No longer niche: Expandables finally going mainstream
By Katie Mazerov, contributing editor
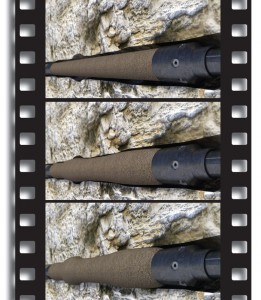
Since they came onto the scene nearly 15 years ago as the game changers that were going to revolutionize drilling and completions, expandables are finally coming of age. Where they once lurked in wellbore niches trouble-shooting particles of sand, isolating undesirable zones and providing only contingency solutions, expandable tools are going mainstream. Continued improvements and years of testing are delivering better solutions and greater reliability in solid expandable technologies as well as sand screens. With today’s increasingly complex wells, operators are recognizing the value of integrating expandable systems in well design, not only to circumvent problems but also to realize increased production.
“Over the years, expandable technology has gradually matured to the point that the technology is dependable to meet business needs, such as resolving drilling trouble and being part of a well deployment plan,” said Shaohua Zhou, petroleum engineering consultant, Drilling Technology Team, for Saudi Aramco. “More competition in the market has further improved the services.”
The company has used expandables primarily in mature wells, for re-entry or workovers for maximum reservoir contact wells. “Saudi Aramco is an industry leader in terms of solid expandable technology deployment in the field, with close to 100 wells that have been installed so far, primarily with 5 ½- to 7-in. expandable liners and/or casing repair patches,” Mr Zhou said.
“Expandables allow continuation of the drilling operation to reach the target reservoir with acceptable hole size, which enables us to directionally drill the remaining reservoir section with geosteering capability,” he continued. “They also facilitate deployment of slim-hole smart completions for production optimization.”
Installed expandable systems fall into three categories, said David Crowley, chief executive officer, Enventure Global Technology, which provides solid expandable technologies for upstream oil and gas operators worldwide. Planned-in systems are designed into the well; a planned contingency approach is when operators want expandable tools on board and experts on call; a contingency installation occurs when there is no upfront planning but problems are encountered, typically in lower sections of the well, that require deployment of expandables to address the problems and, in some cases, save the well.
“We are growing in the planned-in business,” Mr Crowley said, “which speaks to the fact that expandables are gaining a wider industry acceptance. With this option, we know upfront that Enventure will be involved in engineering the well with better insight into pressure regimes and wellbore stability issues. The front-end knowledge sharing before we execute any work often proves to be invaluable.”
Two-fifths of Enventure’s proprietary SET solid expandable systems are being deployed for exploration drilling, with the same percentage for development drilling. The remaining work involves well completions. “In the Gulf of Mexico, for every exploratory well drilled, between two and six development wells are drilled,” Mr Crowley noted. “Planning for challenging development drilling is started much further ahead. Deep wells, below 28,000 ft, are being planned a year ahead of time.”
Drivers in the growth of planned-in expandables appear to be basin-specific, particularly in the deep Gulf of Mexico and the onshore re-fracturing and high-pressure markets, Mr Crowley said. “In the first five offshore wells post-moratorium in the GOM that were permitted and completed this year, we were planned-in to four of them, with expandable sizes ranging from 13 3/8 in. to 7 5/8 in. The four wells were drilled by one major and two independents; two were new wells and two were re-entries.
“In the GOM, where depths pose significant challenges, there is enough offset data from adjacent wells to allow clients to realize whether they are in an overpressured or loss zone, and can expect problems with hole stability,” he continued.
“They will put an expandable system in their arsenal to get to the shoe depths required in one or more phases of the well. We have an independent operator/client that has been consistently drilling in the Wilcox play where the basement is ultra-deep, sub-32,000 ft. To get a reasonable size of completion tubular through the producing zone, they require an expandable somewhere up the hole in order to maintain both hole size and provide options should difficult conditions occur in the lower well sections.”
