Maintenance history materializes with RFID
Radio-frequency equipment tags gain momentum as technology proves value, durability in the field
By Frank Breland, Diamond Offshore

Radio-frequency identification (RFID) has become a key ingredient to increase reliability in the drilling industry. It is one of the only industries where RFID is almost a requirement to better reliability, maintainability and availability, primarily because assets in the drilling industry move. Unlike a process plant or a refinery where a boiler or a turbine stays in one location from cradle to grave, capital equipment in the oilfield moves like inventory.
The “maintainer” changes from the mechanic on the rig to the man in the drilling contractor’s yard to the OEM’s service personnel. Because of the extreme wear and tear in the industry, most styles of identification, serial numbers, name plate, direct part marking, etc, usually get knocked off or worn out after a few years, and there is no way to identify the asset. Maintenance history ceases to exist.
After many trials and tribulations, RFID has finally developed a ruggedness that has transformed itself into the key to asset identification and maintenance management.
The offshore drilling industry is an extremely complex and asset-intensive workplace that requires skilled people working in unison to function like the well-oiled machines they operate. The two primary groups that need constant attention are the equipment being operated and the people who operate them. The focus of this article will be the former (equipment), which results in increased efficiency in the latter (rig personnel).
This article will discuss how imperative it is to make the identification and maintenance of assets as easy as possible in an industry where the equipment are being pushed to the limits of their operating capabilities.
With the industry drilling deeper and more difficult wells, companies want to know where all assets are at all times and be able to have access to their disposition via the Web.
Trying to keep track of equipment manually on paper is not only ineffective but unwise, because technology is available today to make the entire process seamless. Initially there is a certain amount of effort required to set up the process. Because it is becoming harder to find people with 20 years of experience in the drilling industry, it is necessary to leverage the new generation of rig personnel who have grown up with new technology and are accustomed to using the Web. This new demographic of oilfield workers “Google” the Web for how-to’s to find answers.
The key then lies in not only leveraging these technologies to work for our industry to attract the best and brightest but also making it easy enough to retain the experienced personnel already in the industry.
The system is the solution

What is required is a solution that is simple to use, simple to train and simple to manage. One solution uses a combination of RFID tags, rugged handheld electronic scanners and a continuously synchronized distributed database – all connected via the Web. It is critical to have the ability to create visibility into all operations even when the industry is challenged by the limited bandwidth of the satellite connectivity that is the lifeline of rigs.
What bar coding did for other industries, RFID is expected to do for the drilling industry. However, the most important consideration has always been the survivability of the tags in harsh environments. Most traditional forms of identification, such as serial numbers, name plates, direct part markings, etc, usually survive a few years, and then there is no way to identify the asset anymore.
Bar codes are not a solution because of the amount of mud and grease on the machinery, which causes the bar code to become covered or faded and undetectable by a scanner. Radio-frequency technology does not require a clean tag; it is immune to mud and grease.
RFID tags are custom-designed for different asset types, even as far as safety assets like fire extinguishers. These tags are affixed to every piece of owned equipment, regardless of wide-ranging locations or sites that are difficult to access. The latest RFID tags withstand up to 6,000 psi.
Operationally, the process is simple. Once a company’s assets are tagged, personnel can use the handheld device to read each one and electronically feed that information into a central database. The information can then be accessed on the Web, allowing users to immediately see the equipment’s location and status. Users can walk up to the equipment and scan the tag to see the asset’s maintenance history and immediately get step-by-step instructions to perform maintenance.
Making it work
Instead of making calls to managers, toolpushers or offices, RFIDs consolidate the task into a couple of mouse clicks to gather data on:
• Where a critical spare is located;
• If the required maintenance was correctly completed;
• If the maintenance procedure is appropriate for a piece of machinery;
• If all inspections are complete and current;
• If everything is in compliance; and
• If product updates have been applied or acknowledged.
Preparing reports for any group – maintenance, operations or finance – is a matter of mouse clicks as opposed to phone calls. The input into the system was another foreboding and time-consuming task when performed manually.
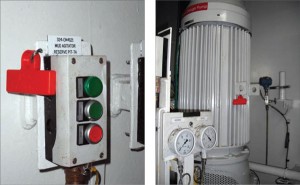
Because the system with RFIDs is always up-to-date, reports are instantaneous. The reports, in addition to a feature called “standardize the search,” can obtain both equipment location/status and maintenance history/step-by-step maintenance instructions from one location. The goal is to provide everyone, regardless of craft on or off the rig, with information that makes them an instant expert.
The repercussions of the Macondo incident also has placed increased pressure on the global work force, which does not always have in-depth knowledge of oilfield equipment primarily supplied by US companies. Therefore, instant Web access to detailed equipment information and simplified procedures in the local language is important and almost required. Considerable time has been spent writing instructions in regional languages and revisiting some that needed to be adapted to the newer workforce and newer operating environments.
Additionally, having the capability to know exactly where all equipment is, even on warm- or cold-stacked rigs, allows companies to see asset location and condition and gives them the ability to gauge which equipment should be deployed or maintained in order of priority.
Certainly, RFID is merely a mechanism. By combining RFID technology with the collective knowledge at Diamond Offshore, the company has the capability to spread that knowledge across the entire fleet, resulting in a sustainable competitive advantage.
This article is based on a presentation at the IADC Advanced Rig Technology Conference & Exhibition, 20 September 2011, Houston.
Frank Breland is manager of worldwide maintenance for Diamond Offshore.