New-design rotary steerable systems target higher doglegs, durability in high-temperature reservoirs, autonomous steering

By Alex Endress, Editorial Coordinator
As operators hunt for reserves in plays with increasingly high pressures and temperatures and where high-dogleg well profiles are needed to access sweet spots, the cost of drilling has continued to grow. To reverse that cost trend, oilfield service companies are working to design and build more reliable and higher-performing rotary steerable systems (RSS). “What we’ve seen here, specifically in the North American land market, is the drive toward factory drilling and automation to decrease costs and an increased focus on improving the quality of wellbore placement to increase reserves,” said Steve Krase, Director of Wellbore Placement at Nabors Drilling Solutions.
Companies are now offering RSS tools that can push dogleg capability up to 16˚/100 ft, tolerate temperatures as high as 200˚C and steer more dependably – even autonomously – toward the targeted reservoir. This has been enabled by things like design changes that provide more flexibility, the use of ceramic electronics and the refinement of control logic for autonomous bit orientation.
Companies are also recognizing that cost-cutting alone won’t bring shale drilling back into an affordable cost window. They also must help operators improve recovery.
“The situation now is much more focused on the margin-per-well,” said Dr Shona Grant, Managing Director of 2TD Drilling, a Nabors company. “A tool like (RSS) can give much better well placement and lateral length in the shale plays so you increase the production per well. It will also give a smoother wellbore that should make the subsequent running of the completion easier, thereby reducing overall time and cost,” she said.
Service Consolidation

For a typical North American land drilling project, an operator may hire up to six different service providers – which can make for a complicated and costly operation. To help streamline the process for operators, Nabors started offering RSS technologies in fall 2014 after acquiring RSS manufacturer 2TD. Integrating RSS with its existing directional drilling and mudlogging services, the contractor rebranded these services as Nabors Drilling Solutions in January.
When oil prices began falling, Mr Krase said, Nabors turned its focus to consolidating rig-site services as a way to increase the value proposition for operators. “We believe that in breaking down the siloes, it’s a one-team, one-service offering. We believe that we can get some significant efficiencies out of that,” he added.
2TD is currently developing an RSS that can achieve buildup rates (BURs) of 15˚/100 ft. The OrientXpress RSS will initially target the North American land market but could move offshore once a track record has been built onshore. The tool features direction and inclination measurement sensors situated 6.5 ft behind the bit. “The control logic within the tool itself tells the tool to adjust position if data from the inclination and/or azimuth sensors are not at desired values. Positioning the sensors so close to the bit gives very good control,” Dr Grant said. The tool is similar to a push-the-bit system, she added, but the company prefers to call it an orient-the-bit system “because of the more passive way the tool adjusts position. There are no pads that come out against the wellbore.”
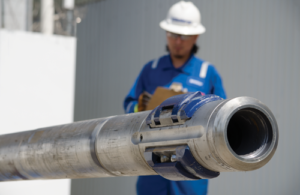
Further, the tool has a length of 12 ft. This enables the MWD system to be placed an estimated 30 ft closer to the bit than drilling with a motor, Dr Grant said.
In lab tests while drilling through concrete, the RSS has shown it can consistently reach 15˚/100 ft, according to Dr Grant. In Q3 2015, the company tested the tool by drilling a well to 1,370-ft (418-m) TD at 2TD’s yard in Ålgård, Norway. “This test was about confirming the steering functionality of the tool, the interface to the Nabors MWD system and two-way communications to the surface. It was also the tool’s first exposure to a real drilling operation,” Dr Grant said.
The test consisted of three stages, each 115 ft (35 m) in length, drilled through granitic gneiss, a type of hard basement rock. The first stage was a vertical hold section, the second was a curve section, and the third was an angle hold followed by a turn to the left. For the curve section, the tool was set to progressively higher BURs – 40%, 60% and 80% offset – to confirm the progressive nature of the tool’s steering response toward the tool’s maximum 15˚/100-ft build angle.
