OOC awards recognize IADC SEMS work
Two IADC staff members were among 10 people who received recognition awards from the Offshore Operators Committee (OOC) on 7 December 2011 in recognition of their efforts and contributions in the development and rollout of the SEMS Toolkit last year. Thr
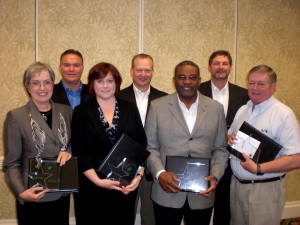
ough an OOC task force and in cooperation with the Center for Offshore Safety (COS), the toolkit was developed to address consistency and compliance with new requirements by the US Bureau of Ocean Energy Management (BOEM), as well as their effective networking with other industry representatives.
IADC’s Dr Brenda Kelly, senior director of accreditation and certification, and Julia Swindle, industry compliance specialist, attended the ceremony to receive the awards from OOC chairperson Susan Hathcock, Anadarko Petroleum.
Dr Kelly’s contributions were her leadership of the Competence Subcommittee, development of the Knowledge and Skills Documentation Tool, contributions to the SEMS Compliance Readiness Worksheet and other tools, and speaking at a series of rollout conferences held in August and September last year. Ms Swindle contributed to review of all tools and provided administrative support of the entire SEMS Toolkit development effort. IADC has seconded Ms Swindle to work with the COS for one year to help with the initial establishment of the COS.
Besides Dr Kelly and Ms Swindle, other recipients of the award included Milton Bell, ExxonMobil; Greg Duncan, ConocoPhillips; Roger Molaison, BHP Billiton; Troy Nugent, Baker Hughes; Jeff Ostmeyer, Anadarko; Kim Parker, Hercules Offshore; Ruth Rodriguez, Delmar; and Bill Walker, Cobalt International Energy. Each recipient contributed significantly to the development of the tools in the toolkit, working with subcommittees and/or providing administrative support. A significant number of IADC member companies also contributed to the effort.
“The participants on the task force have my sincerest gratitude and respect for their leadership and contributions to the SEMS toolkit, which is of immeasurable value to our industry,” said Mr Ostmeyer, who led the toolkit development effort.
Currently, the OOC SEMS Subcommittee and its task groups have concluded their work with the public release of 8 SEMS Toolkit products. Tools developed were:
• Audit checklist;
• Contractor readiness tool;
• Matrix of regulatory required training for drilling, production and marine positions;
• SEMS orientation curriculum;
• Knowledge and skills documentation tool;
• Operator-contractor agree letter templates; and
• Definitions.
These tools are available on the IADC website.
The COS will adopt all tools and maintain them going forward, although a small team from the OOC SEMS Subcommittee continues to work with the COS in the development of the Auditor Certification Program.