In the re-fracturing market, expandables are sometimes installed to address problems with completion tubular integrity. “In some cases, the tubular is in good shape, but the operator has produced and depleted a perforated zone and wants to re-perforate in different areas of a horizontal section,” Mr Crowley explained. “We will install a re-fracturing liner, sometimes as long as 4,000 ft, inside the existing liner and expand it to get the maximum internal diameter (ID) possible. Then, the operator will perforate a new section of that horizontal leg.”

The expandable high-pressure repair market is occurring in basins such as the Haynesville and Eagle Ford plays. There have been cases where operators have installed completion systems on newly drilled wells and then encountered a lot of cyclic loading, both pressure and temperature, during fracturing, Mr Crowley said. “In some cases, when multistage fracturing stresses the initial completion, the completion may break down at a tubular connection. We will then be called in to put a high-pressure expandable across the problem area. Five years ago, we would not have been able to provide these solutions due to the temperature and pressure ratings of our technology.”
Such advances in the technology, along with greater reliability, have helped operators overcome concerns about the perceived risks associated with expandable systems. “Our biggest competitors are conventional casing and conventional mindsets,” Mr Crowley said, noting that eight years ago, Enventure had a reliability rate of 80%. With more than 1,200 installations worldwide, the company has been able to couple its depth of experience with a culture of continuous improvement to achieve a current reliability rate of greater than 98% and several industry bests, including a record of one minor medical incident over a 12-year period.
“We differentiate with people and technology, in that order,” Mr Crowley said. “We have made several modifications over the years to our expansion cone, to the metallurgy of our tubulars and the configuration of connections. And we have put a lot of effort on training.” More casing sizes are also available, ranging from 16 in. to 4 ¼ in.
The company also has modified its elastomers, the seals that go on the outside of the tubes, to extend the temperature regime above 325°F. “In the new-well drilling market, some of our clients are taking total depths past 35,000 ft,” Mr Crowley said. “The deeper we go, the greater the requirement for higher pressure- and temperature-rated equipment.” Enventure has developed a heavier wall on some sizes of expandable tubulars in order to improve the collapse rating of the tubular, to withstand the formation pressures, after the tubes have been expanded by as much as 14%. “This is a significant step forward,” he said, “as we are now able to deliver the conventional tubular collapse rating to our clients.”
The newest technology, launched last year, is a single-diameter open-hole clad for wells with underpressurized or loss zones that cost clients excessive amounts of expensive drilling fluids and loss control materials in a process that can take several days. For an older well in the Middle East with those characteristics, Enventure set an 8-in. MonoSET open-hole clad across the loss zone, expanded it and sealed it off against the formation above and below the loss zone (a cement-less solution) with no loss of wellbore diameter. The client shaved days off the well and benefited from a lower drilling fluid bill and ultimately a lower well cost without sacrificing hole size.
In the pipeline, there are solutions to enhance production in mono-diameter, or monobore, wells. In this case, an operator would drill a section of 12 ¼-in. hole, then set a 9 5/8-in. expandable casing and drill the next section of hole to 12 ¼ in. and repeat the process. “We’re seeing a lot of interest from operators wanting this because they can move less dirt and will have lower drilling fluid costs,” Mr Crowley said. “In some of the deeper reservoirs, this will be an enabling technology that will allow our clients to get a reasonable producing wellbore size through the reservoir, enabling them to access oil and gas that otherwise could be stranded.”
Also on the horizon is expandable liner drilling for complex wells with stability issues. “Once the tubular is installed to the required depth, it could be expanded between 10% and 20%, resulting in much greater production than with conventional liner drilling,” he said.
The MonoSET open-hole clad system targets wells with underpressurized or loss zones that cost clients excessive amounts of expensive drilling fluids and loss control materials in a process that can take several days.
