless fluid management device, the collar opens remotely to allow cement placement, fluid displacement and clean-up following cementing operations. The device’s RFID communication system eliminates the need for wash pipe, intervention, wires or control lines, thus reducing completion time and risk.
An RFID hydraulic communication sub has also been developed to provide an interventionless means of diverting tubing pressure to set hydraulic devices in the wellbore. The sub interfaces with any tool that is normally set and activated via control line but without the need for a dedicated control line to pass through the hanger or wellhead to the surface. The sub is often used to set an annular safety valve (ASV), which isolates gas in the lower annulus to protect the topside facilities and personnel in the event of an unplanned release of gas to surface. This RFID sub/ASV combination has been successfully deployed in 35 wells in the Caspian Sea, saving the operator approximately 36 hours in rig time and intervention operations, valued at nearly $25 million.
As operators face the dual challenges of ongoing cost pressures and increasingly complex well profiles, RFID-enabled completion tools provide safer, more efficient and cost-effective solutions. DC