The ROP in the Norway test was only 7-16 ft/hr (2-5 m/hr) – low because of the very hard nature of the rock. In shale plays, Dr Grant said, the tool would be able to achieve higher ROPs. Each stage in the Norway test lasted approximately four days, with several weeks in between so modifications could be made to the system design and steering logic. The final inclination achieved in the angle hold section was about 26˚ off vertical, as per the test objectives.
By the end of the testing period, the success rate for the receipt of steering commands from the surface increased to 100%, according to 2TD. The test also confirmed a fully functioning interface with the Nabors MWD system, validating the combined steering service that Nabors plans to begin offering in the near future.
2TD is planning to test the OrientXpress in North America in April. Pending the success of these tests, the company anticipates a commercial launch of the tool later in 2016.
Reaching 16°/100 ft

In an environment of low prices and low margins, having reliable equipment becomes even more important. John Rice, Global Technology Manager – RSS/DD at Weatherford, said he sees operators focusing much more on a tool’s ability to reduce downtime and avoid unnecessary trips. In July last year, the company released the point-the-bit Revolution High Dogleg (HDL) rotary steerable system to increase reliability in high-BUR applications.
The HDL can achieve BURs of 16˚/100 ft, which is enabled by changing the geometry of the drive shaft from Weatherford’s base RSS model. Instead of using a bottom stabilizer that screws onto the bottom of the drive shaft, the HDL uses a sleeve-type pivot stabilizer that screws onto the RSS itself. This not only provides more flexibility in build sections but also helps the tool withstand intense vibrations in high-dogleg turns, according to Mr Rice.
To capitalize on the tool’s 16˚/100-ft capability, Weatherford is targeting the Marcellus and Utica plays, where operators are trying to maximize reservoir exposure and minimize drilling time. Because vertical drilling is faster than directional drilling, the HDL enables operators to drill longer vertical sections before kicking off, which helps them reach the targeted true vertical depth with less steered footage. Mr Rice said operators are targeting doglegs of 10-12˚/100-ft on average in these areas, which makes a tool that outperforms these BURs high in demand.
Originally, the HDL was designed not for high dogleg capability but to withstand severe vibrations in lateral drilling in Abu Dhabi carbonates. The pivot stabilizer used in the tool was initially implemented to help the RSS better absorb shock produced by interaction between the formation and drill bit. “As (our team) began to develop the tool, they realized through modeling that they could achieve higher doglegs with it,” Mr Rice said. “Softer formations – carbonate-heavy ones – will break apart as you move through them and excite those vibrations up through the drill string.” Although the RSS is now marketed for its high dogleg capability, it also remains suitable for high-vibration environments. The tool is currently being used to drill six onshore wells in Abu Dhabi, each with lateral drilling requirements.
The HDL is one of four RSS tools that are now part of Weatherford’s Revolution suite. The other three are the Core, which is a base model with a non-rotating sleeve that can reach 10˚/100-ft BURs; the V, which was developed for vertical drilling; and the Heat. The Revolution Heat is designed for extended-reach wells with temperatures up to 175˚C. This RSS uses rotary seals made of hydrogenated nitrile butadiene rubber, a material that is also used in the nuclear power, aerospace and maritime industries. It is able to maintain its protective sealing capability even after long-term contact with high temperatures, chemicals and oil, according to Weatherford. The seals are located on either end of the Heat’s non-rotating sleeve, isolating the drilling fluid flowing around the tool from the hydraulic fluid used internally to power the manifold and allowing the drive shaft to steer. The Heat is particularly suitable for the South Texas Eagle Ford, where downhole temperatures from 163˚C to 174˚C are common, according to Mr Rice.
In 2015, an operator deployed the tool in five wells where formation temperatures exceeded 160˚C. The goal was to drill the curve and lateral sections in one run, thereby reducing rig time. Each of the five wells was drilled in a single run, and average ROP was 130 ft/hr. This allowed the client to save two days per well compared with the drill plan. In the best of the five wells, the RSS built to a 93.46˚ curve and drilled a 15,033-ft horizontal section to a total depth of 18,862 ft without tripping out; the dogleg severity was 10.65˚/100 ft. The well was drilled in fewer than 137 hours, putting it within the operator’s top 10% of wells drilled in terms of speed, according to Weatherford.