[local /wp-content/uploads/2011/07/MonoSET_OHC_3D_final.wmv nolink]
The industry is also seeing enhancements in expandable screen technology. GeoFORM conformable sand management system using Morphic technology, the newest addition to Baker Hughes’ suite of expandable technologies, was launched in March. The technology is designed primarily for open-hole sand control in situations where no additional stimulation, or frac packing, is needed.
“We perceive this system as a potential game changer for the way sand control completions are conducted,” said Eddie Bowen, product line manager, screen-equalizer technology, Sand Control Marketing Division. “Earlier expandable sand control solutions, such as Baker Hughes’ EXPress expandable screen system, once considered unconventional, have now become mainstream. With the GeoFORM sand management system, we have taken our expandable screen portfolio to the next level.”
The GeoFORM sand management system enables activation of a shape-memory polymer to fill the borehole, replacing the need for gravel packing or any type of expandable metal product, Mr Bowen explained. The shape memory material is mounted on a perforated base pipe, run in the wellbore, exposed to an activation fluid at downhole conditions and expands, filling the irregular shape of the borehole up to its manufactured diameter.
“In a full or near-gauge hole, it provides a residual stress,” Mr Bowen said. “It is this conformance that provides optimum filtration and inflow performance. The product is installed at a run-in-hole diameter, and with the aid of a catalyst and bottomhole temperature, expands until it meets resistance of the borehole without the need for a cone or outside hydraulic pressure.”
The system mitigates the risk of a collapsed hole when pumping fluids as in a conventional gravel packing operation, particularly in long intervals. “Once we run it downhole, it is activated in situ at bottomhole temperature with the aid of an activation fluid,” Mr. Bowen said. “We’ve eliminated all the associated health, safety and environmental risk issues that come with rigging all the pumping equipment and bringing multiple personnel on board. It eliminates the hardware, personnel and associated costs of conventional methods as well as the rig time savings.”
The globally deployed system was designed for an open-hole diameter of 6- to 6 1/8-in., with a temperature limitation of 145°F. An enhanced version, for an 8 ½-in. open hole, will be marketed soon, and a version for temperatures up to 195°F will be available later this year. The company sees a niche market in remediation, where sand control was not considered in the original completion design or an existing sand control solution has failed. Morphic shape memory material could have applications beyond sand control.
The GeoFORM conformable sand management system using Morphic technology was launched in March. The technology is designed primarily for open-hole sand control in situations where no additional stimulation is needed.
[local /wp-content/uploads/2011/07/GeoFORM_OTC_30sec.wmv nolink]

Among Baker Hughes’ mainstream applications is the TORXS expandable liner hanger system that can be set conventionally, before the cement sets. “This virtually eliminates any risk of becoming stuck in wet cement,” said Robert Peña, project manager, Wellbore Construction Group. “The system has broad applications for high-load, high-pressure needs. Other applications include deviated and horizontal wells, deep and shallow wells, straight holes, frac liners, monobore completions and drill-down or ream-down liners.
“A lot of formations are depleted or contain lost-circulation zones, where conventional drilling is too risky,” Mr Peña said. “Often there is a chance of losing all circulation because anything that is pumped downhole is lost to the formation, which can cause stuck pipe, lost rig time, sidetracks and expensive mud losses. Using drill pipe with a conventional bottomhole assembly (BHA) and bit in these environments is inherently risky. To minimize this risk, we actually drill the problematic formations with the liner itself. “
Liner drilling is an old method, but in concert with the TORXS hanger system, there is added torque capability to rotate and bypass the area for cuttings removal. “The process is hydraulically balanced,” Mr Peña noted. “That is huge when we are drilling down the liner because we are not limited by circulation pressures. We won’t physically set the liner until we want to. We drop a ball from the surface, to land on a ball seat. We then build up hydraulic force and push the cone through the slips, expanding the slips out to set the hanger. This allows the operator to circulate at high pressures, drill a hole with the liner and clean out the cuttings with circulation pressures at the rate needed.”
The TORXS system was used successfully in an offshore well with complex formations that had experienced four sidetracks and was on track to be abandoned due to continued fluid loss during the drilling phase. Baker Hughes ran the TORXS liner hanger with an 8 ½-in. EZCase liner drilling bit to drill 131 ft of a difficult zone with complete lost circulation at more than 10,500 ft. The well was drilled and cased successfully, after which the liner was set and the annulus sealed. The customer was also able to drill the next section with a seawater system. The operator estimated a $7.5 million cost savings in nonproductive time and mud.
The TORXS expandable liner hanger system can be set conventionally before the cement sets. This virtually eliminates the risk of becoming stuck in wet cement, according to Baker Hughes. The company believes the system has broad applications for high-load, high-pressure needs.
[local /wp-content/uploads/2011/07/TORXS-cut.wmv nolink]
A niche tool that is moving toward mainstream applications is Baker Hughes’ linEXX solid expandable system that enhances production by expanding both the hanger and liner from top to bottom. The monobore expandable liner extension system is enabled by a recess shoe on the previous casing string, said Carl Stockmeyer, global senior applications advisor.
“If a drilling problem or casing design challenge occurs, we can run the liner below the shoe, expand it and keep the same hole size,” he said. The linEXX monobore system uses standard bit and tubular sizes below the expanded pipe for continuity and cost reduction in the well design. “Although the recess shoe could be used on every well as a contingency, we are starting to see customers include the system in their well designs, not just as a contingency.”
The linEXX system was deployed successfully in 2010 in a difficult onshore vertical exploratory well in Egypt. The well had been compromised by lost circulation of 150 bbl/hr and drilling breaks, resulting in caving, sloughing and swelling shale sections. After an unsuccessful first attempt to get the expandable liner through the shale sections, the liner was pulled. The hole was then conditioned further, the liner was picked back up and run to depth, the hanger positioned in the recess shoe of the 9 5/8-in. casing. Both the hanger and liner were expanded to the same inside diameter as the casing above.
The system was able to isolate the problematic zone with no reduction in hole size from the previous casing. Prior to cementing, the expanded liner was pressure-tested to 1,000 psi. While cementing, collapsing formation packed off the casing annulus preventing a full annular cement, therefore pressure was applied inside the casing allowing 15 barrels of cement to be squeezed into the hole.
Weatherford International’s proprietary expandable sand screen (ESS) system has been used successfully for more than 10 years and in more than 650 applications globally as an alternative to gravel packs, particularly in long, single-zone reservoir sections. On the solid tubular side, the company is seeing a shift among operators seeking solid expandable systems for more mainstream applications.
“Solid expandable systems have matured into mainstream technology that is currently being used over the life of the well, whether it be in the early planning stages to improve the well architecture, in hydraulics or to mitigate drilling hazards such as wellbore stability and pressure anomalies,” said Douglas Farley, global product line manager, Solid Expandable Systems. “This used to be a niche technology that was used when a drilling problem was encountered. It was a last resort to avoid downsizing the well.”
Weatherford’s MetalSkin line of products includes the Monobore Open-Hole Liner Extension currently being used as a contingency liner in several difficult deepwater wells in the Eastern Hemisphere. “The value of this technology is becoming ever more evident, not only as a contingency liner to address wellbore stability problems and low- and high-pressure events, but also as a conventional system to improve cementing efficiency by providing more annular clearance,” Mr Farley said.
For wells with problem zones, such as lost circulation or fractured carbonates, Weatherford’s MetalSkin Monobore Open-Hole Clad system, now in field trials used below 9 5/8- to 9 7/8-in. casing in the North Sea and Middle East, reduces the number of expandable tubulars required to address drilling hazards and serves as a steel mud cake. “We run the clad through previous casing, and as we drill ahead and run into a problem in the wellbore, we can set the clad to cover up the problem zone and still maintain an 8 ½-in. drift,” Mr Farley said.