Beating the heat with ceramics
In March 2015, Schlumberger launched the PowerDrive ICE ultraHT RSS, which is rated to 200˚C. This push-the-bit RSS targets high-pressure, high-temperature environments, including onshore North and Latin America, as well as offshore in the Gulf of Mexico, Gulf of Thailand and the North Sea.
Ceramics play the most critical role in the tool’s temperature rating. “The main issue that electronics have in high temperatures are the plastic components’ reliability and life expectancy,” said Juan Restrepo, Drilling & Measurements Product Champion, Rotary Steerable Systems for Schlumberger. In addition to mounting the tool’s electronics, which is packaged into multichip modules, on a proprietary ceramic substrate, the company also uses metal-to-metal seals for reliance in harsh fluid conditions and inert gas to hermetically seal the entire electronics package for protection against humidity and corrosion.
The tool also features automated hold inclination and azimuth, enabled by dynamic inclination and azimuth measurements acquired in the RSS, located directly behind the bit. Sensors read deviation from the set wellbore path during drilling and automatically readjust the RSS commands to steer back into the charted path, Mr Restrepo said.
In summer 2015, PEMEX worked with Schlumberger on an exploratory well in the Sureste basin offshore Mexico. The target reservoir had an estimated bottomhole temperature of 190˚C, and the operator needed to drill a J-shaped well with a 25˚ inclination to reach the reservoir. A conventional mud motor was used first in the 8 ½-in. section. However, it failed to provide directional control due to the difficulties that are usually associated with sliding in very deep wells. Schlumberger then recommended the PowerDrive ICE ultraHT RSS to meet PEMEX’s requirements for an RSS that can perform in high reservoir temperatures and mud weight up to 119 kg/cu m.
Using the new RSS, PEMEX was able to build the curve from 17.5˚ to 26.3˚ and maintain tangent through the well trajectory, even at bottomhole temperatures of 181˚C (357.8˚F). The tool logged 304 operating hours during the job and reached a true vertical depth of 6,065.5 m (19,900 ft).
Drilling straighter
In the US land environment where drilling margins are growing ever tighter, operators are looking for any cost reduction that can boost project economics. “In the land market, the challenge is mostly with cost,” said Paul Neil, Director – Steerable Technologies at National Oilwell Varco (NOV). In July 2015, NOV launched the Vertical Drilling Tool (VDT), an autonomous point-the-bit vertical RSS tool targeting land drilling. “We recognized that there is a need in the market to develop a fit-for-purpose reliable technology that would be cost effective for the US land market.”
Mr Neil said the tool was designed to automatically adjust to formation changes during drilling, when the dip of the formation can force the RSS off its vertical path. To counteract this tendency to veer off track and to help the tool remain vertical, the VDT comes equipped with sensors that read the changing inclination of the wellbore.
“If the tool starts to drift from vertical, the electronics send a signal to the metering mechanism, which turns the toolface into the direction you need to go and then steers the tool in the direction you need to steer it.” The tool is set on path automatically, as there is no need for human interaction to keep the RSS vertical, he said.
In the first half of 2015, the tool was deployed in 20 wells in North Texas next to 10 offset wells that were using only a motor BHA. Average total depth of all wells was 5,200 ft. The RSS was able to improve ROP by 60% over the motor BHA, averaging approximately 100 ft/hr, and improved verticality by 15%, according to NOV. The company attributes the gains to the tool’s automatically seeking vertical features, helping the RSS constantly stay on track without any need for human intervention.
To create a tool that is cost-effective for the land market, NOV aimed to cut as much cost out of the tool as possible without impacting reliability. “By using our expertise in manufacturing, our reach and supply chain, we were able to drive a lot of those costs out,” Mr Neil said. “Using our manufacturing expertise, leveraging our knowledge in motors and coil tubing and electronics, we were able to draw costs out of the tool.”
Further, the company sought to reduce operators’ operational costs for the VDT, Mr Neil added. “We drove the cost out of the tool not just from an overall asset cost but from a durability standpoint, so parts would last longer.” DC
OrientXpress is a trademarked term of 2TD Drilling.
Click here to read about Baker Hughes’ VisiTrak Geospatial Navigation and Analysis Service.