“As we drill farther, the operator can then run a second or even a third clad through the previous clad to address additional problematic formations.” An 8-in. liner can be expanded 20% with a special compliant cone that creates the 8 ½-in. ID. A 5 ½-in. liner can be expanded twice, to 28%, creating an ID of 6 ¼ in. Weatherford is in joint development with a major oil company for further development of the monobore clad and is planning field trials for additional sizes in Q4 2011.
The newest application in the portfolio is a cased-tool method for repairing 4 ½-in. casing using a solid expandable 3 ½-in. pipe. “This system has been needed in the industry for a long time because there are thousands of 4 ½-in. cemented production casing strings that have problems, such as corrosion or unwanted perforations, so remediation operations are very limited,” Mr Farley noted. Here, the challenge is developing a connection that will work with the thin-walled 3 ½-in. pipe. The threaded connection cannot be any thicker than the pipe wall, so the design will be weaker than the pipe mechanically but still seal as much pressure as possible.
The connection piece of the equation is critical to the success of all solid expandable systems. “It is important to remember that with hydraulic expansion systems, the connections must seal before, during and after expansion,” Mr Farley said. “The pre-loads on the connections can be different at any point in the casing string. During expansion, the loads change as the cone passes through the connection.”
To that end, Weatherford has made perfecting connection reliability a major focus through its Oil Country Tubular Goods Technology Center (OCTG). “When pipe is expanded, the connections in particular get worked over,” said OCTG director Richard DeLange. “Advancements in solid expandable systems have far outpaced connection development in terms of reliability. But Weatherford’s investment in the connection research center is fostering the development of advanced connection technology that has been performance verified using industry testing standards. We’ve been able to develop much better connection technology in terms of reliability during expansion.”
For example, the newest connection technology developed at the center allows connections for 5 ½-in. monobore open-hole clad liners to be expanded to a total of 28%, with an expanded drift of 6.250 in. “The new expansion system and connection design can be expanded first to 20% with a solid cone, and expanded again with a segmented cone to a total of 28%,” Mr DeLange said.
The center is playing a key role in developing more comprehensive industry testing standards for connections. “At our testing facility, we have been able to develop connections that we know will work at any point in these liners,” he said. “Weatherford has the only expansion simulator in a lab environment that can expand test samples under exactly the same conditions that occur downhole, from the bottom to the top of the liner, during expansion. Without this capability, there is no other way to make connection test samples under the same downhole conditions without actually expanding the liner downhole and then retrieving it.”
Solid expandable technology also is being used to overcome mature field challenges by addressing casing integrity problems and optimizing the completion side, Mr Farley added. Recently, the company deployed solid expandables for a remediation project in North America where the customer needed to repair some old wells with corroded casing and cover unwanted perforations. “It was important to preserve hole size, and we analyzed several techniques from a cost standpoint,” he said. “We found that cased-hole cladding using solid expandables was 40% cheaper than squeeze cementing and also significantly reduced the number days, bringing the wells back on production earlier.”
In Q1 2011, Weatherford commercialized its TruForm expandable liner hanger product line, which complements the company’s proven conventional liner hanger systems. “Expandable technology utilized in liner hanger and packers designs allows the equipment to have functionality, without the traditional external mechanisms on the equipment,” said George Givens, global product line manager, Liner Systems. “For the right applications, this system provides potentially a stronger, more compact and ultimately more reliable system.” The TruForm design is ISO 14310 level V0 (gas) certified with 12,000 psi at 300°F while supporting full liner weight. Achieving that performance level with conventional liner systems has not been possible. Additional developments continue.
SET and MonoSET are trademarks of Enventure Global Technology. GeoFORM, Morphic, TORXS and EZCase are trademarks of Baker Hughes. MetalSkin and TruForm are trademarks of Weatherford.
Animations demonstrating these expandable technologies can be found online at www.DrillingContractor.org.
A few years ago I’d have to pay someone for this inforatmion.